現代航空發動機整體葉盤及其製造技術(shù)
2014-1-20 來源:數控機床市場網 作(zuò)者:黃春(chūn)峰
[ 摘要] 整體葉盤是現代航空發動(dòng)機的一種新型結(jié)構(gòu)部件(jiàn), 對(duì)於提高其性能具有重要作用。本文主要介紹了航空發動機整(zhěng)體葉(yè)盤結構(gòu)的特點、應用現狀、發展趨勢及其製造技術(shù)。
關鍵詞: 發(fā)動機結構 整體(tǐ)葉盤 特種加工 製造技術
現(xiàn)代航空發動機的結構設計(jì)和製造技術是發動機研製、發展、使用(yòng)中的一個重要環節, 為滿足以 F119、F120、 EJ200 為標誌的第 4 代戰鬥機用發動機(jī)以(yǐ)及未來高推比新概念發動(dòng)機的性能要求, 除采用先進(jìn)技術減少飛機機體結構、機載設備的重(chóng)量外, 關鍵是要求發動機的推重比達到 10 這一級, 重點突破發動機部件的氣動(dòng)、結構設計、材料、工藝等方麵的關鍵技(jì)術。其中,在發動機風扇、壓(yā)氣(qì)機(jī)、渦輪(lún)上采用整體葉盤(Blisk) 結構( 包括整體(tǐ)葉輪、整體葉環) 是重要措(cuò)施。
1 整體葉盤結構的特點(diǎn)
(1) 整體葉盤是航空發動機的一種新型結構部件,它與(yǔ)常(cháng)規葉盤連接相比有以下(xià)特點:·不需葉片(piàn)榫頭(tóu)和榫(sǔn)槽連(lián)接的自重和支(zhī)撐這些重量的結構, 減輕了發動機風扇、壓氣機、 渦輪轉子的重量。英國 R· R 公司在發動機中采用整體葉盤結構後(hòu), 與傳統的葉片、輪盤分體結構相比, 重量可減輕50%; 若采用金屬基複合材料 (MMC) 的整體葉環(Bling), 則可減重 70%。·原輪緣的榫頭變為鼓筒; 盤變薄, 其內孔直徑變大; 消除了盤(pán)與榫頭的接(jiē)觸應力(lì), 同時也消除了由於榫頭安裝角引起的力(lì)矩產生的擠壓應(yīng)力; 減輕了盤的重量, 提(tí)高了葉片的振動頻率。
·整體葉盤可消除常(cháng)規葉盤中氣流在榫根與榫槽間縫(féng)隙中逸流造成的損失(shī), 使發動機工作效(xiào)率增加, 從而使整台發(fā)動機推重比顯著(zhe)提高。
·由於省去了安裝邊(biān)和螺栓、螺母、鎖片等連接件, 零件(jiàn)數量大大減少, 避(bì)免了榫頭、榫槽間的微動摩損、微觀裂紋、鎖片損壞等意外事故, 使發動機工作壽命和安全可靠性大大提高。
·如整體葉盤葉片損壞, 為避免拆換整個轉子, 將整體葉盤與其他級用螺栓相連, 形成可(kě)分解的連接結構。
·由於高壓(yā)壓氣機葉片短而薄, 葉片離心力較(jiào)小,輪(lún)緣徑向厚度小, 采用整(zhěng)體葉盤結構減重不顯著。例如F414發動機的高壓壓氣機, 前3級采用整體(tǐ)葉盤後重量隻(zhī)減少3.632kg;而兩(liǎng)級風扇采用整體葉(yè)盤減重20.43kg, 因此EJ200發動機的高壓壓(yā)氣機僅(jǐn)第一級采用整體葉盤結構。
(2) 航空發動機整體葉盤結構在(zài)研(yán)究發展中(zhōng)也存在一些問(wèn)題。
·整體葉盤(pán)加工困難, 隻有製造(zào)技術(shù)發展(zhǎn)到一定水平後(hòu), 整體葉盤的應用才成為可能。
·發動機在使用過程中, 轉子葉片常遇到外物打傷或因(yīn)振動葉片(piàn)出現裂紋, 整體葉盤要更換葉片非常困難, 有可能(néng)因為一(yī)個葉片損壞而報廢整(zhěng)個整體葉盤。因此風扇的第1、2級一般不用整(zhěng)體葉盤結構, 整體葉盤葉片的修理技術也是整體葉盤擴大應用必(bì)須解決的關鍵問題。
·由於(yú)整(zhěng)體葉盤(pán)的(de)葉型(xíng)複(fù)雜, 精度(dù)要求高, 葉型(xíng)薄, 受(shòu)力後變形大, 所以機械加工非常困難, 又因為齒數多、齒密, 所以加工(gōng)量非常大。因此葉型加(jiā)工是整體葉盤製造的(de)主要工(gōng)序。
2 整體葉(yè)盤結構的應用
隨著航空製造技術(shù)的不斷發展, 近年來整體葉盤結構(gòu)在新研製航(háng)空發動機中已得到(dào)廣(guǎng)泛應用(yòng)( 表 1)。
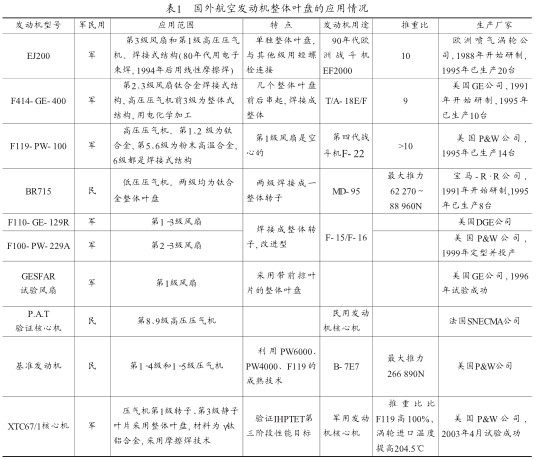
2.1 美國整體葉盤(pán)的應用
美國(guó)GE公司最早(zǎo)在(zài)20世紀70年代就在T700發(fā)動機的壓氣機上大量采用整體葉盤(pán)結構, 爾後又陸續將這一技術應用到CT7、CFE738、GE23A、YF120、F414和F110發動(dòng)機上。YF120的2級風扇和5級高壓壓氣機全部采用整體(tǐ)葉盤(pán)結構的轉子(zǐ), 風扇葉片采(cǎi)用低展弦比葉片, 其中第(dì)1級(jí)為空心葉片。F414的第2、3級風扇采用低(dī)展弦比葉(yè)片的(de)串列轉子采(cǎi)用惰性氣體焊接的鈦合(hé)金(Ti17) 整體葉盤結構,且兩個整(zhěng)體葉盤還(hái)焊接在一起形成整體轉(zhuǎn)子, 使風扇(shàn)轉子重量比F404減輕了20.41kg; 高壓壓氣(qì)機(jī)前3級也采用了(le)整體葉盤, 第1、2級用Ti17合金製成, 且(qiě)焊成一體, 第3級采用Inconel 718鎳(niè)基合金製成, 使壓(yā)氣機的重(chóng)量減輕3.63kg。F404整台發動機5級(jí)整體葉盤轉子比常規葉盤連接的零件減少了484個, 與原型機F404相比, 其推重比由7.5提高(gāo)到9.1。由幾(jǐ)個整體葉盤前後串起焊(hàn)成一體(tǐ)的設計, 是F414優於(yú)EJ200發動(dòng)機的顯著特(tè)點, 它能進一步降低轉子的重量, 提高發動機耐久性。F110- GE- 129改型為F110- GE- 129R時, 即將3級風扇全改成寬弦葉片、整體葉盤結構, 零件數減(jiǎn)少(shǎo)了2/3。由於風扇效率與空氣流量提高(gāo), 使發動機推力增加5.9%。如(rú)維持原推力, 則熱端部件壽命由4000TAC循環(huán)( 戰術(shù)空間循環) 提(tí)高(gāo)到(dào)6000TAC循(xún)環。
90年(nián)代GE公司(sī)還研究了一種前掠葉片的整體葉盤結構風扇, 並在前掠氣動研究試驗台(GESFAR) 上成功(gōng)地進行了試驗。這種新型風扇部件具有(yǒu)高速、小展弦比(bǐ)、前掠葉片的特點, 整體葉(yè)盤由高強度鈦合金製成, 葉尖(jiān)直徑約為508~ 635mm, 空(kōng)氣流量約為100kg/s。試驗結果表明該風扇不僅減輕了重量, 而(ér)且(qiě)比常規風扇的效率高4%, 其中尖部效率提高8%, 失速裕度提高3%~ 5%, 因而使發動機抗流場畸變能力提高80%。目前GE公司已將其安裝到(dào)IHPTET驗證機上進行了評估, 並(bìng)將用於改進現役(yì)發動機, 如(rú)F414等。
80年代初, 美國P&W公司開始在PW5000發動(dòng)機上使用和驗(yàn)證風扇壓氣機整體葉盤結構, 目前已應用到F119和F100發動機上。P&W公司為先進戰術戰鬥機ATF/F22研製的推重比為10的F119- PW- 100發動機, 3級風扇、6級高壓壓氣機的轉(zhuǎn)子, 全部采(cǎi)用了整體(tǐ)葉盤,是唯一一種在風扇與壓氣機中全部采用整體葉盤結構的發動機, 6級軸流高壓(yā)壓氣機(jī)整體葉盤的第1、2級為(wéi)鈦合金, 葉片和輪盤用線性摩擦焊將(jiāng)其焊成一體; 第3~6級為粉末高溫合金(jīn), 葉片與輪盤的(de)焊接采用了鍛接擴散連接技(jì)術。有的F119壓氣機轉子還采用ALLOY- C型阻燃(rán)鈦合金整體葉盤。ALLOY- C型鈦合金不但具有良好的阻燃性能, 而且具有(yǒu)良好的高溫變形、冷軋、延展、焊接和鑄造性能, 其鈑金成形延展率可達40%~ 50%。
在F100- PW- 229發動機改型(F100- PW- 229A) 中的第2~ 3級全部采用整體葉盤結構。 改型後的發動機在保持推力不變的(de)情況下, 渦輪進口溫度降低49℃, 發動機的可靠性和壽命得到提高。在PW7000發動機方(fāng)案中, 5級高壓壓氣機全部采用大後掠(luě)、高效率(lǜ)葉片的整體葉盤結構轉子。90年代初(chū), P&W公司還研究了帶(dài)後掠葉片的整體葉(yè)盤結構的兩級風扇, 其(qí)尺寸(cùn)和流量與F119的(de)風扇的基本相同(tóng), 目前該葉片為後掠實心葉片,但將來可能采用(yòng)空心的(de)金屬葉片或複合材料葉片。該風扇效率比當時的IHPTET基準風扇(shàn)的效率高50%左右(yòu), 每級(jí)風扇的壓比比IHPTET基準風扇的高30%, 不久將裝到IHPTET驗證機發動機上進行試驗驗(yàn)證。
美國聯合攻擊機JSF的升力風(fēng)扇也采用了(le)整(zhěng)體葉盤(pán)結構, 這是迄今為止最大的整體葉盤(pán), 外徑1.27m, 毛坯重1 500kg,成品重100kg。艾利遜(xùn)公司1998年(nián)在XTC16/1A核心機上試驗了渦輪整體葉盤, 這是用鍛接工藝將單晶Lamilloy葉片粘接在粉末冶金盤(pán)上的,Lamilloy轉子葉(yè)片比常規氣膜冷卻葉片少(shǎo)用30%的冷卻空氣, 壽命增(zēng)加100%, 整體葉(yè)盤結構減少重量25%~30%。據《航空周刊》最(zuì)新(xīn)報道, 美國(guó)P&W公司在(zài)IHPTET計劃下成(chéng)功完成了XTC67/1先進發動機(jī)核心機的試驗。XTC67/1核心機壓氣機的第1級轉子、第3級靜子葉片(piàn)采用了比強(qiáng)度高的γ 鈦鋁合金整葉片盤, 目的(de)用於驗證IHPTET計(jì)劃第三(sān)階段的性能目標(biāo), 推重比要比F119發動機提高100%, 渦輪進口溫度提高204.5℃, 4級(jí)壓氣機(jī)的壓比比F119的6級壓氣機壓比還(hái)要高。該核心機(jī)在美國空軍阿諾德工程發展中心的J1試驗台上進行了6批次試驗, 截至2003年(nián)4月累(lèi)計時(shí)數28h。另外, 為滿足波音公司的B- 7E7飛機推(tuī)進係統和(hé)成本目標, 美國P&W公司(sī)的(de)基準發動機也將采用已驗證技(jì)術和先進製造技術。其中B- 7E7發動機(jī)前4級或前5級壓氣機將采用整體葉(yè)盤。P&W公(gōng)司還將在美國空軍阿諾(nuò)德工程(chéng)發展(zhǎn)中心(AEDC) 進行7E7發動機的高空模擬(nǐ)試驗, 累計試驗(yàn)時數將達到15 000個(gè)工作循環。這項計劃已於2004年正式啟動。
2.2其他國(guó)家整體葉盤(pán)的應(yīng)用
英國、德國、意大利和西班牙合作研製的(de)EJ200發動機, 其(qí)3級風扇壓(yā)比為(wéi)4.2, 最(zuì)初(chū)隻在遠離進口處的第(dì)3級風扇上采用了電子束焊接的整體葉盤結構, 後(hòu)來在第2級也采(cǎi)用了整體葉盤結構, 目前第1級上也已采用整體葉盤結構, 並有可調進(jìn)口導流(liú)葉片以保證有足夠的壓氣機喘振裕度。其材料為鈦合金, 用線性摩擦焊取代電子束焊製造整體葉盤。
在寶馬(mǎ)- R · R公司研製的BR715發動機上, 由於第1級風扇葉片采用了RB211- 535E發動機的寬弦無凸台夾(jiá)芯葉片, 塵砂進入極少。風扇後的兩級低壓( 增壓) 壓(yā)氣(qì)機都采用寬弦空心葉片(piàn)的整體葉(yè)盤, 並將兩級(jí)焊成一體, 形成不可分散(sàn)的連(lián)接(jiē)結構, 這是整體(tǐ)葉盤在民用高涵道比發動機上首次應用。加工和修理整體葉盤結構除采用電子束焊外, R· R公司與MTU公司還共同開發了線性摩擦焊工藝。
法國國營航空發動機製(zhì)造公司SNECMA在20世紀90年代初開展了一項為發展新型民用發動機核心機的技術驗證計劃, 即P.A.T計劃( 技術活動計劃, Plan Act~ion Technologies)。在(zài)該計(jì)劃中(zhōng), 11級壓氣機中第8、9兩級采用了整體葉盤結構(gòu), 這實際上也是為整體葉盤結構在大型民用發動機中推廣進行的技術儲備與探索。
我國正(zhèng)在研製帶箍的整體葉盤(pán)結構, 目的是為了克(kè)服前掠葉片(piàn)的顫振。這種葉片帶箍設計, 即葉片尖部加一個環(huán)帶, 這樣葉片振動受到了約束, 顫振可以消除; 但葉片箍的受力非常大, 一般金屬材料是無法承受的。利(lì)的。利用碳纖維可以(yǐ)承受極大的拉力這一特性,在(zài)金屬箍外麵加(jiā)繞碳纖維的複(fù)合材料(liào), 葉片、盤及箍產(chǎn)生的離心力由(yóu)碳纖維複合材料承(chéng)擔。由於碳纖維複合材料密度隻有 1.6~ 1.7g/cm3, 而鈦合金材料為 4.6g/cm3左右, 所以箍的重量不大(dà)。常(cháng)規設計中, 葉片受的是拉伸應力, 現在帶箍葉片上半部受的是壓縮應力, 葉片受的應力下降, 所以葉(yè)片厚度可以下降很多, 盤的重(chóng)量也可以(yǐ)大大下降, 重量大約是常規葉盤結構的50%。預計在不久的將來, 這項(xiàng)技術會普遍應用在航空發動機(jī)的(de)風扇(shàn)和高壓壓氣機(jī)設計中。
2.3 整體葉盤結構的發展趨勢
整體葉盤結構不僅應用(yòng)在研製和改進中的發動機上, 而且還(hái)將用在(zài)未來推(tuī)重比為15~ 20的高性(xìng)能發動機上 ,如歐洲未(wèi)來推重比15~ 20的發動機和美國的HPTET計劃中推重比為20的發動機, 在(zài)這(zhè)些發動機上將采用效果更好的SiC陶瓷基複合(hé)材料或抗氧化的C/C複合材(cái)料製造整體渦輪葉盤(pán)。美國研製的C/C複(fù)合材料整體渦輪葉盤已在(zài)1 760℃環境中進行了地麵超轉試驗(yàn)。采用整體葉盤結構, 其轉子葉片(piàn)必然要設計(jì)成抗外物損傷的葉片, 以減少維修次數費(fèi)用。目前風扇和壓氣機整體葉盤結構的轉子葉片普遍采用(yòng)小展弦比的(de)鈦合金葉片(piàn), 有空(kōng)心、實心、掠式和非掠式的; 而下一代推重比為15~ 20的發動機必將(jiāng)采用氣動性能先進的掠式、重量更輕的空心抗(kàng)外物損傷(shāng)能力強的小展弦比(bǐ)葉片, 如果可能, 也(yě)將用強度和(hé)剛性更好及密度(dù)更(gèng)小的金屬(shǔ)基複合材料代替高溫鈦(tài)合金, 這樣可提高氣動性能和效率, 既滿足強度和可靠性要求, 又大大(dà)減(jiǎn)輕重量, 使發動(dòng)機(jī)推重(chóng)比大(dà)大提高。
如果將整體(tǐ)葉盤中的輪盤部(bù)分去掉, 就成為(wéi)整體葉環, 這(zhè)時該件的重(chóng)量將進(jìn)一步降低。整體葉環直接固(gù)定在(zài)承(chéng)力環上。由於缺少了承受負荷的輪盤, 整體(tǐ)葉環承受不了葉片的離心負荷, 為此(cǐ), 整體葉環隻能(néng)用密度較小的複合材料來製造(zào)。這種整(zhěng)體葉環的重(chóng)量約為常規結構重(chóng)量(liàng)的30%, 目前, 正在研製的整體葉環是用(yòng)連(lián)續單根碳化矽長纖維增強的Ti基複(fù)合材料 (TiMMC)製(zhì)造的。TiMMC具有比強度、比剛度高, 使用(yòng)溫度高及疲勞和蠕變性能好的(de)優(yōu)點。例如德國研製的SCS- 6SiC/IMI834複合材料的抗拉強度(dù)高(gāo)達2 200MPa, 剛度(dù)達220GPa, 而且具有極為優異的熱穩定性, 在700℃溫度暴露2 000h後(hòu), 力學性能不降低。TiMMC葉環代替壓(yā)氣機盤, 可使壓(yā)氣機(jī)的結構重量減輕70%。
美國製造的TiMMC整體葉環已成功用在P&W的XTC- 65IHPTET驗證機的(de)第3~ 4級壓氣機上, 由於材料和結(jié)構的先(xiān)進性使轉子重量大(dà)大減輕, 如第(dì)3級整體葉環轉子重量隻有4.5kg左右, 而常規鎳基合金製造(zào)的同(tóng)樣轉子的實際重量(liàng)為25kg。由於TiMMC複(fù)合材料(liào)隻能承受477℃的溫度, 壓氣機不能在高溫環境下工作, 下一步將考慮用Al- Ti化合物(Ti3Al和TiAl) 作(zuò)基體(tǐ), 可耐溫927℃。英、法、德也(yě)研製了TiMMC葉環, 並(bìng)成功地進行了台架試驗, 用於改進EJ200的3級風扇、高壓(yā)壓氣機(jī)和渦輪, 以便為EJ200在21世(shì)紀推重比達(dá)15~ 20提(tí)供技術基礎。在我國與印度開展(zhǎn)的國際合作項目中, 有一帶環箍的單級風扇試驗研究, 該風扇的設計參數為: 增壓比3.0, 葉尖切向速度470m/s, 有17片葉片, 外徑0.4m, 采用了帶外箍環的整體葉環結構 ( 隻能用複合材料來製(zhì)作), 目前印度(dù)已成功製造(zào)出該試驗件, 在國(guó)際上處於(yú)領先地位。
3 整體葉盤的製造技術
發動機整體葉盤的製造工藝和維修的複雜性是目前影響其應用和推(tuī)廣的兩大因(yīn)素。整(zhěng)體葉盤的機械製造加工麵臨越來越強的挑(tiāo)戰。由於整體葉盤結構複雜,加工精度要求高, 尤其是葉片工作表麵為空間自由曲麵, 形(xíng)狀極其複雜; 特別是為適應其高溫、高壓、高轉速的(de)工作條(tiáo)件, 廣(guǎng)泛(fàn)采用鈦(tài)合金、粉(fěn)末高溫合金等高性能金屬材料和鈦基複合材(cái)料、鈦鋁化合物基複合材料等先進複合材料, 因此影響了材料的可加(jiā)工性, 傳統的機械加工方法已難以勝任, 必須應用現代特(tè)種製造加工技(jì)術, 探索研究出更加(jiā)高效、可靠的加工工藝方法。整(zhěng)體葉盤從(cóng)結構設計上分為整體式和焊接式兩類(lèi)。整體式整體葉盤製造(zào)依賴於精(jīng)密製坯技術、特種加工技術和數(shù)控機床的發展; 焊接式(shì)把複雜、困難的(de)葉型加工改變成單個葉片的葉型加工, 但增加焊接工序, 焊接的精度和焊縫質量與整(zhěng)體葉盤的性能(néng)和工作可靠性密切相關。因此, 焊接工序隻能采用(yòng)先進(jìn)、精密的焊接工藝, 如電子束焊、線性摩擦焊、真空固(gù)態擴散連接等。
目前, 製造整(zhěng)體葉盤有以下5種技術途徑。
3.1 精(jīng)密製坯技術
現代精密(mì)製坯技術( 精密鑄造和鍛造(zào)) 的發展日臻完善。精密鑄造和(hé)精密鍛造采(cǎi)用CATIA軟件、預測模型和計算機模擬技術實現了“實體(tǐ)造型” 以及鑄、鍛過程用計算機模擬仿真, 這些技術提高了金(jīn)屬(shǔ)填充和凝固質量, 消除了(le)疏鬆, 避免了熱裂, 可取代常規的試鑄法,從而提高了精(jīng)密鑄造和精密鍛造的質(zhì)量與效率, 降低了成本。
(1) 精密鍛造技術的發展使鍛壓工藝徹底突破了毛坯生產的範疇, 可以加工出接近成品的(de)零(líng)件。現在,整(zhěng)體葉盤大多采用精密鍛(duàn)造作為製坯手(shǒu)段, 能節省貴重金屬材料, 減少(shǎo)難(nán)加工(gōng)材料的機械加工量(liàng), 提高整體葉盤的疲勞強度和(hé)使用壽(shòu)命。美國GE公司已用等溫鍛造技術製造(zào)出了(le)帶葉(yè)片的(de)壓氣機(jī)整體葉盤轉子, 材料利用率提高4倍。精密鍛造(zào)零件的尺寸精度可以達到 (0.1~ 0.25)mm, 表麵粗(cū)糙度可以達到Ra0.4~ 1.6μ m。整體葉盤精密鍛造的精度和質量主要依靠計(jì)算機對(duì)鍛造過程進行控製。GE公司已用(yòng)熱等靜壓(yā)法將鈦合金粉末高溫合(hé)金盤與精鍛葉片複合成形為鈦合(hé)金整體葉盤;在精密鍛造時還(hái)采用(yòng)了超塑等(děng)溫模擬技術(shù), 獲得了優異的組織和力學性(xìng)能。
(2) 精密鑄造技術。由於精(jīng)密鑄造工藝的新發展,特別是金屬材料定向凝固和熱等(děng)靜壓理論的深入研(yán)究, 使得鑄造合金組織和性能大(dà)大改善, 解決了葉片疲勞斷裂(liè)的裂紋沿垂直(zhí)於葉片主應力方向的晶粒邊界發生; 熔模鑄造內部存在縮鬆缺陷(xiàn)等問題, 使葉片的抗疲勞性、應(yīng)力斷(duàn)裂壽命大為提高, 並且可以減少焊後裂(liè)紋, 降低鑄件的性能變化和分散程度。目前, 較為成熟的精密鑄造技術(shù)有實型鑄造(zào)和熔(róng)模鑄造。
我國航(háng)空(kōng)材料(liào)研究院整體葉盤的精密鑄造技術已取(qǔ)得重要成果。采用 K4184 鎳基高(gāo)溫合(hé)金, 成功鑄造(zào)出了直徑為 120mm, 帶有 34 個(gè)葉片的動力渦輪整體葉盤。采用的方法(fǎ)是將輪盤鑄(zhù)造成細晶, 將整體葉片鑄(zhù)造成定向柱晶(jīng)或(huò)單晶, 不同(tóng)晶粒形態各有優(yōu)勢, 細晶具有較(jiào)好的低周疲勞和(hé)拉伸性能, 適(shì)合於中低溫下使用;而方(fāng)向性柱晶則具有較(jiào)好的冷熱疲勞(láo)、低周疲勞和抗振動疲勞性能, 適合於高溫下工作。
為了進一步提高采用精密鑄造製(zhì)造的整體葉盤坯件的密度, 改善力學性能, 應將坯件進行等靜壓處理和真空熱處理
3.2 鍛接法
美國 P&W 公司在製造粉末高溫合金(jīn)整體葉(yè)盤時, 應用了鍛接擴散連接技術( 即擴散連接技術), 它用局部加熱(rè)法(fǎ)將(jiāng)單晶精鑄葉片直接連接到鍛造渦輪盤的輪緣上。 渦輪盤輪(lún)緣局部加熱至變形(xíng)溫(wēn)度後(hòu), 用待連(lián)接的單晶葉片在局部加熱的輪緣連接部位施壓, 使局部加熱區域產生變形, 即在將葉片植入輪緣內的(de)同時(shí)進行擴散連接, 將葉片牢固地連接在渦輪盤的輪緣(yuán)內。鍛(duàn)接(jiē)法的關鍵是正確有效地控製局部加熱(rè)和變形參數( 溫(wēn)度、壓力、變形量), 這對葉(yè)片與(yǔ)輪盤之間消除鬆動,產生完全致密的高強度結合麵(miàn)是很重(chóng)要(yào)的。用此(cǐ)法製造的整體葉盤(pán)結構必須確保鍛接過程中葉片始(shǐ)終準確定位, 並始終保持定位的位置。P&W 公司已研究出葉片/盤的鍛接專利工具, 可準確地保持葉片的正(zhèng)確位置。
鍛接工藝可有效用(yòng)於超級耐熱合(hé)金和鈦合金(jīn)之間的連接和修補, 可用於風扇、壓氣機(jī)和渦輪(lún)整體葉盤結構的製(zhì)造、修補和更換葉片。
3.3 電子束焊接法
在各(gè)種先進精密的焊接工藝中, 電子束焊發展(zhǎn)較早, 也(yě)較成熟, 並最先用於整體葉盤的製(zhì)造過(guò)程中。整體葉盤因其主要用於風扇的第 2、3 級和高(gāo)壓壓氣機(jī)的第 1、2 級(jí), 故材料多為鈦合金。由於鈦合金電子束焊具(jù)有大穿透、小變形、無氧化、高強(qiáng)度、焊接尺寸精度高、質量(liàng)穩定、效率高(gāo)等優點, 因而在(zài)我國高性能(néng)航空發動機製造中很多鈦(tài)合金零件都采(cǎi)用電子(zǐ)束焊接工藝。
EJ200 也(yě)采用此(cǐ)法製造, 即先(xiān)將單個葉片用電子束焊接成葉片環, 後用電(diàn)子束焊接技術將鍛造和電解加工成形的(de)輪盤腹(fù)板與葉片(piàn)環焊接成整體葉盤結構。這種整體葉(yè)盤結構比傳統的榫頭連接的葉盤轉子結構重量減(jiǎn)輕 30%。
3.4 線性摩擦焊(hàn)(LFW)
線性摩擦焊是一種固態連接技術, 是旋轉(zhuǎn)摩擦焊(hàn)的重要發展, 類似(sì)於擴散連接(jiē)。擴散連(lián)接從結構上講(jiǎng),連接處看不(bú)出“焊縫” 來, 且(qiě)其強度與彈(dàn)性均(jun1)優於本體材料。 線性摩擦(cā)焊與擴散連接不同之處(chù)在於: 在擴散連接中, 連(lián)接的工件是在爐中(zhōng)加溫使其達到高溫的; 而(ér)線性摩擦焊中, 工件的高溫是通過兩配合麵間的相互高頻振蕩(dàng)產生的(de)。 用線性摩(mó)擦焊將葉片焊接在輪盤上,可節省大(dà)量(liàng)葉片的連接件和結構重量。它先將葉(yè)片夾緊在輪緣的葉(yè)根上, 並使輪盤周向以高速振動, 在葉片和(hé)輪盤葉根(gēn)界麵產生(shēng)一個窄的摩擦加熱區, 當加(jiā)熱區的溫度達到要求的溫度時即停止振動, 葉(yè)片與輪盤固定直至固結在一起。最後再在五坐標數控銑床上用銑(xǐ)刀將多餘材料銑掉。F119 的(de) 2、3 級風扇和 6 級高壓壓氣機以及EJ200 發動機的 3 級低壓壓氣機的整體葉盤是線性摩(mó)擦(cā)焊接(jiē)技術成功應用的頂級標誌。其中, 用LFW 技術加工的 EJ200 發動機的整體葉盤, 所用(yòng)設備是英國 Blacks 公司(sī)製造(zào)的線(xiàn)性摩擦焊機。該焊機由(yóu) 1個主驅動電機( 功率 89kW)、振動器及夾具(jù)組成, 振動器可產生線(xiàn)性振動, 振幅 0~ 3mm。夾具帶有分度機構,可對工件進(jìn)行分度、定(dìng)位和(hé)固(gù)定, 並(bìng)傳遞夾緊力、頂鐓力和摩擦力。振動器可以在焊(hàn)接工序完成時的幾分之一秒內使(shǐ)振幅為零, 保證被焊葉(yè)片的定(dìng)位精度。瑞士的一家公司可以提供與之配套的高速磨床和理想的軟件包。目前 R · R 公司和 MTU 公司已用 LFW 技術成功地製造了(le)寬弦風扇整體葉盤, 並將為 JSF 的發動機提供LFW 整體葉盤。用 LFW 技術加工(gōng)整體葉盤與用整體鍛坯在五(wǔ)坐(zuò)標數控銑床上加工或電化學加工相比, 可以節約大量貴金(jīn)屬; 用 LFW 技術可從發動機上更換掉被撞擊(jī)損壞的葉片。也可用 LFW 技術(shù)將葉片與用不同材料製造的輪盤焊接在一起, 以獲得最佳的減重效果(guǒ)。
擴散連接(jiē)和線性摩擦焊是在接合表麵產生塑性變(biàn)形(xíng)和加熱條件下, 達到表麵原子間結合, 並互相擴(kuò)散形成焊接(jiē)頭, 加熱溫度一般為被焊材(cái)料熔點溫度(dù)的 70%,因此焊接接頭的質量比熔焊( 電子束焊) 的質量高, 可以使葉片和盤的過渡區的晶(jīng)粒組織變得很細, 其靜態、動(dòng)態力學性能超過非焊接的基體(tǐ)材料。
采用線性(xìng)摩擦焊加工整體葉盤有下列好處:
(1) 可以節約大量貴(guì)重的鈦合金(jīn)。例如 R · R 公司為 JSF( 聯合攻擊機) 用的升(shēng)力風(fēng)扇發動機生(shēng)產整體葉盤的風扇轉子( 該轉子是目前世界上最大(dà)的整體葉盤,其外(wài)徑為 1.27m) 時, 采用整體(tǐ)鍛坯用五坐標數控(kòng)銑床加工, 坯料重 840kg, 加工後成品件重 97.6kg, 即材料損耗高達 88%; 而采用線性摩擦焊時, 焊接後銑去(qù)的材料不(bú)多, 並且還可減(jiǎn)少加工時間。
(2) 可以對損壞的(de)單個葉片(piàn)進行(háng)修理。在采用(特別是在風扇第 1 級采用)整體葉盤(pán)時, 能否對整體葉盤進(jìn)行修理(lǐ)是要考慮的一個重(chóng)要問題, 因為發動機在使用中, 不(bú)可避免地會遇到外來物(特別是鳥(niǎo)類)撞傷葉片的情況, 在常規的設計中, 可以輕(qīng)易地更換(huàn)損傷的葉片; 而整體(tǐ)葉盤就不(bú)能更換葉片, 如沒有(yǒu)方便而適(shì)用的修理損(sǔn)壞葉(yè)片的方法, 整體葉盤的應用(yòng)就受到限製。有了線性摩(mó)擦焊的加工方法, 可(kě)以(yǐ)將損壞的葉片切去後再焊上新葉片, 由(yóu)於有此優越性, EJ200、F119 發動機風扇第 1 級轉子也采了整體葉盤 (EJ200 最(zuì)初的設計中, 僅風扇第 3 級、高(gāo)壓壓氣機第 1 級采用整體葉盤)。
(3) 可以將 2 種不(bú)同材(cái)料焊在(zài)一起, 這樣可根據葉片、輪(lún)盤的工作條件選用不(bú)同材料, 從而充分(fèn)挖掘轉子(zǐ)結構材料的性能潛力, 使(shǐ)轉子結構的重量進(jìn)一步降低。
3.5 數控電解加工技術
整體葉盤由於構型複雜, 特別(bié)是由難切削(xuē)材料製成(chéng)的、帶薄型葉片(piàn)、結(jié)構複雜的整體葉盤用數控銑削、精密鑄造方法加工時就更(gèng)困難, 甚至(zhì)不能加工( 如帶冠(guàn)整體葉輪)。此時(shí)特種加工方法便顯示出(chū)它突出的優越(yuè)性, 其中, 電解加工與數控技術相結合的數控電解加工技術, 作為一種補(bǔ)充技(jì)術, 可以解決數控(kòng)銑(xǐ)削精密鑄造(zào)不能加工的(de)難題, 為整體葉盤製造提(tí)供(gòng)了一種優質、高效、低成本、且具有快速響應能力的新加工技(jì)術。整體葉盤(pán)的數控電解加工技術能綜合發揮計算機數控和電解加工的技術優勢, 同(tóng)時又能取長補短。這種工藝具有(yǒu)電解加工的優點, 即工具陰極無損耗, 無宏(hóng)觀切削力(lì), 適宜加工各種難切削材料和長、薄葉片及狹窄通道的整體(tǐ)葉盤, 加工效率高, 表麵質(zhì)量好, 這些優點是數控銑削所不具(jù)備的; 它又具有數控的優點, 能以計算機數控方(fāng)式實現(xiàn)型麵三維運動, 可用於加工各類(lèi)複(fù)雜結(jié)構、多品種、小批量零件, 甚至單件試製的生產中,這些優點又是一般拷貝式電解加(jiā)工所不具備的。 因此,這種工藝技(jì)術非常適合於加工用數控銑削、精(jīng)密鑄造難加工或不能加工的(de)零件, 如小直徑、多葉片、小葉間通道(dào)(1.5~ 3mm寬度) 零件, 難切削材(cái)料變截麵扭曲葉片整體葉輪, 以及數控銑無法加工的帶冠整體葉(yè)輪(lún)等。研究及應用情況表明, 整體葉盤電解加工與五坐標(biāo)數控(kòng)銑削方(fāng)法相比有很(hěn)多優點:
·工(gōng)時可(kě)減少50%以上 ( 加工帶長葉片的整體葉(yè)盤工時(shí)減少更多);
·可以加(jiā)工任何高強、高硬度的(de)難切削(xuē)金屬材料;
·不會產生殘餘應力和變形, 這對薄型(xíng)葉片的整體葉盤加工尤為重要。
美、英、俄和中國都高度重視整體葉盤數控電解加工技術的研究並已得到應用, 在新型航空發(fā)動機及航天火箭發動機的研(yán)製中發揮了重要作用。
(1) 美國GE公司的五軸數控電解加工。
美國GE公司(sī)在電解加工先進航空發動機(jī)的整體葉盤時, 采用了(le)以成形或近成形陰極進行(háng)多坐(zuò)標數控送(sòng)進運動(dòng)的加工方式(shì)。在製造為裝(zhuāng)備 “先進戰鬥機ATF(即F22)” 而研製的GE37/YE120發動機的鈦製整體葉盤及F414發動機整體葉盤時, 與(yǔ)美國Lehr.precision公司合作(zuò)發展了五軸數控電(diàn)解加工技術。與原用五坐標數控銑削葉片相比, 加工時間(jiān)減少約(yuē)85%, 同時還避免了在葉片(piàn)加(jiā)工中產(chǎn)生的殘餘應力。電解加工仍分粗加工和精加工兩道工序, 加工出的葉片(piàn)葉型(xíng)厚度公差+0.1mm, 型麵公差+0.1mm, 可不需(xū)手工(gōng)拋光。
(2) 美、俄仿形電加工帶(dài)冠(guàn)整體葉輪。
在帶冠整體(tǐ)葉輪的加工(gōng)中, 美國采用精密數(shù)控電火花工藝, 俄羅(luó)斯則采用機械仿形電火花與電解加工的組(zǔ)合工藝。電解加工既可(kě)以提高加工速(sù)度, 又可以去除電(diàn)火花加工後的(de)表麵變質層, 提高(gāo)表麵質量。電火花—電解加工(gōng)的組合工藝在新型發動機, 特別是(shì)火箭發動機帶冠整體渦輪的研製中發(fā)揮(huī)了重要作用(yòng)。
(3) 國內數控電解加工整體葉盤的研究。
在國內, 南京航空航天大學(xué)從 20 世紀 80 年代中期就開始進行數(shù)控(kòng)展成(chéng)電解加工的(de)研究, 其中重要研究成果有: “直線刃” 陰極數控展成電解加工, 成形或近成形陰極柔性電解加工。
“直(zhí)線刃”陰極數(shù)控展成電解(jiě)加(jiā)工與數控銑相似,以簡單的 “直線刃(rèn)” 陰極進行數控展成(chéng)運動, 基於(yú)電(diàn)化學陽極溶解原理而實現整體(tǐ)葉盤葉(yè)間(jiān)槽和葉(yè)片型麵(miàn)的粗、精加工。數(shù)控展成電解(jiě)加工通常需(xū)要 5 軸聯動, 即直線位移 x、y、z 軸(zhóu)以及陰極擺動 CT軸和工件旋轉 CW軸。該研究成果已經應用於加工(gōng)改型航空發動機(jī)整體(tǐ)導風輪( 外徑190mm) 並裝機使用。
成形或(huò)近成形陰極柔性電解加(jiā)工是(shì)南京航空航天大學正在研究的加工非可展直紋麵的一種新方法, 采用成形或近成形陰極(jí)相對零件(jiàn)作數控仿形運動, 可實現帶冠整體渦輪、整體葉環和組合式整體葉(yè)輪的加(jiā)工。
4 整體葉盤結構的維修
航空發動機上風扇/壓氣機葉片(piàn)經(jīng)常被打壞(huài), 在以往的常規設計中, 遇到這(zhè)種(zhǒng)情況時(shí)更換受損的葉片就可以了, 但是葉盤結構(gòu)就不能因為一個葉盤上有幾個葉片打傷而報廢一個葉盤, 所以必須發展整體葉盤(pán)中個別(bié)損壞葉片的修理技術。GE 公司發展特(tè)殊(shū)的修理技術後才在 F414 中使用了5 個整體葉盤。在 IHPTET 計劃實施中, 利用激光曲線焊接(Laser Twist Weld) 方法對整體葉盤進行修複, 葉片修複後強度與原葉片差(chà)不多。這(zhè)樣, 葉盤結構(gòu)具有了生命力, 就能在航空發動機上得到更廣泛的應用。
5 結束語
(1) 航空(kōng)發動機部件結構正朝著輕量化(huà)、整體化方向發展。美國的先進戰(zhàn)鬥機(ATF) 計劃中把整體葉盤設計製造列(liè)為重要核心技術, 美國國防部的高性能渦輪發動機技術(IHPTET) 的(de)第三階段計劃要求, 到 2020年(nián), 戰鬥機上發動機的渦輪都將采用整體葉盤結構。由此可見, 整體(tǐ)葉(yè)盤( 環) 已(yǐ)經作為新型(xíng)航空發動機、火箭發動機的重大改進部(bù)件, 不僅應用(yòng)在研製中和改進的發動機(jī)上(shàng), 而(ér)且還將用在未(wèi)來 10~ 15 年後(hòu)推重比為25~ 30 的發動(dòng)機上, 用性能更加優異的 SiC 或 C/C 增強複合材料製造出整(zhěng)體葉盤或整體葉(yè)環。
(2) 隨著新的更難切削材料的采用及結構的更複雜化(扭曲葉片整體(tǐ)葉盤、帶冠整體渦輪), 航空發動機的加工(gōng)將更困難。美、英、俄(é)等工業發達國家都在加緊研(yán)究優質、高效、經濟(jì)的加工方法並正逐步取得成果。
(3) 整體式葉盤(pán)的製造將依賴於精密製坯(pī)技術、特種加工和數控機(jī)床的發展。其中數(shù)控電解加工能綜合發揮電解(jiě)加工和計算機數控技(jì)術的優勢(shì), 同(tóng)時又能互相取長補(bǔ)短, 彌補各自(zì)的不足之處, 是優質、高效、低成(chéng)本、快速響應地(dì)解決整體(tǐ)葉盤加工難(nán)題的一條重要途徑。這種(zhǒng)方法具有顯著的技術(shù)經濟效果(guǒ)。
焊接式整體葉盤的焊接工序隻能采(cǎi)用先進的精密的焊接工(gōng)藝( 電子束焊、真空擴散連接和(hé)線性(xìng)摩擦焊),特別是線性摩擦焊的加工成本低, 焊接質量高, 可用於各種材(cái)料的焊接或整體葉(yè)盤的(de)製造、修理和更換葉片,在整(zhěng)體葉盤(pán)的(de)製造(zào)中可以發揮獨特而重要的作用。
投稿箱:
如果您(nín)有機床行業、企業相關新聞稿件發表,或進行資訊合作,歡迎(yíng)聯係本網編輯部, 郵箱:skjcsc@vip.sina.com
如果您(nín)有機床行業、企業相關新聞稿件發表,或進行資訊合作,歡迎(yíng)聯係本網編輯部, 郵箱:skjcsc@vip.sina.com
更多相關(guān)信息
業界視點
| 更多
行業(yè)數(shù)據
- 2024年11月 金屬切削機床產量數據
- 2024年11月 分地(dì)區金(jīn)屬切(qiē)削機床產量數據
- 2024年11月 軸(zhóu)承出口情況(kuàng)
- 2024年(nián)11月 基本型乘用(yòng)車(轎車)產量數據
- 2024年11月 新(xīn)能源汽車產量數據
- 2024年11月 新能源汽車(chē)銷量情況
- 2024年10月(yuè) 新能源汽車產量數據
- 2024年10月 軸承(chéng)出口情況
- 2024年10月 分地區金屬切削機床產量(liàng)數據
- 2024年10月 金屬切削機床產量數據
- 2024年9月 新能源汽車銷量情況
- 2024年8月 新能源(yuán)汽車產量數據
- 2028年8月(yuè) 基本(běn)型乘用車(轎車)產量數據