剮齒加工技術與(yǔ)刀具(jù)設(shè)計
2019-5-5 來源:湖南(nán)中大創遠數控裝備有限(xiàn)公司, 作者:李錫晗
摘要:麵對國內汽車市場的快速發展(zhǎn),以及機械行業對齒輪(lún)加工製造技術提升的需求,原(yuán)有(yǒu)的齒輪加工技術已不能滿足當前的要(yào)求,文中介紹了一種新(xīn)的圓柱齒輪加工工藝方法———剮齒加工,分析介紹了剮齒加工中存在的問題,提(tí)出了刮齒加工中存在問題的解決(jué)方案,以及在這種方案下的刀具參數的修正方法,經過實際驗證,在(zài)加(jiā)工效率、產品精(jīng)度、節能與環保等方麵取得了良好的(de)效果,尤其在內齒的加工上,展現出了更大的優勢,並提供了加工實例以供參考。
關鍵詞:圓柱齒輪(lún);剮(guǎ)齒(chǐ);刀具;刀具前角
隨著我國製(zhì)造技術需求的快速提(tí)升, 製造業各項技術均得到(dào)了迅猛的發展,齒輪加工(gōng)製造技術向著高精度、高效率、高可靠(kào)性、低能(néng)耗、綠色環保的方向快速發展,同時,由於國內工程機械、交通(tōng)運(yùn)輸(shū)業(yè)的快速發展,數(shù)控技術廣泛應用於(yú)齒輪製造,極大推(tuī)動了齒輪技術的進步。隨著國內汽車業(yè)的發展,我國已(yǐ)在短(duǎn)短(duǎn)幾年成為全球第一生產大國,飛速發展的(de)汽車業帶(dài)動了(le)相(xiàng)關產業的提升,而圓柱齒輪加工一直被滾齒、插齒、銑齒、滾軋、剃齒、磨齒等傳統的加工方法所主導(dǎo),陳舊的加工方式已(yǐ)不能滿足發展的需要, 廣(guǎng)泛應(yīng)用的乘用車 AT 變(biàn)速器行星輪減速(sù)機構的齒圈和行星輪, 由於加工技術上的不(bú)足而難於保證產品技術目標的達成,巨大的(de)市(shì)場需(xū)求(qiú)卻全麵依靠進口。 德國 WERA 公司推出的 SCUDDING 技術成功在該行業展示出強大的技術優勢,而正因(yīn)其技術具有非常顯(xiǎn)著的優勢, 其對該項技術包括加工工藝、裝備、刀(dāo)具等進(jìn)行了全麵的技(jì)術封鎖,近年來國際上的齒(chǐ)輪加工裝備製造(zào)商 (如美國格裏森) 也加入該技術研究開發(fā)的行列,為此,我們對該種加(jiā)工技術(shù)進行了深入的研究與試驗、驗證,並(bìng)取得了較為理想的效果(guǒ)。
1、 全新的圓柱齒輪加工原理
該種加工方法命名為“剮齒加工方式”。 剮(guǎ)齒加工仍(réng)基於齒(chǐ)輪加工技術(shù)中成熟的展成加(jiā)工技術理論基礎, 即采用齒形刀具,在刀具與產品之間模擬一對齒輪齧合運動過程,同時,增加刀具相對於產品的連續的軸向相對運動和斷續的徑向相對運動,以實現刀具的進給運動,來實現(xiàn)齒輪產品的加工。 其(qí)加工裝備如(rú)圖 1所示(shì)。
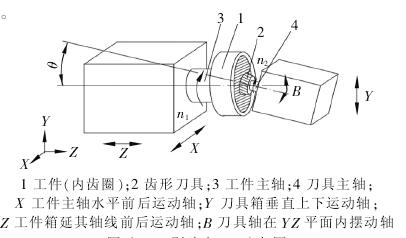
圖 1 剮齒加工示意圖
工件與刀(dāo)具同時旋轉,工件(jiàn)隨其主軸的轉速 n1, 角速度 ω1運(yùn)轉,刀具隨其主(zhǔ)軸的轉速 n2,角速度 ω2運轉,刀具與被加工產品(pǐn)形成一對相互齧合的齒輪。同時,為在這(zhè)一狀態下實現齧合點的齒向方向的位移,保證產品剮削加工的順暢,使工件主軸的軸線與刀具主(zhǔ)軸的軸線相對傾斜,即模擬(nǐ)交錯軸齒輪(lún)齧合狀態(圖2), 形成的軸交角設為 θ, 一(yī)般情況下根據產被加工產品的材(cái)質、規格、刀具材料、工藝等條件選擇軸(zhóu)交角,推薦軸交角的範圍為 5°~35°,確定(dìng) θ 後,即可確定刀具(jù)的螺旋角:
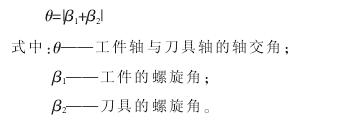
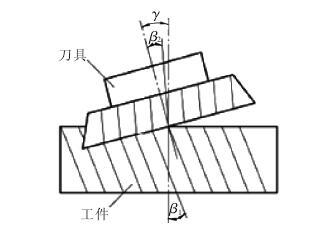
圖 2 交錯軸剮齒加工(gōng)示意圖
根(gēn)據刀具加工點的切削線(xiàn)速度(dù)來確(què)定刀具軸的轉速, 而後可由工件與刀具的齒數計算得出符合齒輪齧合傳動的工件軸轉速;在這 2 個轉速確定後,需對工件軸的轉(zhuǎn)速進行修正,該修正量是由於 Z軸的軸向進給和(hé)被加工齒輪的螺旋角 β1而(ér)附加到模擬(nǐ)齧合(hé)傳動中的,即用 Z 軸軸(zhóu)向進給速度和產品螺旋角 β1等參數進行計算修正, 以保持在加(jiā)工過程中的每一時刻刀具與產品之間正確的(de)齧(niè)合關係。
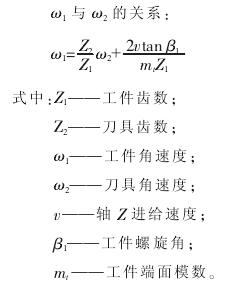
加工過程中齒深的(de)進給運動, 由刀具與產品之間的徑向進給實現,徑向進給采用階段進給方式,由(yóu) X 軸分幾次完成齒全高的切削加工(gōng); 對於如汽車同步器中(zhōng)的錐形齒盤等特殊的錐(zhuī)形內、外齒要求,可以采取徑向連續式聯動進給來實現。刀具的刃形設計成與工件齒形共軛的形狀。加工時,刀具(jù)的刀齒從非齧合(hé)狀態逐步進入齧合狀態, 切削過程從即將進入齧合狀態的(de)刀齒的齒根部的齧合起始點開始, 延刀(dāo)齒的齒廓漸漸向(xiàng)齒頂方向移動, 再由齒頂推進到另(lìng)一個齒廓麵並逐步接近脫離齧合的終止點;配合交錯軸傳動中的齧合點的軸向(xiàng)位移、Z 軸的軸向進給即(jí)可完成指定齒深下齒槽的切削(xuē)加工;而後由間斷的 X 軸徑向進給運動, 改變指(zhǐ)定(dìng)齒深(shēn)重複 Z 軸(zhóu)的軸向進給加(jiā)工,直到完成全齒深的齒槽加工,即完成了產品的加工。 切削過程的狀態如圖 3 所示(shì)。
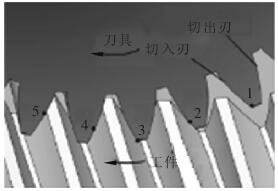
圖 3 剮削過(guò)程示意圖
2 、剮齒加工的主要問題
(1)按常(cháng)規(guī)齒輪刀具的設計方式設計(jì)出(chū)來的刀(dāo)具 ,在采用剮(guǎ)齒加工工藝方法時,在可選範圍內不論怎麽改變軸交角,加工過程振動、噪聲均較大,齒麵效果不好,齒麵有明顯的擠壓(yā)印痕,以及由工件軸與刀具軸同步(bù)波動而產(chǎn)生的齒向波動誤差, 加工出的產品如圖 4 所示(shì),產品齒麵有由於擠壓而產生的(de)凹凸現象(xiàng),明顯不可接受。
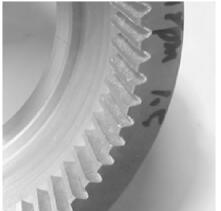
圖 4 加工完成(chéng)後的產品圖
(2)加工後的刀具的齒頂及側刃有燒損(圖 5)。 剮削加(jiā)工(gōng)過程刀(dāo)具在(zài)軸(zhóu)向進給方向的切(qiē)入(rù),在齒頂(dǐng)其前角為 γ,而在切入和切出的齒廓部分均小於 γ,越(yuè)接近齒(chǐ)根其值越,若(ruò)優化切削狀態(tài),提升加工質量則需在刀具上進行改進設計。
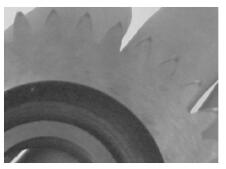
圖 5 切削加工後刀具正麵圖
3 、單側刃剮齒刀的設計
運用(yòng)新的加工工藝方法,其加工方法的變更(gèng),就(jiù)必須配(pèi)以加工工藝相(xiàng)關方(fāng)麵的變更。為解(jiě)決剮齒加工中出現的(de)問題,我們開(kāi)發設計(jì)了專有的剮齒刀具,以保證加工狀態的正常。如圖 6 剮齒刀外形結構圖, 單(dān)側刃剮齒(chǐ)刀具設計成(chéng)與產品具有共軛齒形的刀齒盤,刀具的法向模數與(yǔ)工件的法向模數相同,這些方麵均與前述(shù)的(de)剮齒加工方式保持(chí)一(yī)致, 特別的就是在刀齒的前刀麵進行了專有的改進,設計(jì)了剮(guǎ)齒刀的刀齒側刃前角。
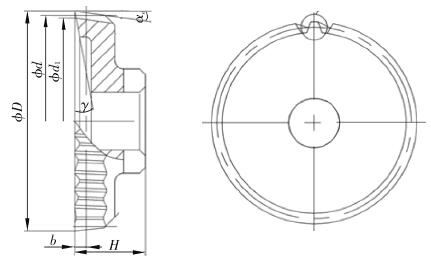
圖6 剮(guǎ)齒刀外形結構圖
(1)如圖 7所示,單側刃(rèn)剮齒(chǐ)刀的每個刀齒均有與產品要(yào)求相適用的參數,如模數、壓力(lì)角、螺旋(xuán)角等,同時,每個刀齒均有齒頂前角 γ,齒(chǐ)頂後角 αe,側刃後角(jiǎo) αc,分度圓螺旋角 β 等(děng) ,單側刃剮齒刀的每個刀齒上有專(zhuān)門設計製造(zào)的(de)側刃前角 γsc,其的大小範圍在(zài) 1°~15°;
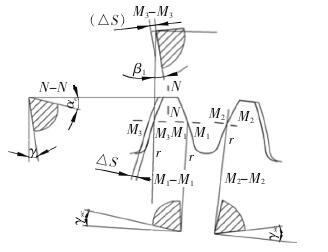
圖 7 單側刃剮齒刀主要切削角
(2)由於該側刃前角的出現 ,增大(dà)切削前角 ,大幅優化(huà)了加工狀(zhuàng)態,但由於 γsc的出現,也會影響切(qiē)削產品的壓力角,因此,要(yào)對刀具的齒形壓力角進行修正, 修正齒形角是為了在保證剮齒刀各切削角度(dù)的同(tóng)時, 確保加工出的(de)產品齒形麵具(jù)有與產品要求一(yī)致的齒形(xíng)角而進行(háng)的修正, 具體修正值可由下式計算得出(chū):
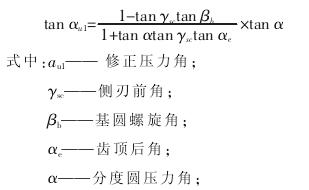
(3)由於頂刃前角的存在(zài)也(yě)同樣會(huì)影(yǐng)響齒形角 ,其(qí)修正值可按下式計算(suàn)得出;
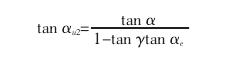
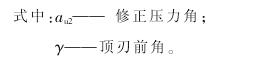
當同時存在頂刃前角和(hé)側刃前角的情(qíng)況下, 修正齒形角 αu為由(yóu)於頂刃前(qián)角和側(cè)刃前角引起的修(xiū)正量的(de)代數和。
(4)由於在剮齒加工過程中,刀具每(měi)一齒牙的左(zuǒ)右麵均參與加(jiā)工,確定側刃(rèn)前角 γsc後,由於(yú)切削前角的出現雖(suī)然可以在切入(rù)側保證理想的加工前角, 但在刀具齒牙的切出側則出現了更大的(de)切削負前角,會嚴重影響加(jiā)工狀態,而產生擠(jǐ)壓和振刀。 為此,在單(dān)側(cè)刃剮齒刀每個刀齒的(de) γsc的傾斜方向上,在相鄰的刀齒上(shàng)是相對分(fèn)布,並在加工的負前角一側的齒廓(kuò)上進行修整,設該修整量的大小為 ΔS,刀齒漸開線(xiàn)上任一點 y 的修整量 ΔSy是在過 y 點的圓上的切線方(fāng)向(xiàng)測量,ΔS 的修整麵與 γsc對應分布,刀齒分度圓上的齒厚為 S:
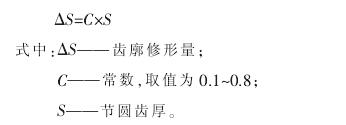
由於(yú)單側刃刀具的設計, 使得產品的加工每一個齒的兩個(gè)麵是由刀具的不同刀齒的兩個齒廓刃加工出來的, 單側刃剮(guǎ)刀的設計要求(qiú),奇數齒的產品用偶數齒的刀具加工,偶數(shù)齒的產品用奇數齒的(de)刀具加工。如果是(shì)奇數齒刀具,則其中一個刀齒上取削與之相對應(yīng)的 γsc。
4 、剮齒加工(gōng)試驗
(1) 選擇一內斜齒輪加工為具體實(shí)例, 工件參數如表 1 所示。
表 1 試加工(gōng)產品參數

(2) 根據產品參數和結構進(jìn)行刀具參數的計算與選擇 (圖8),目標產品為內(nèi)斜齒 ,根據(jù)單麵剮齒刀設計原則及插齒(chǐ)刀設計的(de)相關原則,選用 34 齒(chǐ)的刀具。
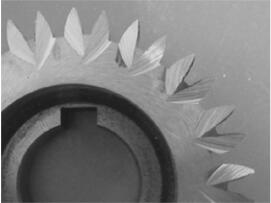
圖 8 單側刃剮(guǎ)齒刀
目標產品的齒(chǐ)向螺旋角為 13°,並(bìng)且(qiě)有大於 5.2 mm 的退刀空間,在(zài)滿足(zú)產品加工(gōng)的前提下方(fāng)便製造,刀具的螺旋角選為 0°。變位係(xì)數選為(wéi) 0.2,試製產品加工刀具參數如表 2 所(suǒ)示。
表(biǎo) 2 試製產品刀具參數表
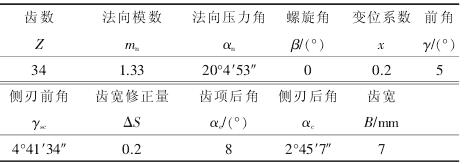
根據側刃前角計算方法,計算得出刀具刀齒側(cè)刃前角為 4°41′34″。 修正後的齒形角為(wéi) 20°4′53″。 確定齒寬修正量為(wéi) 0.20mm。 根(gēn)據加工參數 , 確定加工過程第二行程起(qǐ)最(zuì)大徑(jìng)向進刀量 0.5 mm。 刀具精度等級(jí):AA 級。
(3) 機(jī)床調整參數 : 軸交角為 13° ; 切削行程 (Z 軸軸向(xiàng)進給總行程)為 13.6 mm;工件軸轉速為 1 915.419 8 rpm;刀具軸(跟隨軸)轉速為 4 000 rpm;工件軸角度附加為 3°34′51″;Z 軸軸(zhóu)向進給速(sù)度為(wéi) 100 mm/min; 精切工件軸轉速為 3 016.846 6 rpm;精切 刀 具 軸 轉 速 為 6 300 rpm; 精(jīng) 切 軸 向 進 給 速 度 為 75 mm/min;實際切削時間為 43.52 s。
產(chǎn)品試加工結果(guǒ)如圖 9 所示, 加工的(de)內齒輪精度達到 5 級精度,齒麵效果良(liáng)好,刀(dāo)具加工壽(shòu)命長,加工效率是目前(qián)數控插齒機的(de) 11 倍。
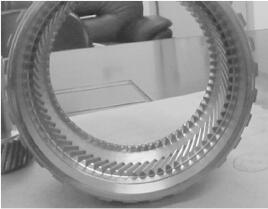
圖 9 加工後的產品圖
5 、結論
在剮齒加工過程中(zhōng),由於加工參數和刀具角度的設計,很(hěn)容(róng)易在(zài)產品與刀具產生嚴重的擠壓現象;運用單側刃剮(guǎ)齒刀具,可以改良(liáng)剮(guǎ)齒加工的切削狀態, 具有適合於剮齒切削狀態的前角γ 和側(cè)刃前角 γsc,大幅減小了剮齒加(jiā)工中的擠壓成份 ,降低了對刀具材料和(hé)機床剛性的(de)要求,提(tí)升(shēng)切削精度與效率,同時簡化了刀具的加工製造,提升了剮齒刀(dāo)具壽命的同時,為剮齒(chǐ)刀(dāo)具的刃磨提供了非常方便簡捷的方式。
投稿箱(xiāng):
如果您有機床行業、企業相關新聞(wén)稿件發表,或進行資訊合作,歡迎(yíng)聯(lián)係本網編輯部, 郵箱:skjcsc@vip.sina.com
如果您有機床行業、企業相關新聞(wén)稿件發表,或進行資訊合作,歡迎(yíng)聯(lián)係本網編輯部, 郵箱:skjcsc@vip.sina.com
更(gèng)多相關信息
業界視點
| 更多
行業數(shù)據
| 更多
- 2024年11月 金屬切削(xuē)機床產量數據
- 2024年11月 分地(dì)區金屬切削機床產量數據
- 2024年11月 軸承出口情況
- 2024年11月 基本型乘用車(轎車)產量(liàng)數據
- 2024年(nián)11月 新能源汽車產量數據
- 2024年11月 新能源(yuán)汽車銷量情況
- 2024年10月 新能源汽車產量數據
- 2024年10月(yuè) 軸承出口情況
- 2024年10月 分地區金屬切削機床(chuáng)產量數據(jù)
- 2024年10月 金屬切削機床產量數據
- 2024年9月 新能源汽車銷量情況
- 2024年(nián)8月 新能源汽車產量數據
- 2028年8月(yuè) 基本型乘用車(轎車)產量數據