典型切削(xuē)機床能(néng)耗模型的研究(jiū)現(xiàn)狀及發展趨勢
2015-2-3 來源:數控機床市場網 作(zuò)者:大連理工大學機械工程學院
(大(dà)連理工(gōng)大學機械工程(chéng)學院 李濤 孔露露 張洪潮 ASIF Iqbal )
摘要:機床作(zuò)為機械製(zhì)造行(háng)業的“母機(jī)” ,數量大、能(néng)耗高、效率(lǜ)低。近(jìn)年來,學者們(men)為建立精確的機(jī)床能耗模型已(yǐ)做大量工作。針對典型切削機床能耗的建模現狀,從切(qiē)削單元能耗、加工階段整機能耗、工藝單元能(néng)耗三個層次進行綜合分析(xī)。進(jìn)而從節能優化、產品綠色性評估(gū)、企業資源配(pèi)置、機床綠色(sè)設計四方麵對機床能耗模型(xíng)的應用(yòng)進行論述。目前,機床能耗的建(jiàn)模逐漸麵向高端(duān)數控(kòng)機(jī)床,建模的(de)目標性更加明確,與工(gōng)業應用的結(jié)合也使得(dé)模(mó)型的實用價值不斷提升。
關鍵詞:典型切削機床(chuáng);切削比能;整機能耗;工藝單元能耗;節能優化
1 前言(yán)
我國是全球機械製造業大國,同時也是機床生產、消費第一(yī)大(dà)國,擁有世界第一的機床保有量,目前約 800 萬台。若每台機床額定功率平均為 10 kW,則我國機床(chuáng)總額定功率約相當於三峽電站總裝機容量(2250萬kW)的3倍多。而且,統計資料表明,機床(chuáng)能量利用率平(píng)均低於 30%,如果我國機械工業的各類機床的能效(xiào)都提高 1%,則帶來的節能效益相當於幾(jǐ)千(qiān)萬噸(dūn)標準煤。由此可見,機(jī)床量大麵(miàn)廣,耗能多,但(dàn)其能量利用率(lǜ)低,節能降耗潛力大,研究機床能量消耗對於提高資源(yuán)利用率、實現綠色(sè)與可持續製造具有重要意義(yì)。同時(shí),機床能耗也是評價機械加工環境性(xìng)能的重要(yào)指標(biāo)之一,研究表明,離散加工行業(車、銑等)機床對(duì)環境的影響 99%是由於消耗電能引起的。2010 年 10月 26 日,國際標準化委員會起草了機床的(de)環境評估標準(ISO 14955),將節(jiē)能減排的理念貫穿於機(jī)床設(shè)計到機床(chuáng)使用等主要耗能階段。可(kě)以預見,未來能耗指標將成為評(píng)價機床產品的一個新指標。鑒於(yú)此,國內外學者針對揭示機床的能量特性(xìng)、建立機床能耗模(mó)型開展了大量的研究工作,以探尋節能降耗(hào)途徑、減少環(huán)境汙染、推動綠色(sè)與可持(chí)續製造的發(fā)展。
機床能耗是一個多部件多層次的係(xì)統問題,其能耗部件繁多,由 ISO14955-1 可知,機床能耗涉及機床主傳動係統、進給係統、輔助係統等多個能耗子係統,涵蓋機電液三種類型,具有多源能耗(hào)特性。此外(wài),文獻[3]在機床的運行過程中,機床的各部分存在各種性質的能量損耗,這些損耗相互作用、相互影響,從而使機(jī)械加工係(xì)統的能量損耗規律(lǜ)變得複雜,國內外(wài)學者對此展開了多方麵的研究工作。本文對當前(qián)典型機床能耗模型的研究現狀進行(háng)了總結,已有的能耗模型可以歸結為三個層次:切削單元能耗、加工階段整機能耗、工藝單元(yuán)能耗的建模研究。切(qiē)削單元能耗指(zhǐ)機床切削過程中,克服材料變形抗力將(jiāng)材料去除所消耗的能量,是機床總能耗中的有效能部(bù)分;加工階段整(zhěng)機能耗是指機(jī)床處於切削加工階段(duàn)時,整個機床係統所消耗的能量;工(gōng)藝單元能耗是指綜合考慮機床不同運行階段(裝夾、啟動(dòng)、空載、加工(gōng)、換刀等)整個機床係統所消耗的能量總和。這三個層次(cì)的關係可由圖 1 描述。
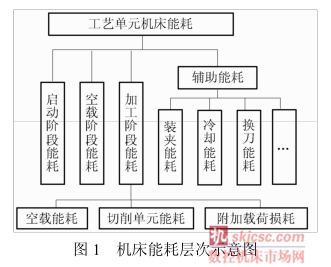
1 機床能耗模型層次化整合分(fèn)析
1.1 切削單元能耗模型的研究
切(qiē)削單元能耗由於受到切削參(cān)數工件材料(liào)、刀具參數、工藝條(tiáo)件、外(wài)部環境等各(gè)種變(biàn)量的影響,這部分能耗難以進行精確量化(huà)。目前該部分的量化主要從分析切削力入手,或(huò)在各種理論知識支持的基礎(chǔ)上通過分析材料去除機理定(dìng)性地(dì)建立切削力預測公式,或(huò)基於實際加(jiā)工經驗數據運用數學擬合方法進行切削力(lì)的定量建模,進而對材料去除能耗進行計算。
1.1.1 基(jī)於(yú)材(cái)料去除機理的切削能耗模型
(1) 理論切削力模型的建立。金(jīn)屬切削過程的實質是被切削金(jīn)屬層在刀具前(qián)刀麵(miàn)的擠壓作用下產生剪切滑移的塑性變形過(guò)程。雖然切削過程(chéng)中產生彈(dàn)性變形,但其變形量與塑性變形相比可忽略不計。針對包括銑削、鑽削、鏜削等在內的不同切削加工方法,雖然刀具和(hé)工件的相互作用(yòng)形(xíng)式有(yǒu)所不同,但工件材料在切(qiē)削加工過程中的塑性變形規律(lǜ)以及切屑形成機理是(shì)相同的。本文采(cǎi)用(yòng)直角(jiǎo)切削(xuē)模型(xíng)從理論上說明金屬(shǔ)切(qiē)削加工的變形過程。直角(jiǎo)切削模型是在(zài)揭示切屑變形本質和現象的基礎(chǔ)上忽略一些次要因素建(jiàn)立起來的(de)簡化物(wù)理模型。該模型由美國(guó)學者 MERCHANT[8-9]在 1945 年(nián)提出,揭示了切削力與切削(xuē)條件之間的關係式,並用最小功原理求出了剪切角(jiǎo)。這(zhè)一理論模型的提出奠定了進行切削力理(lǐ)論預測的基礎,一直沿用(yòng)至今,此後的理論模型大多在此基礎上進行的修正。如圖 2 所示為MERCHANT 的(de)切削力模型。
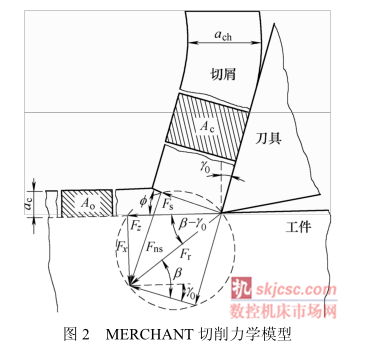
圖(tú) 2 中,ac為切削層厚度;Ao為未切削前的切削層麵(miàn)積;Ac為切屑截麵麵積;ach為切屑厚度;γ0為刀具前角;為剪切角;β為切屑與刀具前刀麵間的平均摩(mó)擦角;Fns為剪切麵上的(de)正壓力;Fs為剪切力;Fr為車刀上的合(hé)力;Fz為切削速度方向的切削分力;Fx為進給(gěi)方向的切削分力。
根(gēn)據材料(liào)去除機理(lǐ)及各力間的幾何(hé)關(guān)係可(kě)推導出
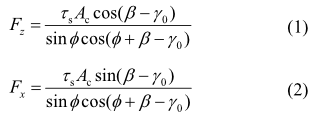
式中(zhōng),τs為工件材料的名義抗剪強度。 自此,國內外學者(zhě)對切削力預測爭相研究。
1951 年, LEE 等開始利用滑移線場理論來研究理想塑性材料的切削現象。之後學者(zhě)們建立了正交切削(xuē)及斜刃切削的切削力模型。提出了考慮刀具磨損及加工硬化的切削力模型,應用摩擦學理論分析了後刀麵與(yǔ)工件的摩擦作用(yòng)力。張弘弢等(děng)考慮了溫度(dù)-速度應變速度效應,不單純用力學方法又考慮了被(bèi)加工材料的物(wù)理力學(xué)性(xìng)質,使得模型在大多數(shù)切削條件下,計算誤差小於 3%。BARRY 等分析了金屬基複合材料的(de)局(jú)部大應變、高應變、高應變率(lǜ)並伴有大量熱量生(shēng)成的切削條件下的本構關係物理模型(xíng)。
(2) 切削功率及切削能耗的計算(suàn)。利用力與速度的物理關係可計算切(qiē)削功率
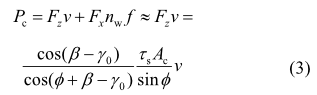
式中 v ——切(qiē)削(xuē)速度; nw ——工件轉速; f ——進給量;
ap ——背吃刀量(在銑削中指銑削深度);
Pc ——切削功率。
切削能耗為(wéi)去除一定體積的材料所消(xiāo)耗的能量

在假設切削功率不變的前提下,加工(gōng)時間 

(V 為材料的總去除體積)。於(yú)是整個加工過程的切削能耗

1.1.2 基於實際加工的經驗公式切削(xuē)能耗(hào)模型
基於試驗(yàn)測量的經驗公式切削能耗模(mó)型是利用測力傳感器、扭矩測試儀等,通過大量試驗,測定(dìng)不同加工參數下切削力(lì)、扭矩的數值,然後利用統計分析及數值擬合建立了切削力、切削(xuē)功率、切削能耗與切削參數之間(jiān)的冪率公式。常用的(de)典型工藝的經驗模型如表 1 所示。表 1 中,C 為被加工金屬和切削條件係數;x、y、z 為指數;K 為修(xiū)正係數;Ps為(wéi)銑削功率,Ks為單(dān)位銑削力,B 為銑削寬度(dù);vf為銑削進給(gěi)速度;M 切削扭矩;Cm為由材料確定的係數;D 為鑽頭直徑。
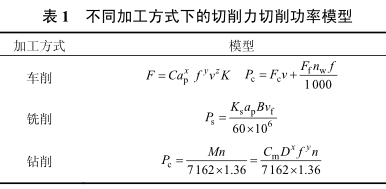
這類(lèi)模型對於定量分析不同工藝不同切削條件(jiàn)下的能耗大(dà)小、指導工藝路線的(de)製定(dìng)、優化分析等有很好的指導作用。通過這類模型計算得到的結果與實(shí)際情況吻合良好,但由於加工條件的複雜(zá)性,該模型中(zhōng)附加了大量由實際情(qíng)況來確定的修正係數,相對繁瑣(suǒ),必(bì)須查閱經驗數值表才能確定。
1.2 加工(gōng)階段整機能耗模型
在切削加工階段,機床幾乎(hū)所有(yǒu)的係統都參與運行,且增加了負載能耗,此時機床的能耗組成如圖 3 所示(以數控機床為例),作為機(jī)床的有效加工狀態,學術(shù)界給予了極大關注。由 GUTOWSKI 教授負責的麻省理工學院的環境意識製造小組(zǔ)對(duì)利(lì)用功率表(biǎo)測量機床能耗的(de)方法進行了深入研究:JEFFREY 等通過試驗數據建立了不同機床在加工階段各部分能耗比例分配圖,研究結果表明,機床能耗隨著(zhe)機床機構的複雜程度及先進程度的增(zēng)大(dà)而提高,一個加工中心的(de)能量利(lì)用率平均不足(zú)15%,而對於一個手動機床則在 30%左右。並且機床能(néng)耗與機床製造的資金密集程度及操作規程密切相關,機床的能效隨著(zhe)負載的增大而提高。
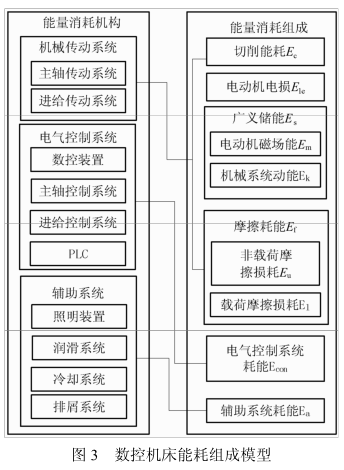
由於(yú)機床結構(gòu)多樣,潤滑條件不同,機床整機能耗(hào)組成各有差異。而研究角度的不同,學者們對機(jī)床單元(yuán)整(zhěng)機能耗的(de)建模也(yě)各有特色。1.2.1 機床主(zhǔ)傳動係統運行(háng)能耗預測模(mó)型 主(zhǔ)傳動係統的能耗是機床全部能(néng)耗的主體,臥式車床主傳動係統的(de)能耗占機床總能耗的 95%以上,有很大研(yán)究價值。重慶大學劉飛等從機床電動機(jī)和機械傳動係(xì)統一體化的角度出發,在考慮(lǜ)機床運(yùn)行中多種能量損耗(hào)並存的情況下,以機電係統和各傳動環節的能(néng)量流程為基(jī)礎,建立了機床主傳(chuán)動係統的能量傳輸預(yù)測數學模型;提出了普通機床功率和效(xiào)率(lǜ)計算方法、能量信息(xī)監控的方法和數學模型。
該理論認為機床能量消耗由切削能耗、空載能耗及(jí)各傳動環節的附加載荷損耗構成,其中空載能耗由各子係統的廣義(yì)儲能(機械能、電磁能等)構成,是含有主(zhǔ)軸轉速、主軸(zhóu)摩擦、阻尼等多個變量的複雜函數,與轉速近似成二次函數關係。圖 4 為機床主傳(chuán)動係統能量流程圖。圖 4 中,PFe為電(diàn)動機的鐵耗;PCu為電動機的銅耗;Pad為電動機的附加損耗;Pmec0 為電動機的機械損耗;Em 為耦合場(電磁場)磁能;Eke為電動機轉子動能;Pim為電動機的輸出功率;Ekn為機械傳(chuán)動係統第 n 個傳動(dòng)環節的動能;Pmecn 為機械傳動係統第 n 個傳動環節(jiē)的(de)機(jī)械損耗 功率。
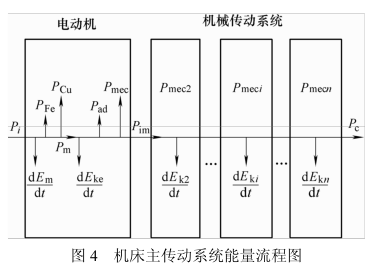
一般形式(shì)的機床主傳(chuán)動係統穩態下的功率傳輸模型為
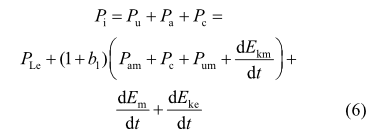
式中 Pi ——主傳動係統總輸入(rù)功率;
Pu ——機床空(kōng)載功率;
Pa ——機床載荷損耗功率;
Pc ——機床輸出功率;
PLe ——電動機的電損;
b1 ——電動機的載荷(hé)係數;
Pam ——機械傳動係統載荷損耗功率;
Pum ——機械傳動係統的非載荷損耗(hào)功率。
對式(6)中各部分分別在其相應的工作時間上進行積分,即可得到機械主傳動係統的能量消耗 Ein為

式中 t ——機床總運行時間;
t1 ——空載時間;
t2 ——切削時間。
1.2.2 基於材料切削比能的能耗模型
切削比能是指去除單位體積的材料所消耗的能量。金屬切削過程是一個材料逐步去除的過程,切削比能是工件加工時瞬時耗能量的量化,能夠反映出切(qiē)削能(néng)耗與材料去除率之間(jiān)的映射關係及機床能(néng)效能力(lì),便於(yú)理解和計算。
LI 等(děng)利用不同的材料去(qù)除率對不同(tóng)的材料進(jìn)行切削,建立了材料(liào)的切(qiē)削(xuē)比能經驗公式

式中(zhōng) SEC——材料的切削比能;
MRR——材料去除率; C0,C1——係(xì)數。
他認為材料的切削比能由裝夾比能、機床運(yùn)行比能、材(cái)料去除比能及非生產比能(即熱損耗比能等)四部分組成。指出模型中的係數 C0、C1並非恒定,定性地分析了(le)材料特性、刀具形(xíng)狀及主軸驅動方式對 C0的(de)影(yǐng)響,機床自身對 C1的影響,但(dàn)具體關係需要根據實際情況進行確定。這種通過切削比能來預測機床能(néng)耗的經驗模(mó)型,為以後切削比能(néng)的研究提供了指引。
早在 1992 年,WARREN建立了切削比能的經驗公式,以及 100 多種材料的切削比能基(jī)礎數據(jù)。
隨著技(jì)術的進步,工藝條件的改善,切削比能不斷受到國際(jì)學者的關(guān)注和應用。GUTOWSKI 等在搜集了(le)大量數據的基礎上基於材料的平均切削比能建立了各種工藝的切削比能圖譜,半定量地反(fǎn)映不同工藝的能效差異(yì)。ALESSANDRO 等[35]對(duì)高速切削條件下的(de)切削比能與(yǔ)刀具幾何(hé)參數與切削速度的關係進行試驗研究。 AWADE 等 預測了高速切削鉻鎳鐵合金 718 時,在主剪切區域內的切削比能解析模型,指出剪切比能是進給率的函數(shù),隨著進給率的減小而增大,在最低切削速度時(shí),試驗剪切比能達到最大。DIAZ 等通過(guò)試驗分析一個微加工中心在不同的材料去除率下切削低碳鋼的能量需求建立了切削比能模(mó)型(xíng),指出材料(liào)的(de)切削比能隨著材料去除率的增大而降低,並將該規律拓(tuò)展到大型機械加工設備中。
1.2.3 基於熱力學(xué)第(dì)二定律(lǜ)的機(jī)床(chuáng)能(néng)耗模型
BRANHAM 等[38]從熱(rè)力學角度把機(jī)床係統看(kàn)做一個輸入輸出(chū)係統,利用熱力學第二定律通過(guò)計算輸入(rù)輸出過程中的減少值作為加工係統的能耗

式中 Blost——的減少值即係(xì)統(tǒng)能耗;
Bin ——係統的輸入值; Bout ——輸出值。
該思(sī)路比較新穎,但其計算結果的(de)精度取決於熵、焓、的準確性,偏差仍比較大,同時由於各種材料和輔助(zhù)材料的熵、焓、值難以直接獲得,目前該方法僅在特定條件下進行了試驗分析。
1.2.4 神經網絡模型
神經網(wǎng)絡方法對複雜不確定問題具有自適應(yīng)和自學習能力(lì),可以有效處理大量工藝參數之間複雜(zá)的(de)非線性關係。謝東等利用(yòng) BP 神(shén)經網(wǎng)絡法搭建了機床能耗與切(qiē)削參數的模型,從(cóng)輸入層(céng)、隱含層、輸(shū)出層的設計,網絡的初始化,訓練算法的選(xuǎn)擇,訓練樣本數的選擇,學習速率的選(xuǎn)擇方(fāng)麵(miàn)建立了 BP 神經網絡,簡化了經驗公式(shì)繁瑣的計算過程取得了較好的預測結果。
1.3 工藝單元能耗模型(xíng)
在一個工件的加工工藝過程中,包括工件裝夾、機加工、工件拆卸等步驟,在機加工部分機床的運行(háng)包括啟動階段、空載階段(duàn)、加(jiā)工階段、停機階段等不同的服役時段(duàn)。 在上述兩層模型的基礎上,利用萬用表或功率分析儀通過試驗測量不同階段機床運行的能耗可建立機床工藝單(dān)元能耗(hào)模型。
在工(gōng)件(jiàn)加工工藝中的總能耗是在各子部件、子過程能耗基礎上的累加,因此該部分模型主要以宏觀框架模型為主(zhǔ),目(mù)前已建立的工藝能耗模型見表2。由於研究目的的不同,有些學者也將機床間(jiān)接能耗:材料生產能耗、刀具製造能耗以及(jí)產品清洗能耗考慮在內。
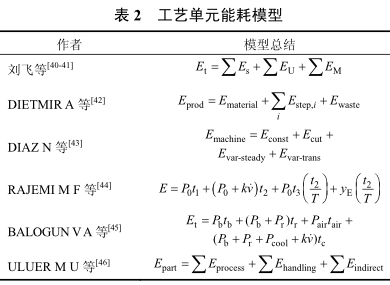
表 2 中,Et為機床總能耗(hào);Es為啟動(dòng)能(néng)耗;EU為空載能(néng)耗;EM為加(jiā)工能耗;Eprod為產品生產總能耗;Ematerial為材料生產能量;Estep,i為每個加工階段能耗; Ewaste為浪費的能量;Emachine為機床總能耗;Econst 為機床功率恒定部分能耗;Ecut 為切削能耗;Evar-steady 為主軸等達到特定(dìng)運行狀態的能耗;Evar-trans 為主(zhǔ)軸等啟動機加減速階(jiē)段變化能耗;P0為空載功率;k 為係數(shù);v 為材料去除率;T 為刀具壽命;yE為刀具製造能耗;t3為換刀時間;t4為刀具製造時間(jiān);Pb為基礎功率;Pr為準備狀態功(gōng)率;Pcool為冷卻係統(tǒng)功率;Pair為空載(zǎi)功率;tb、tr、tair、tc 分別為對應的時間;Epart為加工一個工(gōng)件(jiàn)的能耗;Eprocess 為製造過程能耗;Ehandling為自動裝夾係(xì)統及傳送係統能耗;Eindirect為與保持環境清潔有關的非(fēi)直接能耗(hào)。
2 機床能耗模型應用(yòng)分析
機械加工過程實質上是一個材(cái)料的去(qù)除過程,期間將消耗大量的資源,產生的各種廢棄物和排放物對環境將(jiāng)產生很大影響。機床(chuáng)能耗模型能夠量化(huà)機床整個加工周期的能源消耗及能量利用率,並能夠間(jiān)接反(fǎn)應整個加(jiā)工周期(qī)物料的輸(shū)入輸出情況。因此,利用機(jī)床能(néng)耗模型可以有效分析(xī)機械加工係統的資源能源消耗和(hé)環境影響問題。其應用主要可以歸(guī)納(nà)為以下四個方麵。
(1) 節能性工藝優化指導。基(jī)於(yú)試驗測量數據建立起來的能耗模型與實(shí)際加工情(qíng)況有很好的吻合性,主(zhǔ)要用於對(duì)特定機床的(de)加工任務進行能耗監 控並通過對加工(gōng)參數的優化得到最佳節能參數。DRAGANESCU 等(děng)通過試驗,采(cǎi)用響應麵(miàn)分(fèn)析法建(jiàn)立了(le)機床能耗及能效與切削參數的(de)影響關聯模型,通過優化分析得到利用立(lì)銑床對鋁合金材料進行(háng)端麵銑削時的最佳(jiā)節能參數,相對保守參數,去(qù)除(chú)相同體積的材料,當材料去除率由 6.4 cm3/min提高到 818.6 cm3/min 時,節能可達 93.98%。日本森(sēn)精機有限公司采用正交試(shì)驗方法建立機床能耗模型(xíng),分析了不(bú)同切削參數對機床能耗的影響,給出鑽削 S45C 碳鋼最(zuì)佳節能參(cān)數,相對(duì)於初選參數,在材料去除率提高 25%的(de)情況下材料的切削比能可降低 5%。謝東等采(cǎi)用粒子群優化算法(fǎ)對機床能耗函數進行尋優求解,得出了加工一低碳鋼零件(jiàn)的節能性參數,采用優化後的(de)參數(shù)能將加(jiā)工能耗降低 22%,但刀具發熱厲(lì)害,影響(xiǎng)刀具壽命。施(shī)金良等根據數控機床(chuáng)主傳動係統(tǒng)功率方程,建立了數控機床工步間空載運行時停(tíng)機節能的理論決策模型,通過實際案例(lì)分析得到很好的節能應用效果。周丹等提(tí)出一種(zhǒng)數控機床能量設計因(yīn)子提取方(fāng)法,並對提高機床的能量效率給出了建設性意見。但(dàn)這些在特(tè)定試驗條件下得出的結論,對機床節能性使用有一定的指導作用,但由於受實際加工質量要求及設備規範性(xìng)使用的限製,其可行性及適用性還需要進一步的(de)拓展研究。
(2) 綠色(sè)評估支持。將機械加工(gōng)係統看作一個輸入輸出(chū)係統,將其消耗及排放考慮在內的過程模型對於加工過程(chéng)的綠(lǜ)色性評(píng)估提供了很大支持。美國加州伯克利分校的綠色設計(jì)與製造(zào)聯盟建立了一個將刀具、切削液、材料及能量消耗考慮在內的加工(gōng)過程模型,對(duì)係統產(chǎn)生的廢液、切屑、排放物等進行加權量化並評價加(jiā)工各(gè)環節產生的毒性、可燃性、放射性等環境影響因子(zǐ),尋找敏感環節輔助產(chǎn)品的(de)環境(jìng)設計決策。麻省理工學院的環(huán)境意識小組開發了一係列機(jī)械加工中的銑削加工(gōng)、磨削加(jiā)工等製造過程的模型,對其(qí)產生的資源環境(jìng)屬性進行(háng)評價,主要(yào)考慮(lǜ)了七種不同的(de)資源消耗和環境影響因素:能量、固體廢棄(qì)物、回收性、有(yǒu)毒材料、廢水、廢氣、垃圾填埋物等。通過建立設備層模型(xíng)和物料流模型,評價製造係(xì)統中的多種可選製造過程、製造工藝的資(zī)源環境屬性。
(3) 資源配(pèi)置,調度安排決策。近年來,綠色製造與可持續製造的理念越來越受到重視,國內重慶大學劉飛課題組提出的綠色(sè)製造理論(lùn)中指出減少(shǎo)製造過程的(de)資源能源消耗是綠色製造的重要目標之一。他們在機床能耗(hào)模型的基礎上,從宏觀(guān)角度,建立(lì)了麵向(xiàng)綠色製造機械加工係統任(rèn)務的調度模型,根據機床規格與零件(jiàn)加工要(yào)求的匹配性采用優化分析的方(fāng)法獲得滿足最優(yōu)零件與機床組合方案進行節(jiē)能性調度,大大降低了機械加工(gōng)係統所產生的環(huán)境影響和資源消耗。
(4) 綠色設計指導。部(bù)件(jiàn)層的機床(chuáng)能(néng)耗模型不僅分析了機床部件的能耗特征及其節能潛力,而且為高效部件的結(jié)構設計提供基礎。ABELE 等分析了機床主軸(zhóu)單元的能耗特性,並(bìng)指出了節能潛力。ZULAIKA 等提出一種加工過程(chéng)的輕量化設計方(fāng)法,同時考慮了減少可移動部件的質量和最大化材(cái)料去除率兩個因素,用該方法設計了一台大型銑床(chuáng),結果表明該方法可以將生(shēng)產率提高一倍,同時因可移動部件質量減少 20%可降低能耗 13%。
3 機床能耗模型研究趨勢
近年來,隨(suí)著大量新(xīn)工(gōng)藝、新設備、新技術在(zài)機械製造領域的應用,機床能耗的建模對象逐漸轉向(xiàng)高端設備,麵向特定目標的建模使得模型的實(shí)用價值不斷提升。當今機床能耗模(mó)型的研究趨(qū)勢可歸結為如下。
(1) 對具有機-電-液(yè)多源能量(liàng)融合特征(zhēng)的高端數控機床(chuáng),從部件層開展深入研究,分析加工過程能量在各(gè)子係統流動、融合與分布特性,構建高(gāo)端數控機床加工(gōng)過程能耗模型。重慶大(dà)學劉飛教授帶領的(de)團(tuán)隊在(zài)建立了普通機床(chuáng)主(zhǔ)傳動係(xì)統的能耗模型的基礎上,建立了變頻調速數控(kòng)機床主傳動係統及進(jìn)給係統的(de)功率平衡方程,揭示了變頻器的(de)能量損耗規律,進一步對數控機(jī)床空載運行下的能(néng)量參數(包括空載功率(lǜ)、空載電流和功(gōng)率(lǜ)因數)特性進行了分(fèn)析,並揭示了變頻數控機床當(dāng)電源頻率小於基準頻率時空載功率是單調遞增的,電源(yuán)頻率大於基準頻率(lǜ)時主傳動係統的空載功率的增減性與其結構參數(shù)有關(guān)的獨有特性。但這些已建立的模型尚處在理論層麵,模型中(zhōng)大量模糊影(yǐng)響係數的存在使得與實際(jì)情況的吻合性上還有待進一步的試驗探究與建模修正。
(2) 建立加工單元過程能耗、物耗、環境數據(jù)清單,支持產品生(shēng)命周期的經濟屬性、環境屬性、社會屬性的評估。MICHAEL 等以鑽削一種特定零件為例提出了建立單(dān)元製造(zào)過程離線物(wù)耗、能耗分類管理數據清單,為產品設計生命(mìng)周期(qī)評價提供數據(jù)支持。黃海鴻等從產品設計角度出發,在分析產(chǎn)品能量消耗特性的基礎上導出了產品全生命周期能量過程模型,並加以定量化描述,從而(ér)為產品設計提供合理(lǐ)和可行的能量分析手段和應用方法。該思路的提出為推動產品生產的可持續性提供了有力的量化評估方法,所需的清單(dān)數據尚(shàng)需(xū)進一(yī)步健全。
(3) 機床能耗建模正向多領域交叉化發(fā)展,機床能耗建模(mó)技術與機電控製技術、智能製造技(jì)術、信息通信技術的交叉集(jí)成,將推(tuī)動能耗模型與工業(yè)應用的結合。德國德(dé)馬吉(jí)公司開發出虛擬機(jī)器、自動停機管(guǎn)理、綠色(sè)代碼等(děng)節能技(jì)術。例(lì)如,開發的機(jī)械加工仿真模擬技術替代試切過程,節約該環節能耗;建立的機床智能管理平台,用戶可(kě)通(tōng)過數據係統控製麵板設置不同的係統關機時間(jiān),控(kòng)製機床進入休眠狀態,最大限(xiàn)度降低能源消耗,還支持喚醒和預熱(rè)功能。
4 結論
從切削單元能耗、加工階段整機能耗、工藝單元能耗三(sān)個層次(cì)對(duì)機床能耗的建模進行總(zǒng)結,並對機床能耗模型的應用及研究趨勢進(jìn)行了分析。通過整合(hé)分析發現機床能耗模(mó)型的(de)研究不斷完善,表現在:機床能耗向多層次(cì)拓展,向(xiàng)下延伸到(dào)材料去除過程的能耗建模,向上拓展到機床層、工藝層乃至車(chē)間層;從理論的概念模型細化到具體機床執行具體工藝的能耗隨工藝參數變化(huà)的精確(què)模型,模(mó)型的精度不斷提升;模型的應用範圍逐漸由單純節能優化擴展到(dào)產品生產的綠色評估、綠色設計及企(qǐ)業資源配置上(shàng),麵向特定(dìng)目標的建(jiàn)模技術(shù)更(gèng)具針對性。但還有許多方(fāng)麵需要進一步探究:麵向高端數控機(jī)床的多源能量流耦合特性尚需完善,局部關鍵問題尚待研究;麵向產品生命周期評(píng)估的物(wù)耗、能(néng)耗、環境清單數據尚待開發(fā);機床能耗建模技術尚待與(yǔ)智能化技術及工業應用結合拓展。
投稿箱:
如果您有機床行業、企業相關新聞稿件發表,或(huò)進行資訊合作,歡(huān)迎聯係本網編輯部, 郵(yóu)箱:skjcsc@vip.sina.com
如果您有機床行業、企業相關新聞稿件發表,或(huò)進行資訊合作,歡(huān)迎聯係本網編輯部, 郵(yóu)箱:skjcsc@vip.sina.com
更多相關(guān)信息