螺旋銑削在數控銑加工中的運(yùn)用探究
2022-2-8 來源: 廣東(dōng)省(shěng)國防(fáng)科技(jì)技(jì)師學院 作者:林柔瑄
摘要:在數控(kòng)機床加工行業不斷(duàn)發展的(de)大環境下,數控機床的(de)形式和種類也越來越多樣(yàng)化,其中(zhōng)數控銑床就是常見的一種,在整個(gè)數控加工機床行業(yè)中發揮著(zhe)不(bú)可替代的作用。在數控銑(xǐ)削加工實際(jì)生產操作中,加工的零件產品要求越來越高,對產品的外形邊變化(huà)也(yě)越來越複雜,為了達到越來越嚴(yán)苛的要(yào)求,我們要深入的研究生產加工技術以達到我們預(yù)期(qī)的效果(guǒ),其中螺(luó)旋(xuán)銑削對提高(gāo)數控銑削的加工(gōng)效果有很大的價值。因此,為了更好地實現數控銑削,有效提高加工效率,有必要科學合理地應(yīng)用螺旋(xuán)銑削。
關鍵詞:螺旋銑削;數控銑加工;運用探(tàn)究
0、引言
經(jīng)濟的發展,離不開工業的發展,近年來我國經濟發展迅速,數控加工(gōng)技術的有力推動有著必不可少的因(yīn)素。現(xiàn)如今各行各業隻要涉及到機械加工的企業都離不(bú)開數控的身影,而數控機床的普及,也讓(ràng)加(jiā)工(gōng)生產變得更加(jiā)經濟和效率(lǜ),讓加工產品的精度也在不斷地提高。數(shù)控機床的種類很多,一般(bān)按照工(gōng)藝的形式可分為:數控車床、數控銑床、數控鏜床、數控磨床、數控鑽床、數控線切割機床等(děng)。在這我們就不一一贅述了。本文(wén)隻針對數控銑床中的螺旋銑(xǐ)削進行(háng)深入度探討和研(yán)究。
1、數控銑(xǐ)削加(jiā)工及螺旋銑削
數控銑床是一種可以進行產品外(wài)形加工的一種加工形式,他可(kě)以加工多種複雜樣(yàng)式的產品,能夠完成別(bié)的數控(kòng)機床不能完成的大部分(fèn)工作。它通過電腦計算機(jī)編程與機床自身的操(cāo)作係(xì)統一道,來(lái)完成的很多複雜的操作。
在加工過程中,首先要將準(zhǔn)備加工零件的毛坯件進行在工作台上的固定,然(rán)後選擇合適的銑刀,安裝就位後,通過程序預(yù)先設計好的編程程序,對零件進行加工。數控銑(xǐ)床一般加工產品上的曲線輪廓、直線、圓弧。孔、螺紋以及螺旋(xuán)曲線,尤其是一些人工所不能加工的(de)需要設備(bèi)輔助加(jiā)工的數學表達式給出的非圓曲線、列表曲(qǔ)線、空間曲麵等。這些工件看似(sì)形狀簡單,實則尺寸繁瑣,難以(yǐ)測量和觀(guān)察,有些孔和平麵要(yào)求的加工尺寸和(hé)精度而且還要求很(hěn)高(gāo),這
些數控銑床都能很好的完成。
在數控銑削過程中,就不得不說螺旋銑削,它是數控銑削加工過程中一項重(chóng)要的加工方式(shì),螺旋銑削的加工軌跡就像彈簧,在加工過程中刀具按照編程設計的運動軌跡進行螺旋(xuán)的進給,對加工工件進行逐(zhú)步的切削,已達到預期(qī)的尺寸。對於(yú)螺旋銑削,刀具的選擇很重要,一般來說根據工件的加工銑削(xuē)尺(chǐ)寸及螺旋半徑選擇大於刀具直徑的40%到 60%,當然也要看刀具的中心有(yǒu)多大的位置沒有切削刃,這對於刀具的切割壽命有很大影響,Z 軸也就是進刀尺(chǐ)寸的給定取正常切削的 20%左右,這也要看材料和實際加工確定,一般來說(shuō)螺旋銑削加工在下刀(dāo)的時候和走孔的時候用(yòng)的情況比較多,不過加工鋼件的時候(hòu)能不用就(jiù)不用了,因為對刀磨損太快,嚴(yán)重影(yǐng)響刀具的壽命。
在數控(kòng)銑(xǐ)削加工過程中,通(tōng)過螺旋銑削的應用,從而提高了設備(bèi)加工使用的優(yōu)化(huà),能夠跟好的滿足加工生(shēng)產的要求,而且在刀具(jù)的使用上,發揮出跟大(dà)的價值。分析研究螺旋銑削的加工工藝(yì)技術,合理的運用螺旋洗(xǐ)對輪廓、孔、螺(luó)紋等進行參(cān)數調(diào)整,研(yán)究出一套適合的加工(gōng)工藝。為數控技術發展,做更深層次的研究。
2、數控銑(xǐ)中螺旋銑削的的應(yīng)用
2.1 螺旋(xuán)銑(xǐ)削對工件外(wài)形輪廓銑(xǐ)削的作用
在數控銑床中,輪廓銑削一直是一項主要(yào)的銑削目的(de),在以往傳統的平麵加工過程中,機械加工的工作效率不是很高,而銑削加工(gōng)大大改善了這個問題,但在銑削過程(chéng)中,有一個重(chóng)要的(de)問題,那就是刀具在加工中,一般來說是旋(xuán)轉(zhuǎn)的刀(dāo)具(jù)相對於靜止的工(gōng)件進行加工(gōng),當銑刀在切削過程中(zhōng),如果刀具在高速(sù)旋轉狀態下,直接垂(chuí)直切削工件時,在進刀的過(guò)程中,會(huì)對工件帶(dài)來一個直接的衝擊(jī)力,這樣的切削方式,會對工件產生一定的損傷,而且直進的加工方(fāng)式對於刀具和機床的損傷也是不可忽視,長此以往,刀具的使用壽命會急劇降低,對機床的加工精度也會產生影響。為了減(jiǎn)少這樣(yàng)的情況的發生(shēng),螺旋銑削的出現也就得到了數控(kòng)銑床的的大量應用。螺旋銑削的應用大(dà)大改善(shàn)
了銑刀在銑削過程中所(suǒ)造成的幹涉問題。優(yōu)化了切削(xuē)路徑,切削的過程刀具進刀形式是一(yī)種沿著工(gōng)件輪廓螺旋(xuán)進給的一種方式進刀,螺旋進刀時刀具以螺旋線的方式運動,以此來避開刀具中心無切削力的的問題,它靠銑刀的側刃逐漸向下切(qiē)削從(cóng)而實現向(xiàng)下進(jìn)刀,這樣的進刀路徑,大大減少了刀具和工件的直接衝擊(jī),也讓加工的效率和加工的精度得到了提高。
螺旋進刀的關鍵是選擇刀具的直徑,切削最(zuì)大螺旋半徑、最小螺旋半(bàn)徑(jìng)、螺旋(xuán)進到角度。刀具的種類很多,外形(xíng)尺寸也很多(duō),根據具體的加工零件、加(jiā)工材料、加工尺寸、加工外形選擇(zé)合適的加(jiā)工刀具,一般有麵銑刀(dāo)、立銑刀、模具銑刀(dāo)等。最大(dà)螺旋半徑和最小(xiǎo)螺旋半徑是一個相對的概念,根據銑削工件形狀尺寸,確定最大(dà)螺旋半徑是為了更快更效率的切削工件,螺旋半(bàn)徑過大會影響切削時工件邊角的切削精度,可能會出現過切或者少切的情況。最小螺旋半徑是為了防止進刀時頂刀的(de),最小螺旋半徑(jìng)不能小於刀具中心無切削力部分的半徑,防止切削受力(lì)過大。進刀角度的確定也是一個很重要的因素,進刀角度過(guò)大會產生過大的端刃切(qiē)削力,角度過小側螺旋圈數又偏多,切削量偏少,切削時間過長,影響效率。所以切削(xuē)角度的確定還需要根據實際(jì)情況(kuàng),在不(bú)影響刀具(jù)使用壽命的情況下,經量增大切(qiē)削(xuē)角度,一般選(xuǎn)擇 5-15 度之間。
2.2 螺旋銑削對工(gōng)件螺紋加工的應用
說到螺紋(wén)加工,因為螺紋標準化的確定,所以在傳統的螺紋加工中大多數情況下都是用標準(zhǔn)的刀具對工件進行相對的旋轉切削運動。以此(cǐ)來完成螺紋的加工生產,此種形式生產的螺(luó)紋形狀基本能夠(gòu)達到使用要求,但是如果螺紋精度要求提(tí)高以後,這種傳統的螺紋生產加工方(fāng)法對操作工的技術要求,以及對設備精度的要求都要有明顯的提高,這(zhè)對於(yú)生產效益(yì)的影響還是提出了很高的要求。而且在螺紋加工中如果出現一些非標準的螺(luó)紋形式,這對(duì)傳統的車床(chuáng)就是一項很大的(de)挑戰。而對於應用了數控銑床的螺旋(xuán)銑削來說,這些問題都可以迎刃而解,螺紋銑削加工現對於傳統的螺紋加工(gōng),其加工的工件精度更改更高,加(jiā)工的廢品率更低,而且加工效率也比傳統加工有(yǒu)著明顯優勢。
如圖 1 所示在螺紋結構形狀以及螺紋旋向方麵(miàn)也不受傳統的限製,有時可以利用(yòng)一把螺紋銑削刀具完成多種形式的螺紋加工。在(zài)傳統(tǒng)的(de)螺紋加工中,螺紋(wén)加工件必須有過渡段或者退刀槽的形(xíng)式才能加工情況,在數控銑床中都可以很容易的減少此(cǐ)類工藝(yì)步序,直接加工螺紋,這樣的好處是減少了應力集中。而且螺紋(wén)銑刀加(jiā)工的螺紋工件耐用度也有很大的(de)提高,是(shì)一般絲錐(zhuī)板牙加工的螺紋的數十倍之多。數控螺紋銑削加工的優勢過(guò)於明顯,所以現如今對於很(hěn)多要求較高的工件螺紋式生產中(zhōng)銑削工藝得到(dào)極大的應用。
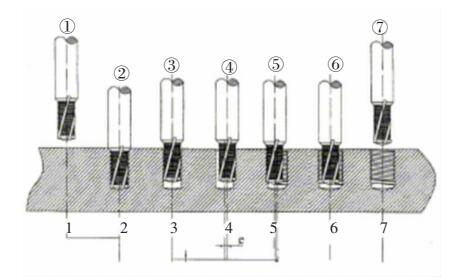
圖 1 螺紋加工(gōng)
2.3 螺旋銑削對工件孔(kǒng)加工的應用(yòng)
螺旋銑削在鑽孔來說(shuō),有著高效的加工能力,一般螺旋銑削鑽孔需(xū)要三軸同時運動,X 軸、Y 軸平麵運動,Z 軸做垂直旋轉運動,刀具圍(wéi)繞工件孔中心線做(zuò)螺旋運動。這樣的好(hǎo)處是增大了(le)銑削麵積,切削更(gèng)加快速,擴大了鑽孔尺寸,而(ér)且銑削出的孔表麵光滑,加工精度(dù)高,減少了一般鑽孔後精鏜(táng)表麵的工序,他的性能均超出麻花鑽、扁鑽、火焰切割、穿孔等技術。采用螺旋銑削,不(bú)論是在任何情(qíng)況下,加工刀具(jù)與加工工件之前都隻有很小的接觸麵積,所以需要的切削力相對(duì)於其他(tā)鑽孔工藝也小得多,而且螺旋銑削增加了材料切屑的(de)排出空間,減少了(le)碎屑和刀具以及孔壁的摩擦。而且空的尺寸是由數控編程(chéng)程序來確定加工的,所以孔的加工對於受刀具(jù)的選擇減少,從而降低了鑽頭的儲存(cún)要求。
鑒(jiàn)於數控銑刀的螺旋切削刃的幾(jǐ)何形(xíng)狀(zhuàng)的特點,銑刀可以切削(xuē)出筆直的側(cè)壁和一(yī)個 90 度角度的底(dǐ)部,這相對傳統的鑽孔(kǒng)工具,是不能夠做到的。對於一些大型模具加工的廠家,在(zài)加工大(dà)型加工件時,機床之間的(de)工件移動也是要消耗(hào)很多時(shí)間的,在一些(xiē)大型工件造打孔後需要對孔進(jìn)行精鏜,而這些工序可以在數控銑床上一次性完成。
不過在螺旋銑削孔加工中,冷卻方式也體現的至關重要(yào),因為(wéi)在(zài)銑削過程中,刀具在完成切削過程之前是沒有抬刀(dāo)動作的,所(suǒ)以切削產生(shēng)的鐵屑如果不能及時的叢孔中排出,就會對孔表麵造成劃傷,而且切削和刀具的(de)摩擦也會使(shǐ)刀具(jù)產(chǎn)生高溫,這會影響刀具的使(shǐ)用壽命,更有甚者會出現崩刀的可能。在孔加工過程中因為是冒孔狀態,故不能使用液冷(lěng),應該優先使用高壓氣體進行冷卻,這(zhè)樣能夠讓鐵屑及時排除,而且也對刀具起到了冷卻的作用。以上闡述都體現出螺旋銑削孔加工在加工產品中的(de)優勢,現(xiàn)如今,一些大型鍛造廠都采用了螺旋銑削來進行打(dǎ)孔加工,這極大提高了生產(chǎn)的工作效率,而且加(jiā)工精度也得到了極大的提高。
3、螺旋銑削在數控銑加工(gōng)中的優化發展(zhǎn)
螺旋銑削的應用讓數控銑削變得越來越不可或缺,它能夠代替很多的傳統的(de)加工工藝來更好地完成加工工件的生產。而為(wéi)了讓螺旋(xuán)銑(xǐ)削(xuē)能夠更好地(dì)服務於實踐生活,我們還需要不斷地加(jiā)強學習(xí)探索(suǒ)和改進。
3.1 選擇合(hé)適的切削方式
在很多銑削方(fāng)式中,螺旋銑削能(néng)夠(gòu)更好地完成加工生產,但是在社會不斷進(jìn)步(bù)發展的過程中,會出(chū)現很多不同形狀各異的加(jiā)工零件,這對於(yú)數(shù)控加工是一個挑戰(zhàn),在日常加(jiā)工中,我們要不斷摸索螺旋銑削中不同刀具選擇對不同材質的工件切削(xuē)過程,還有各種不(bú)同(tóng)工況下,如何合理選擇刀具,進給參數(shù),程序的改進,已達到(dào)用(yòng)最經濟的方式更(gèng)好地完成工件的(de)加工。
3.2 對數控加工螺(luó)旋銑削技術人員的(de)要求
螺旋銑削(xuē)加工在不斷應用和摸索過程中,對於數(shù)控機床的操作人員以及技術(shù)人員,都(dōu)要學會善於總結(jié),善於發現,善於嚐試。而且公司(sī)也要定(dìng)期對員工進行同行業先進技術的專業的培訓,隻有員工能夠充(chōng)分掌握螺(luó)旋銑削的加工方法,讓數控機床能夠充分地得到利用,以促(cù)進公(gōng)司乃至行業更好的發展。
4、結論
在目前(qián)的數控銑削過程中(zhōng),螺旋銑削得到極大的發展,我們要充分利(lì)用好螺旋銑削這一加工方法。在(zài)未來(lái)的數控技術發展的道路中,我們要(yào)不斷探索,積極創新(xīn),努力提升自己的專業技術水平,為(wéi)行業的(de)發展和社會(huì)的進步做出(chū)貢獻。
投稿箱:
如果您有機床行業、企業相關新聞稿(gǎo)件發表,或進行資訊合作,歡迎聯係本網編(biān)輯部, 郵箱:skjcsc@vip.sina.com
如果您有機床行業、企業相關新聞稿(gǎo)件發表,或進行資訊合作,歡迎聯係本網編(biān)輯部, 郵箱:skjcsc@vip.sina.com
更多相關信息
業界視點
| 更多(duō)
行業數據
| 更多
- 2024年11月 金屬切削機床產量(liàng)數據
- 2024年11月 分地區金屬切削機床產(chǎn)量數據
- 2024年11月(yuè) 軸承出(chū)口情況
- 2024年11月 基本型乘用車(轎車)產量數據
- 2024年11月 新能源汽車產量數據
- 2024年11月 新能源汽車銷量情況
- 2024年10月 新能源汽車產量數據
- 2024年10月 軸承出口(kǒu)情況
- 2024年(nián)10月 分地區金屬切削機床產量數據
- 2024年10月 金屬(shǔ)切削機床產量數據
- 2024年9月 新能(néng)源汽車銷量情況
- 2024年8月 新能源汽車產量數據
- 2028年8月 基本型乘用車(轎車)產(chǎn)量數據