TA10 鈦合金的深孔鑽削技術研究
2018-4-20 來(lái)源:西(xī)安石油大學 機械工程學院 作者:趙 超
摘要: 本文通過實驗分析(xī)了對 TA10 材料進行(háng)深孔加工的難點和解決方(fāng)法,並進行了加工試驗,優化了刀具(jù)角度,分析了加工刀具的磨損機理。取得了較好的加(jiā)工效果,對 α 型鈦合金的深孔鑽削有一定的參考意義。
關鍵詞: TA10 鈦合金; 深孔鑽削; 刀具(jù)設計; 磨損機理
TA10( Ti - 0. 3Mo - 0. 8Ni) 鈦合金(jīn)屬於近 α 鈦合金的一(yī)種,一般(bān)情況下以鍛造、擠壓、軋製(zhì)和拉拔的(de)鈦合金圓棒、矩形棒形態。是 20 世(shì)紀 70 年代中期美國研(yán)究開發的 Ti - 12合金,具有很強的抗縫隙(xì)腐蝕能力(lì)。
在 300℃ 時抗拉強度是工業純鈦的將近(jìn)兩(liǎng)倍,抗還原性介質腐蝕能力(lì)強(qiáng),在 150 ~200℃ 的(de)氯化物(wù)中能夠不發生(shēng)腐蝕現象。並且 TA10 材料不含稀有金屬,加工性能相對較好。在一些純鈦可能出現縫隙腐蝕(shí)的環境中(zhōng)得到廣泛應用。TA10 鈦合金工藝性能優(yōu)良,可以在 850 ~ 950℃ 的範圍內(nèi)進行鍛軋,在盡可(kě)能低的(de)溫度下進行熱加工,可使表(biǎo)麵汙染減至最低,為了防止材料(liào)吸氫產生氫脆現象,需(xū)要在氧化環境中進行加熱。其具有優良的可塑性和彎曲性能。在250℃ 環(huán)境中成型可(kě)以減小回彈(dàn)。通常采用氬氣保護鎢極電弧焊,在焊接溫度達到(dào) 430℃ 以上為避免 C、N、H、O 的汙染需(xū)要特殊保護。TA10 材(cái)料具有以(yǐ)下特點:(1) 有較高的設計應力;(2) 在氧(yǎng)化性介質中具有(yǒu)等於或超越純鈦的耐腐蝕性能;(3) 在還原性(xìng)介質中(zhōng)耐蝕性優於(yú)純鈦;( 4) 在高溫氧化物中具有較好的(de)抵抗縫隙腐蝕的能力;( 5) 成本較低。因此 TA10 材料作為熱交(jiāo)換器、管式反應器、蛇形管、結晶器等在化工、輕工(gōng)、核工業、環境保護等領域發展迅速。其機械性能與其他材料對比特性比較明顯。

表 1 TA10 與 TA2 純鈦和 45#鋼的機械性(xìng)能對比
從表1 中可(kě)以(yǐ)看出 TA10 鈦合金具有優良的機械性能,其強度在高溫區域變化幅度較小,其密度隻有(yǒu) 45#鋼的一(yī)半,強度較純鈦類材料高,在硝酸蒸汽中(zhōng)耐腐蝕性遠(yuǎn)優於純鈦類材料。其彈性模量值(zhí)較小,變形(xíng)係數小於1,導致鈦合金材料(liào)在進行加工時(shí)已加工表(biǎo)麵回彈嚴重,鑽(zuàn)削時會產生長薄卷曲型切屑,排屑困難(nán),並且鈦合金化學活性大,在加工表麵容易形成硬化層,導致加(jiā)工表麵硬度和脆(cuì)性提高,粘刀現象嚴重。其熱傳導係數(shù)隻有 45#鋼的一半左右,在進行鑽削時散熱困難,切削熱過大,容易引起(qǐ)刀具磨損或者刀具失效。尤其在進行深孔加工這種特殊的加工方式時,對刀具的磨(mó)損嚴重,加工質量、加工效率無法保(bǎo)證。針對 TA10 材料的難加工性,本文從刀具角度出發進行了實驗(yàn)分析(xī)。
1、試驗設備與工件
加(jiā)工係統: 對(duì) TA10 的深孔鑽削試驗采用 BTA 深孔鑽(zuàn)削係統進行鑽(zuàn)削試驗,係統機床為 CW6163D 深孔加工機床; 鑽頭使用 φ54 mm 五齒深孔鑽鑽頭,如圖 1; 刀片材料為 YG8,刀具角度如圖 2。該深孔鑽係統是深孔(kǒng)加工常用的係統,加工範圍廣,加工質量較高。
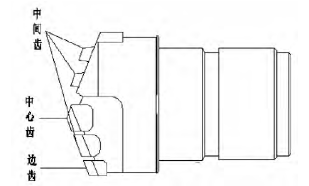
圖 1 鑽頭結構示意圖
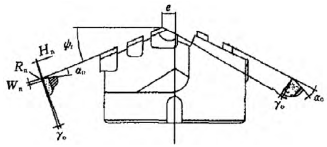
圖 2 鑽頭角度示意圖
掃描電子顯微鏡 JSM - 6390A: 掃麵電子顯微鏡是一種利用電子束掃(sǎo)描樣品表麵從而獲得樣品信息的電子顯(xiǎn)微鏡。
它能(néng)產生樣品表麵的高分辨率圖像,且圖像呈三(sān)維,掃描電子顯微鏡能被用(yòng)來鑒定(dìng)樣品的表麵結構。它由(yóu)三大部分(fèn)組成: 真空(kōng)係統,電子束係統以及成像(xiàng)係統(tǒng)。本文(wén)主要利(lì)用其進行(háng)兩方麵試驗,一是對刀片表(biǎo)麵形貌(mào)進行觀測,二是對刀具表麵進行能譜分析通過成分殘留來分析刀具的磨損機理。手持式粗糙度儀(yí): 用於測量多種機加工零(líng)件的表(biǎo)麵粗糙度,根據選定的測量條件計算(suàn)相應的參數,在液晶顯示器上清晰地(dì)顯示全部測(cè)量結果及圖形。試驗工件為近 α 類鈦(tài)合(hé)金 TA10,為 Φ290 mm × 2700 mm的鈦棒。
2 、試驗方案
本(běn)實(shí)驗對 TA10 棒料進行鑽(zuàn)削,鑽削采用 54 mm 直(zhí)徑的深孔鑽鑽通孔,通過改變鑽頭前角、後角進(jìn)行鑽削(xuē),采用單因素變量法收集數據,觀察加工過程中出現的振動(dòng)情況,利(lì)用粗糙度儀測量工件的(de)內孔壁粗糙度,並且通過電子(zǐ)顯微(wēi)鏡觀察刀具的磨損狀況來取得最佳的工(gōng)藝參數,通過研究(jiū)鑽頭的磨損、殘留成分情況分析刀具磨損原因得到 TA10 材料進行深孔鑽削時的磨損機(jī)理。具體加工參(cān)數:
(1)加工係統: 基於 CW6163D 深孔(kǒng)加工(gōng)機(jī)床的 BTA 深孔(kǒng)加工係統;
(2) 加工刀具: φ54 五齒型錯齒深孔鑽鑽頭,刀片(piàn)材料YG8 硬質合金;
(3) 刀具(jù)角度: 前角 3°、7°,後角 8°、12°,餘偏角 18°,鑽尖偏心量 4 mm;
(4) 工件材(cái)料(liào): Φ290 mm × 2700 mm 的 TA10 鈦棒;
(5) 切削液: 乳化液;
(6) 運動方式: 刀具進給,工件旋轉;
(7) 切削參(cān)數: 鑽孔深度 2700 mm,孔直徑 φ55 mm,刀具轉速 145 r/min,進給量 0.12 mm/r。
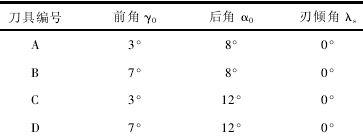
表2 試驗刀具角度
3 、實(shí)驗結果
實驗得到的實驗數據見表3。
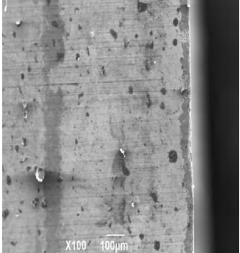
圖3 前(qián)刀麵磨(mó)損現象
綜合(hé)考慮相關加工情況,可以得知,由於材料的(de)塑(sù)性變形能力差,刀具前角取小值 3°時,相比於前角取 7°切屑與前(qián)刀麵接觸長(zhǎng)度增加,前刀麵的磨損相(xiàng)對(duì)來講有所增加,刀具耐用度有所下降; 但由於前刀麵所受應(yīng)力集中現象(xiàng)有所減(jiǎn)緩(huǎn),刀(dāo)具的切削溫度和受力強度降(jiàng)低。同(tóng)時對(duì)比發現,由於鈦合金材料在深孔鑽削時由於變形係數小,彈性模量小,在加工過(guò)程中(zhōng)材料(liào)回彈現象嚴重(chóng),導致刀具後刀麵取小角度時與工件摩擦嚴重(chóng)造成切削熱急劇上升,引(yǐn)發係統異響和振動,刀具的磨損現(xiàn)象比較嚴(yán)重,甚至出現打(dǎ)刀、崩刃等現象,因此刀具後角需要增大,選取 12°為佳。另外通(tōng)過對比發現(xiàn),在切削鈦合金時,刀具後(hòu)角的作用相(xiàng)對於前角來講影響比(bǐ)較顯著,因此增大後角可以在保證(zhèng)刀具強度(dù)的前提下更有效的提高刀具耐用度。因此選用前角 3°,後角 12° 加工狀態良好。其道具磨(mó)損電鏡顯微結果見圖 3 ~ 圖 4。可見在對 TA10 材料進行深孔(kǒng)鑽削時(shí),由於材(cái)料的回彈現象,刀具的(de)後刀麵磨損程度(dù)遠遠比前刀麵嚴重,利用掃(sǎo)麵電子顯微鏡對後刀麵(miàn)的深色和淺色分區進行(háng)取點能譜分析。
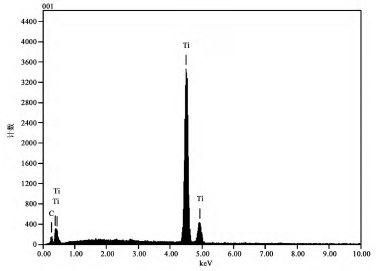
圖5 深色區能譜圖
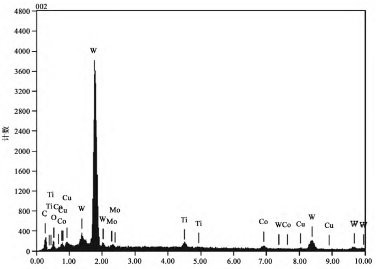
圖6 淺色區(qū)能譜圖
可以發現在貼近刀刃的深色區(qū)域富集了(le)大量(liàng)的 Ti 元素,而在距(jù)離刀刃較遠的淺色區域,為以 W、Co 等刀具材料為主,Ti 元(yuán)素隻有極少量(liàng),說明(míng)在(zài)加工過程中工件材(cái)料在高溫高壓下出現(xiàn)了明顯的粘結現象,綜合研究(jiū)發現,在對 TA10進行深孔加工時由於切削力和(hé)切削溫度比較(jiào)高,工(gōng)件材料的硬度不大,親和性強,因(yīn)此硬質合金刀具的磨損主要以粘結磨損為主。
本次(cì)試(shì)驗利用 TR200 手持式粗糙度儀對加工孔的粗糙度進行測量分析,由於孔深較大(dà),因此采用工件末端出鑽口粗糙度(dù)采樣(yàng)進行對比(bǐ)分析。
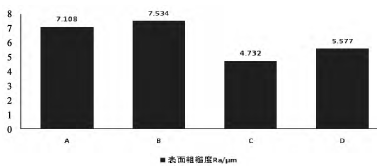
圖7 不同刀(dāo)具角度下(xià)的內孔表麵粗糙度
由圖 7 能夠發現,在保證刀具強(qiáng)度(dù)的前提下,當刀具的前(qián)角和後角越大時,刀具越鋒利,能夠穿過材料的加工硬化層進行切削,從而加(jiā)工孔的表麵質量比較高。針對 TA10 鈦合金的硬度相對較低的特(tè)點,在加工時選用大的(de)刀具角度有利(lì)於切削的順利進行。並且可以看出 C 型角度(dù)的(de)深孔鑽頭加工質量也(yě)相對較好。
4、結論
本文通過對(duì) TA10 鈦合金的物(wù)理性能和切削加工性研究分析,並與純(chún)鈦(tài) TA2 和 45 號鋼進行對比,結合深孔加工的特(tè)點對 TA10 材料進行深孔鑽削試驗。針對 TA10 材料的切削加工特點,選用了Φ290 mm × 2700 mm 的(de)鈦棒(bàng)進行深孔加工試驗,通過不同角度鑽頭的試驗對比,得出了以下幾點結論:
(1) TA10 具有優越的塑性和相對較(jiào)好的高(gāo)低溫強度(dù),並(bìng)且(qiě)比強度高,耐腐蝕性強。其切削加工性和純鈦類似。在對其進行加工時也有很多不利因素,加工硬化嚴重、刀具磨損快等降低(dī)了(le)其的應用性。在切削時,由於工件材料的彈(dàn)性模量低(dī),變形係數(shù)小的特點,已(yǐ)加工麵回彈(dàn)現象嚴重,對刀具後刀麵產生劇烈磨(mó)損; 同時(shí)切屑與前刀麵接觸時間短,導(dǎo)致前刀麵單位麵積切削力大、切削溫度(dù)高; 另外鈦元素的化學活性大,容易(yì)產生加工硬化層,同時與刀具產生粘附(fù)現(xiàn)象。這一係列的加工(gōng)特點加速了刀具的磨損,尤其在深(shēn)孔加工時,加工環境更加惡劣,加工效率和效果均不理想。
(2) 在對(duì) TA10 材(cái)料進行深孔加工時,根據加工材料的尺寸和特點,選用(yòng)五齒型錯齒內排屑深孔(kǒng)鑽進行加工,刀片(piàn)材料選用 YG8 硬質(zhì)合金比較合理(lǐ),其(qí)具有較高的強度和硬度,並且不容易與(yǔ)工件發生親和(3) 根(gēn)據鑽削過程中的(de)振動以及刀具的磨損情(qíng)況(kuàng),在對Φ290 mm × 2700 mm 的 TA10 鈦棒(bàng)時,刀(dāo)具角度取前角 3°,後角 12°時刀具耐用度較好,加(jiā)工效果較好。(4) 加工(gōng) TA10 材料時,刀具後刀麵的(de)磨損相對(duì)於前刀(dāo)麵嚴重,後刀麵的磨損情況決定了刀具的耐(nài)用度,因此(cǐ)刀具後角比其他角度影響明(míng)顯。刀具的磨損(sǔn)形(xíng)式以粘接磨損為主。
投稿(gǎo)箱:
如果您有機床行業、企業(yè)相關新聞稿件發表,或進行資訊合作(zuò),歡迎聯係(xì)本(běn)網(wǎng)編輯部, 郵箱:skjcsc@vip.sina.com
如果您有機床行業、企業(yè)相關新聞稿件發表,或進行資訊合作(zuò),歡迎聯係(xì)本(běn)網(wǎng)編輯部, 郵箱:skjcsc@vip.sina.com
更多相關信息
業(yè)界視點
| 更多
行業數據
| 更多
- 2024年11月 金屬切(qiē)削機床(chuáng)產量數據
- 2024年11月 分地區金屬切(qiē)削機床產量數據
- 2024年11月 軸承出口情況
- 2024年(nián)11月 基本型乘用車(轎車)產量數據
- 2024年11月 新(xīn)能源汽車產量數據
- 2024年11月 新能(néng)源汽車銷(xiāo)量情況
- 2024年10月 新能源汽車產量數據
- 2024年10月 軸承出口情況
- 2024年10月 分地區金屬切削機(jī)床產量數據
- 2024年10月 金屬(shǔ)切削機床產量數據
- 2024年9月 新能源汽車銷量情況(kuàng)
- 2024年8月(yuè) 新能(néng)源汽車產量數據
- 2028年8月 基本型乘用車(chē)(轎車(chē))產量數據