WMEM|航空(kōng)發動機關(guān)鍵製造技術現狀及趨勢
2019-5-16 來源:轉載 作(zuò)者:-
航(háng)空發動機關鍵製造(zào)技術是未來我國航空發動機工業發展的一(yī)個重要指標。傳統的製造工藝和(hé)生產模式已經無法滿足航空發動機製造在高精(jīng)度、高質量、高效率、高可靠性等方麵的需求,隨之而來的三軸、四軸、五軸數(shù)字化加工是未來(lái)中國(guó)航(háng)空發動機製造業發展的重要基礎。
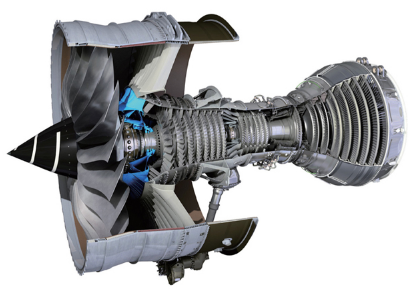
基於航空發(fā)動機高複雜性(xìng)、高可靠性(xìng)等要求,目前航空發動機製造能力仍然按照“製造→試驗→修正製造→再試驗…”的模式,這就注定(dìng)了航空發動機研製本身不(bú)但是個高科技事業(yè),還是一個(gè)高投(tóu)入(rù)的事業。我國在航空發動機研製試驗初期走了不少彎路,幾經坎坷,“三落四起(qǐ)”,目前正處於“第四起”的階段(duàn),對我們既是機遇(yù)又是挑戰。世界上隻有少數的幾(jǐ)個國家具備航空發動(dòng)機製造(zào)技術,它代表了一個國家的科技水(shuǐ)平、工業水平和綜合國力。
通過幾代航(háng)發人的共同努力,我們實現了由噴(pēn)氣發動機向渦扇發動機的曆史(shǐ)性跨越,由小推力到中等推力向大推力轉變,由二代半向三代機、四代機轉變。目前正在開展四代(dài)機及大推力、大涵道比發動機的研發(fā)工作,發展的需求客觀上要求(qiú)我們用更先進的製造技術引領航空發動機技術的(de)提升。
主要關(guān)鍵製造技術(shù)有:整體葉盤、葉環製造技術;靜子、轉子葉片製造技術;機匣製造技術;寬弦風扇葉片製造技(jì)術;金屬基、陶(táo)瓷(cí)基及(jí)碳/碳複合材料構件等製造技術(shù)。
航空發動機需在高空、高速、高溫(wēn)、高(gāo)壓、高轉速和交變負荷的惡劣條件下長期、重複、可靠使用(yòng),與其他運載係統的動力相比,航空發動機是世界上工作(zuò)條件最苛刻,結構最複雜的物理係(xì)統。正如美國在其國家航空(kōng)發動機關鍵製(zhì)造技術推進計劃中(zhōng)寫到的:“這是一(yī)個技術(shù)精深得使新手難以進入的領域,它需要國家充分保護並利用該領域的成果,需要長(zhǎng)期數據和經驗的積累以及國家大量的投資。”
為滿(mǎn)足我國航空發動機更新換代需求,重點需建立、健全航空(kōng)發動機發展型譜。這就使得近年來(lái)發動機機種多,研製周期短,技術難度大。為了能更好地完成各個型號研製的預(yù)定目標,科學高效地開展技術(shù)創新和工(gōng)藝突破,提高技術(shù)成熟度,成為當務之急。
1.梳理(lǐ)流程
在關鍵製造技術領域,以往的技術工作(zuò)一般是圍繞型號任務開展。型號任務下達(dá)後,設計部門(mén)下達技(jì)術圖紙和標準,我們圍繞圖(tú)樣和標準去開展工藝準(zhǔn)備。在(zài)消(xiāo)化圖樣和標準的過程中,不斷發現問題(tí),發現新的工藝(yì)難點和新技(jì)術,再針對新工藝、新(xīn)材料進行立項攻關。
由於之前沒有(yǒu)技術儲備,往往導致研製周期過長,型號(hào)節點一拖再拖(tuō)。針對相關問題,我們需要重(chóng)新梳理流程,改變以往下達圖樣→工藝準備→立項攻關→工藝定型的模式,使相關工作與設計過程(MBD)並行實施。即在設計階段(MBD)開展工藝預(yù)先研究→三維圖下發→工藝準備→工藝定型。針對設計提出的要求開展新材料、新工藝的預先研究,縮短產品研發(fā)時間,提高研發效率。這樣就可以在設計階段即開(kāi)始新工(gōng)藝(yì)和新技術的攻關工作,為型號研製做好(hǎo)技術儲備。當研製任務正(zhèng)式下達(dá)時,可以立即進入生產階段,減少大量的攻關(guān)時間,大大提高研發效率。
2.知識管理
隨著科研型號的不斷增多,新材料、新工藝技術應用也越來越多。但往往(wǎng)隨著優秀專家和技術人才(cái)的(de)退休(xiū)離崗,在新(xīn)材料、新工藝應用(yòng)過程中產(chǎn)生的(de)寶貴經(jīng)驗和知識財富也不斷流失。同時,湧入(rù)的大量新生力量,缺少相關經(jīng)驗知識的支持。如此,人才(cái)隊伍建(jiàn)設能力(lì)不能滿足繁重的型(xíng)號(hào)任務要求。
因(yīn)此(cǐ),建立具有專業(yè)特色的知識工程平台(tái),全麵解決(jué)知識積累、共享瓶頸(jǐng);打造型號研製創(chuàng)新平台,提高研發效率,提升工廠綜合創(chuàng)新能(néng)力,成為(wéi)當務之急。將知識工(gōng)程與工廠(chǎng)型號研發實際結合(hé)起來,針(zhēn)對型號產品研發過程中(zhōng)的工裝設計、材料、製造過程模擬、工藝(yì)改進、產品檢測(cè)等進行知識積累、存儲、共享、應用和創新,建設全麵的知識工程(chéng)支撐平台和計算機輔助創新工(gōng)具,實現知識的快速積累、深度挖掘、充分共享和(hé)高效應(yīng)用,全麵係統地提高型號研製的科研水平,以利經驗(yàn)傳承和創新驅動(dòng),最終形成基於知識工程的產(chǎn)品(pǐn)創新、研發和生產體係。
3.薄壁難(nán)加(jiā)工材料製造
圖1 為某發動機機匣構件,材料為(wéi)奧氏體不鏽鋼難加工材料,牌號0Cr17Ni4Cu4Nb,最小壁厚為1.1mm,外弧麵要求輪廓度≯0.08mm,受變形因素影響,輪廓度(dù)超差,嚴重製約機匣(xiá)組(zǔ)件的裝配質量(liàng),造成安裝應力,影響到機匣組合件裝配及發動(dòng)機的效能。改善和控製薄壁環塊變形不單(dān)是生(shēng)產合格零件的需要,更是提升航空製造能力,提高航(háng)空發動機性能的先決條件。
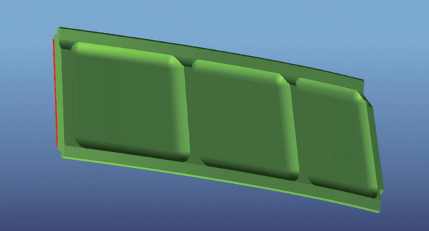
圖1 某發動機機匣構件(jiàn)模型
可通過以下工序滿足構件結構形狀要求:
(1)調整加工餘量。
(2)采用數控機床(chuáng)加工(gōng),調整、固化加工。
(3)改進零件裝夾方式。
(4)采取對(duì)稱銑槽加工。
(5)在銑加工型(xíng)槽之後增加穩定處理工序,改善二次加工應力。
4.先進的複合材料成型製造技術(shù)
樹脂傳遞模(mó)塑,即將幹態的(de)複合材料經過預(yù)定型,放入特定的模具中夾(jiá)緊,從設置的適當(dāng)注膠口在一(yī)定溫度、壓力下將配好的樹脂注入模具中,使(shǐ)之與增強材(cái)料一起固化成型的工藝方法。這是樹脂基(jī)複合材料應用較廣的工藝技術,起源(yuán)於20世(shì)紀50年代的冷模(mó)澆注,其發展(zhǎn)動力是為了使飛機雷達罩(zhào)的成型技術發展(zhǎn)起來。該工藝具有成本低、尺寸精度高的特點,對(duì)技術要求高,特別是對原材料和模具要求較高。
由於(yú)當時未能解決排除氣泡難、纖維浸潤性差、樹脂流動出現死角等製造技術問題(tí),限製了廣泛應用(yòng)。直至(zhì)20世紀90年代(dài),隨著對樹脂(zhī)傳遞模塑工藝及理論的研究,設備、樹脂和模具技術日臻完善,該工藝發展(zhǎn)成了複合材料(liào)行業低成(chéng)本成形工藝之一。與傳統(tǒng)的模壓工藝相比,可(kě)提高纖維(wéi)體含量,有助於樹脂對纖維(wéi)的浸漬,降低(dī)孔隙率,提高產品內在質量。
其工藝特點是(shì):
(1)分為增強材料預成型體成型和樹(shù)脂注射(shè)固化兩個步驟,具有高度靈(líng)活(huó)性和組合(hé)性。
(2)采用與製(zhì)品相(xiàng)近的增強材料預成型技術,纖維樹脂浸潤一經(jīng)完成即固化(huà),可用低(dī)粘度快速固化的(de)樹脂,並可對模具進行加熱而進一步提高生(shēng)產(chǎn)效率及(jí)產品質量。
(3)閉模注入樹脂的方式可極(jí)大減少樹脂有害成分對人體及環境的毒害。
(4)該技術采(cǎi)取低壓(注射壓力≯4kg/cm2)注射技術(shù),適宜大尺寸、外形複雜,表麵粗(cū)糙度低的製件。
(5)模具可根據生產(chǎn)規模要求選擇(zé)不同的材料,從而降低製造(zào)成本。樹脂傳遞模塑隨在國內(nèi)有許多單(dān)位在研製,但一直應用於等厚(hòu)度(dù)、等致密度的產品中去,其膠(jiāo)液的流動狀態和流速易保持一致,產品穩定性好。但對於各截麵(miàn)纖維厚度、致密度、密度變(biàn)化的諸(zhū)如複合材料葉片來說,複雜的內部結構應用樹脂(zhī)傳(chuán)遞模塑技術會造成膠液流動狀態和速率不一致,從而導致其生產工藝更為複雜,工藝難度(dù)增大(dà)。其關鍵製造技術:預成型體(tǐ)製造技術。
預成型體製造技術即預定型(xíng)是樹脂傳遞模塑前工序,其好(hǎo)壞(huài)影響(xiǎng)樹(shù)脂傳遞模塑注(zhù)射效果。大致可分為五種類(lèi)型:手工鋪層、紡織法、針織法、熱成型原絲(sī)氈法和預成型定向氈法。根據產品使用(yòng)要求,可使用不同的預(yù)製體。紡織體做成的預製體不(bú)存在層(céng)與層之間的界麵問題(tí),力學性能和熱學性能優良。該預製體要求具有疏鬆的組織結構,以便液態成型(xíng)時液態樹脂能夠順利地浸潤和浸透結(jié)構預製體。要使幹態複(fù)合(hé)材料結構預製體具有基本的自支撐性和形狀保持能力,利(lì)於預製體反複的鋪放和(hé)定(dìng)位要求,還要有反複變形的性質,製件見圖2。
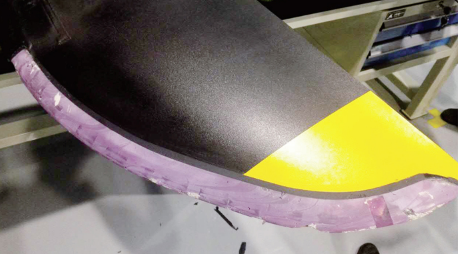
圖2 某複合材料製件
5.先進(jìn)的五軸行寬數控成型製造技術(shù)
航空發動機靜子葉片(piàn)為複雜異型(xíng)麵。起初,考慮加工變形影響,通過多次調整粗、半精、精加工方案,增加工藝過程中校形、人工時效等工序,試加工效果有所改(gǎi)善,但仍不能滿足設計要求。後通過五軸拋銑數控加工實現對其行寬最大化加工,優化加工路線,實現免拋光加工。
6.結語
航空發動機關鍵製造技術的應用,減少了人工幹預、人(rén)為出錯(cuò)的概率,克服了技術瓶頸。同時(shí),為(wéi)我國航空發動機發展提供了堅實(shí)的技術保障,實現了製造(zào)流程的規範化(huà)、自(zì)動化,提高了生(shēng)產效率及產品質量,勢必對(duì)我國未來航空發動機產業的發展起到推動作用。
來源: 世界(jiè)製造技術(shù)與裝(zhuāng)備市場
投稿箱:
如果您有機床行業、企業相關新聞稿件發表,或(huò)進行(háng)資訊合作,歡迎聯(lián)係本網編輯部(bù), 郵箱:skjcsc@vip.sina.com
如果您有機床行業、企業相關新聞稿件發表,或(huò)進行(háng)資訊合作,歡迎聯(lián)係本網編輯部(bù), 郵箱:skjcsc@vip.sina.com
更多相關信(xìn)息(xī)
業界視點
| 更(gèng)多
行業數據
| 更多
- 2024年11月 金屬切削機床產量數(shù)據
- 2024年11月 分地區金屬切削機床產量數據
- 2024年11月 軸(zhóu)承(chéng)出口情(qíng)況
- 2024年11月 基本型乘用車(轎(jiào)車)產(chǎn)量(liàng)數據
- 2024年11月 新能源汽車產量數(shù)據
- 2024年11月 新能源汽車銷量情況
- 2024年10月 新能源汽車(chē)產量數據
- 2024年10月 軸承出口情況
- 2024年10月 分地區金屬切削機床產(chǎn)量數據
- 2024年10月(yuè) 金屬切削機床(chuáng)產量數據
- 2024年9月 新能源汽車銷量情況
- 2024年8月(yuè) 新能源汽車產量數據
- 2028年8月 基本型乘用車(chē)(轎車)產量數據