基於微(wēi)細電火花(huā)加工技術的微衝裁模具在線製備
2017-1-4 來源: 大連理工大學機械工程學院 作者:鞏向偉,曾誌傑,於騰龍,李劍中,徐文驥,
摘要:針對微衝裁(cái)異形截麵的微小模具難以製備及安裝對準的問題,利(lì)用微細電火花(huā)三維銑削加(jiā)工技術加工反拷貝電極及凹模,利用所加工的反拷貝電極通過電火花反拷貝加工技術(shù)加(jiā)工(gōng)凸模,整個工藝過程在線製作,避免了凸凹模具二次裝夾產生的位置誤差。該工藝分別在線製作凸凹模具,實現了複雜截麵形狀微型模具製備和(hé)在線對準。通過設(shè)計(jì)試加工實驗確定加工參數,並(bìng)利用該工藝成功製作了一(yī)套截麵形狀複雜(zá)的具有微小特征結構的高精度微(wēi)衝裁模具(jù)。
關鍵詞:微細電火花加工;微(wēi)衝裁模具;反拷貝加工
隨著產(chǎn)品微型化的發展,對微型零件的需求日益增大。但微(wēi)型零件的低成本、大規模生(shēng)產仍難以實(shí)現,其成為(wéi)製(zhì)約微型產品普(pǔ)及的關鍵因素。微衝(chōng)裁作為微成(chéng)形工藝的(de)一種,具有生產效率高、材料損失小、最終(zhōng)成形零件(jiàn)機械性能(néng)好(hǎo)、尺寸偏差小、淨成形及近淨成(chéng)形等優(yōu)點[1],是製造(zào)微細零件最有前途(tú)的工藝之一(yī)。但微衝裁工藝中仍存在(zài)微(wēi)小模具難以製作及對準(zhǔn)的問題[2]。
早在20 世紀80 年代末,Masuzawa[3]就利用微細電火花加工技術在線(xiàn)製備微衝裁模具,並成功衝出了直徑幾十微米的小孔及(jí)異形孔。Chen[4-5]在此基礎上, 利用vibration-EDM 來提高微(wēi)衝裁模具的加工(gōng)效率及表麵質量(liàng),製造出高精度的微型多邊形衝頭,實現了(le)異形微孔的高質量加工。Joo[6-8]分別采用微細研磨及微細電火花加工技術製作微型凸凹模,在自行設計的微衝裁係統上利用光學原理對其(qí)進行裝配,最終在黃銅及(jí)不鏽(xiù)鋼箔(bó)上製作(zuò)出(chū)深徑比為1、直徑分別為100、50、25 μm 的微孔件。由於微細研磨難以製造(zào)直徑(jìng)更小的衝頭,此後他們改用微細電火花加工(gōng)技術製造微衝裁模具,並在13 μm 厚的(de)黃銅及不鏽鋼材料上成功(gōng)衝出直徑(jìng)15 μm 微孔。徐傑[9]利用塊電極電火花磨削技術(BEDG)加工凸模,然(rán)後利用凸模在線(xiàn)加工凹模, 並分別(bié)在厚度(dù)150、80、50 μm 的不鏽鋼箔上衝出直徑300、150、100 μm的微孔。
目前微衝裁模具加工主(zhǔ)要采用線電(diàn)極電火花磨削技術(WEDG)[10]或塊電極電火花磨削(xuē)技術製作電極,並利用其加工出凹模(mó),然後對電極修整製作出所需的凸模。該(gāi)工藝因無法製(zhì)造截麵形狀(zhuàng)複雜的異形微模具(jù),使微衝裁技術僅局限於衝製簡單形狀的微孔。本文著重介(jiè)紹一種在線製備複雜截麵形狀微衝裁模具的微細電火花加工工藝,並對加工的結(jié)果進行分析,說明了產生誤差(chà)的(de)原(yuán)因。
1.實驗裝置
實驗裝(zhuāng)置為自行研製(zhì)的微細電火花(huā)-微衝裁組(zǔ)合加工機床(圖1),其結(jié)構示意圖見圖2。此係統(tǒng)中, 主軸用於裝夾微細(xì)鎢電(diàn)極,WEDG 單元用於完成微(wēi)細鎢電極製(zhì)備,油(yóu)槽及(jí)凸凹模組件分別用於裝夾反拷(kǎo)貝電極及凸凹(āo)模毛坯(pī)。該加工設備X、Y、Z1、Z2軸重複(fù)定位精度(dù)1 μm, 采用RC 弛張式(shì)脈衝電源,使用正極性加(jiā)工,加工工作液(yè)為(wéi)煤油。
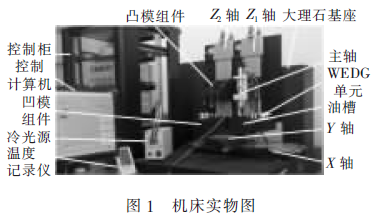
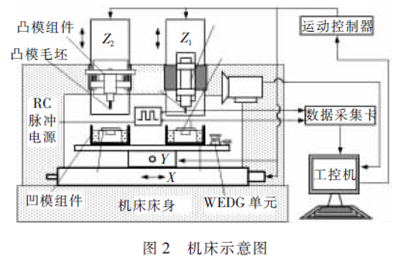
2.微衝裁凸凹模具形狀及設(shè)計尺寸
本文所衝製零件的形狀及尺寸見圖3。該零件為衝裁落料件,凹模形狀(zhuàng)及尺寸與其相同,沿凹模輪廓向內偏(piān)置單邊衝裁間隙即為凸模輪廓。衝裁時,工(gōng)件材料(liào)厚度(dù)為100 μm,取單邊衝裁間(jiān)隙為材(cái)料厚度的10 %,即衝裁單邊間隙為10 μm;凹模厚度300 μm,凸模軸向長度500 μm,凸凹模(mó)具材料為Cr12MoV 模具鋼,各特征設計尺寸見表1。
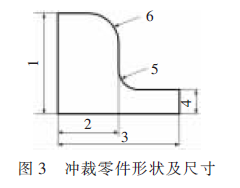
表1 微衝裁零件及凸凹模具各特征尺寸(cùn)設計值μm
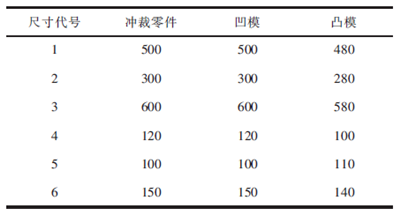
3.微衝裁凸凹模具在線製備
3.1 凹模加(jiā)工工藝
凹模製作(zuò)包括粗、精加工兩個過程。首先,用線電極電火(huǒ)花磨削技術(WEDG)粗加工出直(zhí)徑約160μm 的鎢(wū)電極,采用較大的放電能量,在凹模毛坯的適當(dāng)位(wèi)置加(jiā)工多個通孔(kǒng)(圖(tú)4a)。此過程為粗加工工藝,采用(yòng)較大的放(fàng)電能量(liàng)及鑽孔工藝是為了提高加工效率,快(kuài)速去除工件毛坯材料。粗加工工(gōng)藝不需使用尺(chǐ)寸精確的電極, 隻(zhī)需(xū)合理控製精(jīng)加(jiā)工餘(yú)量(本實驗(yàn)餘量控製為60~80 μm)。
為得到高精度凹模,精加工需使用尺寸精確的微(wēi)細鎢電極及小的放電能量(liàng)。因粗加工鑽孔後微細鎢電極存在(zài)一定的損耗,其徑向損耗會影響電極的尺寸精度, 故鑽孔後先將電極前端損耗部(bù)分切除,再經(jīng)粗、精加工最終加工出直徑100 μm 的高精度電極。利用加(jiā)工出的尺寸精確的微(wēi)細鎢電極(jí)沿圖4b中(zhōng)事先生成的刀具軌跡,采用較小的放電能(néng)量進行微細電(diàn)火花三維分層銑削加(jiā)工, 經過(guò)電極層層掃描,最終加工(gōng)出上下通透的凹(āo)模(圖4c)。分層加工過程電極采用逆、順時針交(jiāo)替的刀具軌跡(jì)進行(háng)掃描, 以盡可能減小每一層被加工麵的不平整度,提高火(huǒ)花放電的穩(wěn)定性,改善加(jiā)工效率。此外采(cǎi)用工(gōng)具電極多進給的加工方式減小凹模入出口尺寸差,提(tí)高加工精度[11]。
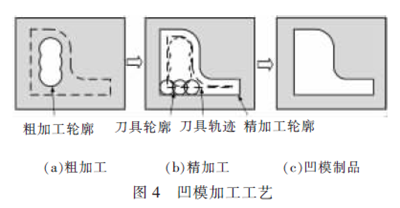
3.2 凸模加工方(fāng)法
凸模加工工(gōng)藝分(fèn)為(wéi)兩步,首先利用微細鎢電極在500 μm 厚的黃銅片上加工出與凹模形(xíng)狀相同的反拷貝電(diàn)極(jí),其與凹模加工方式相同。然後將凸模毛坯對準(zhǔn)反拷(kǎo)貝電極,控製凸模向下進給,最終加工出與反拷貝電(diàn)極形(xíng)狀相同的凸模(mó)(圖(tú)5)。為提(tí)高凸模加工精度, 應保證凸模前500 μm 使用部分能被500 μm 厚反拷貝電極充分加工, 故(gù)將加工總進給量設定為1 mm。此加工工藝采用較小的(de)放電能(néng)量以保證獲得表麵質量較好的凸模,同時采用超(chāo)聲波輔助振動反拷貝電極底部工作液的(de)方(fāng)法來提高加工效率及加工精(jīng)度(dù)。
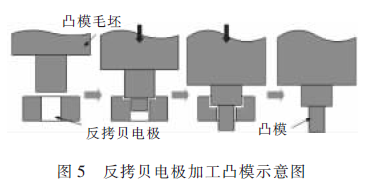
由於反拷貝加工凸(tū)模時間較長,而加工時間與(yǔ)材料去除量成正比,為提高(gāo)加工(gōng)效率,凸模毛坯棒材先用線切(qiē)割工藝加工出0.9 mm×0.9 mm×1.5 mm的正方體凸台(圖6)。
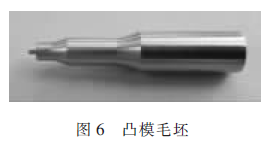
3.3 凸凹模(mó)具在線加工工藝流(liú)程
在(zài)線(xiàn)加工可避(bì)免凸凹模具的裝(zhuāng)夾誤差,是解決微衝裁(cái)模具難以對準的有效途徑,其加工工藝流程見圖7。
(1)確定凸(tū)模中心與主軸旋轉中心之間坐標的轉化關係。首先(xiān)利用(yòng)凸模毛坯在反拷(kǎo)貝電極毛坯上采用較大放電能量加工出方形(xíng)坑(圖7a)並記(jì)錄加工坐標,再利用機床的探測感知功能采用(yòng)圓(yuán)電極旋轉探測方坑四邊每邊各兩點, 擬(nǐ)合出方坑中心,最後利(lì)用(yòng)加工坐標及擬合(hé)坐標計算出其轉化關係。
(2)反拷(kǎo)貝電(diàn)極及凹模粗加工。利用WEDG 粗加工出的微細鎢電極分別(bié)對(duì)反拷貝(bèi)電極(圖7b)及凹模(圖7c)進行粗加工,粗加工工藝為(wéi)提高加工效率均采用較大的放電能量。
(3)反拷貝電極及(jí)凹模精(jīng)加工。利用WEDG 方法加工出的尺寸精確的微細鎢電(diàn)極采用微細電火花三維分層銑削加工技術,在較小的放電(diàn)能量下分別對反拷貝電極(圖7b)及凹模(圖(tú)7c)進行精加工。由於反拷貝電極會被後續(xù)用來加工凸模,加工完後其原始尺寸會因電極損耗無法獲(huò)得。因此在加工過程中(zhōng),為(wéi)便於後續調整加工參數,每次同時(shí)加工兩個反拷(kǎo)貝電極,一個用於對比觀測以獲得原始加工數據,另一個用於反拷貝加工(gōng)凸模。因精加工反拷貝電極時鎢電極徑向損耗相比加工凹(āo)模時小(xiǎo),因此該工藝(yì)過程采用先加(jiā)工反(fǎn)拷貝電極再加工凹模的加工順序,避(bì)免鎢電(diàn)極側壁出現(xiàn)較大損耗(hào)影響後續加工。
(4)反拷貝加工凸模。利用反(fǎn)拷貝電極加工坐標以及先前(qián)獲(huò)得的凸(tū)模中心與旋轉主軸中心的坐標轉化(huà)關係,將(jiāng)凸模毛坯與反拷貝電極(jí)對準,保證凸模毛坯完全覆蓋(gài)反拷貝電極輪廓。對反拷貝電極底部工作液施加超聲波輔助振動,采用較小的放電能量進行(háng)反拷貝凸模加工(gōng)(圖7d)。
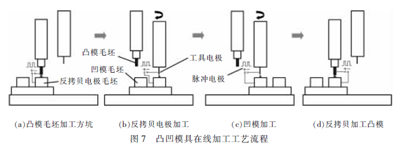
3.4 凸凹模具加工參數確定
要(yào)獲得高精度凸凹模具,就要準確掌握(wò)各加工過程的(de)加工間隙,通過調整刀具軌跡來控製反拷貝電極(jí)及凹模加工(gōng)尺寸。凸模由反拷貝電極經反拷貝加(jiā)工得到,可根據此加工過程(chéng)的加工間(jiān)隙值大小來(lái)調整反拷貝電極(jí)設計尺寸,以加工出與設計尺寸相符的凸模。此處的加工間隙指加工過程中火花(huā)放(fàng)電間隙及(jí)機床因自身運動誤差(chà)及外界幹擾等因素綜合(hé)作用產(chǎn)生的單邊(biān)加工間隙。
反拷貝電極及凹模利用試加工實驗來(lái)確定(dìng)各自加工過程的加工間(jiān)隙。因凸模加工時間較長,為提高加(jiā)工效率,設(shè)計了方形凸模加工實驗來確(què)定反拷貝加工凸模的(de)加工間隙,根據此加工間隙值確定反拷貝電極最終設計(jì)尺寸。
3.4.1 反拷(kǎo)貝電極及凹模加工參數確定
反(fǎn)拷貝電極及凹模加工間隙確定實驗采用與實際加工過程相同(tóng)的放電參數及進給方式(表2),加工與表1 所示凹模尺(chǐ)寸相同的反拷貝(bèi)電極(jí)和凹模。
表2 反拷貝(bèi)電極及凹模(mó)加工參數
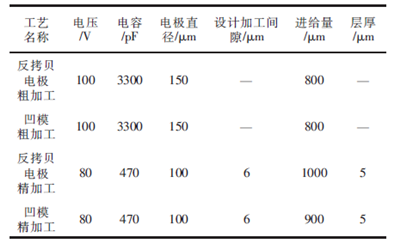
表3 列出了所加工出的反(fǎn)拷(kǎo)貝電極及凹模入口處各尺(chǐ)寸的測量值。其中,反(fǎn)拷(kǎo)貝電極特征尺寸2、3 加工出現較(jiào)大偏差, 而凹模相應(yīng)尺寸偏差並(bìng)不明顯。考慮實際加工過程中,特征尺寸2、3 與機床Y軸平行,而特征尺(chǐ)寸1、4 與機床X 軸平(píng)行。對比發現X 向特征尺寸加工相比(bǐ)Y 向特征尺寸加工更穩定,故在(zài)計算加工間隙時選用特(tè)征尺寸1、4 進行計算,其加工軌跡尺寸分別(bié)為388、8 μm。加工後(hòu)測得所用電極根部未參與加工部分的尺寸為(wéi)100 μm,以此值作為(wéi)實(shí)際計算(suàn)時WEDG 加工出的原始電極直徑,加工間隙的計算方式為:
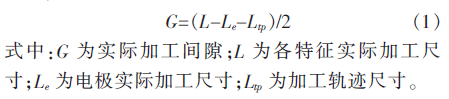
表3 反拷貝電極及凹模(mó)入口處各特征實際加工尺寸μm
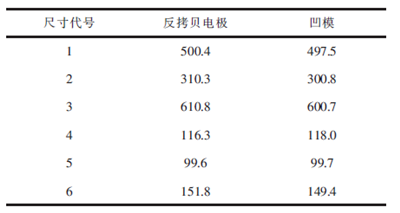
根據式(1)將計算出的反拷貝電極及凹模特征尺寸1、4 的實際加工間隙值列於(yú)表4。凹模特征尺寸(cùn)1、4 的加工間隙相差(chà)較小(xiǎo),可取凹(āo)模加工間隙值(zhí)為5 μm。而反拷貝電極兩特征尺寸加工間隙相差較大(dà),除了存在測量誤差,電火花放電加工過程(chéng)存在一定的不穩定性(xìng)。為(wéi)排除隨機性幹擾及便於對特定尺(chǐ)寸采取加工補償策略, 選取較大加工間隙(xì)6μm 作為反拷貝電極的實際(jì)加工間隙值。
表4 反拷貝電極及凹模實際加工間隙(xì)μm
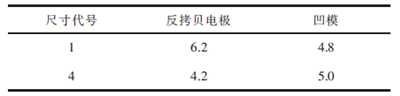
3.4.2 反拷貝加工凸模加(jiā)工參數確定
反(fǎn)拷貝加工間隙確定實驗采用與實際反拷(kǎo)貝加工凸模相同的(de)放(fàng)電參數(表5),通過反拷貝加工簡單(dān)形狀的方形凸模獲得。首先利用微細(xì)鎢電極在500 μm 厚黃銅片上加工出300 μm×300 μm 的方形通孔作為反拷貝電極,然後用其反拷貝加工端部尺寸(cùn)為(wéi)700 μm×700 μm 的方形凸模毛坯, 其加工方式與前文所述相同。因反(fǎn)拷貝(bèi)電極加工凸模後存在(zài)損耗,原始加工數據丟失(shī),故此實驗中設計先後加工兩個反拷(kǎo)貝電極。加工完成後測量實際加工(gōng)出的凸模端麵尺寸及對比使用反拷貝電極(jí)入(rù)口處尺寸,其具體加工結(jié)果見圖8 及表6。
表5 反拷貝加工凸模加工(gōng)參(cān)數
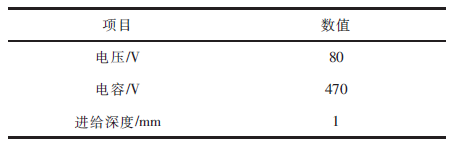
表6 凸模及對比用反拷貝電極加工尺(chǐ)寸μm
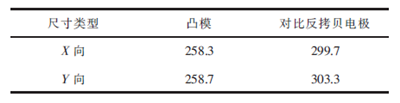
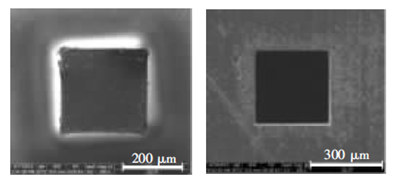
圖8 反拷貝加工凸模加工間(jiān)隙確定實(shí)驗加工出的凸(tū)模(左)及對比反拷貝電(diàn)極(右)
加工數據表明,機床所加工的X 向特征尺寸相比Y 向特征尺寸(cùn)更為穩定,故在計算反拷貝加工凸模(mó)加工間隙時(shí)選用凸模及對比反拷貝電極X 向特(tè)征尺寸,將其(qí)代入式(2),計算得到反拷貝加工(gōng)凸模
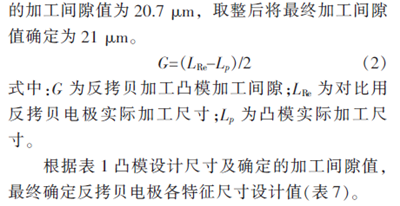
表7 反拷貝電極各尺寸設計值
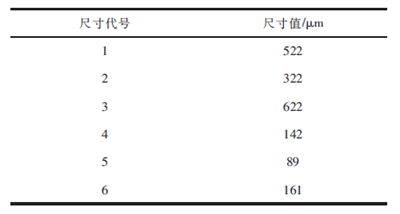
4.凸凹模具加工(gōng)結果及分析
根據前文所(suǒ)述的加工工藝方案,按設計尺寸在線製備了一套(tào)微衝裁凸凹模具,其加工結果(guǒ)見表8~表10 及圖9、圖10,衝裁單邊間隙按凸模端麵及凹模入口(kǒu)尺寸計算得到。凸模側壁選(xuǎn)取特征尺寸1、3、4, 測量端麵至500 μm 處的尺寸值, 測量間隔為100 μm。
表8 微衝裁模具加工結(jié)果μm
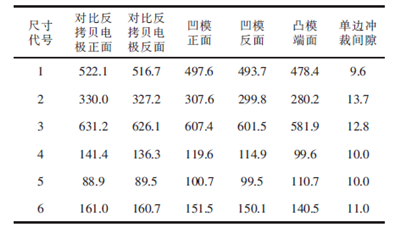
加工結果顯示,凹模及反拷貝電極出口尺寸小於入(rù)口尺寸, 凸模側壁尺寸大於凸模端麵尺寸,凸凹模具存在一定的加工斜度。這(zhè)主要與電火花加工工藝特性有關(圖11)。由於工具電極先參與電火花加工部分的加工時間長,絕對損耗大,而工件先被(bèi)加工出的部分由於電蝕產物的(de)存在,該處的加工間隙隨二次放(fàng)電的概率增大而逐漸(jiàn)增(zēng)大,因而產生了加工斜(xié)度。對比反拷貝電極(jí)及凹模特征尺寸2、3 加工誤差(chà)較大,凸(tū)模此項誤差並(bìng)不明顯,由誤差複映原理可知,參與反拷貝加工凸模(mó)的反拷貝電極此項誤差較小。對比上文加工參數確定實驗中加工(gōng)數據可知,特征尺寸2、3 加工誤差具有一定的 隨
表9 微衝(chōng)裁模具加工誤差μm
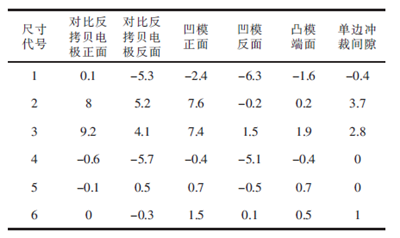
表10 凸模側(cè)麵尺寸μm
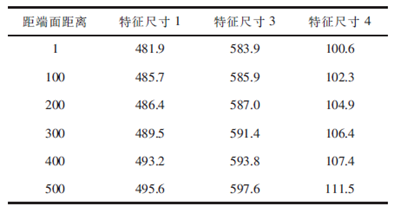
機性。分析表明,加工時此(cǐ)部分尺寸與機床Y 軸平行,說明(míng)機床(chuáng)Y 向存在一定的隨機性擾動。這一擾動的的主要來(lái)源是固定主軸的懸臂(bì)在Y 向(xiàng)產生的熱變形,而X 向由於采用熱對稱設計,則不存在這一問題。影響機(jī)床的熱(rè)源, 一般(bān)可分為內部熱源與外部熱源兩類。實驗中機床主軸懸臂結構的內部熱源主要由(yóu)直流電機(jī)及旋轉主軸產生,外部熱源(yuán)主要(yào)為(wéi)周圍溫(wēn)度變化。圖12 給出了加工過程中一天內機床周圍環境溫度的變化情況, 數據由溫度記錄儀自動采集,采樣間隔半小時。經計算分(fèn)析,當溫度變化1 ℃時,該懸臂結構(gòu)會在Y 方向上產生約(yuē)4 μm 的變形。
5.結束語
本(běn)文(wén)提出了一種(zhǒng)在線製(zhì)備複(fù)雜截(jié)麵形狀微衝裁模具的工(gōng)藝方法。利用微細電火花三維(wéi)銑削(xuē)技術加工反拷貝電極及(jí)凹模(mó),再利用所加工的(de)反拷貝電極通(tōng)過電火(huǒ)花反拷貝加工技術加工凸模,整套工藝流程在線完成(chéng),避免了凸凹模具二次(cì)裝夾產生的位置誤差。采用所提出的工(gōng)藝方法,成功製作了一套截麵形狀複雜的具有微小(xiǎo)特征結構的高精(jīng)度微衝裁(cái)模具,並對加工誤差進行(háng)了分析。
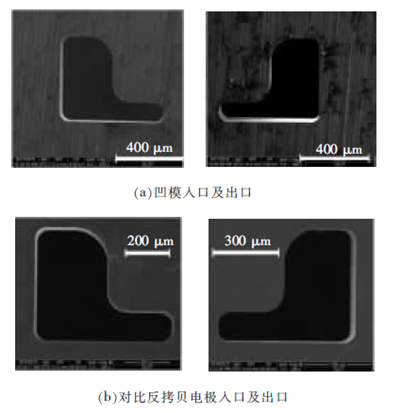
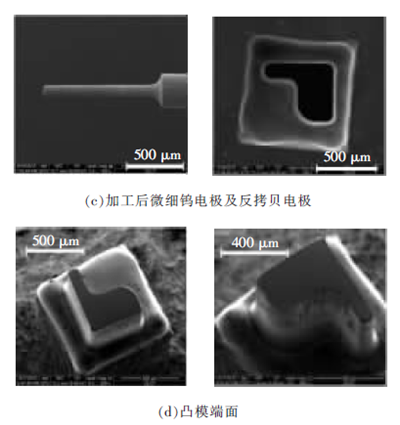
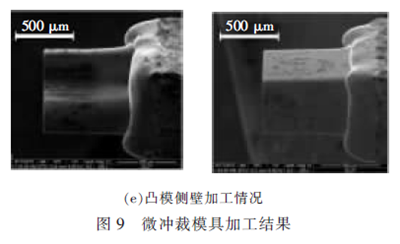
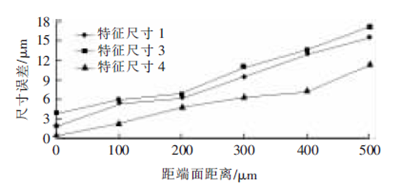
圖10 凸模側(cè)麵(miàn)尺(chǐ)寸誤差
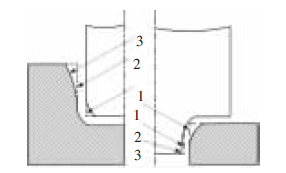
1. 電極無損耗時(shí)工具輪廓線2. 電極有損耗(hào)而不(bú)考慮二次(cì)放電時工(gōng)件輪廓(kuò)線3. 由(yóu)於二次放電引起側壁斜度
圖11 電火花加工斜度示意圖圖
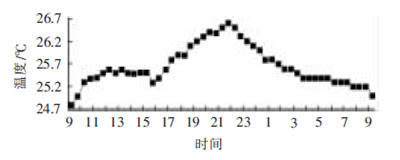
圖12 機床周圍環(huán)境溫度變化情況
投稿箱:
如果您有機床行業、企業相關新聞稿件發表,或進行資訊合作,歡迎聯係本網編輯部, 郵箱:skjcsc@vip.sina.com
如果您有機床行業、企業相關新聞稿件發表,或進行資訊合作,歡迎聯係本網編輯部, 郵箱:skjcsc@vip.sina.com
更多(duō)相關信息
業界視點
| 更多
行業數據
| 更多
- 2024年11月 金屬切削機床產量數據
- 2024年11月 分地(dì)區金屬切削(xuē)機床產量(liàng)數據(jù)
- 2024年11月 軸承出口情況
- 2024年11月 基本型乘用車(轎車)產(chǎn)量數據
- 2024年11月 新能源(yuán)汽車產量數據
- 2024年11月(yuè) 新能源汽車銷量(liàng)情況
- 2024年10月 新能源汽車產量數據
- 2024年10月 軸承出(chū)口情況
- 2024年10月 分地區金屬切削(xuē)機床產量數據
- 2024年10月 金屬切削機床產量數據
- 2024年9月 新能源汽車銷量情況
- 2024年8月 新能源汽車產量(liàng)數據
- 2028年(nián)8月 基本型乘用車(轎車)產量數據(jù)
博文選萃
| 更多
- 機械加工過程圖示
- 判斷一台加工中心精度的幾種辦法
- 中走絲線切(qiē)割機床的發展(zhǎn)趨勢
- 國產數控係統和數控機床(chuáng)何去何從(cóng)?
- 中國的技術工人都去(qù)哪裏了?
- 機械老板做了(le)十多(duō)年,為何還是小作(zuò)坊?
- 機械行業最新自殺(shā)性營銷,害人害己!不倒閉才
- 製造業大逃亡
- 智能時代,少談點智(zhì)造,多談(tán)點製造
- 現實麵前,國人沉默。製造業的騰飛,要(yào)從機床
- 一文搞懂數控車床加(jiā)工(gōng)刀具補償功能(néng)
- 車床鑽孔攻螺紋加工方法及工裝設(shè)計
- 傳統鑽削與螺(luó)旋銑孔加工工藝的區別(bié)