掛車車軸(zhóu)加工的全新工藝及機(jī)床的研究
2021-5-18 來源: 寧夏長興精密機械有限責任公司 作者:施(shī)文(wén)秀(xiù)
摘要:汽車掛車軸專門化數控車床用於掛車軸的車削加工,掛車軸軸身部分為方形或圓形,車軸全長(zhǎng)1.8~2.8 m。車(chē)軸需根(gēn)據毛坯(pī)尺寸不同加工成長度不同(tóng)的成品(pǐn)車軸。本文提出的掛車車軸加工全新藝為(wéi):在(zài)一台機床上,一次上下料即可自動完成車軸兩端的(de)全部車削加工。
關鍵詞:掛車車軸;加工工藝;基準轉換;多連杆測量
汽車掛車軸是汽車車輛(liàng)的重(chóng)要零(líng)部件,主要用於半掛載貨車的長途運輸。隨著公路(lù)網絡的建設及物流運輸的快速發展,該(gāi)零部件市場有(yǒu)很大的需求。目前全國生產該產品的主要廠家有近百家,年(nián)產銷量180餘萬件。大部分廠家製造該產品的工藝及設備(bèi)都比較落後,車軸兩(liǎng)端(duān)的加工均采用分散工藝(yì),一個車軸的軸端(duān)加工約需5~8序完成,存(cún)在生產效率低、製造精度低(dī)、人工(gōng)成本高、生產流程長及難以實現自動化等問題。
通過對現行掛(guà)車軸加工工藝(yì)的分析研(yán)究,充分了解用戶不同車軸製造工(gōng)藝、不同技術(shù)要求,本文提出的加工工藝采用高度集成的加工工藝,可實現一次裝夾,完成(chéng)車軸兩端內(nèi)孔、外圓(yuán)以及端麵的所有車削加工工序內容。為達到本加工工藝要求,機床通過總體方案設計、裝夾基準自動轉換、自動輸送料裝(zhuāng)置、自動化(huà)控製技術等關(guān)鍵技術的研究,以及自動檢測裝置、高精度尾架、主軸托料裝置、送料裝置等關鍵部件的研發,最終設計形成了本文論述(shù)的掛車軸加工用的雙端麵專門化數控(kòng)車床。現就掛車軸(zhóu)的加工工藝和本文論述的雙端麵專門化數控車床的大體結構進行介紹。
1、 車軸生產工藝分析及新型生(shēng)產工藝推(tuī)薦
為詳細了解車軸加工工藝,先介紹掛車車軸的結構(gòu)及要求,汽車掛車軸有很多種(zhǒng),按形狀不同,分為實心方型車軸(zhóu),空心方管車軸、空心圓管車軸,其中空心方管車軸按形狀和尺寸不同又分為美式車軸和德式車(chē)軸。其大體結構見圖(tú)1:掛車車軸結構示意圖。掛車軸要求除外圓內(nèi)孔(kǒng)的通用車削加工要求外,要求後軸承(chéng)位、油封位、過渡(dù)圓弧麵以及底板位壁(bì)厚均勻且不得(dé)小於要求最小值,所以(yǐ)為保證壁厚均(jun1)勻,在加工車軸前,應先對檢測(cè)軸肩進行軸向位置測量,以測量軸肩位置為加工工件的軸向基準,以最小(xiǎo)加工餘量完(wán)成車軸外圓、內孔和端麵的加工。掛(guà)車車(chē)軸兩端(duān)車(chē)加工的形位公差、尺寸公差等精度要求均較高,本文不做過多贅述。
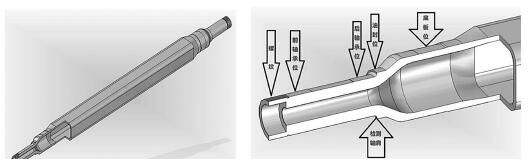
圖1 掛車車軸結構示意圖
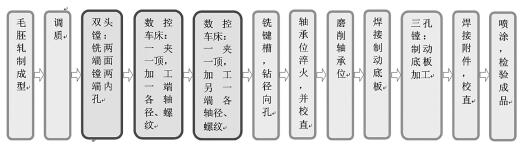
圖(tú)2
1.1 整體車(chē)軸傳(chuán)統生產工藝
工序1:毛胚軋製成型。
工序2:毛胚調質。
工序3:雙頭鏜床(chuáng)/銑專機:加工兩端端麵、內孔/中(zhōng)心(xīn)孔。為保證加工零件壁厚均勻的要求,此序加工工藝基(jī)準為軸承位,軸向檢測油封位檢測軸肩。
工序4~5:采用單刀架通用數控車床:掉頭加工兩端軸徑各部位。此序(xù)加工工藝基(jī)準為(wéi)前序加工的內(nèi)孔及錐麵,軸向(xiàng)檢測端麵位置。少(shǎo)部分用戶用雙刀架(jià)數控車床:一端由主(zhǔ)軸夾(jiá)具內撐(chēng),另一端尾架(jià)頂緊,加工兩端軸徑各部位。采用此設(shè)備比單刀架數控車床效率高,但(dàn)加工一些特定(dìng)車軸,存在由於內孔較(jiào)小,內(nèi)撐夾具傳遞扭矩不夠,不能大扭矩車削等加工質量問題。
工(gōng)序6:銑鍵槽、鑽(zuàn)徑向孔。
工序7:熱處理:軸徑淬火、校直;也有用戶軸徑不(bú)淬(cuì)火。
工(gōng)序8:磨兩端外圓軸(zhóu)承(chéng)位,也有客戶軸徑不淬火,而選用毫克能的。
工序9:焊接製動底板等附件。
工序10:加工製(zhì)動底板端麵孔,或者外側端麵(碟(dié)刹車軸)。
工序11:焊接(jiē)叉架、校直。
工序12:噴塗、檢驗,然後轉車軸(zhóu)總成裝配。
按照此傳統工藝進行車削加工,從工序3~工序5,工序3序(xù)完成車加工工序,掛(guà)車軸零件外形不規則,長度1.8m~2.8m,單件(jiàn)重約150Kg,采用傳統工藝多次上下料(liào),增加(jiā)製造過程的輔助時(shí)間,生產效率低,人工上(shàng)下料不易操(cāo)作,工人勞動
強度大。並且存在發(fā)生特(tè)定車軸內孔小,撐內孔尾架頂緊工件時,夾緊力不(bú)足,發生加工(gōng)效率低下或夾持不牢造成廢(fèi)品等質量問題的可能性。
1.2 整體車軸全新生產工藝
為(wéi)改善和解決(jué)上述傳(chuán)統(tǒng)生(shēng)產工(gōng)藝所存在的問題,提出本文論述的全新生產工藝及車加(jiā)工設備。
新(xīn)工藝將傳統生產工藝中工序3~工序5結合在一台機床上進行加(jiā)工,其(qí)餘傳統加工工藝(yì)不做大幅變動。因工序3加工(gōng)工藝基準(zhǔn)為後軸承位,工序4~工序5加工工藝基準為工序3加工的內孔及(jí)錐(zhuī)麵。如將(jiāng)工序3~工序5結合在一台機床上完
成,加工過程中,機床需具備(bèi)工藝基準轉換的能力。為此(cǐ)結合中間驅動雙端麵數控車床的結構(gòu),提出開發(fā)本文論述的掛(guà)車(chē)軸加工用雙端麵專門化數控(kòng)車床。
2 、 掛(guà)車軸加工用雙端(duān)麵專門化(huà)數控車床方案及結構
通過對掛車車(chē)軸加工工藝的分(fèn)析,以及(jí)上述全(quán)新工(gōng)藝的解析,結合用戶全自動上下料要求和(hé)雙端麵數控(kòng)車床的結構特點,應用(yòng)模塊(kuài)化設計思路,完成了(le)掛車軸(zhóu)加工用(yòng)雙端麵專門化數控車床的總體方案設計:機床采用45°斜床(chuáng)身布局,剛(gāng)性好,排屑方便。機床采用(yòng)雙通道控製係統,左右刀架安裝在上導軌,可同(tóng)時或(huò)分別與主軸聯動,完成零(líng)件兩端的同時(shí)或順序加工(gōng)。由一台機床完成軸端的全部加工,主、副主軸箱夾具夾持(chí)軸端軸承位,雙端同時(shí)加工端麵、內孔和錐麵,然後夾持基準自動轉換,轉為由左(zuǒ)右尾架頂持工件(jiàn)兩端錐麵,主軸箱浮動夾具(jù)夾持軸體並傳遞扭矩,加工軸端外圓各部位。按照工藝要求,機床總體布局方案見圖3。
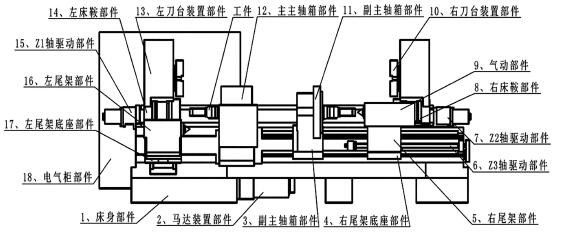
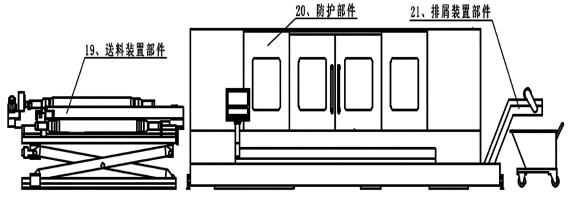
圖3 機床總體布局方案
附圖中所示序號代表的名稱:
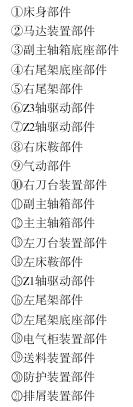
機床(chuáng)為了加工(gōng)工件的高精度和高效率,配置了自動上下料裝置(zhì),上下料裝置通過懸(xuán)伸臂(bì)將工(gōng)件送入機床,至主主軸箱(xiāng)左端,為配合上(shàng)下料,機床主軸箱內孔設有滾動托料裝置,輸送料道的懸臂上帶有動力(lì)裝置。上料時,工件(jiàn)向(xiàng)前(qián)移動,右端刀架(jià)對(duì)工件進行粗定位,當工件(jiàn)進入加工位置後,主軸箱夾持工件(jiàn),懸臂收回;由左右兩套軸向檢測(cè)裝(zhuāng)置(zhì),檢測並反饋工件測量軸肩的位置,對機床程序進行自動(dòng)修正,從而實現零件的精確軸(zhóu)向定位,完(wán)成工件第一工步的加工。第一(yī)工步加工完成後,左尾架升起,主主軸箱卡爪鬆開,副主軸箱拖動工件至左尾架頂尖定位,副主軸箱卡爪鬆開並繼續向左移動,至(zhì)右尾架頂緊範圍,右尾架與左尾架共(gòng)同頂緊(jǐn)工件,實現工件定心,主主(zhǔ)軸(zhóu)箱右端卡爪浮動夾持工件,帶動工件(jiàn)旋轉,完成工件第二工步的(de)加工。第二工步加工完成後,主軸卡爪鬆開,兩尾架鬆開,左尾架下降,輸送料道的懸臂伸入機床,將工件拖出機床。機床完成單次加工循環。
3、新型工藝的優點和特點
(1)工序集中,減少了工件裝夾次數,減少了輔助加工時間,采用兩端同時加工工藝,生產效率顯著提(tí)高。
(2)一次(cì)上料,兩端同時加工,提(tí)高了車軸的加工精度和同軸度。
(3)縮短生產工藝流程,減少生產現場零件周轉,提高場地作業麵積使(shǐ)用效率,有利於提高生產(chǎn)的組織管理(lǐ)。
(4)由於采用了高效加工設備,本機床在研發之初就已經考慮(lǜ)了配備上(shàng)下料裝(zhuāng)置及儲料裝置,這樣很容易就可(kě)以(yǐ)實現全(quán)自動化生產,以降低人工製造(zào)成本。
(5)工(gōng)件在中間位置夾(jiá)緊,裝夾可靠,傳遞機床切削時所需的扭矩足夠,尤其是對端(duān)麵內孔較小的車軸,或者實體車軸而言,相(xiàng)比端麵驅動方式,可以進行大(dà)餘量車削,機床剛性強、加工精度高。
(6)機床可帶自動檢測裝置,尤其是對空心車軸,可以確保加工後的車軸壁厚均勻。
(7)如果車軸兩端的鍵槽和徑向孔需要加工,則本機(jī)床(chuáng)也可配置(zhì)動(dòng)力刀架,將後序的鍵(jiàn)槽和徑向孔(kǒng)一起(qǐ)加工完成。
4、攻克的掛車軸加工用雙端麵專門化數控車床(chuáng)技術難題(tí)
(1)開發了滿足各種掛車軸全新加(jiā)工工藝的需求,可實現轉換基準、軸肩(jiān)測量、自(zì)動上下料等功能(néng)的中間驅動車床的機床布局方案。
(2)研製成功了高性能主軸(zhóu)箱。雙端麵數控車床的核(hé)心關鍵技術在(zài)於中間驅動(dòng)、夾持零件實現雙端車削的主(zhǔ)軸箱,主軸箱的性能、水平決定了整機的性能、水平。其結構(gòu)是將主軸係統、夾具、夾緊油缸、配油係統、驅動(dòng)裝置一體化(huà)設計。滿足掛車車軸加工(gōng)工藝要求。
(3)多連杆擺臂測量裝置,可實現車軸加工時毛坯的軸(zhóu)肩測量,由於測量點位於主軸箱孔內部,測量裝置需(xū)從卡爪中(zhōng)間較小空間內進入測量,檢測裝置采(cǎi)用多連杆機構從而完美解決(jué)這一難題。
(4)機床左端上下料輔機,輔機可將工件從機床左側將工件滾(gǔn)動送入主軸箱,等加工完成後,可(kě)將工件從機(jī)床內拖出(chū),輔機可根據用戶需求,進一(yī)步擴展與自動(dòng)線連接,實現自動線(xiàn)全自動生產。
(5)為配合上下(xià)料動作,主軸箱內孔設計(jì)了專門的(de)滾動托料架,以降低(dī)車軸在上下料(liào)過程中的摩擦阻力。方便上下料。
(6)機床左(zuǒ)側尾架設計了高精度上下移動的結構,滿足上下料動作的同時,實現了大切削力時尾架所需的(de)較高剛性。
(7)機床設計(jì)有三套大行程徑(jìng)向油缸(gāng)卡盤,分別可實現自定心夾持工件和浮動夾持工件的功能,從最大限度上滿(mǎn)足掛車軸全新加工工藝的需求,其最大卡爪行程(chéng)單邊可達(dá)65mm。
5、掛車(chē)車軸加工(gōng)全新工藝實現的(de)意義
汽車掛車軸在長途公路運輸中(zhōng)占據著重要的地位。提高其加工質量和加工效率其意(yì)義(yì)不言而喻;整體式車(chē)軸在(zài)車軸行業(yè)已經普遍應用(yòng),但是由於(yú)國內大部分掛車軸生產企業所用設備普遍落後,效率(lǜ)低,質量差。隨著公(gōng)路交通運輸車輛市場需求的穩步增長及(jí)車軸製造行業麵(miàn)臨設備(bèi)急需更新換代的現狀,采用高集(jí)成化、高複合化、高效率、高自動化、智能(néng)化是現代製造技術的發展方向,也是車軸製造行業眾多用戶的迫切需求。
新工(gōng)藝的實施將為(wéi)該行業提(tí)供效率高、精度(dù)高、自動化程度高、製造成(chéng)本低的先進製造設備,對促進公(gōng)路運輸的發展及國家經濟建設具有重要意義。
投(tóu)稿箱(xiāng):
如果您有機床行業(yè)、企業相關新聞稿件發(fā)表,或進行(háng)資訊合作,歡迎聯係本網編輯(jí)部, 郵箱(xiāng):skjcsc@vip.sina.com
如果您有機床行業(yè)、企業相關新聞稿件發(fā)表,或進行(háng)資訊合作,歡迎聯係本網編輯(jí)部, 郵箱(xiāng):skjcsc@vip.sina.com
更多相關信息
業界視點
| 更多
行業數據
| 更多
- 2024年11月 金屬切削機床產量數據
- 2024年11月 分地區金屬切削機床產量數據
- 2024年(nián)11月 軸承出口情況
- 2024年11月 基本型乘用車(轎車)產量數據
- 2024年11月 新能源汽車產量數(shù)據(jù)
- 2024年11月 新能源汽車銷量情況
- 2024年10月 新能源汽車產(chǎn)量(liàng)數據
- 2024年10月 軸承出口情況
- 2024年10月 分地區金屬切削機床產量數據
- 2024年10月 金屬切削(xuē)機床產量數據
- 2024年9月 新能源汽車銷量(liàng)情況
- 2024年8月 新能源(yuán)汽車產量數據
- 2028年(nián)8月 基本型乘用車(轎車)產量數據
博文選萃
| 更多
- 機械加工過程圖(tú)示
- 判斷一台加工中心精度的(de)幾種辦法
- 中走絲線切割機床(chuáng)的發展趨勢
- 國產(chǎn)數控係統和數控機(jī)床何(hé)去何從?
- 中國的技術工(gōng)人(rén)都去(qù)哪裏了?
- 機械老板做了十多年,為(wéi)何還是小(xiǎo)作坊(fāng)?
- 機械行業最新自殺性營銷,害人害己!不倒閉才
- 製造業大逃亡
- 智能時代,少談(tán)點智造(zào),多談點製造
- 現實麵前,國(guó)人沉默。製造業的騰飛(fēi),要從機(jī)床
- 一文搞懂數(shù)控車(chē)床(chuáng)加工刀具補償功能
- 車(chē)床鑽孔攻螺紋加工方法及工裝設計
- 傳統鑽削與螺旋銑孔加(jiā)工工藝的區別