【技術淺析】數(shù)控機床軸承結構振動諧響應及(jí)疲勞壽命(mìng)研究
2020-11-9 來源:貴州師範大學 機械(xiè)與電氣(qì)工(gōng)程學院等 作者:沈(shěn)明明(míng),李榮,劉祖國(guó),湯(tāng)耿
摘要: 以(yǐ)數控機床用的(de)深溝球軸承為研究對象,分析其運轉中的振型及結構疲勞壽命。首先通(tōng)過Solidworks 建立了深溝球(qiú)軸承的三維模型,利用ANSYS 對軸承進行模態及(jí)諧響應分析,獲得軸(zhóu)承在固(gù)有振動頻率以(yǐ)及在各階次頻率下(xià)的固有振(zhèn)型變化,同時借助有(yǒu)限元諧響應分析,確定了對軸(zhóu)承(chéng)影響最大的(de)模態頻率(lǜ)。其次利用 ANSYS 中的 Faigue 模塊對軸承進行了疲勞壽命研究,通過結合材料的 S-N 曲線理論以及 Hertz 接觸(chù)理論(lùn),對軸承的疲勞壽命(mìng)進行了預(yù)估(gū)分析。仿真結果表明: 在滿足軸承強度工況下,固有頻率 1125Hz 為結構(gòu)共振最大點,且軸承的壽命範圍為5937. 7 ~ 1 × 106次,為後續軸承結構優化提供參考。
關鍵詞: 深溝球軸承; 模態振型; 振動諧響應; 疲(pí)勞敏感性; 疲勞壽(shòu)命
0、引言
隨(suí)著製造工業技術的快速發展,數控(kòng)機床被廣泛(fàn)應用(yòng)於關鍵零部件的加工製造,而主軸係統(tǒng)中軸承結構則是其運轉的關(guān)鍵部件。軸承(chéng)作為重大機械傳動中的重要支(zhī)承傳動部件並且能夠減少摩(mó)擦,因此軸承的好(hǎo)壞直接(jiē)關係到機床加工精度和工作效率等性(xìng)能。
同時軸承的振動疲勞破壞一直是影響機械結(jié)構(gòu)運行的關鍵(jiàn)因(yīn)素。近幾年(nián),國內外學者對軸承結構的運行狀態及振(zhèn)動(dòng)變化進行了研究分析,文獻通過利用有(yǒu)限元法對航空圓柱滾子軸承(chéng)的溫度場及(jí)應力分(fèn)布進行仿真分(fèn)析(xī)同時還對軸承(chéng)熱力耦合下的疲勞壽命進行研究,文獻通過建立接觸模型,提出了(le)一種(zhǒng)載荷計算分布模型對深溝球軸承內部載(zǎi)荷序列與(yǔ)壽命進行計算。文獻中HOUPERT 分析了滾動軸承在(zài)運行過程中對(duì)疲勞壽命造成影響的因(yīn)素(sù),上述研究都(dōu)取得了一定的效果,但都隻是單一(yī)的針對軸承的溫度場及載(zǎi)荷序列進行研究。針對(duì)軸承振動諧響應與壽命的(de)研究的報道並不多。
因此,本文以數控機床用深溝球軸承(chéng)為研究對象(xiàng),通(tōng)過對軸承結構進行參(cān)數化建模,分析軸承靜(jìng)應力及模態振型變化。結合諧響應分析模塊,利用模態疊加法分析深(shēn)溝球軸內圈的(de)諧響應變化(huà)。同時利用材(cái)料的S-N 曲線及(jí)疲勞靈敏度曲線對軸承進行了(le)恒定載荷工況(kuàng)下的(de)疲勞壽命研究,為數控機床主軸係統軸承振動疲勞分析及優化提供了參考。
1、深溝球軸承有限(xiàn)元分析
1.1、深溝球軸承靜應力分析
軸承結構在運行過程(chéng)中其結構的振型變化將會直(zhí)接對結構的性能造成一定的影響,因(yīn)此結構的振動特性決定(dìng)了結構在不同(tóng)載荷(hé)情況下的(de)響(xiǎng)應變化,所以對(duì)結(jié)構進行模態振型仿真分析具(jù)有重要意義。
由於在(zài) ANSYS 中的建模工具並不成熟,因此本文利用 Solidworks 建(jiàn)立(lì)了深溝球軸承(chéng)的參數化(huà)三維模(mó)型(xíng),通過轉(zhuǎn)變模型(xíng)的格式聯立到 ANSYS 中進行分析,在進行(háng)分析時需要對結構的材料進(jìn)行定義,本文分析時主要是利(lì)用有限元的方法進行利用,因此本文設定(dìng)結(jié)構的材料都為軸承鋼,其泊鬆比 為 0.3,密度為7810kg/m3,彈性模量為210GPa,設定完(wán)材(cái)料參(cān)數後,需要對結構的網格進(jìn)行定義,因為在仿真分析時結構的網格是否合格直接影響到結構的分析精度,雖(suī)然係統有手動劃分(fèn)網格的功能,針對複(fù)雜的(de)幾(jǐ)何結構(gòu)大多采用自動劃分功能,通過設定網格為 Fine 劃分得到如圖 1 所示的深溝球軸承有(yǒu)限元網(wǎng)格模型,其中網(wǎng)格節點為10536,單元數為3950,網格質量為良好。
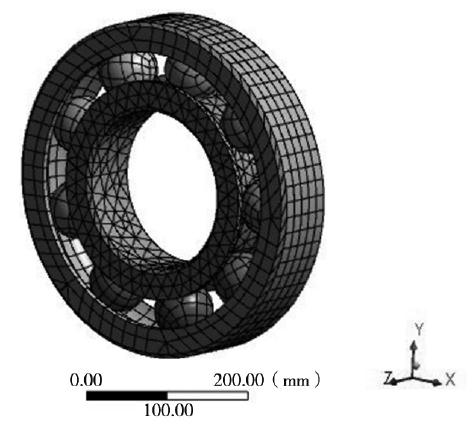
圖1 . 深溝球軸承有(yǒu)限(xiàn)元網格(gé)模型
1.2、邊(biān)界條件設定(dìng)
在軸承運行過程中,其中內圈是與轉子軸接觸,外圈則一般是與固定件接觸在一起,因此在設置深溝球軸承約束條件時將圖 1 中軸承外圈設定為固定(dìng)約束,內圈(quān)設定為旋(xuán)轉(zhuǎn)約束(shù),本文轉速(sù)設(shè)置為10000rpm。
1.3、有限元靜應力結果
通過設定完結構的邊界約束條件和網格模型後,在靜應(yīng)力模塊中選中變形模塊及平均應力模塊,分析解算得到如圖 2a 所示的靜應力總變形和圖 2b 所示(shì)的軸承平均應力雲圖。
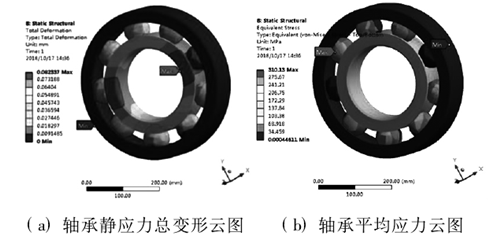
圖2 . 軸承靜應力應變形雲圖
從圖 2 中的雲圖可知(zhī),深溝球軸承的最大變形量為 0.083mm,軸承的最大平均應力為 310MPa,由(yóu)於在設定材料時,定義的軸承材料為是軸承鋼,彈性模量為210GPa,屈服強度為 1667MPa。根據第 4 強度理論(lùn)可以(yǐ)計算材料是否符合強度要求,強度公式為:

式中,σ1,σ2,σ3為 3 個法向的應力。在計算材料的許用應力時,安全係數一般(bān)取的是 1.5,通過許(xǔ)用應(yīng)力公式計算可得到。許用應(yīng)力公式(shì):

通過結合式( 1) 與式( 2) 可以計算軸承的許用應力為 1111.3MPa。結合圖 2 應(yīng)力雲圖可得(dé) 310MPa≤1111.3MPa,所以創建的軸承結(jié)構的強度滿足設計分析要求。因此在(zài)後續的諧響應分(fèn)析及疲勞壽(shòu)命的分析中可以(yǐ)獲得軸承具有參考價值的數據參數,為後期軸(zhóu)承的改進提供有效的優化方案。
1.4、深溝球軸承模態(tài)分析
在繪製深溝(gōu)球軸承結構的三維模型時,忽略掉一些對結構影響(xiǎng)不(bú)明顯特征,這樣將能加快求解時間。由於軸承產生破壞的階段主(zhǔ)要是在負載工況下發生的,所以本文在繼承靜應(yīng)力分析的基礎上對軸承的(de)模態振型進行研究(jiū)分析。設定模態階數為 6 階,得到軸(zhóu)承的前 6 階模態固有頻率如表 1 所示。
表 1 深溝(gōu)球軸承前 6 階振型
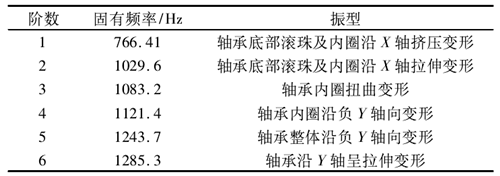
結(jié)合 1.1 節的模態有限元分析可知,結構在運轉過程中,主要(yào)是(shì)低階模態的振型對結構(gòu)的破壞較為關鍵,因此在有限元分析時不(bú)需要考慮到(dào)高階模態的振(zhèn)型,因此選取了軸承的前 6 階進(jìn)行模態振(zhèn)型分析,模態分析結果如圖 3 所示。
從圖 3 中模態振型變化中可以得到,軸承的低階模態振型變化量較大,主要對內圈的軸向振動變形較為明顯,其中在模態 2 階中振動變形(xíng)達到最大,最大約為 20mm,可以判定在內圈與滾(gǔn)珠接觸的部位較為薄弱,為提高軸承的(de)可靠性及壽命(mìng)可以在與軸承的內圈與滾珠接觸部(bù)位提高加工精度或對滾道進行特殊處理,以提高滾道的光(guāng)滑度及強度。對此在本文的(de)後續諧(xié)響(xiǎng)應分析中主要對(duì)軸承結構的內圈進行分析(xī),為後續軸承結構的優化及加工提供參考。
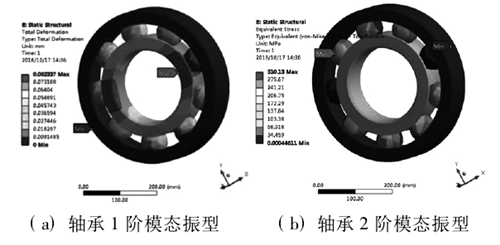
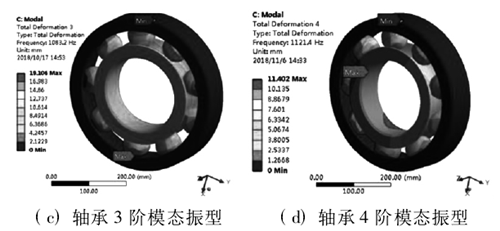
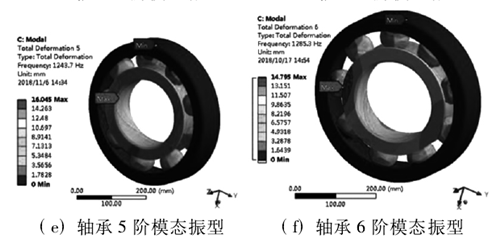
圖3 . 深溝球軸承前6階模態(tài)振型雲圖
1.5、深溝球軸承諧響應分析
結構的諧響應分析主要是(shì)對載荷在(zài)不同頻率(lǜ)下的振動響應,直接與結構的載荷有關,而(ér)模(mó)態分析的(de)結果隻是單一(yī)的(de)獲得在某一頻率下的(de)振型變化,並(bìng)不能獲得在不同頻率(lǜ)下的變形。因此結合(hé)模態分析結果搭建諧響應分析來提高諧響應分析結果的可用性,同時通過(guò)諧響(xiǎng)應分析還可為軸承的疲勞破壞和共振破壞具有一定預(yù)測作(zuò)用,對此本文通過模態疊加法開展軸承結構的諧響應分析,在求解中的設置(zhì)條件為:
① . 設置軸承的邊界條件參考 1. 2 節中的條件。
② . 從圖 3 的模態雲(yún)圖和(hé)表 1 中(zhōng)的前 6 階固有頻率可知(zhī),軸承的第6階頻率為 1285.3Hz,對此(cǐ)設置諧(xié)響應的分析範圍為(wéi)0~1500Hz,同時為了(le)提(tí)高計算結果的(de)精(jīng)確(què)性設置求解步數為 100 步對應的有100個解。由(yóu)模態分析可知變形主要(yào)發生在軸承的內圈,因此在諧響應分析中主要選取內圈進行(háng)了諧響應分析(xī),通過求解(jiě)計算獲得了內圈沿 X、Y、Z 方向的位移變化情況,如圖4所示。
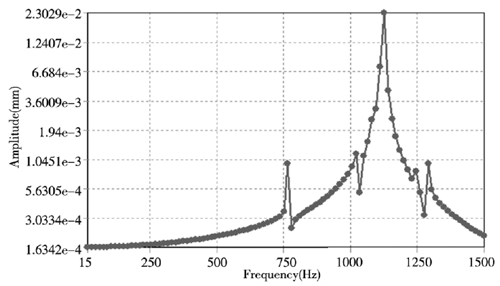
(a) X 方(fāng)向
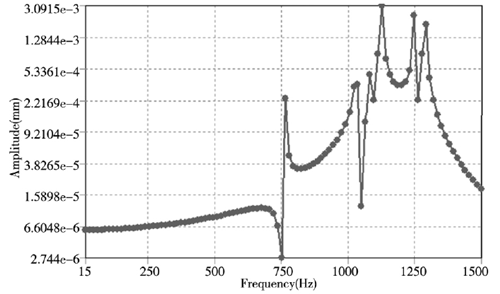
(b) Y 方向
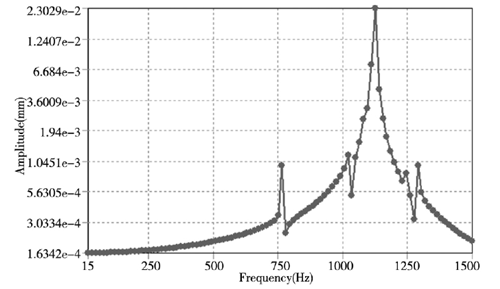
(c) Z 方向
圖4 . 軸承(chéng)內圈(quān)結構 X、Y、Z 方向位移響應曲線
從圖 4 中的軸承內圈(quān)結構 X、Y、Z 方向位移響應曲線可知,軸承結構的位移響應隨著頻率的增(zēng)加而增加,呈正相關。而在 X、Z 方向的位移在模態 5 階( 約1125Hz) 時達到最大位移變化,最大變化量為0.023mm,而對於Y方向的位移變化量(liàng)則(zé)較小為0.003mm,這要是軸承在 Y 方向上主要是受(shòu)到徑向的力,而 X 和 Z 方向還會受到(dào)沿 X 軸的軸向(xiàng)力,因此在 X和 Z 方向的位移較大(dà),雖然 Y 方向(xiàng)的最大位移量沒有X 和(hé) Z 方向的大,但在頻率(lǜ)從1階到 6 階(jiē)範圍內位(wèi)移變形量較為均勻,因此造成的破壞不容忽視。通過對軸承的(de)諧響應的分析可知(zhī) X、Y、Z 方向所造成(chéng)的(de)影響都不可忽視,在後期優化和加工工藝中通過設計特定的工裝(zhuāng)來優化軸承的結構,諧響應分析結果也為後期同類產品的優化提供參考。
2、深溝球軸承疲勞壽命分(fèn)析
2.1、Hertz 接觸應(yīng)力計算
在分析軸承應力疲勞壽命時(shí),應先分(fèn)析軸承的應力,同時找到軸承的最大應(yīng)力區域。對此依據 Hertz接觸應力理論對軸承的應力進行分析,在接觸應力中(zhōng)接觸載荷 Q 與彈(dàn)性趨近量 δ 滿足下式:

式(shì)中,K 代表接觸體之間的載(zǎi)荷變形係(xì)數,一般與接觸(chù)體的材料及外形有關(guān)。
在軸承工作過程中,由於內外滾道(dào)的直徑差異,滾道對滾珠的接觸應力也有所不同(tóng),同時 2 滾道的法向趨近量等於滾珠分別與內外滾道趨近量之和,滿足下式:

對於深溝球軸承,式(shì)( 3) 和式( 4) 中的 n 係(xì)數一般取 1.5。通(tōng)過 Hertz 理論分析球軸承的接觸問題,其最(zuì)大的接觸應力為:

式中,a 表示接觸橢圓的長半軸; b 表示接觸橢圓短半軸。
通過上式理論分析(xī)在結合圖 2 所示的靜應力仿真分析雲圖可知,接觸處的正壓力主要為滾珠與內外(wài)圈接觸部位,其值(zhí)沿曲麵軸向與法向(xiàng)變化(huà),與(yǔ)式( 5) 的接觸理論分析一致。
2.2、疲勞分析
采用 ANSYS 聯合仿(fǎng)真對深溝球軸承進行疲勞計算,在分析軸承(chéng)靜應力的基礎上聯合(hé) Faigue 模塊進行分析,在分析設置(zhì)中為了提高分析的有效性,在(zài)搭建的Faigue 模塊(kuài)中設置疲勞強度因子為 0.8,通過反複模擬分析取最小基本載荷變化(huà)幅度和最大基本載荷幅度分別(bié)為 10% 、300% ,由此獲得軸承結構的疲勞敏感性曲線如圖 5 所(suǒ)示。
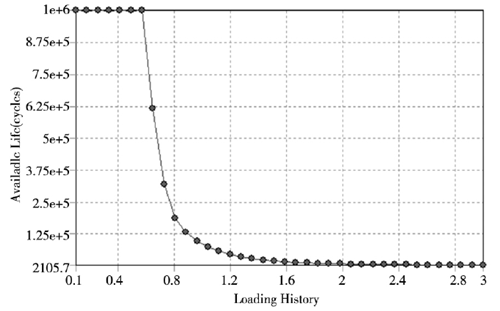
圖5 . 深溝球軸承疲勞敏感性曲線
在設定軸承的疲勞安全因子分布雲(yún)圖命令,可獲得如圖 6 所示的安全因子分布雲圖(tú)。從圖 6 中可以得到,本文選取的深溝球軸承最小安全影響(xiǎng)因子為0.27795,最容易(yì)發生疲勞破壞的部位主要是軸承內圈,這與實際工況下的破壞一致,為提高壽命(mìng),在(zài)後續的優化設計可以改變內圈材料及內圈與滾珠(zhū)接觸處的尺寸(cùn)參數來提高軸承內圈的使用壽命。由圖 5 中的敏感性曲線可知,軸承在載(zǎi)荷變(biàn)化幅度為 10% ~ 60% 範圍內對軸承的壽(shòu)命影響不大,但在載荷變化幅(fú)度(dù)超(chāo)過200% 時則直接對軸承造成破壞(huài)不滿足設計要求,通過上述(shù)分析(xī)可為軸承在設計中(zhōng)驗證軸承疲勞壽命是否滿足要求提供參考。
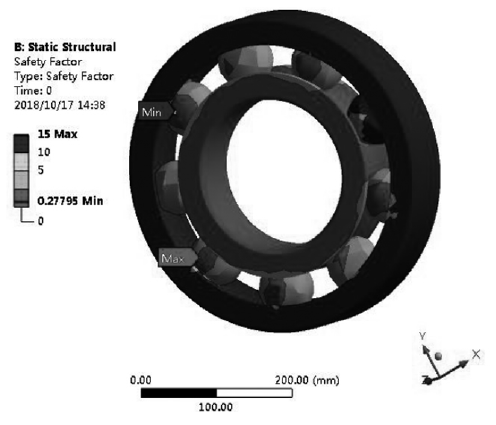
圖6 . 深溝球軸承(chéng)安全因子雲圖
2.3、振動疲勞壽命計算
一般情況下軸承的循環壽命較高(gāo),屬於低應力高周疲勞,通過采(cǎi)用(yòng)全壽命分析方法,即 S-N 曲(qǔ)線對(duì)軸承進行疲勞壽命(mìng)分析計算,通過上述的對軸承的材料進行定義得到軸承的 S-N 曲線如圖 7 所示。
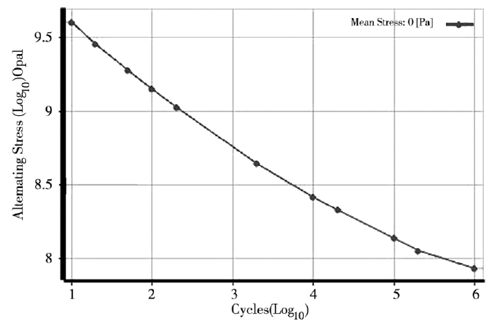
圖7 . 軸承 S-N 曲線
在有限元(yuán)分析中,設置雨流循(xún)環計數的方法對不規(guī)隨(suí)機的載荷時(shí)間曆程曲(qǔ)線進行轉化成一係列恒定幅值的載荷,本文設定的載荷(hé)為恒定幅值載(zǎi)荷對軸承進行疲勞壽命預估,如圖 8 所示。
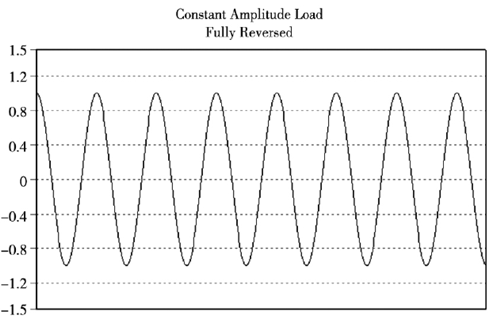
圖8 . 恒定幅值載荷
其中疲勞壽命(mìng)公式如下:

式中,Sm表示平均(jun1)應力; Smax表示最大應力取310MPa; Smin為最小應力取 34MPa; Sa表示交變應力幅。
其(qí)中平均應(yīng)力的修正應力公式(shì)為:

式中,Sn為平均(jun1)應力 Sm的修正應力;
由圖 7 所示的軸(zhóu)承 S-N 曲線來計算曲線間的斜率h,可以假設 S* N = C 為直線,利用最小二乘法來擬合出最優的直線方程,擬(nǐ)合得到如(rú)下方(fāng)程:
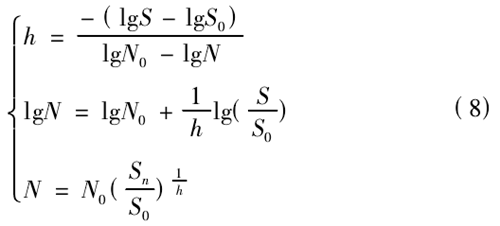
式中,N0表示循環次數,N0= 1 × 106; S0表示(shì)在 N0=1 × 106時的(de)應力;
結合圖7可知 lg N0= 6,lg S0= 7.88,lg N = 3,lg S = 8.75 ,通過計算可(kě)得到 h 值為 - 0.29。其(qí)中平均應力 Sm的修正應力為:Sn=153.8MPa 將其帶入式(8) 中可(kě)得軸承疲勞壽命 N≈8.74 × 104次。結合圖5的(de)敏(mǐn)感性曲線圖可知軸承的載荷變化幅度在 10% ~60% 範圍內,因此對(duì)軸承的壽命影響不大,滿足疲(pí)勞壽命設計要求。
同時借助有(yǒu)限元 Faigue 分(fèn)析模塊,對深溝球軸承循環次數的疲勞壽命進(jìn)行求解計算(suàn),可獲得圖 9 所示的軸承疲勞壽命雲(yún)圖。
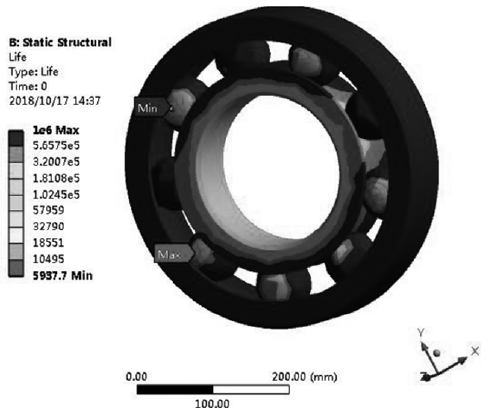
圖9 . 深(shēn)溝球軸承疲勞(láo)壽命( 循環(huán)次數(shù))
由圖(tú) 9 中的疲勞(láo)壽命分(fèn)析雲圖可知,當工況條件為轉速(sù)設置 10000rpm 時,軸承(chéng)的壽命範圍為(wéi) 5937.7 ~1×106次,壽命較小處為軸承的滾珠外側和軸承內圈部位,但是壽命薄弱處較少(shǎo),其有限元(yuán)疲勞壽命分析與理論計算(suàn)結果大體一致,且有限元分(fèn)析法能夠將疲(pí)勞破壞點清晰直觀的(de)表(biǎo)示出來,由此可知通過利用有限元法對結構做疲(pí)勞壽命分析是可靠的,可為後續結構優化提供參(cān)考。
3、結 論
深溝球軸有(yǒu)限元靜應力及模態分析,能獲得結(jié)構的固有頻率及振型變化,可為結構的諧響應及疲勞分析提供基礎(chǔ)。
(1)、結合有限元靜應力及模態分析結果,采用模態疊加法,搭建了軸承結構的諧響應分(fèn)析模塊,獲得了軸承內圈沿 X、Y、Z 方向上的位移響應曲線,得到了軸承在 X、Z 方向的位移在模態 4 階( 約1125Hz) 時(shí)達到最大位移變(biàn)化,最大變化量為 0.023mm;
(2)、通過利用材料的 S-N 曲線理論以及 Hertz 接觸理論開(kāi)展了軸承結構的疲勞壽命分析,在靜應力分析的基礎上,通過(guò) Faigue 模塊建立軸承結構的疲勞分析模型,理論(lùn)疲勞壽命為 8. 74 × 104次,與仿真分析結果大體一致,驗證了仿(fǎng)真計算的可行性,也為軸承結構的後續優化提供參(cān)考,加快研發(fā)進度。
投稿箱(xiāng):
如果您有(yǒu)機床行業、企業相關新聞稿件發表,或進行資訊合作,歡迎聯係本網編輯部, 郵箱:skjcsc@vip.sina.com
如果您有(yǒu)機床行業、企業相關新聞稿件發表,或進行資訊合作,歡迎聯係本網編輯部, 郵箱:skjcsc@vip.sina.com
更多相(xiàng)關信(xìn)息
業(yè)界視點
| 更多
行業數據
| 更多
- 2024年11月 金屬切削機床產量數據
- 2024年11月 分地區金屬切削機床產(chǎn)量數據(jù)
- 2024年(nián)11月 軸承出口情況(kuàng)
- 2024年11月 基本型(xíng)乘用車(轎車)產量數據
- 2024年11月 新能源汽車產量數據
- 2024年11月 新能源汽車銷量情況(kuàng)
- 2024年10月 新能源汽(qì)車產量數據(jù)
- 2024年10月 軸承出口情況
- 2024年10月 分地區金屬切削機床(chuáng)產量數據
- 2024年10月(yuè) 金屬切削機床產量(liàng)數據
- 2024年9月 新能源汽(qì)車銷量情況
- 2024年8月 新能源汽(qì)車產量數據
- 2028年8月 基本型乘用車(轎車)產量數據
博文選萃
| 更多
- 機械加工過程圖示
- 判斷一台加工(gōng)中心精度的幾種辦法
- 中走絲線切割機床的(de)發展趨勢
- 國產數控係統和數控機床何去何從?
- 中國的技術工人都去哪裏了?
- 機械老(lǎo)板做了十多年,為(wéi)何還是小作坊(fāng)?
- 機械行業(yè)最新自殺性(xìng)營銷,害人害己!不倒閉才
- 製造業大逃亡
- 智(zhì)能時代,少談點智造,多談點製(zhì)造
- 現實麵前(qián),國人(rén)沉默。製造業的騰飛,要從機床(chuáng)
- 一文搞懂數控車(chē)床(chuáng)加工刀具補償功能(néng)
- 車床鑽(zuàn)孔攻螺紋加工方法及工(gōng)裝設計
- 傳統鑽削(xuē)與螺旋銑孔加工工藝的區別