高速切削GCrl5切削力的仿真(zhēn)與實驗研究
2017-1-12 來源:鄭州科技(jì)學院(yuàn)機械工程學院 作者:邱慧,班新星,紀蓮清(qīng),王明(míng)義
摘要(yào):應用Deform.3D軟件建立刀具一工(gōng)件三維有限元模型,研究(jiū)了PCBN刀(dāo)具高速切削GCrl5淬硬鋼的切削機理,得出不同切削參數下切削力的變化規律,通過對模擬結果進行分析獲得了最優(yōu)切削(xuē)參數。在最優切(qiē)削(xuē)參數下進行切削實驗,結(jié)果發現:在切削深度和(hé)進(jìn)給(gěi)量不變的情況下,不同切削速度下的切削力模擬值與實驗值(zhí)變化趨勢是一致的,並且其誤差不超過10%,這表明利用Deform-3D有限元(yuán)軟件建立三維切削模型可以有效模擬PCBN刀具高速切(qiē)削GCrl5軸(zhóu)承鋼的切削過程。
關鍵詞:有限元(yuán)模擬;高速(sù)切削;超硬刀具(jù);切削力
0.引言(yán)
聚晶立方氮化硼(Polycrystalline Cubic Boron Nitride,簡稱PCBN)作(zuò)為超硬(yìng)刀具材料,具有良好的耐(nài)磨性和熱穩定性?,普遍應用於淬硬鋼、冷硬鑄鐵及其它高硬黑色金屬的(de)高速切削加工舊J,並且隨著數控機床等自動加工設備的廣泛(fàn)應用,使用PCBN刀具以硬(yìng)態切(qiē)削替代磨削工藝已成為加(jiā)工淬硬軸承鋼的新途徑。GCrl5是一種最(zuì)常用的高鉻軸承鋼,經過淬火加(jiā)回火(huǒ)後具有較高的硬度,其硬度可達HRC60—62,主要應用於製作各種軸承套圈和滾(gǔn)動體(tǐ),屬於難加工材料行列Ho。近年來,國內(nèi)外很多學者對PCBN刀具(jù)高(gāo)速(sù)切削GCrl5的過程進行了研究分析(xī)p剖,主要集中在PCBN刀具的磨損機理、刀具幾何參數、GCrl5表麵粗糙度、切屑形成機理、殘餘應力、表麵白層等方麵,而(ér)針對PCBN刀具高速切削GCrl5切削力(lì)的研究較少。文中通過(guò)使用有限元軟件Deform.3D,係統(tǒng)研究了PCBN刀具高速切削GCrl5時削參數對切削力的影響,得到了切削力隨切削參數(shù)的變化(huà)規律,並通過切削實驗進行驗證。
1.材料(liào)與模型
1.1刀具(jù)材(cái)料
在硬態車削加工中(zhōng),由於低含量CBN刀具(jù)比高含量(liàng)CBN刀具擁有較(jiào)高的抗衝擊性能和刀具耐用度一],並且具有更好的加(jiā)工表麵質量,通常采(cǎi)用CBN含量較低(dī)的PCBN刀具(jù),其機械性能如下:彈性模量587GPa;密度4280kg/m3;泊鬆比0.15;比熱容750J/kg·℃;熱傳導(dǎo)係數(shù)44W/m·oC;熱膨脹係數4.7×10“/℃。本實驗所用的PCBN刀具幾何(hé)參數為刃傾角A,為0。,前角(jiǎo)7。為0。,後角僅。為6。,刃口鈍圓半徑(jìng)。為0.4mm。
1.2工件材料
高鉻軸承(chéng)鋼GCrl5具有高淬(cuì)透性,經熱處理後可獲得硬度為(wéi)62HRC,屬於典型的難加工(gōng)材料¨0l,其物(wù)理力學性能如下:楊氏模量217GPa;密度7850kg/m3;熔點1487℃;泊鬆比0.3;熱傳導係數39W/m·℃;熱膨脹係(xì)數(shù)14.4 X 10~/。C。
1.3材(cái)料(liào)的本構模型
目前,在應用計算機軟件進行模(mó)擬時,廣泛使用的本構模(mó)型是Johnson—Cook模型,它能夠很好的描述大部分金屬在大變形、高應變率和高溫條件下的材料本(běn)構行為,其表達式為(wéi):
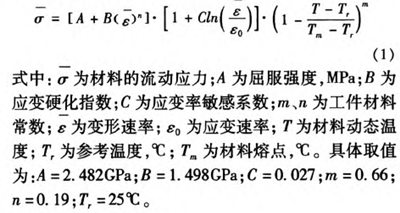
1.4材料的失效模型
Johnson—Cook模型以等效塑性應變作為材(cái)料的斷裂原則,提出以下材料失效模型:
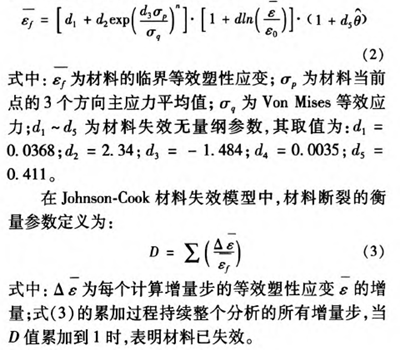
2.切削模(mó)擬
2.1切(qiē)削模擬參數(shù)選擇
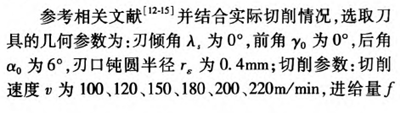
為0.05、0.10、0.15、0.20、0.25mm/r,切削深度口。為0.1、0.15、0.2、0.25、0.3mm。
2.2切削力模擬結果及(jí)分析
切削力是切削過(guò)程中重要的物理參數之一,它的大小(xiǎo)不僅影響加工工(gōng)藝(yì)係統,還影響著工件(jiàn)的加工質量(liàng)和加工精度¨6|。因此,研究加(jiā)工過(guò)程中切削參數對(duì)切削力的影響規律(lǜ),可以為高速切削加工中切削參數的選擇提供科學的理(lǐ)論依(yī)據(jù)。
在模(mó)擬過(guò)程中,切削力並非是穩定不變(biàn)的,而是(shì)在某一平衡值附近上下振(zhèn)蕩,這與實際(jì)切(qiē)削過程中切削力的變化是一致(zhì)的。造成(chéng)這種(zhǒng)現象的原因是,在實際切削中,隨著刀具剛接觸工件,材料會先產生彈性變形,接著工件材料內部的晶格進行滑移並發生塑性變形,此時切削力增大;隨著刀具的繼續前進,在切削(xuē)刃附近會出(chū)現應(yīng)力集中,當材料的金(jīn)屬剪應力超過強度極限時,切屑就被剝(bāo)離,此(cǐ)時切削力(lì)會相應隨之降低。此過程(chéng)周而複始,因次切削力曲線為一定範圍內的振動波,如圖l所(suǒ)示。將切削力以文(wén)本格式(shì)進(jìn)行輸出,然後求其均值即可得出模擬切削力大小。
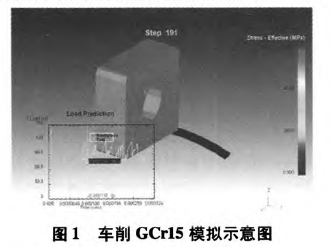
2.2.1切削速(sù)度對切削力的影響(xiǎng)
進給(gěi)量.廠和切削深度n。分別為0.05mm/r、0.1rain,切削速度與切削力之間的關係如圖2所示(shì)。切削(xuē)速度從100m/min增(zēng)加到(dào)220m/min,進給分力F,和徑向抗力F:變化非常小,上(shàng)下(xià)浮(fú)動大約(yuē)在1N左右,而主切削力F。的變化相(xiàng)對較大,最大浮動(dòng)達到11N。當切削速度從100m/rain增加到180m/min時(shí),進給分(fèn)力F,和(hé)徑向抗力t隨著切削速度的增加而略有增加,但變化並不是很明顯,上下浮動不超過0.1N;主切削力F。隨著切削速度的增加而增大,增大幅度達到7.2N,這主要是因(yīn)為主切(qiē)削力F,垂直於基麵,與切削(xuē)速度的方向一致。當切削速度從180m/min增加到220m/min,進給分(fèn)力t和徑向抗力t隨著切削速度的增加而略有減小,主切削(xuē)力F,隨著切削速度(dù)的增加而降低.
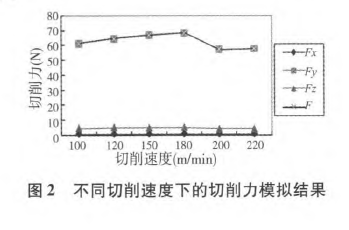
2.2.2進給量對切削力的影響
切削速度穢和切削深度a。分(fèn)別為(wéi)150re/rain、0.1mm,進給量與切削力(lì)之間的關係如圖3所示。進給分力t、徑(jìng)向(xiàng)抗力t和主切削(xuē)力t都隨著進給量的增加而增加,切削合力也隨著進給量的增加而增加在刀具切削時,三個切削分力中主切削力F,是(shì)最大切削分力,對切削(xuē)合力起(qǐ)主導作用,進給量廠的改變引起最大變化的切(qiē)削分力是主切削(xuē)力,所以進(jìn)給量,的改變也使得切削合(hé)力發生巨大變化。當(dāng)進給量(liàng)從0.05mm/r增至0.25mm/r時(shí),切削合力從66.8N增大到191.1N。3
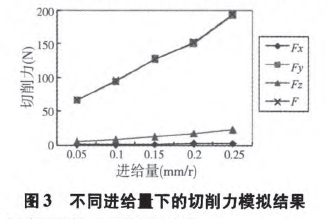
2.2.3切削深(shēn)度對切削力的影響
切削速度穢和進給量,分別為(wéi)150m/rain、0.1mm/r,切削深(shēn)度與切削力之間(jiān)的關係如圖4所示。切削深度%對切削力的影響最大,%每增加一倍,切削力也增大一倍。這是因為切削(xuē)深度a。增大,切削麵積A。成(chéng)正比增加,彈塑形變形總量及摩(mó)擦力增加(jiā),而(ér)單位切削力不變(biàn),因(yīn)而切削(xuē)力成正比增加。當切削深度從0.1mm增(zēng)加到0.3mm時,切削合力從(cóng)94.7N增加到283.5N,可見,在切削用量中,切削深度對切削(xuē)力的影響最大。
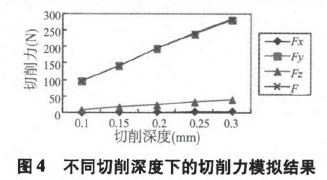
綜上所述(shù),從(cóng)模(mó)擬結果中可以看出,切(qiē)削深(shēn)度%對切削力的影響最大,進給量廠次之,切削速度移最小。切(qiē)削力隨著切削深度1/,。的成倍增(zēng)加而成正比(bǐ)增(zēng)加,這是因為切削深度a。增大,切削麵積(jī)A。成正比增加(jiā),摩擦力及彈塑形變形總量也(yě)相繼(jì)成正比增加;進給量廠對切削力的影響次之,切削麵積(jī)A。隨著進給量,增大也相應增加,但是其變形程度減小,致使單位切削力下降,因而切削力並不隨著,成倍增加而增加;切削速(sù)度(dù)口對切削力的影響最小,並且(qiě)在速度增加到一定程度時,切削力反而會相應減小,並趨於某一穩定值。為保證刀具的(de)耐用度及切削效率,加工GCrl5的工藝參數應選擇較高的切削速度、較小的切(qiē)削(xuē)深度和進(jìn)給量,推薦選取(qǔ):切削速度為150m/rain,切削深度為0.1mm,進給量為(wéi)0.1mm/r。
3.切削(xuē)實(shí)驗
3.1實驗參數及設備
實驗(yàn)刀具:采用鄭州博特硬質材料有限公司生產的PCBN刀具,刀杆使用45。偏頭外圓(yuán)車刀刀杆CSSNR2525—150,刃傾(qīng)角A;為0。,前角^y。為00,後角%為60,刃I=l鈍圓半徑0為0.4mm。加工工件(jiàn)GCrl5軸承鋼。切削參數:切削速度(dù)"分別為100、150、200m/rain,進給量廠為0.1 mm/r,切削深度o,為0.1mm。實驗設備:車床采用CA6240;測力係統采用瑞士Kisfler9257B三向測(cè)力儀。
3.2實驗結(jié)果及分析
切削過程中使用測力裝置獲(huò)得電信號,經過電荷放大器放大,並對信(xìn)號進行數據收集,最(zuì)後(hòu)通過(guò)利用D”o Software軟件對信號進行分(fèn)析處理,從而得出切削力數值顯示在(zài)計算機上(shàng),如圖5所示,將切削力數值以文本格式輸出,取(qǔ)穩態部分求均值即可得到(dào)切削過程中切削力的大小。
圖6顯示了模擬過程同實驗過程中切削力的對比情況,從對比曲(qǔ)線中(zhōng)可以看出,切削力模擬值與(yǔ)實驗值的變化趨勢是一(yī)致的,切削速度(dù)從100m/min增(zēng)加到150m/min,切削力也相應的增加,當切削速度為200m/rain時,切削力有所下降,這符合(hé)高(gāo)速切削的變化規律。比較切削力模擬值和實驗值可知,實驗值比模擬值(zhí)要大,不(bú)過,模擬值與實驗值的誤差不超過10%,究其原因是由於刀具磨損增大導致刀具角度改變造成的。在實(shí)際切削過程中(zhōng),由於GCrl5中存在大(dà)量的硬質顆粒,刀具磨(mó)損較大,使得刀具一切屑(xiè)接觸麵積減少,加(jiā)劇刀具的磨損,使刀具角度在較短切削時間內發生了很大改變,刀具變鈍,刀具前角增大,造成切削(xuē)過程中切削力的增大。
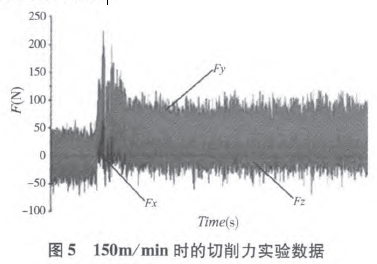
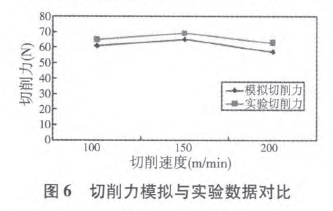
4.結論
通過(guò)對PCBN高速車削GCrl5過程進行模擬,得到了切削參數對切削力的影響規律和最佳(jiā)切削參數,同(tóng)時在最佳切削參數下進(jìn)行切削實驗,得到以下(xià)結論:
(1)應用Deform軟件建立三維(wéi)有限元模型(xíng)並對切削(xuē)過程進行仿(fǎng)真,得出(chū)切削(xuē)參數對切削力的(de)影響規律,發現切削力隨著切削速度、切削深度和(hé)進給量的增加總體上呈上升趨勢。
(2)通過對模擬結果分析獲得了PCBN刀具高速切削GCrl5最佳切削(xuē)參數(shù):切削速度為150m/min,切削深度為0.1mln,進給量(liàng)為0.1mln/r。
(3)切削(xuē)實驗表明,在切削深度和進給量不變的情(qíng)況下,不同切削速度下的切削力模擬值與實驗值(zhí)變化(huà)趨勢是一致的,並且其誤差不超過10%,進一步驗證了使用Deform軟件建立有限元模型並對切削過程進行仿真可以準確模擬C,Crl5軸承鋼的切削加工過程。
投稿箱(xiāng):
如果您有機床(chuáng)行(háng)業(yè)、企業相關新聞(wén)稿件發表,或進行(háng)資訊合作,歡迎聯係本網編輯部, 郵箱:skjcsc@vip.sina.com
如果您有機床(chuáng)行(háng)業(yè)、企業相關新聞(wén)稿件發表,或進行(háng)資訊合作,歡迎聯係本網編輯部, 郵箱:skjcsc@vip.sina.com
更多相關信息
業(yè)界視點
| 更多(duō)
行業數據(jù)
| 更多
- 2024年(nián)11月 金屬切削機床產量數據(jù)
- 2024年11月 分地區金屬切削機床產量(liàng)數據
- 2024年11月(yuè) 軸承出(chū)口情況
- 2024年11月 基本型乘用(yòng)車(轎(jiào)車)產量數據
- 2024年11月 新能源(yuán)汽車產量數據
- 2024年11月 新能源汽車銷(xiāo)量情況
- 2024年10月 新能源汽車產量數據
- 2024年10月 軸承(chéng)出口情況
- 2024年10月 分地(dì)區金屬切削機床產量數據
- 2024年10月 金屬切削機床產量數據(jù)
- 2024年9月 新能源汽車銷量情況
- 2024年8月 新能源汽車產量數據
- 2028年8月 基本型乘用車(chē)(轎(jiào)車)產量數據(jù)