微小顆粒對刀具測量精度的影響及誤差消(xiāo)除研究
2020-2-4 來源: 中北大學機械工程學院 作者:李曉男 曾誌強 王日俊 黨長營 等
摘 要: 為(wéi)了消除(chú)微小顆粒對刀具測量精度的影響,提出一種基於機器視覺的通過設定閾值和方向選定消(xiāo)除微(wēi)小顆粒的(de)方(fāng)法(fǎ)。首先,對刀具進行亞像素邊緣(yuán)提取(qǔ),通過(guò)設定閾值確定刀具邊緣,利用刀具(jù)邊緣和微小顆粒邊緣法線方向的不同(tóng),找出微小顆粒邊緣並對其快速有效的(de)消除。最後,在測量(liàng)係統上對該方法進行驗證。實驗結果表明,經過消除(chú)微小顆粒(lì)後的刀具(jù)測量精(jīng)度達到±0. 02 mm,且單次測量平均運行時間為 100. 76 ms,該(gāi)方法能快速有效地消除微小(xiǎo)顆粒對刀具測(cè)量的(de)影響,提高刀具的測量精度,能夠滿足(zú)刀具測量高精度的要求(qiú)。
關鍵詞: 微小顆粒(lì); 刀具; 機(jī)器視覺; 閾值; 法線方向; 高精(jīng)度
隨著我國(guó)提出中國製造 2025 製造強國的(de)目標,製(zhì)造業正在快速的發展,同時(shí)對於製造業(yè)的高精度、高效(xiào)率測量也越來越受到重(chóng)視(shì) 。基於機器視覺技術的刀具在線高精度測量技術是(shì)保證高精度製造加工的重要手段之一。然而,刀具的測量工作環境較惡(è)劣,測量(liàng)精度易受到工作環境中微小顆(kē)粒等因素的影響,這對高精度加(jiā)工製造就會因測量精度不足導致加工產品不(bú)合格,進而造成(chéng)較大(dà)的(de)經濟損失。因此,研究對微小顆粒的消除對高精度測量具有重要的工程意義(yì)和實用價(jià)值。H. H. Shahabi 等對采集到的刀尖(jiān)圖(tú)像進行中值濾波以及(jí)形態學開運(yùn)算處理,達到減少光線強度變化和降低粉(fěn)塵微小顆粒對刀尖(jiān)測量(liàng)精度影響的(de)目的 。
此算法能消除一定的粉塵(chén)微小顆粒的幹擾,但是對圖像(xiàng)進行形態學開運算會改變刀具邊緣的實際輪廓,使測量精度提高有(yǒu)限 。周洋利用霍夫變(biàn)換(huàn)和差分(fèn)逼近幾何法將刀具輪廓分為直線和圓弧,並進行了兩種方法的比較分析———把刀(dāo)具輪廓假設為直線-直線連接或直(zhí)線-圓弧連接兩種情況,證明了前者抗噪(zào)更強(qiáng),計算量更小。但是此方法假設過(guò)於理想化,不適合粉塵(chén)微小顆粒這(zhè)種形狀不(bú)規則性和提取的邊緣多樣性的特點。對於沒有采用微小顆粒消除技術的刀具檢測儀,一般測量者采取先擦試刀具後再測量,但是此(cǐ)方式也無法保證空氣中的粉塵再次附著,而且對刀具進行反(fǎn)複擦試會使測量效率(lǜ)大大降低。
針對上述問題,本文主要運用機器視覺圖像處理軟件 Halcon 並結(jié)合 . NET,采用圖像處理(lǐ)技術(shù),對(duì)圖像進行邊緣檢測,粉塵(chén)微小顆粒消除(chú)、邊緣(yuán)擬合等方法達(dá)到微小顆粒(lì)的最終消除。
1 、微(wēi)小(xiǎo)顆粒對刀具測量精度的影響
由(yóu)於(yú)加(jiā)工車間的環境(jìng)較為惡劣,空氣中常常會充滿粉塵,而且在刀(dāo)具加工過程中產生的切屑也極易附著於刀具表麵,這些微(wēi)小顆粒會對測(cè)量過程中刀具的邊緣(yuán)提取與邊緣擬合產生一定的幹擾。對於隻(zhī)附著在刀具表麵的切(qiē)屑的邊緣提取以及擬合,由於其灰度值和刀具的灰度值相近,對於小的離群點可以直接使用最小二乘(chéng)法擬合原理進行擬合,對於遇到較大的離群點或者擬合點的樣本數量不足(zú)這些情況時(shí),在使用(yòng)最小二乘法(fǎ)擬合原理的同時加入權重函數再進行擬合。
對於附著在刀具(jù)表麵的粉塵、切屑等微小顆粒(lì)而言,粉塵(chén)的灰度(dù)值較高且灰度分布不均(jun1)勻、範圍廣,如圖 1 所示,邊緣提取時(shí)會得到多段邊緣信息(xī),如圖 2b所示,若是直接使用附著切屑的刀(dāo)具(jù)的邊緣擬合方法(fǎ),會擬合出多條線段,如圖 2c 所示,無法有效獲得所(suǒ)需的刀具單向邊緣信(xìn)息,難以保證(zhèng)測量參數的精確性,甚至導致測量失敗。一般(bān)測(cè)量者(zhě)先擦試刀具後再測量,但是也無法保證空氣中的粉(fěn)塵再次附著,而且對刀具進行反複擦試會使測量效率大大降低。其(qí)中(zhōng)圖 2 是含有粉塵顆粒對刀具擬合的影響: ( 1) 含有粉塵微顆粒的刀具圖,如圖 2a 所示; ( 2) 提取出的亞像素邊(biān)緣,如圖 2b 所示(shì); ( 3) 擬合效果,如圖 2c 所示,其結果(guǒ)沒有擬合出(chū)刀(dāo)具單向邊緣(yuán),進(jìn)而影響後續的測量精度。
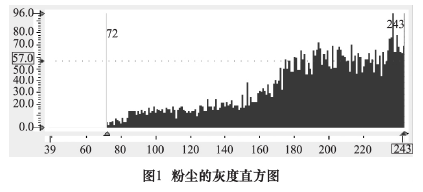
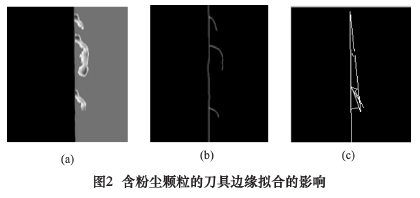
2 、消(xiāo)除微小顆粒的方法研究
為了達到消(xiāo)除微(wēi)小(xiǎo)顆(kē)粒的目的,本文采取圖像(xiàng)處理技術對微小顆粒進行消除。首先對(duì)刀具圖(tú)像進行(háng)邊緣檢測,分析微小顆(kē)粒(lì)邊緣特點,並引入相關概念,再根據消(xiāo)除微(wēi)小顆粒的原理對其進(jìn)行消除。此以處理附著微小(xiǎo)顆粒的平底銑刀圖像為例。
2. 1 邊(biān)緣檢測
Canny 算子是具有濾波、增強和檢測的多級優化算子 ,在圖像處理前,Canny 算子首先使用高斯平滑濾波器來平滑圖像以(yǐ)消除噪聲,Canny 分割算法使用有限的點並采(cǎi)用(yòng)一階偏導的方(fāng)法進行梯度(dù)幅值和方向(xiàng)的計算。在處理過程中,Canny 算(suàn)子還將經過一個非極大值抑製的過程,最後,Canny 算法通過設定兩個閾(yù)值來檢測邊緣,使其連續性更好。
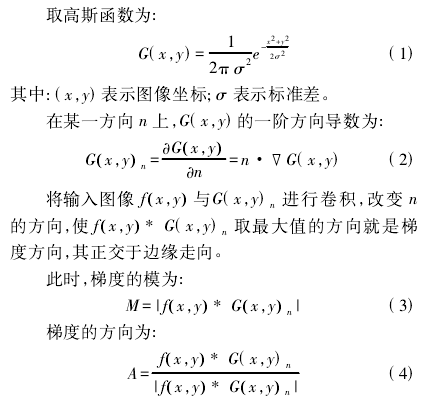
基於 Canny 算子對邊緣檢測的優點,本方(fāng)案選擇Canny 算子對刀具區域進(jìn)行亞像素級邊緣提(tí)取。
2. 2 微小顆粒(lì)邊緣的特點(diǎn)
基於對切屑等金屬微顆粒(lì)的可以直接使用最小二乘法並加入權重函數的方法進行邊緣擬合,故可以不進行消除。本文主要對(duì)粉塵微小顆粒的邊緣進行(háng)消除,通過對刀具圖像邊緣提取,提取的粉塵邊緣或者刀具邊(biān)緣的斷線此統稱為分枝,其類型(xíng)大概可(kě)以分(fèn)為以下 3 種情況如圖 3 所(suǒ)示:
( 1) 交叉邊緣,此刀具的邊(biān)緣與粉塵的邊緣出(chū)現交叉現象,如(rú)圖 3a 所示。
( 2) 噪聲點,由於(yú)噪聲在前期沒有完全(quán)消除,而導致邊緣提取後 的 圖(tú) 像出 現 點 狀的 噪 聲 點,如 圖 3b所(suǒ)示。
( 3) 斷線,由於光源角度等原因使粉塵中間段的灰度高(gāo)於兩端而造成(chéng)提取邊(biān)緣時出現斷裂,如圖 3c 所示,或者亞像素邊緣提取灰度閾值選取(qǔ)造成的刀具邊(biān)緣有斷裂,如圖(tú) 3d 所示。
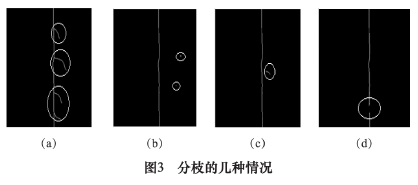
2. 3 消除分枝原理
通過分(fèn)析刀具亞像素邊(biān)緣圖像可知,基本上(shàng)所有的交叉邊緣在(zài)交叉點(diǎn)處和刀具邊緣的主幹都會成一個比較大的夾角(jiǎo),粉塵微小顆粒的斷線和噪聲點都偏離刀具邊緣主幹,而且邊緣(yuán)提取後由噪聲產生的邊緣也非常短。
基於此(cǐ)種情況,提出一種基(jī)於曲線追蹤技術的消(xiāo)除分枝的算法,其基本思想是: 利用閾值(zhí)選擇和刀具(jù)邊(biān)緣(yuán)和微小顆粒邊緣方(fāng)向不同原則,對微小(xiǎo)顆粒進行消(xiāo)除。首先通過設定閾值找出刀具邊緣的主幹,然後(hòu)在所有的交叉點和斷點處,消除與刀(dāo)具邊(biān)緣法向方向不一致的分枝,這樣(yàng)最後得到的就是具有(yǒu)單一連通性(xìng)的曲線,那些與刀(dāo)具邊緣方向不一致和(hé)小於閾值的分枝都會被消除。
2. 4 消除分枝過程
以處理平底銑刀的(de)其(qí)中一條邊緣為例(lì),消除分枝(zhī)的具(jù)體步驟如下:
Setp1: 首先設(shè)定一(yī)個長度閾值。
Setp2: 找到圖像中所有的分枝,如圖 4a 所示,並計算交叉點、端點和孤立點的個數(shù),如果沒有(yǒu)交叉點(diǎn)和獨立(lì)點且端點數不大於兩(liǎng)個,則不進(jìn)行消除分枝操作,退出。
Setp3: 如果交叉點隻有一個,計(jì)算各個分枝(zhī)長度,選取較長的一根作為主幹,然後計(jì)算主幹和(hé)各個分枝在交叉點處的法線方(fāng)向,保留與主幹夾角最小的分枝。
Setp4: 如果交叉點多於一個,計算各個分枝的(de)長度,先將(jiāng)長度小於閾值的分枝消除。
Setp5: 再次計算交叉點的個數,判斷(duàn)有無交(jiāo)叉點(diǎn),如果沒有,執行下步操作; 如果(guǒ)有一個,則重複步驟( 3) 操作; 如果還有多個,則重新設定閾值,重複步驟(zhòu)( 4) 操作,直至沒有交叉點為止,此時剩餘的部分應該就是主幹和斷(duàn)線、孤立點,如圖 4b 所示。
Setp6: 計算此(cǐ)時(shí)圖中的端點數,如果端點個數不多於兩個(gè),進行下步(bù)操作,如(rú)果多於兩個,則證明有斷線存(cún)在,然後計算與該端點相連的斷線在該(gāi)點處的法線方向,與主幹過(guò)此點的法線方向進行比(bǐ)較,保留與其方向最為接近的分枝。
Setp7: 清(qīng)除孤立點。
Setp8: 輸出結果,即輸出的就是消除粉塵微小(xiǎo)顆粒後的刀(dāo)具邊緣(yuán),如(rú)圖(tú) 4c 所示。
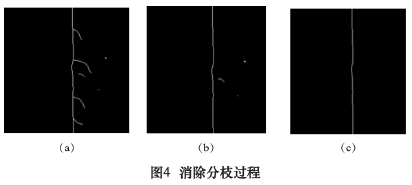
3 、實驗研究
3. 1 實驗平台搭建
為了驗證此算法能較好的消除微小顆粒,運用此算法並以刀具測(cè)量係統( 以下簡稱“檢測儀(yí)”) 中的刀具直徑測量為例進行驗(yàn)證。實驗平台的搭建如圖 5 所示。實驗平台主要包括銑床、被(bèi)測刀(dāo)具和檢測儀,其檢測儀主要包括照明係統、CMOS 工業相機、鏡頭、驅(qū)動部分、顯(xiǎn)示器(qì)以及微型計算(suàn)機等。照明係統實現對被測刀具的穩定、均勻照明; COMS 工業相機精確采集刀具圖像; 鏡頭的主要作用是將目標成像在圖像(xiàng)傳感器的光(guāng)敏麵上; 驅(qū)動部分主(zhǔ)要驅動照明係統(tǒng)亮度的調節;顯示器(qì)主要是圖像和結果的顯(xiǎn)示; 微型計(jì)算機(jī)主要做圖像的數字化處(chù)理。針對該係統(tǒng)要(yào)求選取如下硬件:相機選用 MV-EM 1200C 型相機,其 1 200 萬的像素在視場為(wéi) 5 mm×5 mm 時像素精(jīng)度可達 1. 5 μm; 鏡頭(tóu)選用清晰度高(gāo)、倍率可變、光學無畸變、高對比度的 BT-2216 型雙遠心鏡頭; 光源采用 OPT - RI9060 - W 型矩形光。
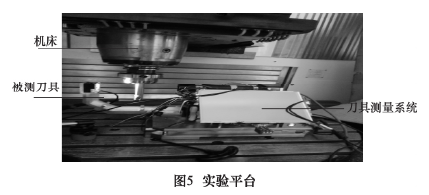
3. 2 圖像處理消(xiāo)除微小顆粒及實驗數據分析
其中利用檢測儀拍攝並選取含粉塵微小顆粒較多且顆粒較(jiào)明顯的平底銑刀圖像為例,利用 Halcon 軟件結合 . NET 和對其進(jìn)行相關(guān)圖像處理,獲得(dé)消除微小顆粒的圖(tú)像。圖 6a 為刀具原圖,b 為二值化後的旋轉刀具後的包絡圖像(xiàng),c 為利用 Canny 算子提取的(de)刀具以及粉塵微小顆粒的亞像素邊緣圖像,d 為消除粉塵微小顆粒分枝後的效果圖像,e 為直線擬合後的刀具邊緣圖像,f 顯示了消除粉塵微小顆粒後的結果在刀具包絡圖像中的位置。從這些(xiē)圖中可以看出(chū)此(cǐ)消除粉塵微小顆粒(lì)的算法,能較好(hǎo)地消除粉塵(chén)微小顆粒,獲得刀具的(de)單一連通邊緣。
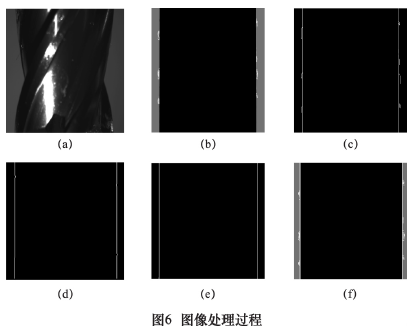
對於(yú)刀具幾何參數測量的(de)高精(jīng)度要求,利用本算法對(duì)獲取的刀具邊緣進行擬合(hé)後(hòu)進行一維(wéi)距離直徑測量。采用上述圖像處(chù)理方法,選取四幅含有較多且明顯的粉塵微小顆粒的平底銑刀圖(tú)像進行實驗,其直徑分別為 10 mm、16 mm、20 mm、32 mm,首先使(shǐ)用刀具視覺檢測儀測量( 刀具擦除粉塵等微顆粒幹淨後進行測量(liàng)) 的刀具直徑分別為(wéi) 10. 027 5 mm、16. 024 7 mm、20. 026 2 mm、32. 025 6 mm。為(wéi)了減(jiǎn)小誤差,本實驗對以上四種刀具(jù)分別進行 5 次測量,並且刀具直徑測(cè)量分兩種情況,一種是消(xiāo)除粉塵(chén)前的刀具直徑測量(liàng)數據對比結果如表 1; 一種是消除粉塵後的刀具直徑測量數據對比結果如表 2 所示。
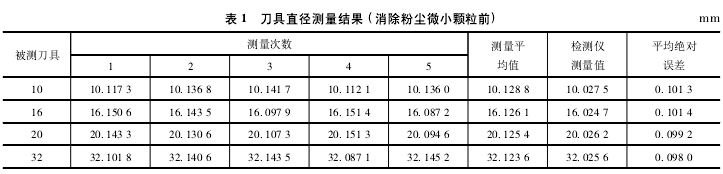
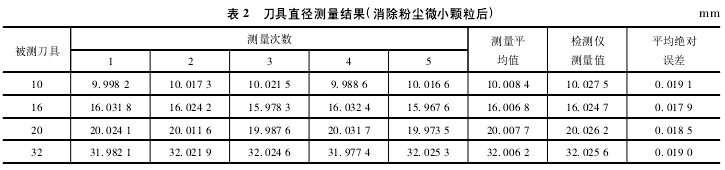
經(jīng)過兩組數(shù)據進行比較,消除粉塵微小顆粒前的刀具直徑(jìng)測量結(jié)果的平均誤(wù)差最大達(dá)到了 0. 101 4mm,誤差(chà)較大; 而運(yùn)用本算法消除粉塵(chén)微小顆粒後的刀具直徑測量結(jié)果(guǒ),其最大的平均絕對誤差為(wéi) 0. 019 1mm,測量精度達到(dào)±0. 02 mm,且單次測量平均運行時間為 100. 76 ms,運行效率(lǜ)比較高,可以較好滿(mǎn)足測量要(yào)求,對於圓(yuán)鼻刀、球刀等圓弧部分的微顆粒消除,此消除粉塵微小顆粒對刀具參數測量(liàng)精度影響的方法同樣適用。
4 、結語
本(běn)文從理論上分析了微小顆粒對刀具測量精度的影響,並在刀具邊緣擬合的過程中通(tōng)過消除分(fèn)枝算法對微小顆粒進(jìn)行消除。在高精度刀具測量(liàng)係統上對手動(dòng)擦(cā)除粉塵微小顆粒的檢測(cè)儀測量所得(dé)數據和(hé)使用本算法消除粉塵微小顆(kē)粒(lì)前後測量所得數據進(jìn)行了數據對比(bǐ)。實驗結果表明,測量精度達(dá)到±0. 02 mm,單次測量程序的平均運行時(shí)間為 100. 76 ms,該(gāi)方(fāng)法能快速有效地消除(chú)粉塵(chén)微小顆(kē)粒(lì)對刀具測量的影響,提高(gāo)了刀具測量的精度。
投稿箱:
如(rú)果您有機床行業、企業相關新聞稿(gǎo)件發表,或進行資訊合作,歡迎聯係本(běn)網編輯部, 郵箱(xiāng):skjcsc@vip.sina.com
如(rú)果您有機床行業、企業相關新聞稿(gǎo)件發表,或進行資訊合作,歡迎聯係本(běn)網編輯部, 郵箱(xiāng):skjcsc@vip.sina.com
更多相(xiàng)關信息
業界視點
| 更多
行業數據
| 更多
- 2024年11月(yuè) 金屬切削機床產(chǎn)量數據
- 2024年11月(yuè) 分地區金屬切削機床產量數(shù)據
- 2024年11月 軸承出口情況
- 2024年11月 基本型乘用車(轎車)產量數據
- 2024年11月 新能源汽車(chē)產量數據
- 2024年(nián)11月 新能源汽車(chē)銷量情況
- 2024年10月 新能源汽車產量數據
- 2024年10月 軸承出口情況
- 2024年10月 分地(dì)區金屬切削機床產量數據
- 2024年10月 金屬(shǔ)切(qiē)削機床產量數據
- 2024年(nián)9月 新能源汽車銷量情況
- 2024年8月 新能源汽車產量(liàng)數據
- 2028年8月 基(jī)本型乘用車(轎車)產量數據