核電冷卻泵泵體五軸數控加(jiā)工工藝研究(jiū)
2021-1-13 來源: 雲南機(jī)電職業技術學院校企合(hé)作(zuò)辦公(gōng)室實訓 作者:孫建明,黃曉明,朱蘭(lán),楊曉春,劉春美
摘要: 核電冷卻泵泵體是(shì)主回路係統中三大核心部件之一,泵體的製造加工精度(dù)對整體(tǐ)設備的運行安全有直接影響。為提高泵體的加工精度,提出用(yòng)五軸數控加工工藝加工泵體。分析泵體特征,應用尺寸中差建(jiàn)模,並設計專用夾具(jù)。基於遺(yí)傳算法,研究加工工藝及方法(fǎ),應用五軸聯動數(shù)控加工中心(xīn)完成核電冷卻泵泵體加工。解決了圓柱(zhù)倒(dǎo)扣麵、90°彎管(guǎn)管道、薄壁件等加工難題。
關鍵詞: 核電冷卻泵; 夾具設計; 中差建模; 五軸聯動
0 、前言
核電冷卻(què)泵泵體是主回路(lù)係統中三(sān)大核心部件之一,也是核島中的一級安全部件。泵在主回路係統(tǒng)中所起的作用相當(dāng)於人體內的(de)心髒,泵體負責將主(zhǔ)回路的冷卻劑完成熱循環,在反應堆輸出功率(lǜ)之前加熱反應堆裝(zhuāng)置。泵體(tǐ)內部管道必須銜接光順,以保證冷卻劑高效完(wán)成熱循環。
泵體(tǐ)的製造加工精度直接影響整個設備的運行安全。傳統的鑄造技術很難滿足核電冷卻泵泵體的使用功能要求,五軸數控加工技(jì)術在提高泵體(tǐ)內部管(guǎn)道表麵質量及精度方麵具有很大的優勢。五軸加工的主要優勢:
( 1) 通過調整刀軸矢量避免刀具、主軸與工件及工裝發(fā)生碰撞幹涉; ( 2) 刀具相對於加工工件(jiàn)的位置可以靈活調整,保證刀具切削時處於最佳姿態,有效提高(gāo)工件的表麵質量。因此(cǐ),五軸數控加工技術主要應用在航空、航天、水利水電、船舶、軍工等(děng)領域的核心產品製造。
1 、泵體分析
泵體工程圖如圖 1 所(suǒ)示,泵體主要(yào)由泵心、90°彎管、支(zhī)撐體組成。泵心(xīn)呈 R150 mm 倒扣麵,管道壁厚為 5 mm,並且要求管道內壁銜(xián)接光順、無明顯接痕,管道外壁 R4 倒角麵(miàn)光順。
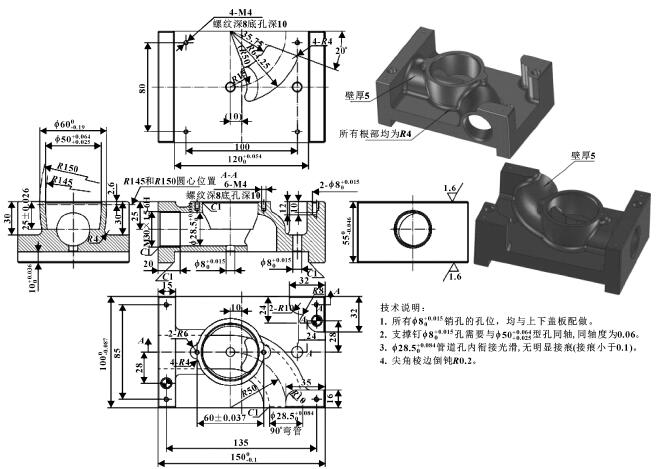
圖 1 核電(diàn)冷卻泵泵(bèng)體工程圖
加工難點:( 1) R150 圓柱倒扣麵,加工時需合理調整刀軸的角度及刀具切(qiē)削姿態,才能保證加工完(wán)成的倒扣(kòu)曲(qǔ)麵(miàn)表麵質量(liàng)及精度符合設計要求。( 2) 管道壁厚僅為 5 mm,要求設(shè)計合理(lǐ)的加工(gōng)工藝方案,保證(zhèng)薄壁加工不變形。( 3) 90°彎管(guǎn)內壁要求銜接光(guāng)順,內外壁曲麵呈均勻壁厚管道狀,應用(yòng) 3+2 軸、4+1 軸任意擺動刀軸(zhóu)均無法(fǎ)滿足彎管(guǎn)內(nèi)壁銜接光(guāng)順的(de)設計要求,必須(xū)應(yīng)用五軸五(wǔ)聯動加工工藝技術才能滿足加工設計要求。
2 、中差建模(mó)
按(àn)照設計人員的習慣建模方式,建模時都以(yǐ)對零尺寸建模,至於實際加工精度是否能夠滿足設計圖紙要求,主要取決於操作機床的工人能否依(yī)經驗調整刀具半徑補償(cháng)值。隨著現代技術不斷發展,機床生產廠家生產的數控機床定位精度已達到 0. 02 ~ 0. 05 mm級,發達國家生產的機床定位精度能夠達(dá)到 0. 005mm 級,機床控製係統也越來越(yuè)先進。通(tōng)過控製係統(tǒng)的補償,在刀具未磨損的情況下加工出來的產品都能(néng)夠達(dá)到圖(tú)紙要求。
編程工程師隻需(xū)嚴格按照中差建模及編程,機床(chuáng)運行加工一次,零件尺寸就能達到(dào)圖紙要(yào)求。
例如文中冷卻泵泵體尺寸 60+0-0. 19,如果建模時不計算尺寸中差,還是按對零尺寸建模(mó),加工完(wán)成的零件尺寸(cùn)偏(piān)大,操作機床的工(gōng)人需反複修改刀具半(bàn)徑(jìng)補償值並運行機床再加工,直到零件尺寸(cùn)符合圖紙要求為止(zhǐ),這種做法(fǎ)費時(shí)費力(lì)耗能,並且容易出錯。故中差建模是保證產品零件尺寸精度的關鍵。

3 、夾具設計
五軸聯動加工時(shí),工作(zuò)台 A、C 軸都要轉動,當(dāng)A 軸擺動角度大於等(děng)於 90° 時,工(gōng)作台(tái)與主軸容易發生碰撞。為了避(bì)免此(cǐ)類事故(gù)發生,工件(jiàn)裝夾時應抬(tái)高裝夾位置,需要設計五軸專用夾具來實現。根據EMCO LM600 五軸聯動加工中心工作(zuò)台直徑、主軸直徑,設計夾具。夾具安裝在(zài)工作台中心,充分利用五軸聯動機床的行(háng)程,同時保證 A 軸擺動角度大於等於 90°位置時,主軸(zhóu)與轉台(tái)保(bǎo)持一定的(de)安全距離。
工件(jiàn)裝夾示意圖如圖 2,L 代表 A 轉台直徑,L1代表最小安全間隙,L2代表主(zhǔ)軸半徑,H1代表三爪卡盤高度,H2代(dài)表夾具高度。經分析可得 H2計算公式。

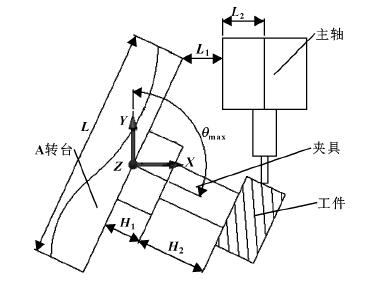
圖 2 裝夾(jiá)示意圖
為了(le)方便(biàn)裝夾及拆卸工件,設計如圖 3 所示的夾具,夾具上 3×8. 2 的通孔(kǒng)用於 M8 螺栓鎖緊工件。
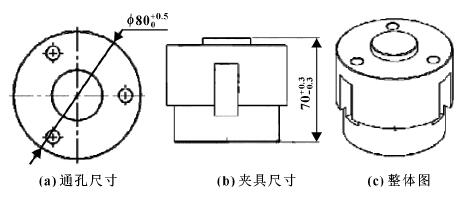
圖 3 夾具設(shè)計圖樣(yàng)
4 、加工工藝方案
4. 1 基於遺傳算法(fǎ)優化加工工藝
核電冷卻泵泵體加工有多種加工工序,一種加工工序有多(duō)個(gè)加工(gōng)策略,一個加工(gōng)策略又有多個加工參數。例如: 加工 28. 5+0. 084+0彎管外(wài)管(guǎn)麵工序有 4 種:
( 1) 先把(bǎ)外管麵粗加工、精加工到尺寸,然後再粗加工、精加工內管道; ( 2) 先粗加工、精加工內管道,再(zài)粗(cū)加工、精加工外管麵; ( 3) 先粗加工外管麵,然後粗加工內管道,再精加工外管(guǎn)麵,最後精加工內管道; ( 4) 先粗加工內管道,然後粗加工外管麵,再精加(jiā)工內管道,最後精加工外管麵。
精(jīng)加工外管麵時可以應(yīng)用 Power Mill 最佳等高精加工(gōng)策略,也可以應用 Power Mill3D 偏置精(jīng)加工(gōng)策略。加工工藝包括 8 個(gè)關鍵參數: 加(jiā)工工序、加工策略、切深 ap、切寬 ae、主(zhǔ)軸轉速 S、進給量 F、加工(gōng)時間、表麵粗糙度。應用遺傳(chuán)算法優化加工工藝,既能保證加工精(jīng)度和表麵質量又能縮短加工時間。遺傳算法優化加工工藝流程如圖 4 所示。
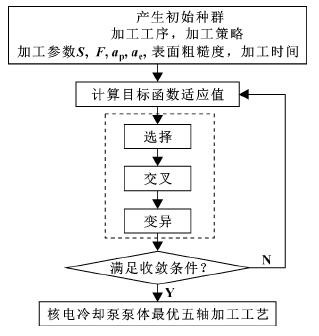
圖 4 遺(yí)傳(chuán)算法最優解(jiě)流程(chéng)圖(tú)
4. 2 加工策略
4. 2. 1 刀具(jù)選擇
選擇合適的刀具材料和刀具類型不僅可以提高(gāo)加工效(xiào)率,而且能夠保證零件的加工精度。刀具(jù)的選擇可遵循以下原則:
( 1) 粗加工時在尺寸允許(xǔ)條件(jiàn)下盡量(liàng)采用大直徑刀具,提高生產效率,降低刀耗。
( 2) 在保證產品零件尺寸的情況下,為使刀具有足夠的剛度(dù),其懸伸長度應盡可能短。核電冷卻泵泵體毛坯材料為 2AL2,屬於易加(jiā)工材(cái)料。在綜合考慮核電冷卻泵泵體的形狀、材料(liào)等各個方麵的(de)因素後所選刀具的參數如表 1 所示。
表 1 選用刀具參數
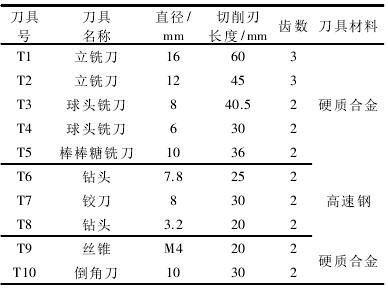
4. 2. 2 關鍵重(chóng)要工序過程
( 1) R150 倒扣型腔及彎管外(wài)管麵半(bàn)精加工粗加工後(hòu)外管麵留有大(dà)量台階(jiē)餘量,如圖 5 所示(shì)。
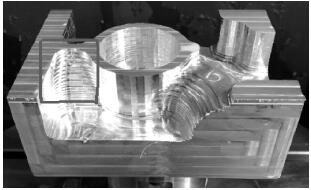
圖 5 泵體外管麵粗加工成(chéng)品(pǐn)
如果(guǒ)直接精加工(gōng),精加工餘量大並且不均勻,加工後的外管麵表麵質(zhì)量較差。應將外管(guǎn)麵大(dà)部分餘量除去後再進行精加工,去除(chú)大(dà)部(bù)分(fèn)餘量可以應(yīng)用模型殘留區域(yù)清除策略,也可以應用最(zuì)佳等高精加工策略(luè),還(hái)可(kě)以應用等(děng)高精加工策略。應用遺傳算法優化加工工藝後采用等高(gāo)精加工策略。優化後的刀路軌跡如圖 6 所示,提刀 301 次,加工時間 24 min4 s。
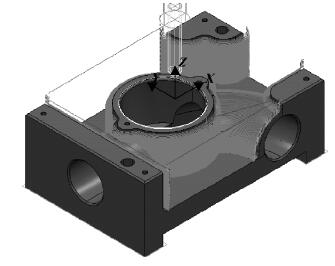
圖 6 優化後(hòu)的刀路軌跡
沒有優化前的刀路軌跡如圖 7 所示,提刀 781 次,加(jiā)工時(shí)間 50 min23 s。
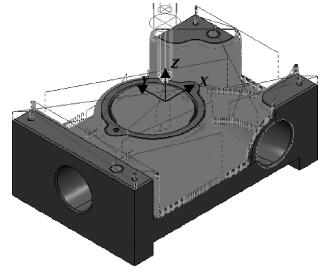
圖 7 優化前的刀路(lù)軌跡(jì)
( 2) 內(nèi)管道粗加工
為了(le)保證內(nèi)管道銜接光順,外(wài)管麵粗加工後加工內管道。如果外(wài)管麵精加工完成後再加工內管道,內管道加工時(shí)工件會產生振動,導致內部管道麵產生振紋,表麵不光順。粗加工內部管道麵應用 Power-Mill2016 等高精加工策略從兩端分(fèn)別加工,比應用(yòng)常規(guī)的模型區域清除策略開(kāi)粗加工節省時間 23 min50 s,減少提刀 89 次(cì)。
( 3) 內管道半精加工應用
Power Mill2016 管道加工策略(luè)半精加工內管道,其刀路軌跡(jì)計算有 2 種(zhǒng)方式:
①隻需設置(zhì)中心參考(kǎo)線,根據(jù)參考線(xiàn)的變化截取管道,完成刀路軌跡的(de)計算,這種方式適合截麵變化(huà)規律的管道; ②需要設置中心參考線、管道上下麵坐(zuò)標(biāo)係,根(gēn)據上下坐標係確定加工範圍,用平行(háng)等距(jù)的方式截取管(guǎn)道,中心參考線作(zuò)為刀軸的傾斜曲線,從而(ér)計算刀路軌跡,這種方式適合截麵變化不規律的管道。此次加工的管道呈90°,總(zǒng)長為 115 mm,通過刀路軌跡計算,測得有效切(qiē)削刃 95 mm 才能完成該管道加工,查閱山高刀具樣本,最長的棒棒(bàng)糖銑刀有效(xiào)切削刃為(wéi) 60 mm。由此可知,想用(yòng)一個加工策略完成整個管(guǎn)道(dào)加工是不可行(háng)的。仔細分析內部(bù)管道麵,有 65 mm 管道(dào)麵是直管道麵,應用 3+2 軸就能把該部分加工完成,為了(le)保(bǎo)證內部管道麵(miàn)銜接光順、無明顯接刀痕,計算直管加工(gōng)深度 W,W = 65-25+6+0. 5= 46. 5 mm。加(jiā)工部位及
刀路軌跡如圖 8 所示。
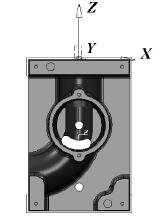
圖 8 3+2 直管加工(gōng)刀路軌跡
另一端長度為 64. 25 mm 的彎管麵應用 3+2 軸定軸加工(gōng),應用管道粗加工策略配合直徑 10 mm 的棒棒糖銑刀加工內管道彎管部位。中心參考線從管麵到型腔中心位置,軸向餘量為0. 35 mm, 行距為(wéi) 3 mm, 下(xià)切步距為 0. 3 mm, 刀軸方向為自動,傾斜角度(dù)為 15°,順序自末端均勻螺旋方式,快進高度為幾(jǐ)何形體安(ān)全區域方框,打開自動碰撞模塊,夾(jiá)持(chí)間隙為 0. 5 mm
,刀柄間隙為 0. 5 mm。刀路軌跡、中心參(cān)考線、加工位置如圖9 所示。

圖 9 彎管加(jiā)工參考線及刀路軌跡
( 4) 內管道精加工
內(nèi)管(guǎn)道加(jiā)工的精度影響到核電冷卻泵主回路係統冷卻劑的熱循環效率(lǜ),加工精度至關重要。長 46. 5mm 直管道麵加工應用等高精加工策略加工(gōng),3 + 2 軸定軸加工方(fāng)法,最小下切步距為
0. 9 mm,螺旋(xuán)下刀方式。
彎管部精加工有 2 種精加工策略:
①管道(dào)插銑精加工策略,適合加工管道內部截麵變化的管道; 管道螺旋精加工策略(luè),適合加(jiā)工(gōng)管道內部截麵一(yī)致的管道。文中加工的內(nèi)部管道麵屬於截麵一致的管道(dào),應用管道螺旋精加工策略加工,行距為(wéi) 5 mm、下切步距為 0. 3 mm、合並點為(wéi) 60,提刀(dāo)高度開始為 10mm,重疊為 8 mm,提刀高度為 0. 3 mm,打(dǎ)開自動碰撞 模 塊,夾 持 間 隙 為 0. 5 mm,刀柄間隙為 0. 5mm,刀軸方向為自動,快進高(gāo)度為幾何形(xíng)體安全區域方框,切入切出(chū)延伸(shēn)移(yí)動方(fāng)式,距離為 1. 5 mm。
( 5) 外管麵精加工外(wài)管麵精加工有 3 種加工策略:
①平行精加工策略; ②3D 偏置精加工(gōng)策略; ③最佳(jiā)等高精加工策略。平行精加工策略計算刀路軌跡的原理是計算出 2D 刀路,然後沿著(zhe) Z 軸方向投影到(dào)曲(qǔ)麵上,采用該策略計算(suàn)的刀路軌跡有一個弊端,如果加工的曲麵較陡,投影到該區域的刀路就稀疏,加工出來(lái)的曲麵(miàn)不光滑,刀路軌跡如圖 10 所示; 等高精加工策略計算刀路軌跡的原理是根據設定的下切步距把曲麵(miàn)按照(zhào)層切方(fāng)式分割(gē),得到曲麵加工刀(dāo)路
。
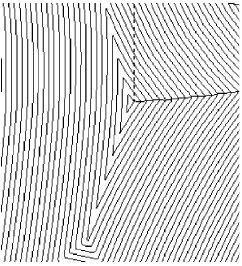
圖 10 平行精(jīng)加工刀路軌跡局部截(jié)圖
該策略計算生成的刀路軌跡隻能按照 U、V 方向(xiàng)排列,不能(néng)按照(zhào)彎管的彎曲率均勻生成刀(dāo)路軌跡,存在多處零點切削,加工後的管麵也不光(guāng)滑; 3D 偏(piān)置精加工策略計算(suàn)刀(dāo)路軌跡的原理是根據曲麵的法向線投影計算,計算生成的刀路軌跡無論是陡曲(qǔ)麵還是平緩曲麵行距均一致。設置參考線及參考線方向後,可以按照參考線方向計算生成刀路軌(guǐ)跡,這樣生成的刀路軌跡能有效減少刀具零點切削問題,加工出來的曲麵表麵質量較好,刀路軌跡及參考線如圖 11 所示。
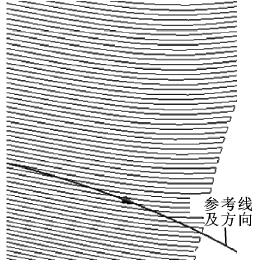
圖 11 3D 偏置精加工刀(dāo)路軌跡及參考局部截圖
( 6) 底部(bù) R4 倒角精加工中心型腔兩側(cè) R4 倒角呈倒(dǎo)扣(kòu)負角麵,需要旋轉工件把負角轉化為正角才能加工。
文中(zhōng)加工方法是通過新建編程坐標係來(lái)控製工件旋轉(zhuǎn)的(de)方向及角度,複製 G54 坐標係得(dé)到 G54-1 坐標係,該坐標係繞 X 軸旋轉 30°得到編程(chéng)坐標係。加工 R4 倒角負角麵應用清角精加工策略,按照默認的加(jiā)工策略計算生(shēng)成的刀路軌跡像縫衣服一樣加工倒角麵,如圖 12 所示。
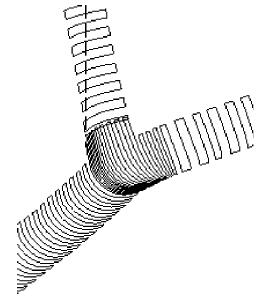
圖 12 縫衣式刀路
加工出來的倒(dǎo)角麵不光順,有一道一道的接刀痕。為了倒角麵光順,應改變刀路軌跡(jì)的加工方向,通過(guò)把清角精加工策略中的方式設置為自動方式,重新計算生成的刀路軌跡沿著倒角麵平滑走刀,如圖(tú) 13 所示。
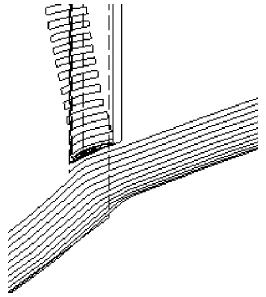
圖 13 光順式刀路
泵體(tǐ)左(zuǒ)右兩側(cè)支撐體 R4 倒角(jiǎo)麵應用原(yuán) G54 坐標係編程,加工存在 2 個弊端: ①刀具懸伸長; ②刀杆擦到已加工麵。刀具伸出夾持刀柄的長度(dù)要大於 30 mm,刀具伸出長度過長(zhǎng),切削(xuē)時刀具會振動(dòng)並存在讓(ràng)刀現象。切削(xuē)過程加工倒角特征(zhēng)的刀具直徑隻有(yǒu) 6 mm,直徑為 6 mm 的球體銑刀(dāo)有效切削刃隻有(yǒu) 18 mm,刀杆會把已加工(gōng)表麵(miàn)擦(cā)傷。
為了避免上述弊端,加工(gōng)兩側支撐體時均(jun1)要旋轉工作,讓刀具和刀杆與側麵呈5° ~ 10°角度,如圖 14 所示。
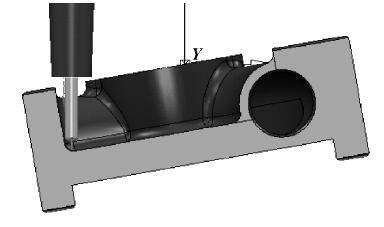
圖 14 刀具與側麵夾角示意圖
4. 2. 3 關(guān)鍵工藝參數
根據(jù)工序過程,分析零件各加工區域幾何特征,結合(hé)加工過程,應用(yòng)遺(yí)傳算法得到最佳(jiā)工(gōng)藝參數,如表 2 所(suǒ)示。
表 2 加(jiā)工工序及關鍵工藝參數
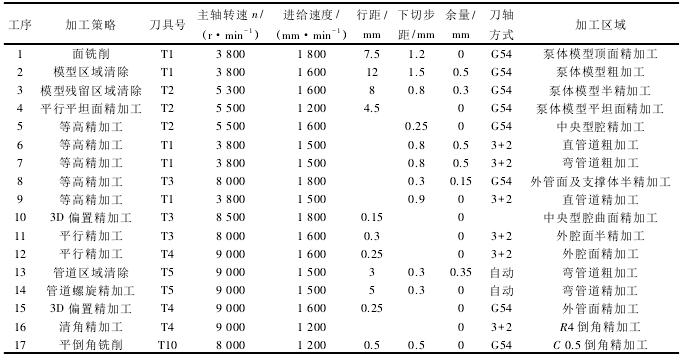
5 、五軸聯動加工
5. 1 裝夾方式
用三爪卡盤夾持夾具,然(rán)後用螺釘固定待加工的毛坯,如圖 15 所示。卡盤用 4 塊壓板壓緊在工作台上,卡盤壓緊固定前裝夾圓柱度小於等於 0. 005mm 的環規,用百分表校正三爪卡盤與機床工(gōng)作台軸心線 同軸度,調整(zhěng)三爪卡 盤(pán)位(wèi) 置,保(bǎo) 證 同 軸 度 在0. 02 mm 跳動範圍之內,如圖 16 所示。
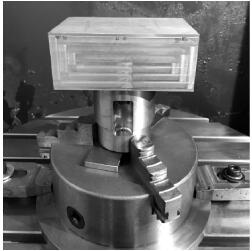
圖 15 毛坯裝夾
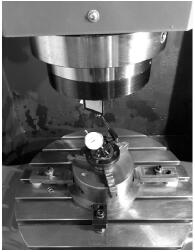
圖 16 校正三(sān)爪卡盤
5. 2 機床運行加工
嚴格按照刀具參數表表 1 夾持(chí)刀具長度(dù),按照刀具參數表序號依(yī)次把刀具裝入機(jī)床對應刀庫刀號。應用 EMCO LM600 定製後處理器,處理生成的刀位軌(guǐ)跡,轉化成(chéng) NC 程序。通過 DNC
把加工程序輸入機床控製係統,按照加工工序運行程(chéng)序,加工過(guò)程中注(zhù)意觀察。加工過程如圖 17 所示,加工完成泵體如圖 18 所(suǒ)示(shì)。
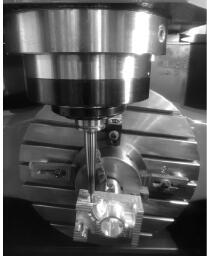
圖 17 五軸(zhóu)聯動加工過程
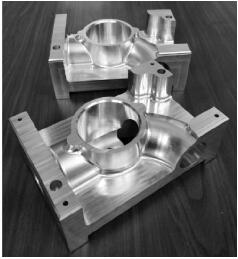
圖 18 產品(pǐn)零件泵(bèng)件
6 、結束語
核電冷(lěng)卻泵泵體作為(wéi)具有代表(biǎo)性的五軸(zhóu)加工零件,本(běn)文(wén)作者應用 Power Shape 2016 尺寸中差建模,Power Mill 2016 編程,應(yīng)用遺傳算法,獲得最優核電冷卻泵泵體加工工藝方法; 利用
EMCO LM600 五軸聯動加工中心加工完成(chéng),經 HEXAGON GLOBAL SDL07 10 07 三(sān)坐標測量機檢測,尺寸精度及表(biǎo)麵質量(liàng)均到達要求; 解決了圓柱(zhù)倒扣麵、90°彎管管道、薄(báo)壁件等加工(gōng)難題。該加工工藝可為企業生產,學員培訓提供參考。
投稿箱:
如果您有機床行業、企業相關(guān)新聞稿件發表,或進行資訊合(hé)作,歡迎聯係本網編輯部, 郵箱:skjcsc@vip.sina.com
如果您有機床行業、企業相關(guān)新聞稿件發表,或進行資訊合(hé)作,歡迎聯係本網編輯部, 郵箱:skjcsc@vip.sina.com
更多相關(guān)信息
業界視點(diǎn)
| 更多
行業數據
| 更多
- 2024年11月 金屬切削(xuē)機床產量數據
- 2024年11月 分地區(qū)金屬切(qiē)削機床產量數據
- 2024年11月 軸承出口情況
- 2024年11月 基本型乘用車(轎車)產(chǎn)量數據
- 2024年11月 新能源汽車產量數據(jù)
- 2024年11月 新(xīn)能源汽車銷量情況
- 2024年10月 新能源汽車產量數據
- 2024年10月 軸承出(chū)口情況
- 2024年10月 分地區金(jīn)屬切削機床產量數據
- 2024年10月 金屬切削機床產量數據
- 2024年9月 新能源汽車銷量情況
- 2024年8月 新能源(yuán)汽車產量數據
- 2028年8月 基(jī)本(běn)型乘用車(轎車)產量數據