凸輪磨床X—C廓形誤差推導與仿真水
2016-9-5 來源:北京第二機床廠有限公司等 作者:張培碩 李偉華 韓秋實 李啟光 彭寶營
摘要:在數控聯動加工時。由數控(kòng)係統引入的跟蹤誤差是影響凸輪加工廓形誤差的主因之一。通過研究凸輪磨床跟蹤誤差,分別推導x軸、C軸跟蹤誤差(chà)與廓形誤差計算模型,進一步推導出x—C軸聯(lián)動時跟蹤誤差與廓形誤差的計算模型。借助(zhù)姒TLAB工具編寫程序。分別實現數學模型仿真和模擬加工仿真。將實驗采集的跟蹤誤差(chà)采用不(bú)同的方法引入到仿真中。通過仿真結果對比(bǐ)。驗證了x—c廓形誤差數學模型的正確性。
關鍵詞:數控凸輪軸磨床;跟蹤誤差;廓形誤差;仿真
在數控凸輪軸磨床加工過程中(zhōng),x軸和C軸要求隨加工形狀的不同瞬時啟停或改(gǎi)變速度,控製係統要實時精確地控製坐標軸運動的位置與速度,由於(yú)係統的穩態和動態特性影響了(le)各坐標軸的協調運動和位置精度,從而產生了凸輪的(de)廓形(xíng)誤差(chà)¨。3 J。數控凸輪軸磨床的(de)伺服係統是影響磨削質量最關鍵(jiàn)的部分之一。作為執行部件的(de)伺服驅動係統和電動機,能否準確執行給定的命令,對最終的(de)磨削質量的影響是顯而易見的。凸輪軸磨床多采用(yòng)砂輪架住複運動(dòng)和工件旋轉運動的聯動來實現凸輪的磨削加工,在數控聯(lián)動加工時,伺服係統(tǒng)引入的跟蹤誤差是產生(shēng)廓形誤差的一個重要因素‘4|。
國內學者近幾年涉足了數控係統的跟隨誤差研究領域,其中,浙江大學朱年軍等(děng)推導了數控加工中穩態(tài)誤差的形成過(guò)程,並從直線和圓弧輪(lún)廓誤差模型出發探討了數控跟蹤誤差和輪廓誤(wù)差(chà)之(zhī)間的關(guān)係"1;蘭州理工大學孫建仁等從分析(xī)輪廓誤差、跟(gēn)隨誤差和位置環增益著手,分析兩種基本插補運動的輪廓誤差及其(qí)相應的(de)跟隨誤差與輪廓誤差之間(jiān)的關係∞1;南京航空航天大學滕福林等針對不同類型(xíng)的位置給定,仿(fǎng)真分析了動態位置跟蹤誤差的產(chǎn)生機理,並(bìng)提出采用S曲線給定可以大大減小實際係統的動態位置跟蹤誤差的方法川。以(yǐ)上3種方法研究的對(duì)象都是(shì)通用的數控係統的簡單插(chā)補過程,未涉及到複雜聯動加工,如(rú)果將以上研究成(chéng)果直接應用(yòng)到加工凸輪的x—C聯動(dòng)是不(bú)科學的。此(cǐ)外,華中科技大學李勇(yǒng)等從係統傳(chuán)遞函數人手,完成(chéng)了(le)數控凸輪軸磨床控(kòng)製係統的建模,引入粒子群算法,優化了PID參數,此(cǐ)方法(fǎ)沒有涉及到跟蹤誤差數學模型的推導問題[8]。本文主要完成(chéng)工作是,在數(shù)控凸輪軸磨床的x—C軸聯動係統中,推導跟蹤誤差引起的廓形誤(wù)差(chà)數學模型,利用加工實驗(yàn)采集(jí)到的(de)跟蹤誤差值,借助MATLAB工具實現仿真,來驗證數學模型(xíng)。
1、X—C軸跟蹤誤差(chà)引起的廓形誤差數學(xué)模型推導
廓形誤差(chà)是(shì)指任(rèn)意位置處(chù)實際廓形軌跡與理論廓形軌跡之間的最短距離[9]。在磨削過程中,凸輪軸磨床通過兩軸聯動合成運動軌跡,完成凸輪廓形加工,由於各個軸都存(cún)在跟蹤誤差,運動分別會稍有(yǒu)偏差,因此,最終體現在磨削工件上的跟(gēn)蹤誤差是二者合成的結果。
1.1 X軸跟蹤誤差引起的廓形誤差數學模型推導
對於凸輪軸(zhóu)磨(mó)床而言,x軸跟(gēn)蹤誤差,是指砂輪在伺服係統要求到達指定位置時,實際位置偏離所要求的理(lǐ)論位置的誤差(chà)值。設x軸跟蹤誤差為血,如圖1所示,凸輪輪廓偏(piān)差量為(wéi)εs。
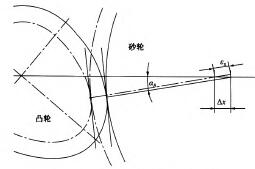
圖(tú)1 X軸跟蹤誤差與廓形誤差(chà)關係示薏圖
由幾何關係,可以(yǐ)得出:

用泰勒公式展開上式,並忽略高次微分量,有:

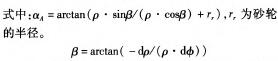
式(2)即為(wéi)x軸的跟蹤(zōng)誤差與廓形(xíng)誤差的數學(xué)模型。
1.2 C軸跟蹤誤差引起的廓形誤(wù)差數學(xué)模型推導
凸輪磨床C軸的跟蹤(zōng)誤差,是由於加工凸(tū)輪時實際(jì)磨削點在C軸上偏離了理論磨削點而引起的凸輪廓形的加(jiā)工(gōng)誤差。根據凸輪(lún)輪(lún)廓解析法¨0|,見圖(tú)2,%為基圓半徑,s為升程值,6為轉角值,e為偏心距,rr為滾子半(bàn)徑。有:
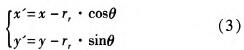
式(3)即為凸輪工作過程中廓形的直角坐標。
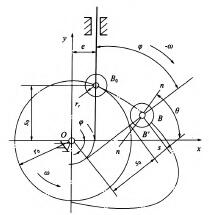
圖2俱置(zhì)直動滾子推杆盤形凸輪機構
式中:
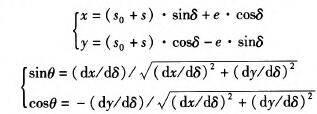
將滾子視為砂輪,該式就轉(zhuǎn)化為磨削模(mó)型,借助x坐標計算廓形誤差(chà),設極角誤差為△δ,容易得(dé)出:

將坐標轉換到n—n向,有:

即:

由於當C軸(zhóu)進給誤差為(wéi)△C,極角誤差為△δ時,可以(yǐ)認為△c=△δ,於(yú)是(shì):

式(6)即為(wéi)c軸跟蹤誤差與廓形誤差的數學模型。
1.3 X—C跟蹤誤差引起的廓形誤差(chà)數學模型
在凸輪實際磨削(xuē)時,c軸跟蹤誤(wù)差與x軸(zhóu)跟蹤誤差是同(tóng)時存在的,由於在式(2)與式(6)建立起的數學(xué)模型中,計算出的廓形(xíng)誤(wù)差都是法(fǎ)向值,因此,綜合考慮C軸跟(gēn)x軸,由它們造成的凸輪廓形誤(wù)差ε為(wéi):
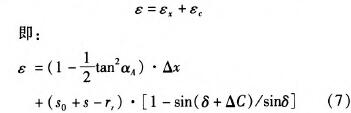
2、實驗驗證
2.1 實驗凸輪軸磨床數控係統簡介
數控凸輪軸磨床(chuáng)通常采用x—C兩坐標聯動實現凸輪輪(lún)廓的磨削,以PMAC卡(kǎ)為主(zhǔ)要(yào)運動控製核心(xīn),控製x軸(zhóu)砂輪架前後往複移(yí)動(dòng)和C軸工件主軸旋轉運動,z軸工作台的左右移動實現凸輪軸的自動磨削加工(gōng)循環和砂(shā)輪的自動修整,c軸由(yóu)電主軸驅動,x軸采用直線電動機驅動,z軸由交流伺服電動機驅動。磨(mó)削過程中,x軸執行(háng)磨削進給和退避到安全位置(zhì),z軸移動依次磨削凸輪軸上的各個凸輪。凸輪軸磨(mó)床數(shù)控工作原理圖如圖3所(suǒ)示。
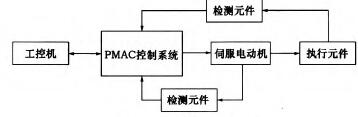
圈3效控(kòng)係統工作(zuò)原理圖
數控凸輪軸磨床數控控製原理圖如圖4所示,x軸直(zhí)線電動機帶動砂輪架水平往(wǎng)複移動,C軸伺服電主軸帶動工件主軸轉動,x—c兩軸聯動,實(shí)現凸輪廓形加(jiā)工,z軸伺服電動機帶(dài)動工作台移(yí)動,完成整根凸輪軸的加工。
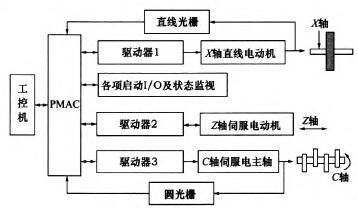
圖4數控(kòng)凸輪軸磨(mó)床致(zhì)控控翻原理圖
2.2跟(gēn)蹤誤差采集u¨
本文(wén)采用雙端口RAM數據讀取方式,利用雙端口所帶(dài)的函數進行數(shù)據(jù)采(cǎi)集(jí),這種方式更(gèng)加的方便,雙端口RAM函數封裝了PMAC數據讀取過程,用戶調用相應的函數即(jí)可從雙端口RAM中直接讀取運動參數,不需設置采集源及數(shù)據地址,雙端口RAM有很多運動參(cān)數采集函數,利用這些(xiē)函數就能采(cǎi)集電動機的(de)狀態、實(shí)時位置、速度、跟隨誤差等等。采集的實現(xiàn)是通過編寫采集軟件來完成(chéng),為提高采(cǎi)集時間精度,軟件采用(yòng)多媒體定時器(qì),設置多媒體定時器采集間隔20ms,定時器精(jīng)度1 ms,采集結(jié)果寫入數據文件。實驗共采集3組數(shù)據,按c軸轉速分別為30 r/min、60 r/rain、90 r/rain,從(cóng)低到高依次為數據1、數據2、數(shù)據3。
2.3仿真驗證
2.3.1仿真實現方法
(1)計算模型仿真
在伺服跟(gēn)蹤誤差與凸輪廓(kuò)形誤差數學模(mó)型建立的基礎上,借助MATLAB工具(jù),編寫(xiě)出仿真程序代(dài)碼,將凸輪升程擬合成凸輪廓形,伺服跟(gēn)蹤誤(wù)差值(zhí)由式7的數學模型引入,在法(fǎ)相將疊加到凸輪廓形上,可得到由單一曲線構成的凸輪實際廓形。該仿真方法部分MATLAB程序如下:
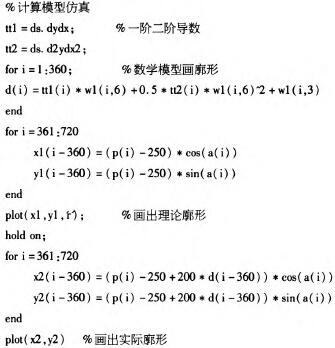
(2)模擬加工仿(fǎng)真
非圓曲麵零件采用x—C聯動磨削時,實質是一種砂輪包絡,為了便於觀察與計算(suàn),常采用砂輪反轉法(fǎ)即工件(jiàn)不動、砂輪反向旋轉對非圓曲麵零件加工過程進(jìn)行分析。借(jiè)助MATIAB工具,編寫出反轉法模擬凸輪廓形加工的仿(fǎng)真程序,跟蹤誤差分別由x軸跟蹤誤差缸和(hé)C軸跟蹤誤差AC分別引入,程序運行(háng)時,砂輪反方向旋轉(zhuǎn)一周,可得到由多重砂輪輪廓逼近出的凸輪實際廓形。該仿真方法部分(fèn)MATIAB程序如下:
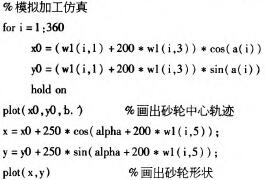

2.3.2仿真結果對比分析
將采集到的x軸、C軸跟蹤(zōng)誤差的3組數據分別導入MATLAB程序,仿真出凸輪理(lǐ)論廓形與實際廓(kuò)形(xíng),為了讓誤(wù)差效果(guǒ)明顯,誤差被放大了200倍,如圖5—7所示。圖5a、6a、7a三幅(fú)仿真圖,由單(dān)一曲線構成,為本文推導出的數學模型仿真(zhēn)結(jié)果(guǒ);圖5b、6b、7b三幅仿真圖,由多重曲線輪廓構成,為砂輪反轉法(fǎ)模擬凸輪(lún)加工的仿(fǎng)真結果。
將圖5—7中上下兩幅圖(tú),分別進行對比,可以得出廓形誤(wù)差曲線整(zhěng)體變化趨勢基本一致,桃尖整體(tǐ)位(wèi)置沿l,軸正方向偏移,隨著C軸速(sù)度的依次增加,偏(piān)移量依次增加(jiā)。
分析不同仿真方法的廓形對比圖,可發(fā)現較之於理論(lùn)廓形,凸輪實際廓形(xíng)曲線明顯向上(shàng)偏移,二者仿真結果基本一致,但是計算模型仿真出的實際廓形與反轉法模擬加工仿真(zhēn)相比,誤差有輕(qīng)微(wēi)波動,分析原因,在實際加工過程中,除去伺服跟蹤誤差以外還有其他誤(wù)差(chà)因素影響,有一定程度的波動是合理的(de)。這就證明了推算的(de)伺服跟蹤誤差與廓形(xíng)誤(wù)差的數學模型式 (7)是丁F確的.
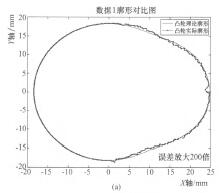
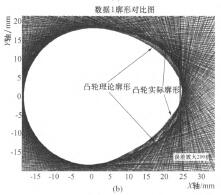
圖5數據1廓形對比圖
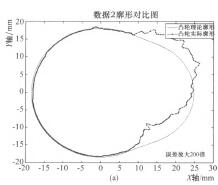
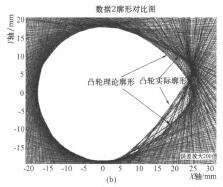
圖(tú)6數據2廓形(xíng)對比圖(tú)
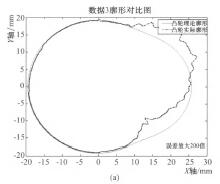
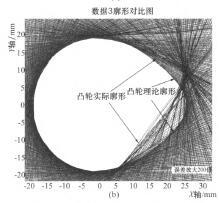
圖7數數據3廓形對比圖
3、結語
通過(guò)對凸輪軸磨床(chuáng)X軸、C軸(zhóu)跟蹤誤差引起的廓形誤差研究,提出了x—C聯動時伺服係統的跟蹤誤差與廓形誤差的數學模型。采集跟蹤誤差,借助(zhù)MATLAB工具編寫的(de)兩套仿真程序,對模擬加(jiā)工出的(de)凸輪廓形進行比對分析,最終驗(yàn)證(zhèng)了數學模型的正確(què)性。該模型的提出,為數控凸輪軸磨床伺服跟蹤誤差實時反饋係統的研究奠定了(le)基(jī)礎,對進一(yī)步提高凸輪磨削精度有重要意義。
投稿箱(xiāng):
如果您有機床行業、企業相關新聞(wén)稿(gǎo)件發表,或(huò)進行資訊合作,歡迎聯係本網編輯部, 郵箱:skjcsc@vip.sina.com
如果您有機床行業、企業相關新聞(wén)稿(gǎo)件發表,或(huò)進行資訊合作,歡迎聯係本網編輯部, 郵箱:skjcsc@vip.sina.com
更多(duō)相關信息
業界視點
| 更多
行業數(shù)據
| 更多
- 2024年11月 金屬切削機床產量數(shù)據
- 2024年11月 分地區金屬切削機床產量數據
- 2024年11月 軸承出口(kǒu)情況(kuàng)
- 2024年(nián)11月 基本型乘用車(轎車)產量數據
- 2024年11月 新能源汽車產量數據
- 2024年11月 新能(néng)源汽車銷量情況
- 2024年10月 新能源汽車(chē)產量數據
- 2024年10月 軸承(chéng)出口情況
- 2024年10月 分地(dì)區金屬切削機床產量數據
- 2024年10月 金屬切削機床產量數據
- 2024年9月(yuè) 新能源汽車銷量情況
- 2024年8月 新(xīn)能源汽車產量數據
- 2028年8月 基本型乘(chéng)用車(轎車)產量數據
博文選萃
| 更多