槍鑽深孔加工顫振(zhèn)穩定性及振動加工技術綜述
2019-2-18 來源:江西洪都(dōu)航空工業(yè) 南京航空航(háng)天(tiān)大學 作者: 汪洋華 李亮 龍韜 何俊傑(jié) 馬曉波 等
摘(zhāi) 要: 深孔(kǒng)槍鑽加工中的顫振問題,嚴重地影響了產品的(de)加工質量和機床的效率(lǜ)。以鈦合金(jīn)小直徑深孔的槍鑽加工為研究對象,從實驗研究、理論分析、顫振(zhèn)預測、振(zhèn)動(dòng)加工等幾個方麵,對目前小直(zhí)徑深孔槍鑽加(jiā)工技術進行分析,為後續的槍鑽深孔加工鑽削穩定性與振動加工技術(shù)的基礎研究提供理論依據(jù)。
關鍵詞: 深孔(kǒng)加工; 槍鑽(zuàn); 穩定性; 顫振(zhèn)預測; 顫振抑製; 振動(dòng)加工
0 引言
深孔加工是機械加工(gōng)領域的一個(gè)重要分(fèn)支。孔加工在(zài)整個機械加工中約占 25%,而深加工的總量在孔加工的比例達到了一半。深孔加工技術和應用開發過程崛起於炮管生(shēng)產。20 世紀 60 年代以前,深孔加工技術主要用於生產槍管、炮管,此後隨著生產格局的轉變(biàn),深孔加工技術也轉向能源、航空航天、冶(yě)金、汽車、化工和機床行業。
20 世紀 90 年代以後,隨著我國經濟建設的(de)加速發(fā)展,極大地推動了上述(shù)行業對深孔加工技術的需求,傳統的(de)孔加工方式已不能滿足生產需求。因此,采用較先進(jìn)的專用刀(dāo)具及特殊的深孔加工技術進行深孔加工是非常有必要的。深孔(kǒng)加工係統按照排屑方式可分(fèn)為外(wài)排屑和內排屑兩類,其中外(wài)排屑係統有槍鑽、深孔扁鑽和深孔麻花鑽等; 內排屑(xiè)係統因所用的(de)加工係統不同,分為 BTA 深孔鑽係統、噴吸鑽係統和 DF 深孔鑽係統等 3 種。
對於內排屑加(jiā)工係統主要適用場合在直徑>Φ18 mm 的深孔加工; 而外(wài)排屑加工係統中深(shēn)孔扁鑽和深孔麻(má)花鑽由於加工深度的(de)製約,無(wú)法完(wán)成對於長(zhǎng)徑比>50 的超長小直徑深孔的加工。通常長徑比 L/D>10 的超長小直徑深孔( Φ2 ~Φ20 mm) 均(jun1)采用深孔槍鑽加工工藝。目前航空航天、軍事和民用產業中,超(chāo)長小直徑深(shēn)孔加工的需求越來越多。例如: 在航天航空業中各類飛機艙(cāng)門中導軌孔以及模具行業中(zhōng)大型汽車覆蓋件的注塑(sù)模具水道孔。
所以本文提出針對超長小直徑深孔槍鑽鑽削問題的研究,也正是符合國家航空航天(tiān)、能(néng)源和汽車等行業發展的需求。
1 、深孔槍鑽加工工藝(yì)
深孔槍鑽加工(gōng)工藝有以下的特點:
1) 是小直徑深孔加工範疇最有效的刀具(jù),且長(zhǎng)徑(jìng)比越(yuè)大,優越(yuè)性越顯著;2) 生產效率高(轉速(sù)高,進(jìn)給量較大,且是連續進給(gěi),不需(xū)要中途退刀排屑) ;3) 孔徑尺寸(cùn)較(jiào)穩定( 鑽和鉸一次(cì)完成) ,孔徑變化範圍較小;4) 被加工孔表麵較為光(guāng)滑,標準鋼材表麵(miàn)粗糙度可達 Ra3.2~ Ra1.6,鑄鐵表麵粗糙(cāo)度可達 Ra0.8;5) 具備高的(de)形位公差,孔圓度 < 0. 005 mm,軸線平行度<0.2 mm/1 000 mm;6) 適應範圍廣,被(bèi)加(jiā)工(gōng)材(cái)料(liào)硬(yìng)度>HRC45,仍可加(jiā)工;7) 孔鑽通(tōng)後,孔口無飛邊、毛刺。

深孔槍鑽結構如圖 1 所示(shì)。分為槍頭、鑽杆和鑽柄 3部分。有單(dān)溝槍鑽(zuàn)和雙溝槍鑽 2 種類型。鑽尖形狀如圖(tú)2 所示,鑽尖結構複雜,幾何參數(shù)較多。
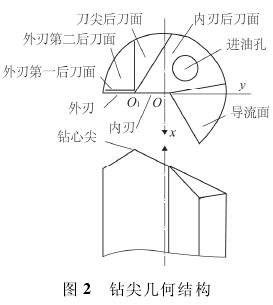
深孔加工中,由於加工過程屬於封閉式(shì)或半封閉式切削(xuē),所以在切削加工過程中存在切屑(xiè)的斷屑、排屑、切削液的流動、鑽(zuàn)削刀具選擇和工件(jiàn)的散熱以及刀具的導向等問題,這些問題會導致零件加工表麵質(zhì)量惡化。
難加(jiā)工材料( 鈦合金等(děng)) 的超(chāo)長小直徑深孔的(de)加工,因(yīn)其孔徑小,孔深長(zhǎng),加工過程中的影響因素更加複雜,所以加工尤為困難。在小直徑深孔槍鑽加工過程中,由於被加工孔較深,且槍鑽鑽杆又細又長極易誘(yòu)發鑽削的顫振現象。顫振一直是影(yǐng)響槍鑽加工質量和機床切削效率的關鍵問題之一。深孔鑽削產生(shēng)的顫振不僅會惡化零件的加工表麵質量,降(jiàng)低機床和刀具(jù)的使用壽命,嚴重時會使鑽削加工無(wú)法進行。
其形成的原因包(bāo)括切屑無法順利的排出產生的顫振、鑽杆加工時懸伸量過長導致剛性不足產生的(de)顫振、鑽削過程中切削液與工件之間的流固場耦合作用力產生的顫振、鑽削刀具(jù)崩刃或堵屑產生的顫振、加工參數選擇不當引起(qǐ)的顫振等等。因此迫切需(xū)要揭示深孔槍鑽加工過程中顫振的產生本質,拓展深孔鑽削顫振的基礎理論,創新深孔鑽削顫振抑製方法。
2 、深孔加工顫振(zhèn)穩定性分析研(yán)究
通過資料的檢索,現(xiàn)有研究主要(yào)是建立相應的鑽削顫振模型,通過解析法或數值(zhí)方法來求解,推導出鑽削穩定性 lobe 圖,並結合穩定性 lobe 圖來(lái)分析鑽削係統穩定性,進而為顫振控製提(tí)供理論依據。
小直徑(jìng)深孔槍(qiāng)鑽過程中,隨著鑽孔深度(dù)的增加,鑽杆(gǎn)的懸伸長度不斷增加,是一個典型時變係統。此外,鑽頭除了切削刃部分與工件接觸,導向部分也與已加(jiā)工的孔壁接觸,使得這(zhè)一時變係(xì)統的動力學(xué)問題更為複雜。
目前對於深孔加(jiā)工顫(chàn)振穩定性的研究主要針對的是小直徑麻花鑽和 BTA 鑽削(xuē)係統(tǒng),而關於
深(shēn)孔槍鑽係統顫振(zhèn)穩(wěn)定性的研究較少。Mehrabadi 和 Nouri 等人(rén)提(tí)出了一個(gè)考慮彎曲振(zhèn)動的模型。
通過該模型可以(yǐ)預測出 BTA 深孔加工過程中的顫振穩定域,利(lì)用歐拉數值法模擬出鑽頭的運動軌跡。結合穩定域圖形,可以分析出鑽頭在不同的轉速下加(jiā)工出的的孔形狀和(hé)精度的差別。Arvajeh 和 Ismail提出了一個BTA 鑽削顫振的動力學模型。
該模型綜合研究了由於彎曲產生的橫(héng)向振(zhèn)動和由於扭(niǔ)轉產生的軸向振動,並(bìng)考慮了回轉效應。Weinert 等用統計方(fāng)法更全麵地解釋了加工參數和表麵粗糙度(dù)的關係,他指出 BTA 鑽杆的大長徑比和較低的彎曲剛度使鑽杆容易發生顫振現象。Messaoud等指出深(shēn)孔加工中出現的顫振現象也是導致直線度降低(dī)的原因之一,並用非(fēi)線性連(lián)續建模(mó)的方法對加工過程的動態(tài)變 化 建 立 了 一 個 實 時 的 模 型。Chin提 出 了BTA 深孔加工切屑狀態監測的數學模型,在此基礎上(shàng)對刀具斷屑、排屑狀態與切屑液流體動態壓力變化的聯係進行(háng)了研(yán)究,並提出了一套新的關於切屑狀態監(jiān)測的仿真計算方法。Bayly將理論分析與(yǔ)實驗結果相比較,對鑽杆係統的扭轉振動進行了(le)分析,詳細地考察了刀具顫振頻率的(de)分布範圍以及穩定性判據,指(zhǐ)出深孔加工過程中鑽杆係統存(cún)在明顯的非線性特征。
國內一些高等院校和科研機構也在(zài)深孔(kǒng)加工顫振(zhèn)方(fāng)麵做了(le)研究。張(zhāng)秋麗根據二元直角切削(xuē)模(mó)型,提出了三元切削模型,推導出槍鑽的鑽(zuàn)削力數學模型。白萬民等人以槍鑽為研究對象,分析了深孔(kǒng)鑽削時刀具的受(shòu)力狀況,給出了深孔鑽的力學模型和求解方程,提出了一種測量和計算相結合的方法來求解鑽削力分量。哈爾濱工業大學(xué)提出了利用(yòng)多個特征參(cān)數綜合監測鑽削過程(chéng),通過大量實驗,觀察刀具在破損、折斷等(děng)異常情況下,各個特征(zhēng)參(cān)數的變化規律,並設定閉值,對鑽削加工過程進行監測。
西安理工(gōng)大學李言、孔(kǒng)令飛等設計了一種將周期值(zhí)作(zuò)為參數一起參與打靶迭代的算法,通過優化確定迭代過程中的增量值。針對單孔和槽孔兩種孔(kǒng)結構形式,將非線性切(qiē)削(xuē)液流體力及其 Jacobian 矩陣聯(lián)合求解法與改進的打(dǎ)靶法及(jí) Floquet 論相結合,研究了 BTA 深孔加工係(xì)統中中鑽杆係統非線(xiàn)性動態行為。唐英等(děng)利用小直徑麻(má)花鑽進行微小孔(kǒng)高速(sù)鑽削實驗研究表明: 鑽削過程中,在一定速度範圍內,隨著(zhe)轉速的增加、軸(zhóu)向力和轉矩下降,說(shuō)明摩擦型顫振的發生條件。
高本河等分析了深孔加工孔軸線的偏斜機理(lǐ),提出(chū)了利用靜止(zhǐ)外力進行糾(jiū)偏的理論和方法,並確定出合適的糾(jiū)偏位置。試驗證明該方法具有良(liáng)好的糾偏能力,為深孔鑽削孔軸線偏斜的糾正提(tí)供了(le)理論和實踐依據。國內外現有(yǒu)針對深孔鑽削顫振(zhèn)的理論研究,主要還是以線性理論為主,雖然能成功揭(jiē)示和預測發生(shēng)顫振的臨界條件,但無法揭示切削顫振增長的過程與規律以及探求抑製顫(chàn)振振幅的途徑與措施,並且研究方法主要(yào)是將物理模型轉化為時滯(zhì)微分方程,然後通過半解析法或數值方法來求解,並結合穩定性圖(tú)表來分析(xī)係(xì)統穩(wěn)定性,從而指導鑽削顫振控製; 並且研究的(de)重點主要集中在小直徑麻花鑽和BTA 深孔鑽削(xuē)係統,對(duì)於槍鑽顫振的係統研究較少。
且對於一些難加工材料如鈦合金(jīn)等,鑽削參數調整範圍遠小於鋁合金等易切材料零件,穩定性(xìng) lobe 圖的應(yīng)用價值並不顯(xiǎn)著,難以用來指導工程實際。深(shēn)孔槍鑽加工中(zhōng)顫振產生的(de)主要動力學根源是由於係統阻尼或者係統剛度出現負值,現有的顫振判斷難以區別出對於這種多自由度係統中,是哪(nǎ)一個阻尼、或者剛度對(duì)顫振的(de)影響較大(dà)。而深孔槍鑽加工係統中阻尼可分為機床結(jié)構阻尼和由槍鑽後刀麵與工件表麵相互幹涉(shè)而產(chǎn)生(shēng)的過程阻尼,及鑽頭的(de)支撐部位和(hé)已加工(gōng)孔壁的接觸摩擦(cā)產生的過程阻尼。采用勞斯判據的優點(diǎn)在於可以(yǐ)把(bǎ)阻尼、剛度進(jìn)行等效,實現阻尼歸一化。較(jiào)為直觀判斷(duàn)各阻(zǔ)尼(ní)項和剛度項對顫振的影響,為顫振控製提供了鑒(jiàn)別工具。
3 、深孔加工顫振抑製方法研究
顫振研(yán)究的最終目的是抑製顫振的產(chǎn)生和減小顫振的影響。目前,抑製顫振的方法一般可以分為被(bèi)動型控製、半主動控製、主動型控製和變參數控製。因為(wéi)半主動控製(zhì)顫振和變參數(shù)控製顫振在(zài)控製方法上的簡便性(xìng)和易操作性,一直是大多數研究者研究的重點。半主動控(kòng)製(zhì)主要是(shì)通過增加鑽削係統剛度、阻尼或(huò)者附加動力吸振器吸收振動來抑製顫振的方法。
要是采用各(gè)類(lèi)減振器。例如: Tewani 和 Sanjiv G等設計在深孔加工鏜杆(gǎn)上麵加(jiā)吸(xī)振器(qì)來(lái)抑製顫(chàn)振。變參數控製的實質則是(shì)通過(guò)調整切(qiē)削(xuē)參數( 如刀(dāo)具工作角度、進給(gěi)量和切(qiē)削速度等(děng)) 將切削工(gōng)作位置從不(bú)穩定區移到穩定區,實質就是破壞顫振產生的條件。例如: Tarng 等通過 Nyquist穩定標準分析了切削速度、寬度與顫振頻率的關係圖,找到在一定顫振頻率下,主軸轉速以及穩定切削速(sù)度(dù)與內外(wài)調製相位變(biàn)化的關係,提出了利用改變主軸轉速來抑製鑽削中顫振(zhèn)的方法。
王仁德等通過頻率掃描法分(fèn)析再生顫振的衰減係數模型,提出了一種新的變(biàn)速切削(xuē)抑製振動機理,指出變速切削時係統頻(pín)率和衰減係數會(huì)隨轉速變(biàn)化而變化,變速範圍增加會使係統衰減(jiǎn)係(xì)數增加,從而實現抑振。從實際應用效果看,半主動控製和調整切削參數法均具有一定的局限性。對於深孔槍鑽加工而言,加工過程(chéng)是單刃多點接觸,刀具後刀麵與工(gōng)件表麵相互幹涉而產生的阻尼(ní),鑽頭的支撐部位和(hé)已加工孔壁的接觸與摩擦,產生(shēng)的摩擦阻尼,都屬於過程阻尼的範疇。因此必須在顫振模型中(zhōng)考慮過程阻尼的影響。目前國外(wài)研(yán)究人員開始(shǐ)研究利(lì)用加工(gōng)過程中的非線性力(lì)學行(háng)為來抑製顫振,即充分考慮過程阻尼對切削穩定性的影響,通過改變過程阻尼來實現顫振抑製(zhì)。
目前對於(yú)過程(chéng)阻尼的研究主(zhǔ)要集中於車削和(hé)銑削。例如: Altinta通(tōng)過一係列正交試驗,識別動態切削力中的過程阻(zǔ)尼係數,該試驗由快速伺服係統控製,使得刀具 以 預 期 頻 率 和 振 幅 振(zhèn) 蕩。Turkes E,Orak S 等人基於刀具剪切角變化以及後(hòu)刀(dāo)麵和工件表麵波紋(wén)之間幹(gàn)涉力的變化,建立了車削過程阻尼模型,對零階(jiē)頻率法的臨界切深表達式(shì)進行逆求解(jiě),識(shí)別過程阻尼率。
Huang C Y,Wang J-J. Junz 等人提出了包含切削阻(zǔ)尼的銑削動能模(mó)式(shì),模式中包含剪(jiǎn)切、犁耕兩種切削機製,以及切削(xuē)力大小及方向變動所產生的阻尼效應,建立線性(xìng)周期性時變的銑削動能模型(xíng)。Budak 和 Tunc 等人克服了試驗建模的弱點,在過程阻尼建模和係數辨識方麵,進(jìn)行了較為細致(zhì)的工作。Ahmadi 和 Ismail 等人基於小振幅(fú)假(jiǎ)設,將過程阻尼等效為線性粘性阻尼,利用半離散法,計算銑削穩定性極限,該模型具有一定局限性,預測出的穩定性極限低於實(shí)驗值(zhí)。
李欣和李亮等人(rén)利(lì)用隱式龍格(gé)庫塔法,計算典型鈦合(hé)金材料銑削加工中(zhōng)幹(gàn)涉產生的侵入麵(miàn)積以及阻力,建立考慮過程阻尼效應的非線性銑削動力學模型。在現有文獻中,深孔鑽削穩定(dìng)性分析均采用較為(wéi)傳統的線(xiàn)性模型,未(wèi)考慮過程(chéng)阻尼,其在低速區(qū)會產(chǎn)生很大誤差。特別對於一些難加工材(cái)料如鈦合金加工來說,為保證刀具壽命,切削速度一般較低,這時如(rú)果(guǒ)還采用常用的線性模型,預(yù)測的(de)極限切深遠低於實際極(jí)限切深,勢必會影響加工效率。而且過程阻尼的大(dà)小和刀具幾何參數息息相關,設計幾何參(cān)數,利用過程阻尼來減(jiǎn)振的(de)文獻,國內則更為缺乏。
4 、深(shēn)孔加(jiā)工振動鑽削技術國內外研
究(jiū)現狀振動鑽削是振動切削的一(yī)個(gè)重要分支(zhī),其與(yǔ)傳統切削的主要區別是在鑽孔過程中可以通過振動裝置使鑽頭與工件之間產生可控的相對運動,使切削速(sù)度(dù)、進給(gěi)量、切削深度按一定的規律(lǜ)變(biàn)化,改變工件與(yǔ)刀具(jù)之間的時間與空間分配(pèi)。
在振動鑽削過程中(zhōng),合理選擇振動參數( 振動頻率和(hé)振幅) 、進給量、主軸轉速等加工工(gōng)藝參數,可(kě)明顯提高(gāo)孔加工精度,減小(xiǎo)出口毛刺,降低切削(xuē)力和切削溫度,延長(zhǎng)鑽頭壽命。振動鑽削技術使傳統(tǒng)鑽削加工技術有了質的飛躍。目前,國內外學者對振動鑽削(xuē)技術的研究主要集中振動鑽削本質與機理研究、振動鑽削係統裝備研究(jiū)、振(zhèn)動鑽削數學模型建立三個方麵,而且均取
得了很大成果。
在振動鑽削本質與(yǔ)機理(lǐ)研究方麵,1954 年,日本宇都宮大學的隈部淳一郎教授提出振(zhèn)動鑽削理論,並在其(qí)著(zhe)作《精密加工與振動切削( 基礎與應用) 》中對振動鑽削做了詳細的介(jiè)紹與實驗研究,認為振動鑽削與傳統的鑽削加工相比具有斷屑排屑效果好、切削力小、加(jiā)工精度較高、刀具壽命較長等優點。
在此基礎上(shàng),隈部淳一郎教授率先提(tí)出了超聲波振動鑽削的“鑽(zuàn)頭剛性化效果”理論,為(wéi)超(chāo)聲波振動鑽削的鑽入定(dìng)位精度奠定了理論基礎。隨後,其又提出了脈衝能量與應力集中理論,認(rèn)為在分離型振動鑽削時,鑽頭由普通鑽削時的連續切(qiē)削轉變成振動鑽削時(shí)的脈(mò)衝式切(qiē)削,特別橫刃由連續擠壓工件轉變成脈衝式楔入(rù)工件。1973 年,前蘇聯鮑曼工學院的 V.N. Poduraev 通過實驗研究提出了振動鑽削的衝擊理(lǐ)論(lùn),認為振動鑽削時鑽頭橫刃的衝擊作(zuò)用能明顯改善橫刃的切削條件,並運用彈塑性理論對振動鑽削的動(dòng)力學機理進行了分析論證。1979 年,日本學者足立勝重提出了槍鑽低頻(pín)振動斷(duàn)屑理論,該理論指出相鄰切(qiē)屑若存在非零的(de)振動相位差,就會出現薄弱環節(jiē)而折斷,否則,無法實現斷屑(xiè)。1982 年(nián),薛萬夫教授對深孔槍鑽振動鑽削時刀刃相鄰運動軌(guǐ)跡波形進行了理論分析和(hé)計算,得出了保證斷屑的條件,進一步豐富了足立勝重的振動斷屑(xiè)理論。
同時,他在實驗研究(jiū)的基礎上,進一步提出了振動(dòng)鑽削的動態角度理論,指出主切削刃的前角和後角在鑽削過程中是動態變化的,並給出了實際動態後角 α 的計算公式(shì)和計算(suàn)圖。在後續的研究工作中,動態後角的提(tí)出給加工塑性金屬時可以改善刀具與工件的摩擦條件提供了理論依(yī)據。1984 年開始,王立江教授(shòu)和他的課題組對高頻和低頻振動鑽削都(dōu)進行了係統的研究。研究成果無疑彌補了足立勝重從(cóng)運動學角度對振動鑽削分析時得出的零相位差不能斷(duàn)屑的缺陷和不足,使振動斷屑(xiè)理論進(jìn)一步完善化。
其次,在研究中還提出了低頻振動提高鑽入定位精度的新觀點,即具有“鑽入-偏移-退回(huí)-恢複-重新鑽入”的動力學特性。這一特性的發現無疑豐富了剛性化理論,推動了振動鑽削理論研究(jiū)的進程。1986 年劉華(huá)明教授在自製的超聲波振動鑽床上(shàng)進行了實驗研究,結果發現振動鑽削使切削力(lì)下降、表麵質量和孔徑精度提高,並進一步探討了鑽頭耐用度與振幅之間的關係,給出了兩者的關係曲線。1995 年,楊(yáng)兆軍博士對微(wēi)小鑽頭低頻軸向振動(dòng)鑽削的動力學特(tè)性進行理論與實驗研究時發現,指出(chū)由於微小鑽頭的固有頻率極高,即使在阻尼比極小的情況下,振動能量迅速衰減,恢複變直後再重新鑽入,具有(yǒu)低頻振動鑽削時微(wēi)小鑽頭(tóu)的“分離衰減多次校正”的(de)動力學(xué)特性。2000 年楊兆軍教授、王立(lì)平教授(shòu)提出了三區段變參(cān)數振動鑽削微(wēi)孔的(de)新工藝(yì),探討並研究(jiū)了用非線性回歸求取各(gè)區段最佳振動(dòng)參數的方(fāng)法,驗證了以三區段最佳振動參數(shù)作變參數(shù)時,可以全麵降(jiàng)低微孔加工誤差的工藝效果。2004 年(nián)東華大學的黃誌榮等人通(tōng)過(guò)對普通麻花鑽的(de)改進,在 JCS-018 立式加工中心,加工不鏽鋼 316,孔徑 2 mm,孔深 20 mm,加(jiā)工參數為: 主軸(zhóu)轉速: 2 500 r/min,轉速倍率: 100%,進給速度:100 mm / min,取得一定的成果,實現小直徑(jìng)深孔的高速鑽削。2006 年,張平寬研(yán)究了在軸向振動鑽削過程中,各切削參數的變化,對鑽頭的工作角度會(huì)產生很大(dà)影(yǐng)響,給出了振動鑽削參數選擇的理論依據。2006 年,北京航空航天大學張德(dé)遠等對微孔加工難題進行了研(yán)究,釆用超聲振動(dòng)加工將微孔(kǒng)壽(shòu)命提(tí)高了 10 倍(bèi)以上。
在振動鑽削係統裝備研究方麵(miàn),隈部淳(chún)一郎教授成功研(yán)製出超聲波扭轉和低頻軸向複合振動鑽孔設備,極大地增強了振動鑽削的加工(gōng)能力。美國學者 W.Hansen 在對低頻振動鑽削的研究過(guò)程中,提出了低頻振動鑽削的概念和方法(fǎ),研製了安裝在自動車床上的用凸輪控製的機械式軸向振動鑽削裝置並進行了實驗研究,發現低頻振動鑽(zuàn)削能(néng)夠(gòu)減少鑽頭燒傷,提高鑽頭壽命,加快(kuài)排屑過程以(yǐ)及提高孔的位置精度。這一研究成果為“鑽頭(tóu)剛性化效果”理論及脈衝能(néng)量(liàng)和(hé)應(yīng)力集中理論提供了強有力的依據,並為振(zhèn)動斷屑理論的提出(chū)奠定了基礎。1982 年,薛萬夫教(jiāo)授成功研發出一種(zhǒng)安裝在機床溜板上的低頻振動刀架,通過采用伺服電機驅動偏(piān)心凸輪實現鑽頭(tóu)的低頻軸向振動,並對鈦(tài)合金(jīn)等(děng)典型(xíng)難加工材料進行驗(yàn)證實驗。
實驗證明,對於難加工材料,采用低頻振動鑽削可有效提高刀具耐用度、降低切削力、抑製刀杆振動以及(jí)保證斷屑穩定。1986年,哈工大劉華明研發用於台鑽的電磁振動工作台(tái),並深入分析鑽頭耐用度與振(zhèn)幅之間的聯係。1994 年,西安石(shí)油大學王世清教授等人設計研發了機械式軸向激振裝置,其振幅與頻率均連續可調。1997 年,原吉林工業大學高印寒教授研製開發出能夠產生複合振動永磁振動鑽削裝置。2007 年西安(ān)石油大學深孔加工研究所的楊立合等(děng)人基於高頻振動切削原理,自行設計階梯型複合變(biàn)幅杆,研製了一套旋(xuán)轉超聲振動鑽削裝置,該(gāi)裝置在一定固有頻率的(de)情況下達到係統諧振,滿足要求。
在(zài)振動鑽(zuàn)削數學模型建立方麵,2002 年,佳木斯(sī)大學盧紅影在 Merritt 等人所建立的傳(chuán)統切削閉環模型的基礎上,考慮刀具振動對機(jī)床的結(jié)構以及切削(xuē)過程的動態特性的影響,建立低頻(pín)振動切削數學模型,並提出了低頻振動切削可使加(jiā)工係統剛性化的觀點。2006 年,華東理工大學王曉威從運動學角度分析研究振動切削的內在特性,並在傳統切削模型的基礎上給出了振動切削的數學(xué)模型。
提出振動切削切削力較小且(qiě)切削過程比傳統切削更穩定的觀點。2012 年,西安理工大學李言等人在自由模態綜合技術的基礎上構建了深(shēn)孔振動鑽削(xuē)加工過程中鑽杆在軸向振動、振動切削力以(yǐ)及切削液(yè)流體力綜合(hé)作用下的多跨動力學有限元模型,並通過該模型研究輔(fǔ)助支撐的位置及加工(gōng)深度(dù)對孔直線度(dù)誤差的影響,獲(huò)得了孔直線度變化規律,為(wéi)深孔振動(dòng)加工機床(chuáng)的精度設計以及加工(gōng)誤差分(fèn)析提供了理論依據。
中航工業佐景濤通過(guò)分析低頻超聲振(zhèn)動切削過程中的運動學特征,構建了低頻超(chāo)聲振動切削力學模型,認為(wéi)振動(dòng)切(qiē)削係統具有較高的穩定性。從(cóng)上述國內外研究現狀可以(yǐ)看出,雖然學術界在鑽削顫振(zhèn)的研究方麵(miàn)已經取得了大量(liàng)的成果,但從過程阻(zǔ)尼的角(jiǎo)度探索(suǒ)鑽削顫振的產生(shēng)本質、影響因素及其控製(zhì)等方麵(miàn)的研究還很少,尤其是針對鈦合金這種難加工材料的超長小直(zhí)徑深孔鑽削顫振控製基礎理論與方法研究還不夠深入和係統,現(xiàn)有深孔鑽削顫振理論研究仍(réng)無法為顫振主動控製技術提供統一判據和基礎支撐。
並且對於振動鑽削的(de)研究,學術界主要集(jí)中在使用高(gāo)頻(pín)超聲振動和機(jī)械式振動鑽削,研究的對象主要集中在麻花鑽和 BTA 噴(pēn)吸鑽。對於小直(zhí)徑深孔振(zhèn)動(dòng)鑽削(xuē)主(zhǔ)要還是采用超聲振動方案,刀具的選擇還(hái)是為(wéi)小直徑的麻花鑽。而對(duì)於槍鑽(zuàn)的振動切削研(yán)究相對較少。
5 、總結與展望
深孔(kǒng)加(jiā)工(gōng)顫振一直是機加工領域無(wú)法(fǎ)回避和亟(jí)待解決的關鍵技術難題之一。加工過程中,鑽削力大小和方向都隨時間周期性變化,加上槍鑽係統自身具有多自由度的結構動力學(xué)特性,使深(shēn)孔鑽削過程的穩定性分析變得非常複雜。國(guó)內外(wài)學者在深孔加工顫振方麵的研究,主要集中在顫振穩(wěn)定性(xìng)分析和顫振控製等方麵。因此仍存在以(yǐ)下問題有待繼續深入研究。
1) 現有研究關於建立深孔(kǒng)鑽削顫振模型,主要是將物理模(mó)型轉化為時滯微分方程,然(rán)後通(tōng)過半解析法或數(shù)值方法來求(qiú)解,並結合穩定性 lobe 圖來分析係統穩定性,或結合(hé) Nyquist 判據或 Liapunov 判據(jù)來進行係統穩定性(xìng)分析。該方法建模複雜(zá),求(qiú)解過程繁瑣,實用性不高。能否引入統一的判據如勞斯判(pàn)據建立鑽削顫振模型,通過阻尼歸(guī)一化的原理,係統的分析槍鑽各部分結構在顫振中的作用(yòng)機製,實現對深孔槍鑽鑽削穩定性的直觀快速判別。
2) 當前難(nán)加工材料如鈦合金等是研(yán)究的熱點 ,其單位麵積切削力倍增,可選加工速度範圍有限,穩定(dìng)性(xìng)極限大大降低且範圍窄,因此需要引入考慮(lǜ)過(guò)程阻尼效應的非線性理論,以擴大穩定域,提高加工效率(lǜ)。但目前對於(yú)過程阻尼的研究,主要集中在車削方(fāng)麵,對於深孔槍鑽鑽削加工的(de)過程阻尼效應,尚缺少完善的動力學(xué)分析模型。
3) 深孔鑽削加工中過程阻尼的大小,與槍鑽結構(gòu)參數如刀尖的後刀麵(miàn)、外刃的(de)第一後刀麵、內刃、導流麵等密切相關,然(rán)而現有深孔槍鑽鑽(zuàn)削顫振控製方(fāng)法(fǎ)中,槍鑽結構的優化設計,均沒有係統考慮(lǜ)過程阻尼效應,在減振槍鑽結構設計方麵仍缺少完善的理(lǐ)論(lùn)支撐,因而有必要建立(lì)基於過程阻尼效應的(de)深孔槍鑽鑽削顫振主(zhǔ)動抑製刀(dāo)具的設(shè)計理論(lùn)與方法(fǎ)。
4) 深孔振動鑽削的研究(jiū)主(zhǔ)要集中(zhōng)在低頻超聲振動鑽削,研究對象也以麻花鑽和噴吸鑽為主。對於(yú)槍鑽的振動鑽削研究很少,而將鑽削顫振轉化(huà)為(wéi)振動鑽削的研究目前屬於空(kōng)白,如何設計這種自激振動鑽削裝(zhuāng)置和實(shí)現(xiàn)其(qí)顫振的主動控製和(hé)如何選擇其加工(gōng)工藝的參數滿足鈦合(hé)金超長小直徑的(de)深孔(kǒng)加工,將是本項目研究(jiū)的主要創新之處。
對以上問題,本課題將係統研究(jiū)基於(yú)勞斯判據(jù)的深孔槍鑽鑽削顫振機(jī)理分析與顫(chàn)振抑製策略,建立基於過程阻尼效應的非線性深孔鑽削動力學模型和穩定性極限預測,提出小直徑深孔鑽削顫振主動抑製的設計理論與方法; 解決麵向超長小直徑深孔鑽削振動主動抑製的工藝新技術。並為解決鈦合(hé)金等難加工材料的超長小(xiǎo)直徑深孔鑽削問題(tí)提供理論方(fāng)法與技術支(zhī)撐,促(cù)進航空(kōng)航、能源、軌道交通等國家重點(diǎn)發展行業產品核心零件的“控形”與“控性(xìng)”加工技術的進(jìn)步,豐富製造(zào)技術基礎理論,推動製造技術發展,為我國占領(lǐng)製造學科前沿奠定基礎,項目研究具有重要的理論意義和工程應用價值。
投稿箱:
如(rú)果您有機(jī)床行業(yè)、企業相關新(xīn)聞稿件發表,或進行資訊合作,歡(huān)迎聯係本網編輯部, 郵箱(xiāng):skjcsc@vip.sina.com
如(rú)果您有機(jī)床行業(yè)、企業相關新(xīn)聞稿件發表,或進行資訊合作,歡(huān)迎聯係本網編輯部, 郵箱(xiāng):skjcsc@vip.sina.com
更多相關信息
業界視點
| 更多
行業數(shù)據(jù)
| 更多
- 2024年11月 金屬切削(xuē)機床產量數據
- 2024年11月 分地區金屬切削機(jī)床產量數據
- 2024年11月 軸承出(chū)口情況
- 2024年11月 基本型(xíng)乘用車(轎車)產量數據(jù)
- 2024年11月 新能源汽車產量數據
- 2024年11月 新能源(yuán)汽車銷量情(qíng)況
- 2024年10月(yuè) 新能源汽車產量數據
- 2024年10月 軸承出口情況
- 2024年10月 分地區金屬切削機床產量數據(jù)
- 2024年10月 金屬切削機床產量數據
- 2024年9月 新能源汽車銷量情況
- 2024年8月 新能源汽車產量數據
- 2028年8月 基本型乘用車(轎車)產量數(shù)據
博文選(xuǎn)萃(cuì)
| 更多
- 機(jī)械加工過程圖示
- 判斷一台加工中心精度的幾種辦法(fǎ)
- 中走絲線(xiàn)切割機床的發展趨勢
- 國產(chǎn)數控(kòng)係(xì)統和數控(kòng)機床何(hé)去何從?
- 中國的技術(shù)工人都去(qù)哪裏了?
- 機械老板做(zuò)了十(shí)多年,為何還是小作坊?
- 機械行業最新自殺性營銷,害人害己!不倒閉才
- 製(zhì)造業大逃亡
- 智能時代,少談點智造,多談點製造
- 現實麵前,國人沉(chén)默。製造業的騰飛,要(yào)從機床
- 一文搞懂數控車床加工刀具補償功能
- 車(chē)床鑽孔(kǒng)攻螺紋(wén)加工(gōng)方法及工裝設計
- 傳統鑽削(xuē)與螺旋銑孔加工工(gōng)藝的區別