鈦合金材料在我國航空緊固(gù)件中的應用
2014-1-22 來(lái)源:數控機床市場網 作者(zhě):張利軍 王幸運 郭啟義 謝田 薛祥義
鈦合金材料作(zuò)為一種 20 世紀中期出現並(bìng)發(fā)展起來(lái)的新興結構材料(liào),因其具有優異的耐腐蝕性、高(gāo)的比強度以及無磁性等一係(xì)列優點,在(zài)航(háng)空航天等端工業部門(mén)獲(huò)得了廣泛應用。在 20 世(shì)紀 50 年(nián)代,美國就已經(jīng)開始(shǐ)使用鈦(tài)合(hé)金材料製造航空緊固件,我國從20世紀 80 年代開(kāi)始才陸(lù)續使用鈦合金材料製造少量的工程用航空航天緊固件,進入(rù) 21 世紀之後,隨著我國航空航天(tiān)工業製造技(jì)術水平的整(zhěng)體提升,緊固件用鈦合金材料及其(qí)加工製造技術獲得了係統化、專業化(huà)的發展。
關鍵詞: 緊固件 鈦合金 航空
鈦及鈦合金(jīn)由於具有比強度高、抗腐蝕性好、耐高溫等一係(xì)列突(tū)出優點,使其發展成為現代航空航天工業中廣有前途的金屬結構材料。自從 20 世紀 50 年(nián)代美國首次將(jiāng) Ti-6Al-4V 鈦合金螺(luó)栓(shuān)應用於 B-52 型轟炸機上,並取得了非(fēi)常(cháng)好的減重(chóng)效果後,各航空工業發達國家都紛紛展開了鈦合金緊固件的研究及工程應用。鈦合金緊固(gù)件代替大部分比強度較低的鋼製緊固件後,對飛行器減重取得非常顯著的效果。如波音 747 飛機緊固件以(yǐ)鈦代鋼後,其結構質量減輕了1814 kg;俄羅斯的伊爾 -96 飛機,一架(jià)用 14.2 萬(wàn)件鈦合(hé)金緊(jǐn)固(gù)件,較鋼件重量減(jiǎn)輕達 600kg ;一架圖 204 飛機上采用 940kg 的BT16 鈦合金緊固件,較鋼件減輕(qīng) 688kg[4]。鈦合金的(de)正電位性能恰好與碳纖維複(fù)合(hé)材料相匹配, 有效地防止了緊固(gù)件的電(diàn)偶腐蝕,使鈦合金成為複合材料的最佳連接材料(liào)。因此(cǐ),隨(suí)著先進軍民用飛機鈦合金和複合材料用量的不斷增加,對鈦合(hé)金緊固件的(de)需求日益增加。鈦合金比鋁合金的使用(yòng)溫度(dù)高出 150~200℃,對於在飛行器結構中因工作溫度過(guò)高而不能采(cǎi)用鋁合金緊(jǐn)固件的部位,鈦合金將是一(yī)種更好的選擇。此(cǐ)外,鈦合金所固有的(de)良好彈性和無磁性,對(duì)防止緊固螺(luó)栓的鬆(sōng)動和防(fáng)磁場幹擾也具有非常重要的作用。
在美國(guó)軍民(mín)用飛機上,鈦合金緊固件(jiàn)已基本取代了合金鋼緊固(gù)件(jiàn)。國外鈦合金緊固件(jiàn)的應(yīng)用已經非常普遍,大型民用飛機單機鈦合金緊固件的用量達到數十萬(wàn)件,同時各類新型的鈦合金緊固件也被不斷地研製開(kāi)發出來。我國鈦合(hé)金緊固件的研製曆史可追溯到 1965年(nián),成都飛(fēi)機設計(jì)研究所根據新(xīn)機需要提出研製鈦合金鉚釘,20 世紀 70 年代相(xiàng)關單位進行了鈦合金鉚釘及應用研究工(gōng)作,20 世紀 80 年代在我國部分第二代軍用飛機上(shàng)開始少量使用鈦合金鉚釘、螺(luó)栓等緊固件。20世紀 90 年代後期,隨著國外第三代重型戰鬥機生產線的(de)引進和國產(chǎn)第三代戰鬥機的研(yán)製,以及大(dà)量航(háng)空轉包生產業務的開展,我國航空工(gōng)業中開始使用一些(xiē)鈦合金緊固件(jiàn)。近年來隨著我國航空航天工業的發展,國內相關單位有針對(duì)性地開展了大量基礎材料與緊固件製造(zào)技術(shù)方麵的研究開發工作,目前(qián)我國自主研製生(shēng)產的鈦合金緊(jǐn)固件已經在我國的改型飛(fēi)機和新設計的(de)飛(fēi)機中獲得了大量工(gōng)程(chéng)應用(yòng)。
1 鉚釘類(lèi)緊固件用鈦合金(jīn)材料
航(háng)空航天工業中常用的緊固件主要包括鉚釘、螺栓及特種緊固件 3 大類。對鉚(mǎo)釘來說,最重要的是材料的冷態塑性(xìng),隻有(yǒu)冷態塑(sù)性好的材料(liào)製造的鉚釘,才(cái)能夠進行冷鉚接安裝。通常在對強度要求不太高而對耐蝕性能要求高的部位采用鈦合金鉚(mǎo)釘,β 型鈦合金由於在固溶狀態下為單一的β晶粒、且由於其具有體(tǐ)心立方的原(yuán)子結構排列,所以該(gāi)類合金具有十(shí)分優異的冷加(jiā)工性能,非(fēi)常適用於製造鈦合金鉚釘
1.1 TB2 鈦(tài)合金
我國鈦合金緊固件的研製就是以 TB2 鈦合金鉚釘的研製工作(zuò)為起點的。1965 年(nián),成都飛機(jī)設計(jì)研究所在新(xīn)機研製時提出(chū),計劃在其後機身鈦結構件上采用鈦合金(jīn)鉚釘,並提出了論證和設計。從 1970 年開始,在天津冶金局材料研究所(suǒ)和有色金屬研究院等單位的配合下,成都飛機設計研究所與成飛公司聯合展開了 TB2 鈦合(hé)金鉚釘的研製及(jí)應用研究工作,先後完成了 TB2 鈦合金材料研製、絲材冷鐓成形研究、鉚釘鉚(mǎo)接試驗研究(jiū)等工作,並於 1979 年完成了相關工作技術鑒定,製訂了暫行(háng)技術條件。TB2 鈦合金是一種亞穩定型 β 鈦合(hé)金,合金名義成分 Ti-3Al-8Cr-5Mo-5V。該合金在固溶處理(lǐ)狀態下具有優異的冷成形性能和焊接性(xìng)能,我國目(mù)前主要(yào)用作製造衛星波紋殼體、星箭連(lián)接帶及各(gè)類冷鐓鉚釘,有時也用於小規格螺栓的製造。製造航空緊固件時,其使用溫度一般在 300℃以下(xià),航天(tiān)緊固件可在短時間內使用到 500℃。
1986 年,我國頒布了第一部(bù)鈦合金緊固件專用(yòng)標準 GJB120-1986《鈦合金鉚釘》,1990 年我國頒布了第2部及(jí)第3部鈦合(hé)金(jīn)緊固件專用技術標(biāo)準(zhǔn)GJB856-90 《抗拉型鈦合金環槽鉚釘規(guī)範》 與 GJB857.1-90《100°沉頭抗拉型鈦合金進環槽鉚釘》,這 3 部標準(zhǔn)都是 TB2 鈦合金鉚釘的專用技術標準,就各類規格的 TB2 鉚(mǎo)釘進行了明確規範,為其工程化批產及應用奠定了標準基礎。目前 TB2 製造的鈦合金(jīn)鉚釘(dìng)已經在(zài)我國航天工業中的多個型號獲得了大(dà)量應用,同時在航空型號產品(pǐn)中也獲(huò)得了一定數量的應用(yòng),均取得了良好(hǎo)的(de)效(xiào)果。
1.2 TB5 鈦合金
TB5 鈦合金是一種亞穩定 β 型鈦合金,其名義(yì)成分為 Ti-15V-3Cr-3Sn-3Al。該合金最初是在(zài)美國空軍的資助下開發的,由洛克希(xī)德·馬丁公(gōng)司確定成(chéng)分、TIMET公司進行規模化生產。該合金具有(yǒu)優(yōu)異的冷成(chéng)形性能,其冷成形能力與純(chún)鈦相當,可在固溶狀態下進行各種複雜零件的冷成形 (如鉚釘鉚接),時效後室溫(wēn)拉伸強度可達(dá) 1000MPa 以上,該合金由(yóu)於其 V 元素含量高,抗氧化性能較差,一般在 200℃以下的工作環(huán)境中使用,但是該合金(jīn)具(jù)有優異的抗腐蝕性能。
美國普惠(huì)公司在其生產的(de)航空發動機上(shàng)大量使用Ti-15V-3Cr-3Sn-3Al 鈦合金作(zuò)為托架,美國 B-1B 轟炸機上 Ti-15V-3Cr-3Sn-3Al 鈦合金零(líng)件的用量達到1000 多個, Ti-15V-3Cr-3Sn-3Al 鈦合金緊固件在波音(yīn)飛機上也應(yīng)用(yòng)了很多年。我國使用 TB5 鈦合金替代30CrMnSiA 製造某殲擊機傘梁以及製造衛星發動機波紋板等部(bù)件,同時采用(yòng) TB5 鈦合金製造與殲擊機傘梁和衛星波紋板配套(tào)使用的冷鐓鉚釘。1.3 Ti-45Nb 合金Ti-45Nb 合金作為一種鉚釘專用材(cái)料,其突出的優點是塑性高(gāo) (伸長(zhǎng)率可達 20% 以上,斷麵收縮率高達 60%~80%),冷加工性能優異,其剪切強度(τ ≥ 350MPa)和抗拉強度 (σb≥ 450MPa)均高於純鈦,並且冷變形抗力低於純鈦,非常(cháng)適(shì)合做(zuò)複合材料連接用鉚釘材(cái)料。美國(guó)針對 Ti-45Nb 合金進行了大量的基礎研究工作,研製技(jì)術較為(wéi)成熟,並於(yú) 1974 年列入AMS4982 規(guī)範,2002 年修訂為 AMS4982C,至今獲得廣泛(fàn)使用。美國在航(háng)空航天鉚釘產品中,Ti-45Nb 合金已經全麵取代純鈦。該合金(jīn)與 Ti-6Al-4V 合金(jīn)搭配,製成的雙金(jīn)屬鉚釘,已經在空客和波音飛機上獲得大量應(yīng)用。
對於要(yào)求剪切強度高,在安裝(zhuāng)過程(chéng)中不允許鉚釘杆(gǎn)變形的鉚釘,一般采用雙金屬鈦(tài)合金鉚釘,雙(shuāng)金屬鈦合金鉚(mǎo)釘是(shì)由(yóu) Ti-6Al-4V 釘杆和 Ti-45Nb 頭部組(zǔ)成,經過慣性摩擦焊接,緊密融合在一起而形成了一個整體實心鉚釘。這種雙(shuāng)金屬(shǔ)鉚釘在鉚接時,隻需用較小的衝擊力就可以使 Ti-45Nb 鉚釘(dìng)頭產生塑性變(biàn)形,而 Ti-6Al-4V鉚釘杆卻不變形(xíng)。雙金屬鈦合金鉚釘在 B-1 轟炸機、波音等飛機上廣泛用於鈦合金構件及複合材料構件的鉚接。如美國 F-14 戰鬥機(jī)機翼前緣使用 4000 隻該雙(shuāng)金屬(shǔ)鉚釘,其疲勞性能與高鎖螺栓相當,而成本(běn)可降低50%,重量輕 30%~40%,這種雙金(jīn)屬鉚釘的成本要低於其他 β 型鈦合金鉚釘。近(jìn)年來我國也相繼研製開發(fā)了該型雙金屬鉚釘和 Ti-45Nb 鉚釘,已經在(zài)新一代飛機的複合材料蒙皮鉚接(jiē)中獲得了工程應用。
2 螺栓類緊(jǐn)固件用鈦合金材料
航空航天緊固件中(zhōng)使用量最大的是鈦合金螺栓,鈦合金螺栓按其用途可分為普通(tōng)螺(luó)栓、高鎖螺栓及幹涉型螺栓(shuān)等(děng)。以來製造(zào)螺栓的鈦合金材料,一般要求(qiú)其(qí)熱處理後獲得高(gāo)的抗(kàng)拉強度和剪切強度,通常要求其強度水(shuǐ)平與 30CrMnSiA 高強度合金鋼(gāng)相當。
2.1 TC4 鈦合金(jīn) (σb≥ 1100MPa 級)TC4(美國牌號 Ti-6Al-4V)鈦合金(jīn)最初由美國在1954 年首先研製成功,目前已經(jīng)發展(zhǎn)成為(wéi)一種國際性的鈦合金,是目前人們對其研究最為全麵、最為深入的鈦合金。在航空、航天、民用等工業中得到了廣泛應用。已經廣泛用(yòng)於製(zhì)造飛機結構中的梁、框、起落(luò)架、緊固件,航空發動機風扇、壓氣機盤、機(jī)匣、葉片等,同時也大量用於(yú)其他行業中,目前占鈦合金產量的一半以上。該合金(jīn)具有良好的工藝塑性和超塑性,合金 α+β/β 轉變(biàn)溫度980~1010℃,長期工作溫度可達400℃。1973年(nián)開始,為配合渦扇 -8 航空發動機 TC4 鈦合(hé)金葉片的(de)研製工作(zuò),我國開始了(le)該合金的研究與工程應(yīng)用。
1956 年,美(měi)國采用 TC4(Ti-6Al-4V)鈦合(hé)金製造了當今(jīn)世界(jiè)上第一批鈦合金螺栓,首先用在 B-52 轟(hōng)炸(zhà)機上(代替原 30CrMnSiA 螺(luó)栓),由於使用效果非常好(hǎo),很快(kuài)就被推(tuī)廣應用,現在西方幾乎所有(yǒu)的飛(fēi)機都在大量采用 TC4(Ti-6Al-4V) 鈦合(hé)金製造其(qí)螺栓。但是由於TC4(Ti-6Al-4V)是 α+β 雙相合金,不能冷鐓成形、其釘(dìng)頭必須加熱鐓製(zhì), 熱處理需真空水淬(cuì)和時效,對加工(gōng)設備及工藝要求高。20 世紀 80 年代後期,我國相關單位開展了 TC4 鈦合金緊固件(jiàn)熱鐓技術研究,先後開發出(chū)了熱鐓機床,與 20 世紀 90 年代實現了(le) TC4 鈦合金(jīn)緊固件的工(gōng)業化生產。目前(qián)我國多個航空航(háng)天標準件廠都(dōu)具有批量生產 TC4 螺栓的熱鐓設(shè)備與技術能力,采用TC4 鈦合金製造的螺栓已(yǐ)經在我國新一代軍機、航天飛行器、衛星中(zhōng)獲得了大(dà)量工程應用。
2.2 TC6 鈦合金 (σb≥ 980MPa 級)
為滿足航空(kōng)發動機高溫使用(yòng)要求,北京航(háng)空製造工程研究所研製出了可耐 500 ℃以下高溫的 TC6(俄羅斯(sī)材料 BT3-1) 鈦合金緊固件,與 TC4 鈦合金相比,該(gāi)材料對溫度具有較高的敏感性,其緊固件製(zhì)造更困難。該合(hé)金是前蘇聯研製的 BT3-1 鈦合(hé)金,名義成分為 Ti-6Al-2.5Mo-1.5Cr-0.5Fe-0.3Si,目前在俄羅斯(sī)得到廣泛應用。我國在(zài) 1979 年為(wéi)配合 WP13 航空發動機TC6 鈦合(hé)金(jīn)尾杆等(děng)部件及配套緊固件的研製工作,進行了該合金的(de)仿製工作及應用研究工作。TC6 合金是一種綜(zōng)合性能良好的馬氏體型(xíng) α+β型雙相鈦合金,一(yī)般在(zài)退火(huǒ)狀態下使用,也可進(jìn)行適當的熱處理強化。該合金具(jù)有良好的(de)性(xìng)能,抗氧化(huà)性能和耐腐蝕性能非常優異,其製造的零部件可在 400℃下長時間工作 6000h 以上、450℃下長時間工作(zuò) 2000h 以上。等溫(wēn)退火處理(lǐ)後室溫抗拉(lā)強度大於 980MPa,屈服強度大於 840MPa、延伸率(lǜ)大於 10%、斷麵收縮(suō)率大於 25%。400℃高溫(wēn)拉強度大於 720MPa、延伸率大於 14%、斷麵(miàn)收縮率(lǜ)大(dà)於 40%。為了進一步提(tí)高其使用強度,也可進行“固溶 + 時效” 處理。
2.3 TC16(σb≥ 1030MPa 級)
目前對(duì)於鋼製緊固件,大(dà)部分都采用冷鐓成形加(jiā)工,隻有少數(shù)尺寸較大的采用熱鐓成形加工,冷鐓工藝使緊(jǐn)固件實現了大批量連續生產。但是大部分工業鈦合(hé)金由於冷成形性能差,無法進(jìn)行冷鐓成形(xíng)加工。因此,在西方國家,TC4 鈦(tài)合金緊固(gù)件(jiàn)主(zhǔ)要采用熱鐓成形(xíng)工藝方法生產,熱鐓工藝的缺點(diǎn)在於:坯料加熱時易出現局部燒傷和過熱以(yǐ)及表麵氧化,同時不易實現自(zì)動化連續鐓製、生產效率低。為了提高鈦合金緊固件生(shēng)產效(xiào)率(lǜ)及其質量的穩定性,前蘇聯研(yán)製開發了緊(jǐn)固件專(zhuān)用冷鐓(duì)用BT16 鈦合(hé)金,實現了鈦合金緊固件冷鐓技(jì)術的(de)發展和跨越,並在伊爾 76、伊爾 86、伊爾(ěr) 96、安 124、Su27 係列等蘇製(俄製)飛機上獲得了大量工(gōng)程應用。
BT16(我國仿製牌號 TC16) 鈦合金名義成分 Ti-3Al-5Mo-4.5V,該合(hé)金是(shì)馬氏體型 α+β 型(xíng)雙相鈦合金,β 穩定(dìng)係數(shù)為 0.83,接近臨界成分。該鈦合(hé)金主(zhǔ)要用於製造工作溫度 350℃以下的航空緊固件,合金α+β/β 轉變溫度 (860±20)℃。較小的 β 晶粒和在退火狀態(tài)下高達 25 % 的 β 相體積分(fèn)數決定了 BT16 合金具有(yǒu)優異的室溫工藝塑性,所以該合金可在室溫條件(jiàn)下完成緊固件(jiàn)頭部的冷鐓成(chéng)形,因而明顯提高了其螺栓(shuān)生產效率、 降低(dī)了生產成本,隨後在固溶時效熱處理後其強度可達 1030~1180MPa。俄羅斯(前蘇聯) 鈦合金螺栓類(lèi)緊固件主要采(cǎi)用 BT16 鈦合金製造(zào),使用了幾十年沒有出現(xiàn)任何質量事故(gù)。我國 20 世紀 90 年代(dài)從俄羅斯引進了 Su-27 飛機生產線,為了滿足 Su-27 飛機的國產化需求,國內相關單(dān)位隨即開展了 BT16 鈦合(hé)金及(jí)其緊固(gù)件的國產化工作, 我國仿製後命名為 TC16 鈦合金(jīn)。目前,我國自主研製生產的 TC16 鈦合金螺栓已經在國產的第(dì)三代戰鬥機上獲得了大(dà)量工程應用。
2.4 TB3(σb≥ 1100MPa 級)
20 世紀七八十年代,美國等西(xī)方工業發達國家的航(háng)空航天用 1100MPa 級鈦合金螺栓主要采用 TC4(Ti-6Al-4V)鈦合金材料製(zhì)造,都是(shì)采用熱鐓成形工藝生產。我國 20 世紀 70 年代末 80 年代初應複合材料結構連接需求(qiú),急需 1100MPa 的(de)鈦合金(jīn)螺栓類緊固(gù)件,由於受到熱鐓設備的限製 (當時(shí)國(guó)內沒有熱鐓成形設備),無法研製生產 1100MPa 級的 TC4(Ti-6Al-4V) 螺栓,為此主要集中精力研製可以直接冷鐓的 β 型(xíng)鈦合金,TB3 鈦合金(jīn)就是在這(zhè)種背景條件下(xià)研製開發出來的。TB3 合金的成分設(shè)計參照了美(měi)國鈦金屬公司 20 世紀研製開發的Ti-8Mo-8V-2Fe-3Al 鈦合金。
TB3 鈦(tài)合金是一種可熱處(chù)理強化的亞穩定 β 型(xíng)鈦合金,合(hé)金名義成分為(wéi) Ti-10Mo-8V-1Fe-3.5Al。該合金的主(zhǔ)要優點是固溶處理狀態具有優異的冷成形性能,冷鐓(duì)比(Dt/D0) 可達 2.8,“固溶 + 時效” 製度處理後可獲得(dé)高的強(qiáng)度,主(zhǔ)要(yào)用於製造使用溫(wēn)度低於 300℃的 1100MPa 級高強度(dù)航空航(háng)天緊固件。1982 年 10 月,我國開始了 TB3 鈦合金螺栓的研製工作,1985 年研製工(gōng)作取得進展,並形成了相關技術規範。在(zài) 20 世紀(jì) 80年代中後期國產 TB3 鈦合金先後製成高鎖螺栓和幹(gàn)涉型螺栓,裝於飛機複合材料(liào)結構與金屬結構,為我國鈦(tài)合金螺栓類緊固件的應用(yòng)摸索出了一定經驗基礎。該合金現已廣泛用(yòng)做 1100MPa 鈦合(hé)金螺栓的製造(zào),並已成(chéng)功應用於 Y-7、J-8、J-10 飛機及某些航天飛行器上。
目前,TB3 鈦合金已成為我國能夠工業化生產的宇航(háng)飛行器用鈦(tài)合金螺(luó)栓類緊固件的(de)主要材料(liào)。同時,該鈦合金也(yě)用於鉚釘的製造,我國在 2006 年頒布的 GJB120-2006《鈦及鈦合金鉚釘》中也將 TB3 鈦材作為鉚釘用料正式(shì)列(liè)入標準。
2.5 TB8 鈦(tài)合金(jīn) (σb≥ 1280MPa 級)
隨著航空航天技(jì)術的飛(fēi)速發展,在軍民用(yòng)飛機上所采用的機械連接技術要求越來越高,其所采用的標準件技術含量也越來越高,其在整機上所起的作用已不僅(jǐn)是 “緊固” 、“連(lián)接” 作用(yòng),而是成為實現整機性能的重要結構件。未來航空航天技術的發展趨勢要求新型緊固件的比(bǐ)強度高,即要求重量輕、強度高。所以美(měi)國、俄羅斯、法(fǎ)國等世(shì)界(jiè)航(háng)空強國都在積極開發抗拉強度1200MPa 以上的高強度鈦合金材(cái)料及其緊固件。近(jìn)年來,美鋁(lǚ)公司開發出了 Timetal555 鈦合金高(gāo)強螺栓,其固溶時效(xiào)後抗拉強度(dù)達 1300MPa 以上、雙(shuāng)剪強度大於745MPa、延伸(shēn)率大於 10%,各項性能指標完全達到了典型的 1250MPa 鍍鎘合金鋼(gāng)緊固件規範的要求。SPS 航(háng)空緊固件(jiàn)集團采用 SPS TITANTM761 鈦合金加工製(zhì)造(zào)的螺栓產品 Aerlite180,其抗拉強度可達 1240MPa、剪(jiǎn)切強度可達 745MPa,達到了許多合金鋼和耐蝕合金緊固件的強度水平,同時減重 40% 。
為了緊跟國(guó)際先進航空航天鈦合金緊固件發展趨勢,近年來西工大超晶公司與信陽航天標準件廠聯合(hé)研製開發了(le)緊固件專用(yòng) TB8 鈦(tài)合金棒絲材及其(qí) 1280MPa 高強螺栓類緊固件,其規格從φ4~φ25。TB8 鈦合金是我國仿製美國(guó)的 β21S 鈦合金,其名義成分為 Ti-3Al-2.7Nb-15Mo,β21S 合金是美國鈦金屬(shǔ)公(gōng)司(Timent)1989 年為 NASP 計劃研(yán)製(zhì)開發的(de)亞穩定 β 型鈦合金,β21S鈦合(hé)金(jīn)具有優異的冷熱加工性能(néng)、深的淬(cuì)透性、高的抗蠕變性能、高的抗氧化性能和良好的抗(kàng)腐蝕性能,所以該(gāi)合金得到(dào)了飛機設計者(zhě)和(hé)製造者的認可,作為優良的宇(yǔ)航結構材料於 1994 年首先被列入美國(guó)的 ASTM 標準中,美國(guó)主要使用該(gāi)合金製造航天飛機用(yòng)鈦基複合材料及(jí)波音 777 等飛機發動機吊(diào)艙部件。我國從 20 世紀 90 年代開始進(jìn)行了該合金(jīn)的仿製工作,完成了某型飛機結構件用(yòng) TB8 鈦合金鍛件(jiàn)及鈑金件的研製及應用研究工作,由於(yú)最終沒有獲得工程化應用,僅在 GB/T3620.1-2007《鈦及鈦合金牌(pái)號和化學成分》 中對其牌號及成分(fèn)進行規範,其材料及產品沒有形成國標、國軍標(biāo)以及(jí)航標規範。
信(xìn)陽航(háng)天標準件廠與西(xī)工大超晶公司聯合研製開發的 1280MPa 級 TB8 鈦合金螺栓實物照片見圖 1,主要性能指標(biāo)見表(biǎo) 1。由於該合金的采用的 β 穩定元素為高熔點、抗氧化的(de)鉬元素和铌(ní)元素,而非 TB2、TB3 鈦合金采用的抗(kàng)氧化性能差的釩元素(sù),所以該合金製造的緊固件長時間使用溫度可(kě)達 550℃,徹底解決了傳統高強 β 鈦(tài)合金緊固件使用溫度低 (不高於 300℃)的問(wèn)題。目前,研製開發的該 1280MPa 級 TB8 鈦合金高強螺栓已經在我國新一代飛機中獲得了工(gōng)程(chéng)應用(yòng),取得了(le)良好(hǎo)的減重效果和與複合材料相容性效果。
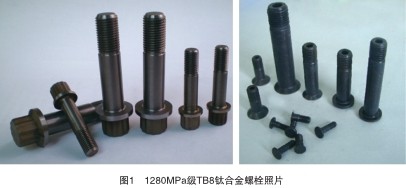
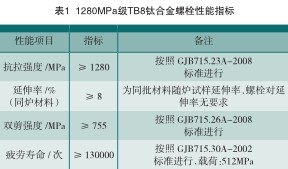
3 總結
可以(yǐ)看出,航空(kōng)用鈦合金緊固件的研究與應用自工業鈦(tài)合金出現(xiàn)就已(yǐ)經開始,美國、俄(é)羅斯(前蘇聯)等航空工業發達(dá)國家在很早就已經形成了(le)符合自身工藝(yì)技術的緊固件用鈦合金材料體係,鈦合(hé)金(jīn)緊固件已(yǐ)經(jīng)在其航空製造領域獲得了大量應用。而我(wǒ)國航空用(yòng)鈦合金緊固件的研究及應用起步較晚,都是在航空發動機或飛機的(de)仿製、技術借鑒或引(yǐn)進改進過程中被動進行的,製造緊固件的鈦合金材料基本都是借鑒或仿製(zhì)俄羅斯(前蘇聯)、美國的,同時我們國家航空緊固件中鈦合金緊固件的占有量相對(duì)較低。隨著(zhe)我國航(háng)空工業的迅速發展及對飛行器性(xìng)能要求的不斷(duàn)提高(gāo),未來高性能航空緊固件對其製造鈦(tài)合金材料提出了更高強度、更高斷裂韌性、更高疲勞性能要求。
投稿箱:
如果(guǒ)您有機床行業、企(qǐ)業相關新聞稿件發表,或進行資訊合作,歡迎聯係本網(wǎng)編輯部, 郵(yóu)箱:skjcsc@vip.sina.com
如果(guǒ)您有機床行業、企(qǐ)業相關新聞稿件發表,或進行資訊合作,歡迎聯係本網(wǎng)編輯部, 郵(yóu)箱:skjcsc@vip.sina.com
更多相關信息
業界視點
| 更多
行業數據
| 更多
- 2024年11月 金屬(shǔ)切削(xuē)機床產量數據
- 2024年11月 分地(dì)區金(jīn)屬切削機床產量數據(jù)
- 2024年11月 軸承出口情況
- 2024年11月 基本(běn)型乘用車(轎車)產量數據
- 2024年11月 新(xīn)能源汽車產量(liàng)數據(jù)
- 2024年11月 新能源汽車銷量情況
- 2024年10月 新能源(yuán)汽車產量數(shù)據
- 2024年10月 軸承出口情況
- 2024年10月 分地區金屬切削機床產量(liàng)數據
- 2024年10月 金屬(shǔ)切削機床(chuáng)產量數據
- 2024年9月 新能源汽車銷量情況
- 2024年8月 新能源汽車產量數據
- 2028年8月 基本型乘用車(轎(jiào)車)產量數據
博(bó)文選萃
| 更多
- 機械加工過(guò)程圖(tú)示
- 判斷一台(tái)加工中(zhōng)心精度的幾種辦(bàn)法(fǎ)
- 中走(zǒu)絲線切割機床的發展趨勢
- 國(guó)產數控係統和數控(kòng)機床何去何從?
- 中國(guó)的技術工人都(dōu)去哪裏了?
- 機械老板做了十多年,為何還是小作坊?
- 機械行業最新自殺性營銷(xiāo),害人害(hài)己!不倒閉才
- 製造業大(dà)逃亡
- 智(zhì)能時代,少(shǎo)談點智造,多談點製造
- 現實(shí)麵前,國人沉默。製造業的騰飛,要從機(jī)床
- 一文搞懂數控車床加工刀具補償功能
- 車床鑽孔攻螺紋加工方法及工裝設計
- 傳統鑽削與(yǔ)螺旋銑孔(kǒng)加工(gōng)工藝的區別