汽輪機轉子末葉片銷孔加工裝置的設(shè)計(jì)與研(yán)究(上)
2017-7-4 來源:遼寧工業大學 作者:張晚青
摘要:位於(yú)汽輪機轉子各級葉輪的末葉片采用錐(zhuī)型銷孔鎖緊結構.由於每兩級葉輪間(jiān)的距離(lí)最小可達到 75mm,普通鑽床(chuáng)很難達到鑽孔要求。為了(le)提高加工效率,針對目前(qián)某公司的加工現狀,設計了一種新型的鑽孔裝置。新型的鑽孔裝(zhuāng)置主要由定位與夾緊裝置、進給(gěi)裝置、傳動裝置、平衡裝置等四部分組成。該裝(zhuāng)置在(zài)定位與夾緊部分(fèn)的巧妙設計使其在短時間內快速安裝完畢。通過(guò)人工手柄控製,實現工作台在(zài) X、Y、Z 方向的移(yí)位。平衡裝置能夠最大限度減少工人的(de)勞動強度,提高工作效率。 該鑽孔裝置利用“螞蟻啃骨頭”的加工方式將本身固定在汽輪機(jī)轉子上(shàng),並對(duì)末葉片(piàn)銷孔進行鑽孔加工。定位機構采用“一麵兩銷”的定位方(fāng)式,即平麵與一個圓(yuán)形銷和一個削邊銷配(pèi)合用以限製裝置相(xiàng)對轉子的位置;夾緊機構利用快速卡鉗和連接卡鉗與 Z向進給框架的連接架對(duì)裝置進行夾緊;進給裝(zhuāng)置的作用(yòng)是通過對 X、Y、Z 方向手柄的(de)轉動(dòng)來實現鑽孔裝置在(zài)這三個方(fāng)向的調位與進(jìn)給;傳動裝置是(shì)采用(yòng)帶傳動的傳動方式(shì)以3:1 的傳動比(bǐ)進行動(dòng)力傳動,以實現鑽頭的主軸轉動;平衡裝置的作用是使鑽孔裝置(zhì)近似處於無重力狀態,以確保鑽孔過程能夠平穩的進行(háng)。 運用(yòng)有限元(yuán)法對鑽孔裝置的部分(fèn)機構進行了分析,其中包括進給裝(zhuāng)置的 Y 向連接(jiē)架、Z 向進給裝置中連接錐(zhuī)齒輪的軸(zhóu)和梯形絲杠、以及夾(jiá)緊機構中的連接架等,並實施了優化設計。
關(guān)鍵詞:汽輪機;鑽孔(kǒng)裝置(zhì);快速(sù)夾緊;螺旋傳動;平衡裝置;有限元分析法
1.緒論
1.1 研究背景和研究(jiū)意義
1.1.1 汽輪機的分類及工(gōng)作原理
汽輪機是能將蒸(zhēng)汽熱能轉化為機械功的外燃回轉式原動機,是火電和核電的主要設備之一,用於拖動發電機發(fā)電來自鍋爐的蒸汽進入汽輪機後,依次經過一係列環形配置的噴嘴和動葉,將蒸汽的熱能轉化為(wéi)汽輪機轉子旋轉的機械能。它主要用作發電用的原動機,也可直接驅動各種泵、風機、壓縮機和(hé)船舶(bó)螺旋槳等[1]。還可以利用(yòng)汽(qì)輪機的排汽或中間抽汽滿足生產和生活上的供(gòng)熱(rè)需要。變速汽輪機還用(yòng)於拖動風機,壓氣機,泵及艦(jiàn)船(chuán)的螺旋槳等。在大型火電機組中還用於拖動鍋爐給水泵。就凝汽式汽輪機(jī)而言,從鍋爐產生的新蒸汽經由主閥門進(jìn)入高壓缸,再進(jìn)入中壓缸,再進入(rù)低壓缸,最終進入凝汽器。蒸汽的熱能在汽輪機內消耗,變為蒸汽的動能,然後推動裝有葉片的汽輪機轉子,最終轉化為機械能。除了凝(níng)汽式汽輪機,還有背壓式汽輪機和抽汽式汽輪機,背壓式汽輪機可以(yǐ)理解為沒有低壓缸和凝汽器的凝汽式汽(qì)輪機,它的出口(kǒu)壓力較大(dà),可以提(tí)供(gòng)給供熱係統或其它熱交換係(xì)統。抽汽式汽輪機則是指在蒸汽流通過程中抽取一部分用於供熱和再熱(rè)的汽輪機[2]。
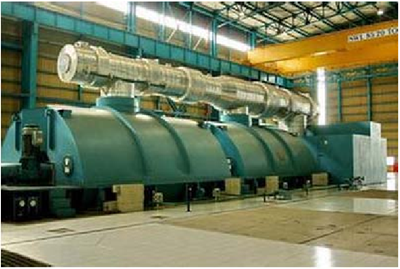
圖 1.1 汽輪機
汽輪(lún)機的轉子在汽輪機工作中承載著重要的作用,轉子通常用合金鋼整鍛,並加工(gōng)成(chéng)型。高壓轉子的一端的軸上安裝超速跳閘機構,並(bìng)安裝上主油泵。在此端(duān)還配有調速器,其連接方式是將剛性聯軸器和長軸對接在一起。轉子的尺寸均遵循加工圖紙的精度,精加工後的轉子需配置上其相應的葉片。為確保轉子的安全(quán)運行,帶著葉(yè)片的轉子需要做精(jīng)確的動平衡試驗和(hé)全速的轉動試驗。在轉子(zǐ)工作時,轉(zhuǎn)子上的工作葉片受到蒸汽對其的推動力,在推動力的作用下使其做回(huí)轉(zhuǎn)運動,作回轉運動(dòng)的部件還包(bāo)括主油泵,調速(sù)器(qì)和發電機。在工作時,葉片在高速氣流的推動下,將(jiāng)氣流的動(dòng)能轉化為葉片的機械能,進而(ér)推動葉片所在轉鼓和葉輪的高速旋轉。一(yī)般情況下,葉片的組成包括葉根,葉頂和葉型。葉根在葉片轉(zhuǎn)動時起到(dào)及其(qí)重(chóng)要的作用,葉片通過葉(yè)根連(lián)接在轉(zhuǎn)鼓和葉輪上,蒸汽(qì)的強大推力將葉片推動進行(háng)高速旋轉。因此,葉根與葉輪的連接牢固程度是決定轉子安全運轉的必(bì)要前提,當然裝配方便和加工簡單可以減(jiǎn)小工作強度和生產效(xiào)率[3]。
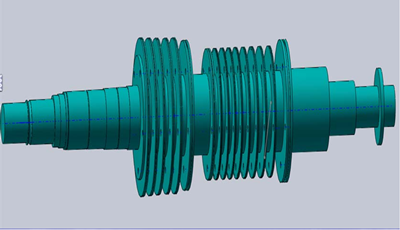
圖 1.2 汽輪機轉子三(sān)維圖
葉片的表麵(miàn)設計為複雜的曲麵,由於汽輪機的工作原理是完全通過葉片在高速氣流的驅動下工作,從而推動轉子的高(gāo)速轉動。在這種(zhǒng)高溫高壓(yā)的工作環境(jìng)下,葉片的工作狀態起到了(le)極其重要的作(zuò)用。這種惡(è)劣的(de)工作環境對葉片提出了更高(gāo)的要求,它不僅僅要求高強度,還要求(qiú)高(gāo)抗腐蝕性,高抗疲勞性(xìng)和較高的抗衝擊能力。汽輪(lún)機的葉片由於長期處於在高溫高壓(yā)的環境下,所以對(duì)其材料的(de)耐高溫性能的要求顯得更加重要。由於葉片的 T 型葉根是順著轉(zhuǎn)子的主軸上麵的末葉窗口滑動到轉子的輪槽中,因此,當汽輪(lún)機的轉子高速旋轉時,會產生(shēng)強大的離心力,而這些離(lí)心力主要作用在葉片的 T 型根(gēn)處,而(ér)且,每一級的葉輪上的末葉片都處在末葉的窗(chuāng)口的位置。所以,對末葉片的葉(yè)根鎖緊的牢固與否對轉(zhuǎn)子的正常工作起到了(le)決定性的作用。要是不采用合理的鎖緊方式,在高速(sù)旋轉中產生的離心力會造成葉片(piàn)脫離轉子,可能會產生重大的事故(gù),一方麵機器會遭受損壞,最主(zhǔ)要的是可能會致使工作(zuò)人員的傷亡。目前在汽輪機轉子末葉片上應用最廣泛的鎖緊方式(shì)是錐型銷孔鎖緊方式(shì)。這種鎖緊方(fāng)式(shì)的設(shè)計不僅使鎖緊牢固的程度加(jiā)強,同樣可(kě)以使(shǐ)其拆卸方便。這樣不僅保障了汽輪機轉子的正常工作,同時,保證在葉片受(shòu)損的情況下,方便(biàn)拆換。然而(ér)在加工過程中發現錐形銷孔加工難(nán)度很大,在這種情況下,研製(zhì)能夠(gòu)加工汽輪機轉子末葉片錐形銷孔的鑽孔(kǒng)裝置,具有重(chóng)大意義[4-6]。
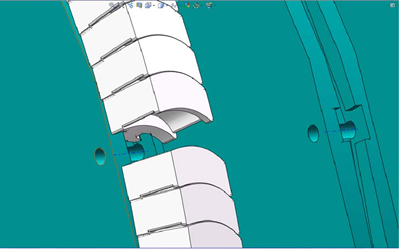
圖 1.3 汽輪機轉子末葉片及銷孔位置三維圖
1.1.2 課題來源及其研究意義
本課(kè)題來源自錦州汽輪機有(yǒu)限公司汽輪機轉子末(mò)葉片錐形銷孔鑽床(chuáng)的改(gǎi)進項目。汽輪機轉子葉片錐形銷孔的加工具有其特殊性,由於葉輪(lún)和主軸整鍛(duàn)為一體,葉(yè)輪之間的距離大(dà)小不(bú)同,最小的距離僅為 75 毫米,因此,這對鑽孔裝置的要求很高,銷孔加(jiā)工起來也比較(jiào)困難,一般的鑽床無法達到要求,這就要求研製一種特(tè)殊的鑽孔裝(zhuāng)置對汽輪機轉子的末葉(yè)片銷(xiāo)孔進行加工。
原有的鑽孔裝置裝於(yú)普通的車床上,利用(yòng)車床的溜板箱實現(xiàn)進給的換向和 X 向與 Z向進給,因此,鑽削末葉片(piàn)銷(xiāo)孔這道工序(xù)的一半以上時間用(yòng)於鑽孔裝置的定位,包括對水平(píng)度的定位和垂直度的定位,且加工精度低。新型末葉片錐形銷孔的鑽孔裝置是將其固定在轉(zhuǎn)子上(shàng)進行鑽孔,節省用(yòng)於定位所需要的大量時間,解決精度不(bú)高帶來的弊端。這台鑽孔裝置的研製不僅降(jiàng)低勞動成本,減輕了工人的勞動強度,同時,也可縮短整個加工(gōng)周期,提高生產效率。

圖 1.4 改進前的鑽孔裝置
1.2 汽輪機末(mò)葉片(piàn)鑽孔裝置的相關發展
範萬生[7]將鑽孔工裝首先裝於 DAK65 臥式車床(chuáng)的小刀架上適當壓緊。在裝鑽頭的空心軸內裝上(shàng)檢驗棒用以找正,在(zài) 80mm 長度上,千分表跳動小於 0.03mm,即可壓(yā)緊工裝。工裝的基木結構和(hé)傳動是:由(yóu)功率為 0.55kw 的電動機帶動皮帶(dài)輪(lún),通過一對皮帶輪減速傳動至(zhì)軸上(shàng),再經過三級齒輪減(jiǎn)速和傳遞(dì)運動(dòng)到鑽頭上,轉(zhuǎn)速由電動機的 1400r/min減為 60r/min。四個齒輪的模數為(wéi) 1.5mm。軸兩端采用銅襯套作軸承,支(zhī)承軸的旋轉運動。用擋圈作止推,齒輪(lún)齧合部位和軸承套(tào)的潤滑(huá)采用滴油潤滑。
張文華,張文慶[8]在研製(zhì)汽輪機轉子末葉片銷孔的加工裝(zhuāng)置中,使用折向鑽對(duì)轉子末葉片錐型銷(xiāo)孔進行鑽削。他們把折向鑽固定在(zài) C630 車床上,利用車(chē)床的手柄來實現折向鑽在 Z 向和 X 向的進給(gěi)。在進行 X 向進給時,同樣(yàng)向左或向右旋動 X 向的手柄,以使折向鑽位於 X 向目標位置。在進行 Z 向進給時,此(cǐ)時,實現(xiàn)的是折向鑽的鑽孔過程,向左或向右根據相應的(de)進給速度旋動 Z 向的手柄,直至(zhì)最後完成整個鑽孔過程。
目前,大多數(shù)的(de)汽輪機廠基本都在采(cǎi)用類似上述的鑽孔(kǒng)裝置,將鑽孔工裝安裝的車床上,以用(yòng)來(lái)對汽輪機(jī)轉子末葉(yè)片的銷孔進(jìn)行加工。
1.3課題的主要研究內容
(1)針對(duì)課(kè)題,初步確定各個機構實現其相應功(gōng)能的方案。主要包括鑽孔機構(gòu)需要通過“螞(mǎ)蟻啃骨頭”的方式將裝置固定(dìng)在轉子上,簡化了加工(gōng)工藝,節省了用於定位所需要(yào)的大量時間,可以有效提高加(jiā)工效率;由於不同轉子以及同一轉子各(gè)級葉輪的錐型銷孔的位置不同,故采用手輪搖動實(shí)現 X、Y、Z 三個方向的進給;通過平衡裝置來抵消由於自身質量產生的力和減(jiǎn)小力矩等。
(2)鑽孔裝置總體方案的製定。鑽孔(kǒng)機構由四部(bù)分組成,定位與夾緊(jǐn)裝置,進給(gěi)裝置,傳動裝置(zhì)和平衡裝置。構成鑽孔機構的各個部分的有機配合可以使機構更好的實現其(qí)鑽孔功能。
(3)鑽孔機構各(gè)個組成(chéng)部分詳細方(fāng)案的擬定,包括鑽孔機構與預加工零件(jiàn)的連接方式以及夾緊(jǐn)方式的設計與相關零件的選型,進給裝置(zhì)中傳動(dòng)方式的選取(qǔ)與相關零部(bù)件(jiàn)的選型(xíng),鑽孔工裝與電機連接的傳動方式的選擇與電機的選型,平衡裝(zhuāng)置的選擇(zé)及其與鑽孔機構的連(lián)接方式等。
(4)繪製設計裝置工程圖與(yǔ)工作原理圖。繪製零件圖和 Solid Works 三(sān)維圖並(bìng)對鑽孔(kǒng)裝置進行仿真。
(5)利用 ANSYS Workbench 有限元分(fèn)析軟件(jiàn)對(duì)鑽孔機構的部(bù)分機構進行強度和剛度分析與校核。通過分析,能對鑽孔機構的結構(gòu)設計(jì)和(hé)優化提供(gòng)依據,以便更好的檢驗設計的合(hé)理性。
2 .汽輪機轉子末葉片銷孔新型加工裝置的總體方案設計
2.1係統技術需求分(fèn)析
本(běn)次設計研究的課題是針對汽輪機的高中壓整體轉(zhuǎn)子的末葉片銷孔的加工裝置,利用五個平衡孔將加工裝置(zhì)安裝在體積和質量都巨大的轉子上進行加工。這台汽輪機轉子(zǐ)末葉片(piàn)錐型銷孔加工具體的技術方案和進(jìn)行結構設計之前,首先(xiān)對其技術需求進行分析:
(1)可以較(jiào)大地降低勞動(dòng)強度
汽輪機(jī)轉子末葉片錐型銷孔的原有加工裝置在(zài)工作過程中將一半以上的時間與工人的勞動強度用於對加工裝置的定位,在(zài)新的加工裝置的(de)設計上應采用合理的定位方式來提高勞動效率(lǜ),縮短勞動時間,簡(jiǎn)化工作流程。
(2)可以降低裝置的(de)製造成本
采用(yòng)傳統的機械傳(chuán)動方式,合理的連接(jiē)方式,以及盡量多的使用標準件,以降低整個的加工裝置的(de)製造成(chéng)本,使其具有良好的實用性和推廣性。
(3)采用較合(hé)理的鑽孔工裝的結(jié)構設計
汽輪機轉子末(mò)葉片錐型銷孔的所需要設計的加工裝置存在其特殊性,在轉子上分布著不同級別(bié)的葉輪,每兩級葉輪間的距離不完全相等,而葉輪之間的距離最小可達(dá)到75mm,一般(bān)的鑽孔工裝無法(fǎ)對其進行加工,故設計合(hé)理的鑽孔工裝結(jié)構對整個(gè)裝(zhuāng)置的設計顯得尤為重要。
(4)合理性與(yǔ)可行性分析
利用分析(xī)軟件對加工裝置的關鍵部件進(jìn)行合(hé)理性與可行性(xìng)分析,以確(què)保所設計的加(jiā)工裝置具有更好的(de)適用性(xìng)。
2.2 汽輪機轉子末葉片銷孔的加工現狀
本課題選自某公司,該(gāi)某公司目前加工汽輪機轉子末葉片錐形銷孔采(cǎi)用經改造的普通車床。將一套鑽具置於 CA6140 車床溜板箱上。其目的是利用溜板箱把光(guāng)杠和絲杠傳遞過(guò)來(lái)的(de)螺旋傳動轉化為溜板箱的直線進給。通過溜板箱的直線進給使鑽具做同樣的(de)進(jìn)給運動。簡而言之,車床在加工過程中是(shì)鑽具的承載者,帶著鑽具進行各方向的移動,以完成鑽具在鑽孔過(guò)程所需要完成的功(gōng)能。
溜板箱通常設有以(yǐ)下幾種機構:接通絲杠傳動的開合螺母機構。將光杠的運(yùn)動傳至縱向齒輪齒條和橫向進給絲杠的傳動機構,接通、斷開和轉(zhuǎn)換縱橫進給的轉換機構,保證機床工作安全的過載保險裝置,絲杠、光杠互鎖機以及控製刀架縱、橫向機動進給的(de)操縱機構。溜扳箱上有一個小齒輪。而小齒輪又與床身前下(xià)麵的齒條相齧(niè)合,可(kě)用手轉動溜扳箱手輪,可使床鞍縱向(xiàng)移動(dòng)。
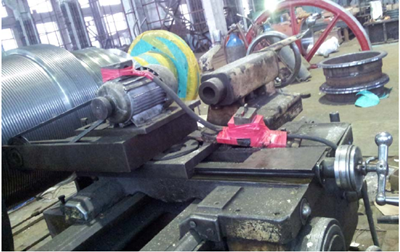
圖 2.1 車床(chuáng)及溜(liū)板箱
2.2.1 汽(qì)輪機末葉片銷孔加工裝置的(de)加工流程
(1)定位鑽孔裝置
將精加工後的轉(zhuǎn)子固定在兩(liǎng)個三角架上,三角架座(zuò)於水平度較(jiào)好的地麵。將鑽孔裝置用吊車(chē)將其置於轉子附近。
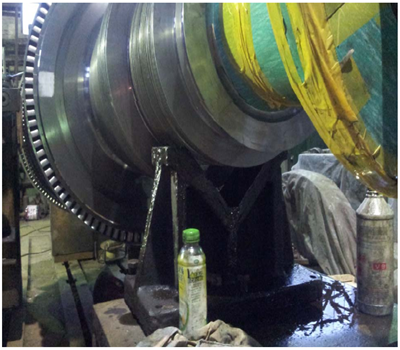
圖 2.2 精加工後的轉子(zǐ)固定在兩個三角架上
(2)確定水(shuǐ)平度與(yǔ)垂直度
將鑽孔裝置進行微調,使鑽頭與鑽孔位置重合。首先,調整鑽頭與預加工平麵的垂直度。調節垂直度(dù)是通(tōng)過移(yí)動整個鑽孔裝置來實現的。將百分表固定在鑽孔裝置上進行測量,當(dāng)測量結果不符合要求時,用撬(qiào)杠撬動鑽孔裝置進行(háng)微調(diào),直到達到要求為止,一般控製誤差在 0.05mm 以內。而後,調整鑽頭與鑽孔位(wèi)置的水平度。水平度的調節是通過(guò)千斤頂調(diào)節(jiē)轉子來(lái)實現的。將鐵棒穿在(zài)兩相鄰葉輪的平衡孔上(shàng),用千斤頂支撐鐵棒來進行調節。
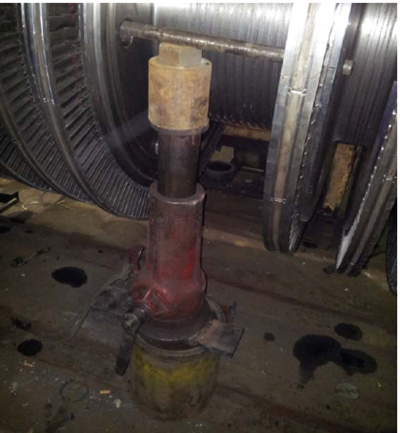
圖 2.3 千斤頂調節轉子水平度(dù)
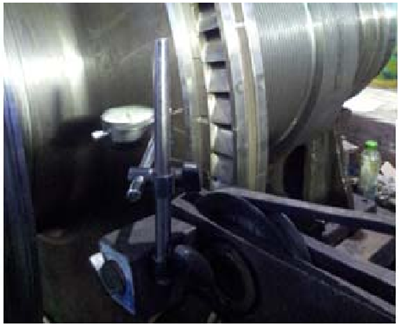
圖 2.4 用百分表測(cè)轉子垂(chuí)直度
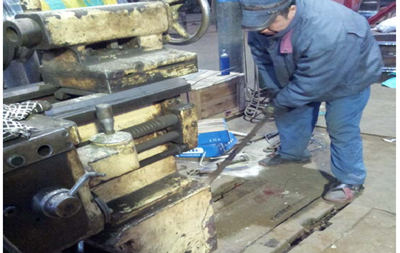
圖 2.5 工人用撬(qiào)杠撬(qiào)動鑽孔裝置進(jìn)行微調
(3)鑽孔
在完(wán)成校準鑽頭與鑽孔位置後,連接電源進(jìn)行鑽(zuàn)孔程(chéng)序。由電動(dòng)機帶動皮帶輪,通過 3:1 的(de)一對皮帶輪減速傳到(dào)鑽頭上,來進行(háng)鑽(zuàn)孔。
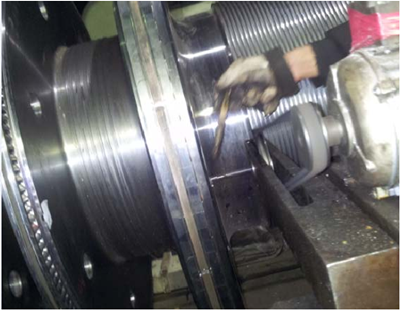
圖 2.6 工人用鑽(zuàn)孔裝置進行鑽孔
由於兩葉輪之間的(de)距(jù)離小,而葉輪的厚度大(dà),鑽孔(kǒng)的過程無法一次性順利(lì)完成,故在鑽頭加工到(dào)它所能加工(gōng)的最大(dà)深度後,將在鑽孔框架後麵的用來(lái)夾緊鑽頭的圓形螺母旋鬆,而後用卡鉗將鑽頭拉長至能鑽透葉輪長(zhǎng)度,再旋緊圓形螺母,接(jiē)通電機的電源線,旋動手柄實現進給,進行第二次鑽削。
在鑽直徑在 9mm 以上的(de)孔時,先用直徑 6mm 的鑽頭(tóu)鑽孔,而後用要求大小的鑽頭鑽削(xuē),由於圖(tú)紙要求(qiú)是(shì)錐形孔,用來插入錐(zhuī)形銷,故(gù)最後(hòu)還有鉸孔的一(yī)道程序。而這每一步的實現都不是一次性(xìng)完成,都需要進行第(dì)二次鑽削。
由於轉子的(de)長度至少是一個半車床長度,定位一次鑽孔裝置無法滿足鑽孔要(yào)求,因(yīn)此(cǐ)還要重複以上步驟。
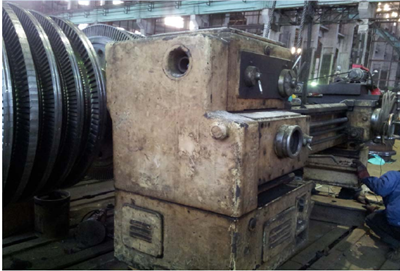
圖 2.7 轉子的長度約是 2 個車床長度(dù)
2.2.2 存在問題
目(mù)前各汽輪機廠所(suǒ)使用(yòng)的用(yòng)於加工轉子末葉片錐(zhuī)形銷孔的鑽孔(kǒng)裝置普遍采用齒輪傳動和將鑽孔工裝置於車床上,利用車(chē)床的工作台(tái)實現四個方向的進給,采用這種加工方式存在如下問題:
(1)將鑽孔工裝安裝在普(pǔ)通的車床上,通過移動車床來調節鑽(zuàn)孔(kǒng)裝置相對(duì)於轉子的垂直度和水平度,這種加工方式增加了(le)工人的勞(láo)動時間和勞動量(liàng);
(2)在調節垂直度和水平的過(guò)程中,無法保證其(qí)加工精(jīng)度;
(3)鑽孔裝置無法一次順(shùn)利完成整(zhěng)個鑽(zuàn)孔過程,需要將螺栓擰鬆後用卡鉗將(jiāng)鑽頭拉長到能夠將葉輪鑽透(tòu)長度,進行第二次鑽孔加工。
2.3 汽輪機轉子末葉片錐型銷孔新型加工裝置(zhì)的總體結構設計(jì)
在實際工作中,通常對汽(qì)輪機轉子末葉片銷孔的(de)配鑽精度要求較高,原因是(shì)葉片長(zhǎng)期處於一(yī)種高溫高壓且具有較強的腐蝕性(xìng)的工作環境中。汽輪機轉(zhuǎn)子葉片錐形銷孔的加工(gōng)具有其特殊性,由於葉輪(lún)和主(zhǔ)軸整鍛為一體,每兩級葉(yè)輪之間的距離大小不同,最小的距離僅為 75mm,因此,這對鑽孔裝置的(de)要求很高,銷孔加工起來也比較困難,一般的鑽床無法達到要求。
某公司原有的鑽孔裝置裝於普通車床上,利用車床的 X、Y、Z 軸(zhóu)充(chōng)當進給裝置,在車床定位時,用吊車進行移位,用撬杠等(děng)簡單工具進(jìn)行微調,因此,鑽(zuàn)削末葉片銷孔這道工序的一半以上的時(shí)間用於鑽床的定位(wèi),且精度(dù)低。新型鑽孔裝置的研製目的是對原鑽孔(kǒng)裝置進行優化設計,改進(jìn)後的(de)鑽孔(kǒng)裝置可以較大地提高生產效率。
改進(jìn)後末葉片錐(zhuī)形銷孔的鑽孔(kǒng)裝置采用“螞蟻啃骨頭”的加工方式將其固定在轉子上進行鑽孔,節省了用於定位所需要的大量時間,解(jiě)決了精度不高帶來的弊端。這台新(xīn)型鑽孔裝(zhuāng)置的設(shè)計,可以(yǐ)減(jiǎn)少勞動成本,縮短整個加工周期,同時可以提高生產效率。
2.3.1 總體結構設計與工作(zuò)流程
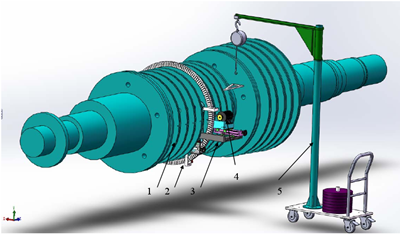
1-轉(zhuǎn)子(zǐ) 2-定位與(yǔ)夾緊裝置 3-進給(gěi)裝置 4-傳動(dòng)裝置 5-平衡裝置
圖 2.8 鑽孔裝置和轉子裝配總圖(tú)
該鑽孔裝置主(zhǔ)要包(bāo)括定位與夾緊裝置,進給裝置,傳(chuán)動裝置和(hé)平衡裝置(如圖 2.8所示(shì))。工作流程如(rú)下:
平衡裝置吊起鑽孔裝置,以減少工作人員的工作強度,使(shǐ)鑽頭調節到鑽孔位置高度(dù),並通過(guò)轉子上的平衡孔(kǒng)(如圖 2.9 所示)將裝置的定位在轉子上,用快速卡鉗將鑽孔(kǒng)裝置與轉子夾緊。調整 Z 向手柄,使鑽頭在 Z 向調節(jiē)到與劃線位置的水平位置附近,再調節(jiē) X 向手(shǒu)柄,使鑽頭在 X 向(xiàng)調節到劃線位置附近,而後依次調節 Z 向與 X 向,直到鑽頭隊準劃線位置,再用(yòng)鎖緊機構將 Z 向和 X 向(xiàng)分別進行鎖緊(如圖 2.11 和圖 2.12),以確保鑽孔過程的順利進行,至此鑽孔的前期工作已經完成。接下來(lái)的程序(xù)就是(shì)鑽孔(如圖 2.13 所示)。鑒於存(cún)在兩葉輪(lún)之(zhī)間距離小的情況(如圖 2.14 所示),鑽孔裝(zhuāng)置無(wú)法一次順利完成整個鑽(zuàn)削(xuē)過程,將固定鑽(zuàn)頭的螺栓(shuān)旋鬆後用卡鉗將鑽頭伸長到能夠將葉輪鑽透長度,進行第二次鑽孔,直(zhí)到完成通孔鑽削為止。而後逐個孔進行鑽削。轉子中的每(měi)一級葉(yè)輪與末葉片(piàn)的葉根所需配鑽(zuàn)的數目不一定相同,這需要按照圖紙的要求進行劃線後配鑽,一般一(yī)個末葉片配(pèi)鑽 1 個、2 個或 4 個銷(xiāo)孔,那麽一個葉輪需配鑽 2 個,4個或(huò) 8 個銷孔[9-12]。
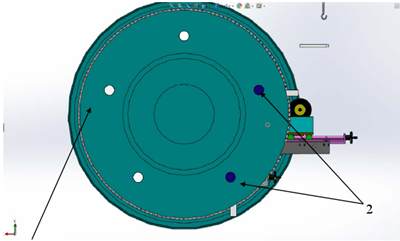
1-轉子上的平衡孔 2-用於固定鑽孔裝置的平衡孔
圖 2.9 轉子(zǐ)上的平衡孔位(wèi)置(zhì)
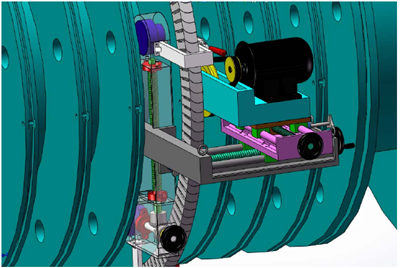
圖 2.10 鑽孔裝置機構總圖
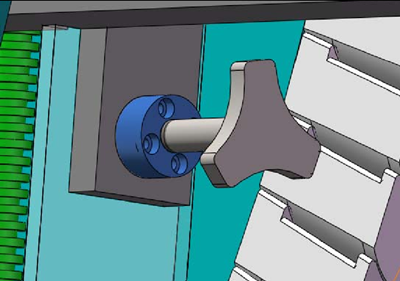
圖 2.11 Z 向梯形(xíng)絲杠鎖緊裝置
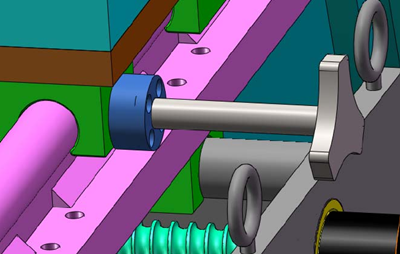
圖 2.12 X 向滾珠絲杠(gàng)鎖緊裝置
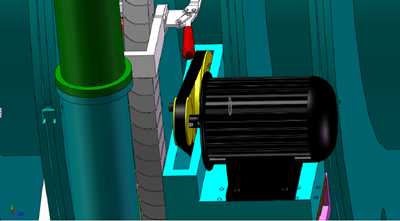
圖 2.13 傳動裝置(zhì)調節到鑽孔位置
每兩級葉輪之間的距離不完全相同,某些葉輪之間的距離較(jiào)小,這樣,鑽孔裝置無法一次性完成鑽削,如圖 2.14 所示,用(yòng)卡鉗將鑽頭拉長到(dào)已鑽削的長度後,再次鑽削,而後再觀察能否完成葉輪的通孔鑽削,以此類推,直至完成通孔鑽削。
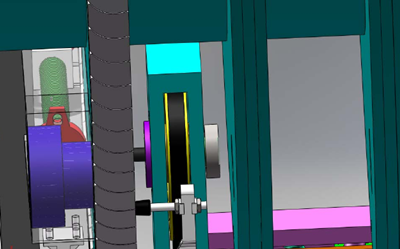
圖 2.14 某些葉輪之間(jiān)的(de)距離較小
工作流程圖如圖 2.15 所示。
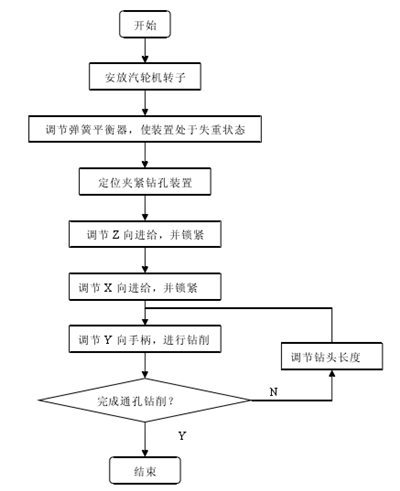
圖 2.15 新型鑽孔裝置的工作流程圖
2.3.2 鑽孔裝置(zhì)的機構設計
由於被加工件的質量和體積的巨大,用(yòng)更大的機床加工程序繁瑣,且消耗大量不必要的生產資源,故新型鑽孔(kǒng)裝置采用“螞(mǎ)蟻啃骨頭”的加工方式(即將鑽孔裝(zhuāng)置(zhì)固定(dìng)在工件上進行加(jiā)工),采用這種加工方式節省(shěng)了用於定位所(suǒ)需要的大量時(shí)間,解決了精度不高帶來的弊端。新型鑽孔裝置所采用定位和夾緊機構的巧妙設計,極大的提高了生產效率與加工精度(dù)[13,14]。
(1)定位與夾(jiá)緊機(jī)構的設計
定位與夾緊機構的設計包括定位機構設計和夾緊機構的設計。定位機構的設計是基(jī)於(yú)汽輪機轉子平衡孔的均勻分布進行設計的。汽輪機的轉子一般(bān)分布 5 或 7 個平衡孔,利用相鄰的(de)兩個平衡孔將鑽孔裝置(zhì)固定在轉子上。將銷子(zǐ)分別穿過鑽孔裝置(zhì)與平衡孔,在設計中,為了(le)避免兩個圓銷孔過(guò)定位,通常利用“一麵兩銷”的(de)定位方式,即設計定位元件一個為圓柱(zhù)銷,一個為削(xuē)邊銷。
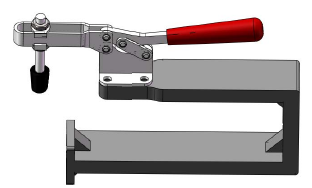
圖 2.16 快速卡鉗和連接架
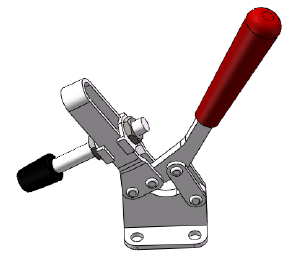
圖(tú) 2.17 快速卡鉗打(dǎ)開位(wèi)置
夾緊機構是將定位好的鑽孔裝置完全固定到(dào)轉子上,它(tā)的主(zhǔ)要組成部(bù)件(jiàn)是快速卡鉗和連接架,如圖 2.16 所示,圖 2.16 中的快(kuài)速卡鉗為鎖死位置(zhì)。快速卡(kǎ)鉗是利(lì)用(yòng)機械連杆機構中的死點原理,對預(yù)夾緊工件進行的一種快速夾持與打開的一種機構(gòu)。快速(sù)卡鉗具有定位準確,裝卸快速(sù),自鎖夾緊的功能。圖 2.17 所示(shì)快速卡鉗為打開位置。
(2)進給裝置的設計
新(xīn)型(xíng)鑽(zuàn)孔裝置的進(jìn)給裝置可以實現 X、Y、Z 方向進給,主(zhǔ)要包括螺旋傳動副,導軌和連接板等組(zǔ)成。Z 向進給裝(zhuāng)置的設計是在考慮其自身(shēn)重力的基礎上(shàng)進行設計的。雖然平衡機(jī)構能夠使鑽孔裝置處於無(wú)重狀態,但為避免操作不當或操作失(shī)誤所引起的危害,將螺旋傳動副(fù)設計為帶自鎖(suǒ)功能的梯形絲杠副。
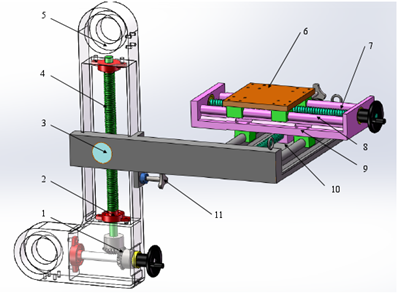
1-傘形錐齒輪 2-帶座軸承 KFL002 3-梯形絲杠螺(luó)母及連接螺母 4-梯(tī)形絲杠 5-Z 向進給框架 6-工作台連接板(bǎn) 7-X 向連接板8-導軌9-滑塊10-Y 向連接板11-鎖緊機構
圖 2.18 進給(gěi)裝置結構圖
(3)傳(chuán)動機構的設計
根據某(mǒu)公司原有的(de)鑽孔設備,該鑽孔裝置的傳動(dòng)機構同樣采用皮帶(dài)傳動的方式,以3:1 的(de)傳(chuán)動比進(jìn)行(háng)傳動(dòng)。由電機帶動主動輪進行轉動,主動輪通過帶與帶輪間的摩擦力將動力傳動到從動輪(lún),而後在從動(dòng)輪上安裝鑽頭對汽輪機轉子末葉片的銷孔進行配鑽。在(zài)現實(shí)生活中,皮帶輪憑借著簡便,高效並且可以緩衝,吸振,傳動起來平穩無噪音等優點,得到了更加廣泛的使用。因(yīn)此,本次設計(jì)沿用了原鑽孔裝置的帶傳動機構,如(rú)圖2.17 所示。
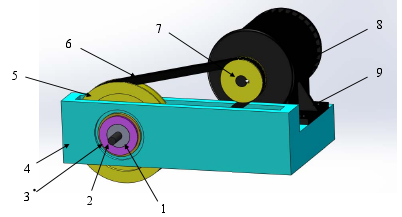
1-鑽頭套 2-軸套 3-外軸(zhóu)套 4-連接框架 5-從動輪 6-傳動皮帶 7-主動輪 8-電機 9-電機(jī)安裝架
圖 2.19 傳動裝置結(jié)構圖
(4)平衡裝置的設計
鑽孔裝置(平衡裝置除外)的自身重量在 50Kg 左右,為保證鑽削過程更加平穩精準,設計一款(kuǎn)平衡裝置,使加(jiā)工過(guò)程在(zài)無(wú)重的狀態下進行。平衡裝(zhuāng)置包括小型移動起重機和彈簧平衡器兩部分。小型移動起(qǐ)重(chóng)機由橫梁,立柱,車輪和配重片等組成(chéng)。為防止小型起重機發生側翻,加配重片以使(shǐ)裝置達到受力平衡(héng)。
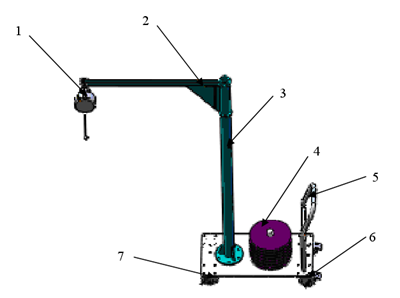
1-彈簧平衡器 2-橫梁 3-立柱4-配重片(piàn) 5-手柄 6-刹車後輪 7-小車前輪
圖 2.20 平衡裝(zhuāng)置結構圖
2.4本章小結
本章節通過分析汽輪機轉子末葉片銷孔加工(gōng)裝置的(de)技術需求(qiú)以及對現有鑽孔裝置加工流程及存在問題的分析,對汽輪機轉子(zǐ)末葉片銷孔加工裝置進行了總體結構設計,將設備劃分為(wéi)定位與夾緊裝置、進(jìn)給裝(zhuāng)置(zhì),傳動裝置和平衡裝置 4 個功能子(zǐ)部分,闡述和分析了各個功能子部分的工作(zuò)內容(róng)。
投(tóu)稿箱(xiāng):
如果您(nín)有(yǒu)機床行業、企業相關新聞稿件發表,或進行資訊合作,歡迎聯係本網編輯部, 郵箱:skjcsc@vip.sina.com
如果您(nín)有(yǒu)機床行業、企業相關新聞稿件發表,或進行資訊合作,歡迎聯係本網編輯部, 郵箱:skjcsc@vip.sina.com
更多本專題(tí)新聞
專題點擊前十
| 更多