提高汽車模具零件加工精度與效率的方(fāng)法
2017-11-27 來源: 四川宜賓普什模具有限(xiàn)公(gōng)司(sī) 作者:堯軍(jun1)
摘要:通過對加工工藝流程和裝配工藝(yì)流程的分析,找出影(yǐng)響汽車(chē)模具零件製作精度的因素,通過改善模(mó)具零件的裝夾方式(shì)、加工順序、加(jiā)工條(tiáo)件和(hé)優化裝配淬火流程,在保證單件加工尺寸精度(dù)的同時強調過程檢驗,以達到提高模具零件製作精(jīng)度的目的。
關鍵詞:等高墊鐵;淬火流程;過程(chéng)檢驗;模具零件
l 、引言
隨著汽車工業的飛速發展,對(duì)於汽車(chē)模具零件的加工精度要求越來越高,周期要求越來越短。為滿足模具零件加(jiā)工的要求,越來越多的(de)企業采用購買高精機床進行模具零件加工,但是從實際加工生產來看,加工的模具零件精度仍不能得到很好的保證,因此如何優化模具(jù)零件的加工工藝流程(chéng)顯得尤為(wéi)重要。
2、合理的加工工藝
模具零件加工受機床、切削力、溫度的影響,導致模具零件的加工質量及尺(chǐ)寸精度也受到影響,因此需要通過優(yōu)化加工流程來提高零(líng)件的加工精度。
2.1零件裝夾優化
模具零件裝夾的一般流(liú)程為:采用墊鐵安裝模具零件,保證墊鐵等高(同時平磨),將墊鐵分布到零件的四周,如圖1、圖2所示,然後(hòu)按操作流程進行模具零件的裝夾。
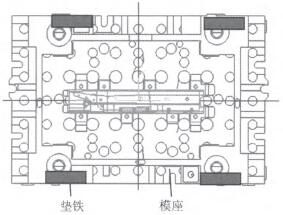
圖1模具零(líng)件尺寸<2m
加工時(shí)通常隻關注墊鐵是否等高,而忽略當墊(diàn)鐵擺到機(jī)床工作(zuò)台(tái)上時是否等(děng)高,由於機床工作台長期使用(yòng),有可能(néng)導致墊鐵放到點後而高度不一致,導致模具零件裝(zhuāng)夾不平。每次零件裝夾前應確認墊鐵擺到機床工(gōng)作台上後是否等高。
模具零件加工(gōng)後由(yóu)於切削應(yīng)力和熱變形,將會導致模具零件加工完後有變形,零件底麵與墊鐵接觸麵越(yuè)多,越能反映加工後零件的(de)平麵真實情況。試驗表明,4塊墊鐵(tiě)和(hé)6塊墊鐵導致的模具零件精度差在O.05 mm左右,模具零(líng)件越大精度差越明顯。
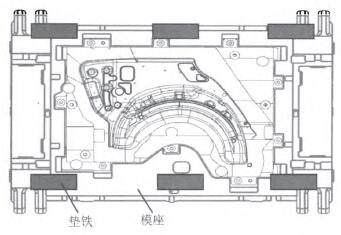
圖(tú)2模具零件尺寸>2 m
對於薄板類模具零件(如落料模模座(zuò))加(jiā)工前其自身(shēn)就會產生變形,即使對零件進行多次加工(gōng)仍可能(néng)無法保證底麵平(píng)整,裝好(hǎo)後始終會有一個角與接觸麵有間隙,對於這種(zhǒng)情況,再用機床加工來解決變形隻會增加製造成本。由(yóu)於模具零件最終是在機床上進行作業,上機床後工作狀態(tài)為直接將模具裝夾到工作台上(shàng),隻(zhī)要保(bǎo)證模具的裝夾狀態與(yǔ)機床的裝夾狀(zhuàng)態一致,就能保證其加工精(jīng)度。為此對於此類模(mó)具零件無法加工平整的,加工時保證其(qí)平麵度在0.3 mm以(yǐ)內,對於模具零件的裝夾,條件允許(xǔ)的情況下直接放在工作(zuò)台上更能保證其加工精(jīng)度。
墊鐵安裝好(hǎo)後就需要對模具零件進行校平(píng)找正(zhèng),為了能夠(gòu)快(kuài)速校平(píng)找(zhǎo)正(zhèng),可利(lì)用模具零件底平麵的十字鍵槽進行定位,製作定(dìng)位鍵,定位鍵的上端與模具零件的(de)鍵槽配(pèi)合,下端與機床工作台上的鍵槽或者T型槽配合,如圖3、圖4所示(shì)。
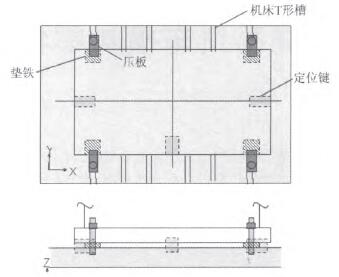
圖3 模具零件定位安裝樣圖
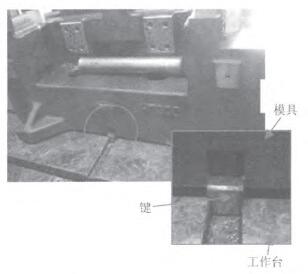
圖4模(mó)具零(líng)件(jiàn)定位安裝
相對傳統的手工校平(píng)方式,用定(dìng)位鍵自動校(xiào)平可提(tí)高約50%的裝夾效率(lǜ)。同時模具零件緊固從以往靠壓(yā)板與零件及工(gōng)作台之間的摩擦來限製模具零件的水平自(zì)由度,改為直接剛性限製其水平自由度,這樣能獲得更好的安裝效果。
2.2製作工序的(de)合理安(ān)排
對於零件加(jiā)工,最重要的是(shì)基準(即瓜,,、z基準(zhǔn)),基準的準確與否直(zhí)接影響模具零件的最終加工精度。Z基準即模具零件的底(dǐ)麵,考慮如何裝夾來應對模具(jù)零件(jiàn)的變(biàn)形,首先要考慮盡量減小或(huò)者消除零件自身(shēn)的變形(xíng)。一般模具零件底麵的製(zhì)作流(liú)程(chéng)為:①底麵粗加(jiā)工;②底麵壓夾槽、鍵槽等粗(cū)精加工;③底(dǐ)麵精加工,然後進(jìn)行正麵的一次加工,組裝後的二次加工。這樣的製作流程(chéng)消除了模具零件底麵由(yóu)於大(dà)餘量切削(xuē)產(chǎn)生的加工變形,但是加工應力和熱應力不(bú)能得到充分釋放,也(yě)就是後期模具零件(jiàn)還會有變形,同樣(yàng)會使得後期進行二次加工時Z基準平麵不平,經驗證,其變形量約O.2 mrrd2 m。一般模具零件一次加工完成後進入鉗工組(zǔ)裝(zhuāng)鑲件,然後再進行(háng)加工需要2~3天,在這過程(chéng)中模具零件也在進行自(zì)然時效,而模具零件(jiàn)的二(èr)次加工量很少(shǎo),對模座加工產生的應力很(hěn)小。因此隻要在(zài)二次加(jiā)工時先將底麵重新精光加工一次(cì),就能很好消除底麵變形產生的影響,保證模(mó)具零件z基準精度。
Z基準重新精光後(hòu),原來的從】,基準也會(huì)有相應的變化。在一次加(jiā)工時,基準孔做小一號(同樣按H7製作),二次加工時將其精加工到位,這樣能保證其精確。同時將精度要求高的導向麵、導向孔也安排在二次加工時精加工,以保證導向精度。
2.3 加工機床(chuáng)的合理使用
零件加工(gōng)時常會將粗加工機床和精加工機床分開,可以更好地保護(hù)機床。由於各種因素的影響,精/JnY-.機床的精度一般(bān)≤0.01 mm/1 m,重複(fù)精度一般≤0.006 mm/1 m,但是對於不同的機(jī)床(chuáng),有(yǒu)些(xiē)機床(chuáng)精度(dù)可能是0.01 mm/1 m,有些是一O.01 mm/1m,這樣同樣用於(yú)精加工的不同機床,其誤差就在0.02 mm/1 m。模具零件的(de)精度要求:型(xíng)麵+--0.05mm,導向孔±0.01 mm,導向麵±0.05 mm,也就是不同機床不能(néng)滿足導向孔的(de)精度要求。因此(cǐ)對於模具零件的(de)二次精加工,采用上、下模同一台機床加工更能保證(zhèng)其配合精度。
3、運用合理的裝配流程
裝配流程的優(yōu)劣(liè)直接影響(xiǎng)模具零件的製作質量和生產(chǎn)成本,因此在模具零件製作環節起著關鍵性的作用。模具零件的裝(zhuāng)配包括下模與凸模(mó)的組裝、上模與鑲件的組裝、上模(mó)與壓料器的組裝、斜楔(xiē)與模座的組裝等,這裏主要是淬火工序和組裝基準對模具零件(jiàn)精度的影響。
3.1淬火工序的合(hé)理安排
隨著模具(jù)零件製作技術的不斷(duàn)進步,淬火(huǒ)工序也在進行不斷優化,以鑲件淬火為(wéi)例,以往的淬火流程如表1所示。
上(shàng)述流程的優點(diǎn):能夠很好地保證鑲件(jiàn)之(zhī)間拚接,精加工時餘量均勻。缺點:組裝粗(cū)加工會增加加工(gōng)難度,整體(tǐ)型麵粗加工容易出現加工盲區,球刀粗加工時加工量大,對機床損傷嚴重,同時也增(zēng)加了模具零件在機床的占機時間,加工周期長(zhǎng)。優化後的淬火流程如表2所示。
優化後的加工流程優點:機床的加工時間(jiān)得到有效降低(隻有8 h),對加工效率提高具有很大的作用,節約了加工成本,後期鉗工(gōng)裝配時間也大大縮短,進一步縮(suō)短模具零件生產周期(qī)。缺點(diǎn):由於采用單件加工隻有單件基準,也就是會出現基準誤差,再加(jiā)上(shàng)鉗工的研(yán)配,會出現組裝後鑲件之間型(xíng)麵輪廓結(jié)合不好的情況,嚴重時沒有加工餘量,增
加了返修次數。要解決這一問題,首先要保證鑲件的一次加工質量,同時加工工藝充分考慮鑲件淬火前的加工餘(yú)量。
表1淬火流程
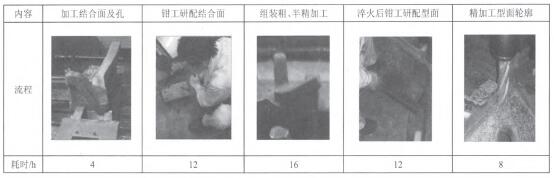
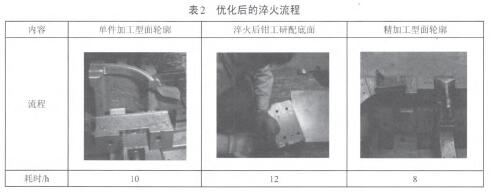
綜上所述,采用優化後的淬火流程能夠很(hěn)好地在保證零件加工(gōng)質量的前提下提高生產效率,這是目前廣(guǎng)泛采用的(de)加工方式。也並非所有的鑲件都適(shì)合先淬火後加(jiā)工,圖5所示的鑲件內圓角(jiǎo)R1 mm,由(yóu)於CNC加工(gōng)很難達到R1 mm的加工(一(yī)般到R2mm),導致加工完(wán)成後內圓角尺加工不到位,隻能留給鉗(qián)工(gōng)修(xiū)配,如果先淬火,勢必會增加鉗工(gōng)的修配難度,還會由於工具限製無法實現修配,此類鑲件適宜鉗工研配好後進行淬(cuì)火。
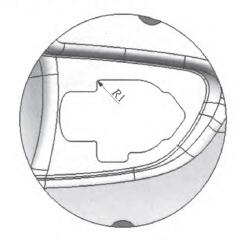
圖5車門(mén)板鎖口位置
3.2組裝工序的合理選擇
各零件組裝加工有利於保證整體模具的(de)製作精度,但影響模具的製作周期,如何保(bǎo)證(zhèng)零(líng)件加工精度需從工藝流(liú)程上對其進行優化。
一般在凸模(mó)基(jī)準側的壓料器和斜楔、整形壓料器都需要組裝加工,這樣能更好地保證基準精度。而對於其他壓料(liào)器和斜楔采用單件加工,能縮短加工周期。單件加工(gōng)會產生(shēng)基準累積誤差,導致模具零件精(jīng)度下降(jiàng)。壓料器、斜楔與模(mó)座一般都是采用(yòng)導板或導柱導(dǎo)向進行組合,以保證其組合精度。壓料器、斜楔其導向一般都是在背麵加工,而型麵在
正麵加工,因此就存在背麵和正麵的相對誤差,而且導向(xiàng)尺寸公差的不一樣,會產(chǎn)生直線誤差,這樣就使得加工完成後組裝到模座裏(lǐ)麵型麵不吻合。對於不組裝的壓料器、斜楔,在做正麵加工時需以背(bèi)麵導向尺(chǐ)寸類來確定基準,首先保證導向類尺寸公差一致,然後將(jiāng)其轉換到正麵,保證相對基準。
4、進行有效的過程檢驗
檢驗可以第一時間發現製作過程中加工零件的質量問(wèn)題,但是一(yī)般檢驗都是在模具零件加工完成下機後或者是(shì)鉗工裝配(pèi)完成後進行(háng),這樣雖然發現了(le)問題,但是沒能在第一時間解(jiě)決加工尺寸問題,會造成模具零件的返工返(fǎn)修。因此(cǐ)在模(mó)具零件製作過程中引入過程檢驗,在加(jiā)工過程中,對零件關鍵尺寸進行實時檢查確認,對沒有加工到位或者裝(zhuāng)配不合理的及時予以(yǐ)修正,保證其加工下機前零件合格,如圖6所示。
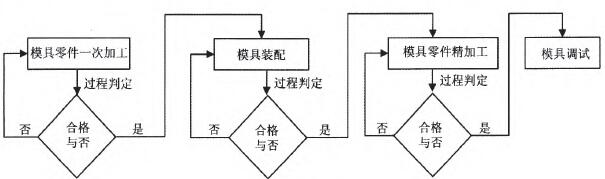
圖6過程檢驗流程圖
通過在加工製作的同時確認加工零件尺寸精(jīng)度,避免了重複上機床翻修,可大大降低返修時間(裝(zhuāng)夾、轉運、二次加(jiā)工找正等工(gōng)時消耗)。
5、結束語
影響模具零件加工(gōng)精度的因(yīn)素有很多,如操作技能等。隨著自動(dòng)化加工的(de)不斷深入,模具零件的製作采用機床全程序加工,同時將裝配工序細分,保證每一部(bù)位零件的裝配質量;並(bìng)且重視模具零件存放時的(de)擺放狀態,減小模具零件變形(xíng)對其精度的影響,更有利於模具精度的提高。
投(tóu)稿箱:
如果您有機床行業、企業(yè)相關新聞稿件(jiàn)發表,或進行資(zī)訊合(hé)作,歡迎聯係本網(wǎng)編輯部, 郵箱:skjcsc@vip.sina.com
如果您有機床行業、企業(yè)相關新聞稿件(jiàn)發表,或進行資(zī)訊合(hé)作,歡迎聯係本網(wǎng)編輯部, 郵箱:skjcsc@vip.sina.com
更多相關信息(xī)
業界(jiè)視點
| 更多
行業(yè)數據
| 更多
- 2024年11月 金屬切削機床產量數據
- 2024年11月 分地區金屬切削(xuē)機床產量數據(jù)
- 2024年11月 軸承出(chū)口情況
- 2024年11月 基本型乘用車(轎車)產量數據
- 2024年(nián)11月 新能源汽車產量數據
- 2024年11月 新能源(yuán)汽車銷量情況
- 2024年10月 新能源汽車產(chǎn)量數據
- 2024年10月 軸承出口情況
- 2024年10月 分地區金屬切削(xuē)機床產量數據
- 2024年10月 金屬切削機床產量數據
- 2024年9月 新能源汽車銷量情況
- 2024年8月 新能源汽車產量數(shù)據
- 2028年8月 基本型乘用(yòng)車(chē)(轎車)產量數據
博文(wén)選萃
| 更多
- 機械加工過程圖示
- 判斷一台加工中心(xīn)精度的幾種辦法(fǎ)
- 中走絲線切割機床的發展趨勢(shì)
- 國產數控(kòng)係(xì)統和數控機床何(hé)去何從?
- 中國的技術(shù)工人都去哪裏了?
- 機械老板做了十多年,為何還是小作坊?
- 機(jī)械行業最新(xīn)自殺性(xìng)營銷,害人害己!不倒閉才
- 製造業大逃亡
- 智(zhì)能時代,少談點智造,多談點製造
- 現實麵前,國(guó)人沉默。製造業的(de)騰飛,要從機床
- 一文搞懂數控車(chē)床加工刀具(jù)補償功能
- 車床鑽孔攻螺紋(wén)加工方法及工裝設計
- 傳(chuán)統鑽削與螺旋銑孔(kǒng)加工工藝的(de)區別