基於加工(gōng)中心的線(xiàn)鏜工藝研究與應用
2019-8-6 來源:一汽海馬汽車有限(xiàn)公司 作者:周夥英 馬小娟
摘 要:研究(jiū)了基於柔性生(shēng)產(chǎn)線加工中心的線(xiàn)鏜(táng)技術,分(fèn)析了曲軸孔從粗加(jiā)工到精加工所用(yòng)到的夾具、刀具,並根據實際(jì)加工情況,對發動機缸體曲軸孔的線鏜的(de)精加工不斷進行研究和(hé)持續改(gǎi)進,收效顯著,使加工質量和效率都得到了有效提升,從(cóng)而解決了中、小批量多品種(zhǒng)缸體加(jiā)工的投資大、成本高的問題。
關鍵詞:柔(róu)性製造技(jì)術(shù);線鏜;夾(jiá)具;刀具;缸體
0 引(yǐn) 言
曲軸(zhóu)孔的作用主要是支撐曲軸,傳遞從(cóng)曲軸柄傳來的轉矩並通過法(fǎ)蘭輸出,同時吸收活塞運動過程中產生的軸向和(hé)側向力。由於曲軸孔的加工質(zhì)量對發動機的(de)工作性能具有極其重大的影響,所以對發動機曲軸孔工藝的(de)要求一般比較嚴格,包括直徑、位置度、圓度、同軸度、各檔曲軸孔中心的直(zhí)線度及表麵粗糙度等。
為了滿足這些要求苛刻的(de)工藝指標,精加工一般采用專機線鏜或鉸珩兩種加(jiā)工方式。
為了降低投(tóu)資,實(shí)現(xiàn)三、四缸(gāng)發動機的共線生產,海馬某型號缸體曲軸孔精加工取(qǔ)消了鉸珩,采用加工中心線鏜加工工藝,實現機床內機械手自動(dòng)調(diào)刀,質量得到可(kě)靠的保證。該(gāi)曲軸孔整個加工工藝流程為:半圓(yuán)孔粗加工→瓦蓋合裝後的兩次半(bàn)精加工→精加(jiā)工,所有(yǒu)工序都在加工中心上完(wán)成(chéng)。
1 、曲軸孔粗加工
1.1 曲軸(zhóu)孔粗加工夾具
曲軸(zhóu)孔粗加(jiā)工夾具如圖1所示,本工(gōng)序選擇缸體瓦蓋結(jié)合麵(miàn)和(hé)缸孔來定位,以保證缸孔的加工餘量均勻及缸孔與結(jié)合麵的垂(chuí)直度。
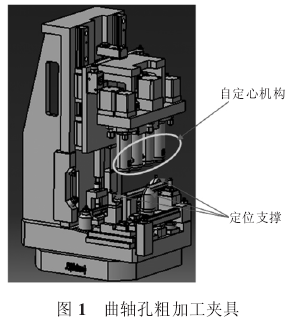
工件進入夾具後,導軌下降,缸體瓦蓋結合麵落在定(dìng)位支撐上,而後自定心結構下降到指定位置,通(tōng)過四個缸孔定位,自定心結構定位後中心在同一直線上。定位完成後,油缸開始動作並壓緊缸體。若缸體定位氣密檢測通過,機床便開始運行加工程(chéng)序;若氣密檢測(cè)報(bào)警,則需重定位夾(jiá)緊。
1.2曲軸孔粗加工刀具
曲軸孔粗鏜刀如圖2所示,刀片分為3組,每組3片,粗加工(gōng)後曲軸孔留下單邊0.85 mm的餘量。
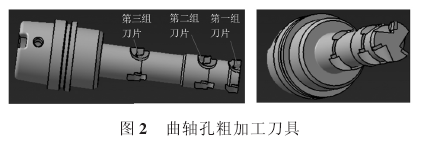
粗鏜刀最初使用R0.4刀片,刀具壽命太(tài)短,而且加工(gōng)後的曲軸孔粗(cū)糙度較高。經改進,換用R0.8刀片,試用後粗糙度有明顯改善,壽命也有很大提高。
1.3 曲軸孔粗加工
主(zhǔ)軸夾緊刀具→刀具(jù)進入(rù)曲軸孔→鏜刀與曲軸孔同(tóng)軸→粗鏜3、4、5檔(第一組刀片鏜第3檔、第二組鏜第4檔、第三組鏜(táng)第(dì)5檔)→刀具退出→夾具旋轉(zhuǎn)180°→刀具進入曲軸孔(kǒng)→鏜刀(dāo)與曲軸孔同軸→粗鏜1、2檔(第一組刀片鏜第2檔、第(dì)二組鏜第1檔)→刀具退出,加工過程如圖3所(suǒ)示。
2 、曲軸孔(kǒng)線鏜(táng)
2.1 采用加工中心設備線鏜的可行性(xìng)分析
在(zài)大批量生產中,用專機線鏜曲軸孔是常見的加工工藝(yì)。用CNC替代專機,其難點有兩個:
1)夾具設計較為複雜(zá),工序內要實現工(gōng)件的上升和再次夾緊動作;2)此工藝是否能滿足曲軸孔的表麵粗糙度及孔位、孔徑(jìng),孔的圓度、同軸(zhóu)度的過程能力CPK≥1.33或CP
≥1.33的質量要求。
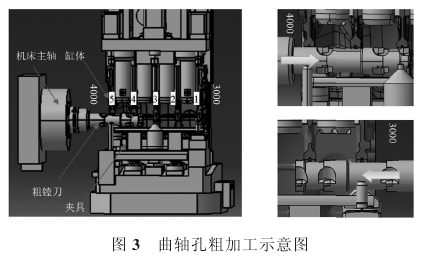
夾具的上升與下降可以通過PLC控製係統與油缸等機械部件實現(xiàn),夾具設計要保證工件的定位精度。曲軸孔位的(de)精度,由於缸孔未精加工,僅需考慮曲軸孔與設計基(jī)準的加工誤差。影響因素為工件的定(dìng)位誤差、設備的定位與重(chóng)複定位的誤差,托(tuō)盤的定(dìng)位與重(chóng)複定位誤差。依據ISO標準,若機床主軸的定位精度為0.006,重複定位精度為0.003,托盤的定位為5",重複定位精度為2";導套的位置偏差控製在0.003的範圍內,若工件的定位誤差≤0.02,經計算(suàn),長度400 mm的(de)曲軸孔,在設備(bèi)的精度範圍內,理論上其位置度將在0.034的區間範圍(wéi)內(nèi)(可信度≥99.74%)。
再考慮到實際加工刀(dāo)具(jù)的受力情況及原點定位的係(xì)統偏差,則加工後工件(jiàn)的(de)位置均值保證在0.05的偏差範圍內則(zé)可保證工序能力CPK≥1.33。 曲軸孔的圓度與同軸度,則與主軸的遠端跳動及整個係統的(de)剛性有關。因曲軸(zhóu)孔為雙材質(軸承蓋(gài)材(cái)質為粉末冶金,缸體材質為鑄鐵),其(qí)表麵粗糙度與孔徑的(de)工序能力較難保證,對刀具的剛性和刀(dāo)片的材質有較高(gāo)的要求。
經考證,刀具供應商有類似加工案例(lì),可以作為借鑒。綜上,采用CNC線鏜技術(shù)在當(dāng)前的技術條件下是可行的,可以進入實施階段。
2.2 曲軸孔線鏜(táng)夾具(jù)
曲軸孔精加工夾具如圖4所示,該工序選擇缸體底麵及底麵兩銷孔來定位。工件進入夾具後,支撐導軌動作,缸體下降到定位支撐處,圓銷(xiāo)與菱銷上升(shēng)進入定(dìng)位銷孔,油缸開始動作並夾緊缸體,待缸體定位氣密檢(jiǎn)測(cè)通過後,機床(chuáng)開始運行加工程序。
加工曲軸孔時,在鏜刀進入曲軸孔前,夾具油缸動作,夾爪鬆開,支撐導軌動作,缸體上升2.38 mm,待上升氣密檢測通過後,鏜刀偏心進入,鏜刀定位後,缸體恢(huī)複至初始夾緊狀(zhuàng)態。加工(gōng)結束後,之(zhī)前(qián)動(dòng)作重複一(yī)次,鏜刀偏心退出(chū)。
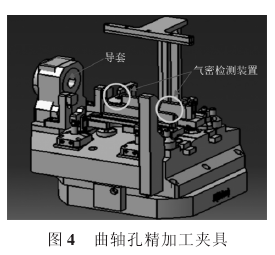
上升氣密裝置如圖(tú)5所示,在(zài)實際加工中,該氣孔容易進入鐵屑,造(zào)成氣密檢測(cè)報警,影響缸體線正(zhèng)常生產。為了(le)解(jiě)決這(zhè)個問題,臨時措施是經常用水(shuǐ)槍(qiāng)衝洗氣孔麵,後期對夾具進行改造,改造後的氣密檢測裝置(zhì)如圖6所示。該氣密檢測(cè)位於(yú)裝置內部,鐵屑無(wú)法進入,類似的報警問題將不會再出現。
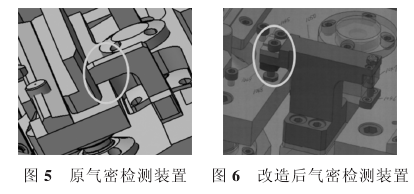
導套是運用於發動(dòng)機曲軸孔加工的一(yī)個(gè)精密機床部件。滾動導套的結構、精度、安裝、調試、使用、維護及與之相(xiàng)配的直線鏜杆的精度、直線鏜杆與(yǔ)滾動導套的配合間(jiān)隙等將(jiāng)直接影響所加工的曲軸孔的粗(cū)糙度、圓柱度、同軸度。本(běn)夾具使(shǐ)用GATCO精密滾動(dòng)導套,由靜(jìng)止外套、與鏜杆一起旋轉(zhuǎn)的淬硬並經過磨削的內套、精密(mì)軸承、密封件組成。
導(dǎo)套在夾具上的(de)安裝定位(wèi)方式采用導套外(wài)徑定位,與夾具定位孔(kǒng)的配合選用間隙配合,這樣可以避免軸承外圈因溫度升高而膨脹影響滾動(dòng)導套回轉精度和壽命,一般要(yào)求滾動導套外徑與夾具定位孔的內(nèi)徑至(zhì)少留(liú)有0.008 mm的間隙。
2.3 曲軸孔線鏜刀具
2.3.1 線鏜刀
曲軸孔線鏜刀通過(guò)刀杆頭部的導向鍵與導(dǎo)套實現固定(dìng)聯(lián)接,刀杆材(cái)質(zhì)為(wéi)重(chóng)金屬,在刀(dāo)杆上分布著五組半精鏜刀片和精鏜刀片,如圖7所示。
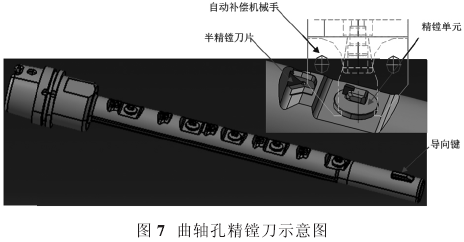
第二次半精鏜(táng)留下單邊(biān)0.05~0.06的餘量。其中每個精鏜單元(yuán)都可以單獨調整,調整精度在直徑方向能達到0.002 mm,保證(zhèng)極好的孔徑公差。刀片磨損後在機床數控係統輸入孔徑(jìng)數據,可通過自動補償機械(xiè)手調節精調單元,調(diào)整刀尖高度。自動補(bǔ)償機械(xiè)手(shǒu)卡爪(zhǎo)上帶有金剛(gāng)石塗層,具有防滑效果。
2.3.1.1 自動補償裝置
說明:“Y”表示本次刀(dāo)具自(zì)動補償成功,“N”表示本次刀具(jù)自動補償(cháng)不成功(gōng),試驗前1檔表讀數為100,2檔表讀數為98,3檔表讀(dú)數(shù)為99,4檔表(biǎo)讀數為99,5檔(dàng)表讀數為95。
在使用過程中,發現機械手調刀的準確性、可靠性不能滿足要求。為驗證機械手自動調整性能,我們做了(le)調(diào)刀試驗。
試驗方案為:
1)試驗前記錄每檔刀片高度;
2)通過機械手自動調刀機構將孔(kǒng)徑調(diào)大或調小2~6 μm;
3)自動調刀後,測量並記錄各檔刀片高度(表1),看其是否變化及其變化量。
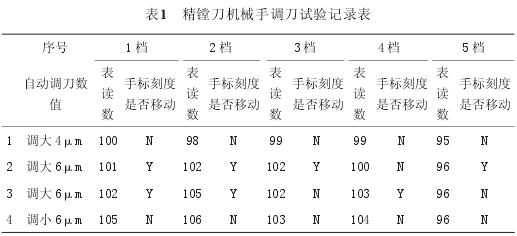
從表1可知,機械手自動調刀不成功率為65%。對精鏜單元依據數據進行持續改進,經過多次驗證,發現改進後(hòu)的精鏜單元通過機械手(shǒu)調(diào)整(zhěng)的數值比實際輸入值小2μm, 按(àn)照此規(guī)律(lǜ),目前已能用機械(xiè)手自動調刀。
2.3.1.2 線鏜的精鏜刀片
線鏜刀首次實(shí)驗刀片為SPCE731 UK20, 是非塗層硬質合金刀片,在用各種組合參數試切削後,曲軸孔的表麵粗糙(cāo)度為Rz12~18 μm,達(dá)不到圖樣要求。通過更改刀片材質 , 選用(yòng)一款金屬陶瓷刀片SPCE731 VC610。此次變更刀(dāo)片材質後,表(biǎo)麵粗糙度上有較大的改善,能(néng)到達Rz8~10 μm,但孔(kǒng)徑減小很快,刀片(piàn)抗磨損能力較(jiào)差。再次(cì)改善,選用SPCE732 VC610和Ti Al N物理塗層的SPCE732 VC610兩種方(fāng)案。
試切(qiē)削後,發現隻是增大圓角方案SPEC732 VC610刀(dāo)片(piàn)的(de)抗磨損能力沒有明顯增強,而加了塗層(céng)的刀片,雖在(zài)抗磨損方麵有了很大(dà)的提升,但是粗糙度有所提高。而後又將塗層後(hòu)的刀片做頂麵拋光處理,使刀尖變得更圓滑,來降低(dī)加工粗糙度,結果還(hái)是不理想。
隨後,我們對線鏜刀的刀片材質進行了另外一(yī)種方(fāng)案的驗證,即更換(huàn)現有的硬質合金刀片(piàn)材料為CBN刀片材(cái)料,選用型號為(wéi)SPHN050204-T01015。然後,進行(háng)了新刀片的驗證工作,該刀片總共試驗3次(cì),第(dì)一次總加工件數(shù)為(wéi)152件;第二次總加(jiā)工件數為246件,平均加工29件調一次刀;第三次(cì)總加工件數為250件,平均加工27件調一次刀。從本次試驗來看,在粗糙度的控製方麵CBN刀片明顯優於硬質(zhì)合金刀片,單刃(rèn)均加工壽命能夠突破210件,調刀(dāo)頻次也可滿足生產要求。
經過不斷地摸索與改進(jìn),目前該刀片平(píng)均每(měi)刃加工(gōng)件數可達260件。
2.3.2 曲軸孔線(xiàn)鏜
主軸夾緊刀(dāo)具→刀具進入曲軸(zhóu)孔→刀頭(tóu)進入導向(xiàng)套→夾具托盤下降→夾緊工件→鏜刀與曲軸(zhóu)孔同軸→半精(jīng)鏜曲軸孔(五檔同步)→精鏜曲軸孔(拉鏜順序:5檔→2檔→3檔
→4檔→1檔)→夾具放鬆→工件上(shàng)升→鏜刀退出,加工過程如(rú)圖8所示。
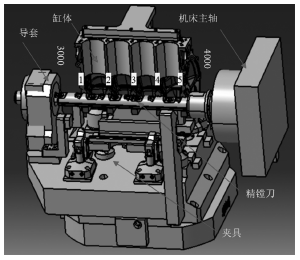
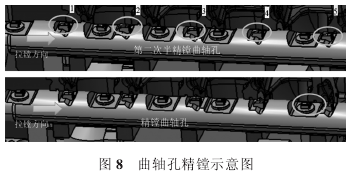
經過機床與刀(dāo)具的多次實(shí)驗調整,第1檔(dàng)與第2檔的各項數據穩定,達到Cpk≥1.33的要求,如圖9選取第1檔的直徑(jìng)數據。但第(dì)3檔的直徑隻達到Cpk=1.0。針對(duì)該問題,我們(men)將繼續在刀片(piàn)的材質、調刀的穩定性等方麵做進一(yī)步的改善(shàn)。
此狀態可以進入量產,但需加大工件的抽檢頻次,並對數據做持續的監控。
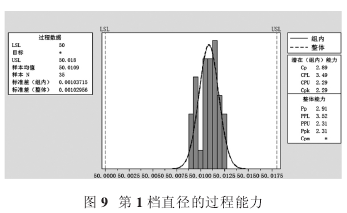
3 、結(jié)語
本文研究並實踐基於加工中心的線鏜工藝,通過(guò)對線鏜夾具的設計、刀具和刀片的改進,實現(xiàn)了(le)多品種共線的生產模式,經實踐驗證,中、小批(pī)量生產質量(liàng)較為穩定。鑒於缸體曲軸孔的重要性,在今後(hòu)生產過程中還需對(duì)曲軸孔的粗、精加工進行緊(jǐn)密跟蹤,通過不斷摸索與改進(jìn),使其(qí)達到最佳狀態。
投(tóu)稿(gǎo)箱:
如果您有機床行業、企業相關新聞稿件(jiàn)發表,或進行資(zī)訊合作(zuò),歡迎聯係(xì)本網編輯部, 郵箱:skjcsc@vip.sina.com
如果您有機床行業、企業相關新聞稿件(jiàn)發表,或進行資(zī)訊合作(zuò),歡迎聯係(xì)本網編輯部, 郵箱:skjcsc@vip.sina.com
更(gèng)多相關信息
業界視點
| 更多
行業(yè)數據
| 更多
- 2024年11月 金屬切削機床產(chǎn)量數據
- 2024年11月 分地區金屬切削機床(chuáng)產量數據
- 2024年11月 軸承出口(kǒu)情況
- 2024年11月 基本型乘用車(chē)(轎車)產量數據
- 2024年11月 新能源汽車產量數據
- 2024年11月 新能源汽車銷量情況
- 2024年10月 新能源汽車(chē)產量數據
- 2024年10月 軸承出口(kǒu)情況
- 2024年10月 分地區金屬(shǔ)切削機床(chuáng)產(chǎn)量數據
- 2024年10月 金屬切削機床產量數據
- 2024年9月 新能源汽車銷量情況
- 2024年8月 新能源汽車產量數據
- 2028年8月 基本型乘用車(轎車(chē))產量數據