大型齒輪加工精度受齒(chǐ)坯自重(chóng)變形影響的研究
2019-5-23 來源: 武漢大學動力與機械學院 江鈴汽車 作者:肖華 曹(cáo)安全 陶(táo)毅 劉青嶽 徐科揚
摘要: 大型(xíng)重載(zǎi)開(kāi)式圓柱齒輪( 簡稱(chēng)大齒輪) 廣泛應用於礦山(shān)機械、冶金機械各種(zhǒng)大型機床中(zhōng),尺(chǐ)寸大且加工精度要求高,加工過程中齒坯的自重變形會對齒輪精度產生一定的影響,但目前相(xiàng)關研究(jiū)較少。
先從(cóng)理(lǐ)論(lùn)上分析齒坯(pī)自重(chóng)導致的徑(jìng)向(xiàng)變形和周(zhōu)向變形對齒輪精(jīng)度的直接影響; 然後,從滾齒切削力入手,分析自重變形對齒輪(lún)加工精度的間接影響;最後,結合有限元(yuán)仿(fǎng)真,對比分(fèn)析(xī)在相同工藝方案下 7 個不同規格大齒輪的加工誤(wù)差,驗證了理論分析的合理性。
關鍵詞: 大齒輪; 自重變形; 加工精度
0 引言
在(zài)礦山機械、冶金機械及各種(zhǒng)大型機床中,大齒輪被廣泛用作傳動機構。較於其他齒輪,大齒輪一般(bān)具有以下特點(diǎn): 重量大(dà)、開式傳動、轉速低(dī)、傳動功率大、傳(chuán)動比(bǐ)大及工作壽命長。低精(jīng)度的大齒輪會造成設備(bèi)異常振動、噪聲及齒麵過早磨損(sǔn),導致齒(chǐ)輪損壞,傳動副(fù)失效,設備損壞甚至無法(fǎ)運,所以齒輪製造精度往(wǎng)往直接影響設備的運轉狀況及使(shǐ)用壽命,因此,在加工中(zhōng)要求盡可能地提高齒輪加工精度(dù)。
對大齒輪加工精度的影響,就加工過程中的應力變形、熱(rè)變形、切削力、進給量及振動等因(yīn)素已有較為深入的研究,但齒坯自重變形對加工精度影響的(de)研究還比較少。
1 、齒坯變形對大齒(chǐ)輪精度的直接影響
齒坯自重變形對(duì)加工精度的影響主要發生在最終的滾齒階段,由於支撐均布在齒坯(pī)外圈,在重力作(zuò)用下,齒坯內圈和支撐兩側會下垂,支撐麵處由於兩側下垂會有一定的凸起,齒坯自重變形如圖 1 所(suǒ)示。
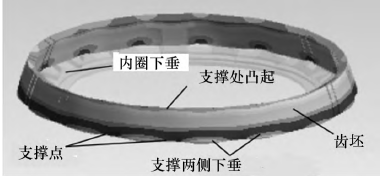
圖 1 齒(chǐ)坯自重變(biàn)形
以支撐麵中線與齒坯外圓的交(jiāo)點為原(yuán)點,以外圓(yuán)切(qiē)線方向為 X 軸,徑向並指向圓心為 Y 軸,向上為 Z軸(zhóu),建立右手坐標係,齒坯變形分析坐標係如圖 2所(suǒ)示。
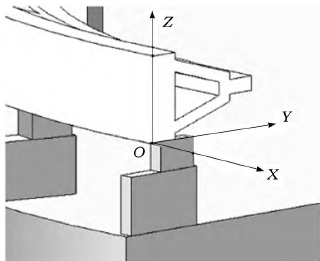
圖 2 齒坯變形分(fèn)析坐(zuò)標係
1. 1 齒坯徑向變形對加工精度的影響(xiǎng)
先隻考慮齒坯內圈下垂(chuí)變形對齒形加工精度影響,不(bú)考慮支撐兩側下垂以及支撐處凸(tū)起變形,不考慮其他影響因(yīn)素。
由於齒坯內圈下垂,齒(chǐ)坯外圈會向(xiàng)內側傾斜,滾齒加工時會產生錐齒現象。齒坯徑向變形如圖 3 所示,在 yz平(píng)麵內,虛線為(wéi)理論齒坯形狀,實線為實際齒坯截(jié)麵形狀。
設齒坯外緣 OA1與 Z 軸夾角為 α,滾刀按預(yù)定軌跡 T1T2T3進行滾齒切削,OABC 為理(lǐ)論齒形,OA1B1C 為 實際加工出來的齒(chǐ)形。
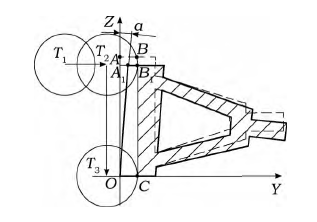
圖 3 齒坯徑向變形
由於坯自重變形為彈性變形,在實際安裝使用過程中可以自動恢複。以齒坯位置為參考,齒坯變形角α 相當(dāng)於滾刀進給(gěi)路徑反向偏轉(zhuǎn) α 角,以齒(chǐ)坯為參考的徑向變形如圖 4 所示,刀具路徑為 T11T21T31,T21T31與 Z 軸夾角為 α,OA1B1C 為實際加工齒(chǐ)形。
該(gāi)變形在齒輪圓周方向基本沒有差異,不影響齒輪齒頂圓的加工尺寸,主要影響其齒形誤差。加工時在上端麵處對刀,徑向進給量以上端麵齒頂圓為準(zhǔn),由於上端麵(miàn)處齒(chǐ)頂圓最小,所以滾(gǔn)齒時會有少量過切,且(qiě)過切量沿著齒長方向增加,並在下端麵處達到(dào)最大值。齒形整體向內移動,輪齒變(biàn)薄,移動距(jù)離為過切量,最大(dà)過切量即上下兩端麵齒頂圓半(bàn)徑之差。
變形齒(chǐ)坯加工出來的(de)端麵齒形如圖 5 所示,圖 5a 為(wéi)上端麵處齒形,是理想齒形; 圖 5b
為下端麵處齒形,實線(xiàn)為實際(jì)齒形; 虛線為理論(lùn)齒形; 細實線為實際加工齒形的理論齒頂線。
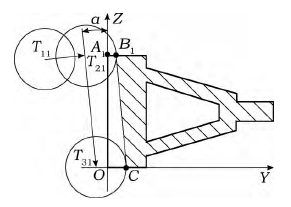
圖 4 以齒(chǐ)坯為參考的(de)徑向變形
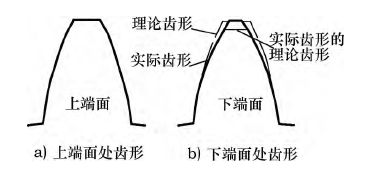
圖 5 變形齒坯加工(gōng)出來的端麵齒形
上端麵齒頂圓與下端麵齒頂(dǐng)圓半徑之差為:ΔR = OA1sinα
當齒形加工完成,由於輪齒上端麵為標準齒形,而齒厚(hòu)沿齒(chǐ)長方向逐漸(jiàn)變薄,導(dǎo)致同一輪(lún)齒的齒厚不均勻,輪齒齒厚不均(jun1)勻(yún)如圖(tú) 6 所示,以及齒側間(jiān)隙不(bú)均勻(yún),進而(ér)影響齒輪的使用壽命和傳動精度。
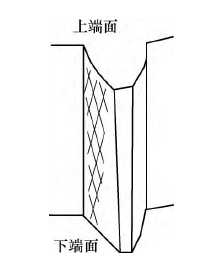
圖6 輪齒齒厚不(bú)均勻
1. 2 齒坯周向變形對加工精度的影響
在 XZ 平麵內,支撐點(diǎn) O 處(chù)向上凸起,兩(liǎng)側下垂,齒坯呈波浪形,設齒坯外緣邊線切線與 X 軸(zhóu)最大夾角為 β,滾(gǔn)齒加工時滾刀沿 - Z 軸方向運動,齒坯周變形如圖 7 所示。考慮支撐中(zhōng)間凸(tū)起對加工精度的影(yǐng)響,忽略其他因素(sù),由於大齒輪直徑較大,隻考慮局部少(shǎo)數幾個齒時(shí)可(kě)以(yǐ)將之近似作為齒條分析。支撐兩側下垂變形的影響與支撐處凸起變形影響相反。
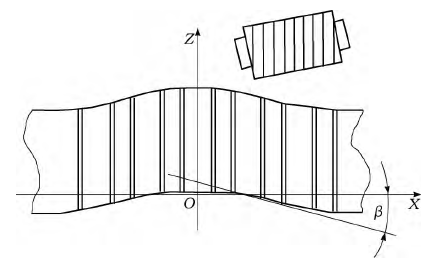
圖 7 齒坯周變形
由於大齒輪自重變形為彈性變形,在實際(jì)安(ān)裝使用時,波浪形齒輪端麵會恢複成平麵。以齒坯為參考,滾刀豎直運動加工傾斜 β 角的齒坯相當於(yú)滾刀軸和滾刀路徑反向旋轉 β 角(jiǎo),以齒(chǐ)坯為參考的周向變形如圖 8 所示,圖 8 中實線為實際(jì)加工齒形,虛線為理論(lùn)齒形。
由於滾刀相對於理論位置傾斜了 β 角,所以滾切出來的輪齒(chǐ)為(wéi)斜齒,且 Z 軸兩側輪齒(chǐ)的傾斜方向相反。斜齒直接會影響齒輪的齒距(jù)累積誤差,影響齒輪傳動的準確性。設理論齒寬為
B 由支撐兩側下垂變形引起的齒(chǐ)距累積誤差為:

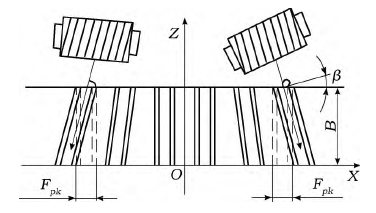
圖 8 以齒坯為參(cān)考(kǎo)的周向變形(xíng)
由於產生了斜齒,上端麵齒形與下(xià)端(duān)麵齒形在水平(píng)麵上投影不完全重合,齒側間隙變(biàn)窄,齒隙減(jiǎn)小量ΔL = Btanβ,變形對齒側間隙的影(yǐng)響如圖 9 所(suǒ)示。同時,斜齒還會(huì)導(dǎo)致傳動齧合時不能與對應齒輪完全接觸,影響載荷分布的均勻性。齒輪齧(niè)合(hé)局部(bù)斜(xié)齒接觸不良(liáng)如圖 10 所示(shì),陰影(yǐng)麵(miàn)積(jī)為(wéi)斜齒與理論(lùn)直齒輪(lún)齧合時的實際接(jiē)觸區域。齒坯的周向變(biàn)形會導致加工時產(chǎn)生相反方向的斜齒,增大齒距累積誤差,直接影響傳動精度,同時會影響齒側間隙和載荷分布均勻性,使齒輪在傳動時接觸不良過早磨損,影響齒輪傳動的平穩(wěn)性和使用壽命。
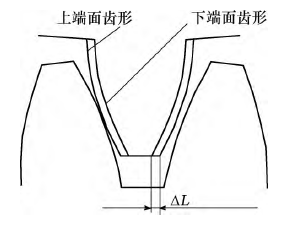
圖 9 變形對齒側間隙的影響
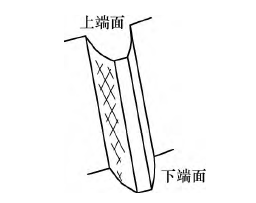
圖 10 齒輪齧合局部斜齒接觸不良(liáng)
2 、齒坯自重變形對齒形精度間接影響(xiǎng)
齒坯(pī)自(zì)重變(biàn)形(xíng)使滾刀與齒坯相對位置(zhì)發生改(gǎi)變,影響齒輪滾刀的切入(rù)角度和切削深度,進而影(yǐng)響齒輪切削過程(chéng)中切削力(lì)的大小。當切削深度增大時,切削(xuē)力也隨之增大,並且切入角度的改變對刀具的穩定(dìng)狀態也會產生一定的影響。
徑向切削力的反作用力會使滾刀刀杆產生一定的撓性變形,使得滾刀與齒坯的中心距增大。而在滾齒過程中,切(qiē)削力的變化會使變形量發生 改 變,從 而(ér) 使 滾 刀 與(yǔ) 齒 坯 的 中 心 距 發 生改變(biàn)。齒坯的徑向變形使(shǐ)整個齒坯呈錐形(xíng),進入穩定切削狀態後,滾刀從上到下切削深(shēn)度逐漸增加,切削力逐漸增大(dà)。
齒坯的周(zhōu)向變形會使得相鄰兩齒的切削力不同,在滾(gǔn)齒切入時,支撐處向上變形的部分切削力大,非支撐處向下變(biàn)形,切削力小,滾齒切出時,向(xiàng)上變形的支撐處切削力小,非支撐處切削力大,滾齒切削力會交替增大或減小。滾齒(chǐ)切(qiē)削力(lì)增大會增大滾刀刀杆的彎曲變形(xíng)量,增大滾刀與齒坯的中心距,使齒形輪廓整體向外偏移,切削力變(biàn)大的(de)齒形如(rú)圖 11 所示,實線為實際齒形,虛線為(wéi)理(lǐ)論齒形。分(fèn)度圓直徑變大,齒高變小,齒厚增加,齧合時齒側間隙變小。
滾齒切削力(lì)變小會減小滾刀刀杆的彎曲變形量,滾刀與齒坯的(de)中心(xīn)距(jù)減小,滾刀切深(shēn)增加,齒形輪廓整體向內偏移(yí),切削力變小的(de)齒形如圖(tú) 12 所示,圖 12中實線為實際齒形,虛線為理論齒形,分(fèn)度圓直(zhí)徑變小(xiǎo),輪齒變薄(báo),則齒側間隙變大。
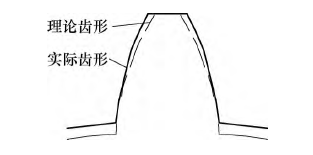
圖 11 切削(xuē)力變大的齒形
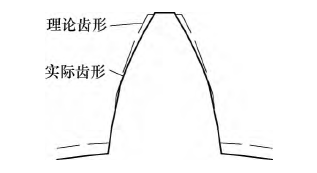
圖 12 切削(xuē)力(lì)變(biàn)小的齒形
由於切削力的增(zēng)大或減小也會沿(yán)著齒長方向改(gǎi)變,齒厚會(huì)隨之沿著齒長方向改變,增大了齒形誤差,降低(dī)了載荷分布的均勻性和傳動的平穩性以及(jí)傳動精度。由於(yú)齒坯的周向變(biàn)形呈周期性(xìng),切削力會呈現周期性波動(dòng),產生周期性誤差,影(yǐng)響切(qiē)削過程的(de)平穩性,使齒廓表麵出現波紋,增加了輪齒的表麵粗糙度,降低齒形精(jīng)度。
切削力的周(zhōu)期性變化還會導致機床的強迫振動,對(duì)滾齒加工產生較大(dà)影響。當激振頻率(lǜ)等於或者與(yǔ)機床固有頻率相接近時,將可能會引起(qǐ)機床共振,共振嚴重的時候甚至還會破壞刀具(jù)以及機床結構部件,且(qiě)在齒輪表麵(miàn)會留下振刀紋。在大型數控滾齒機對大型齒(chǐ)輪進行加工時,由切削力而引起的振動(dòng)將更為明顯。會使滾刀、工件主軸及兩主軸中心距(jù)位置產生較大振動位移,不單影響機床精度更降低齒輪(lún)的整體加工質(zhì)量,並且還會加劇(jù)刀具磨損,降低滾刀使用壽命。滾齒本身是一個斷續切削的過程,切削力會出現振動,但由於齒坯(pī)自重(chóng)變形導致(zhì)的切削力變化會(huì)進一步(bù)加強或減弱這種振動,使得齒形誤差波動更大。
3 、實驗分析
為驗證之前的(de)分(fèn)析,收集了 7 個實際加工的礦山磨(mó)機大齒輪數據,其實驗齒輪參數如表 1 所(suǒ)示(shì),材料均為 ZG45。由於齒厚(hòu)誤差可以綜(zōng)合反映齒形精度(dù)和齒側間隙,對大齒輪使用壽命影(yǐng)響較大且容易測量,所以(yǐ)實(shí)際生產中選取齒厚誤差(chà)作(zuò)為(wéi)檢驗標準。實際生產中為了提高檢測效(xiào)率,隻在齒輪各(gè)分瓣中間以及分瓣結合處取 12 個齒測量(liàng)輪齒中部實際加工齒(chǐ)厚,選取3 個任意圓,用齒厚卡尺測量相應(yīng)齒高的弦齒厚。
表 1 實驗齒輪參數
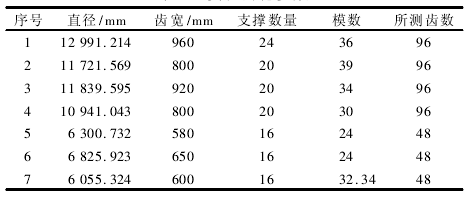
注: 32. 34 為國外標準換算,故有兩位小數
3. 1 齒厚誤差與齒坯外圈最大變形量之間的關(guān)係(xì)
由(yóu)於齒坯外圈變(biàn)形量在實(shí)際加工中難以測量,所以通過 ANSYS 軟(ruǎn)件對(duì) 7 個齒坯分別進行仿真,材料選用鑄鋼,彈性模量 EX = 2 × 1011Pa,泊 鬆比 PRXY =0. 3,得(dé)到各個齒坯外圈的最大變形量,齒坯外圈變形量仿真如圖 13 所示(shì)。
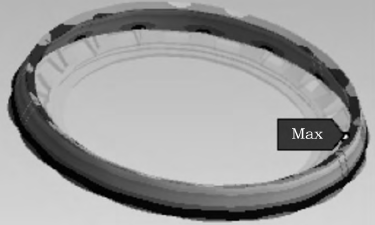
圖 13 齒坯外圈變形量仿真
最大變形量發生在相鄰(lín)兩支撐正中間內側,在徑向截麵 YZ 內。計算輪齒測量處(chù)相應的理論齒厚,用實際齒厚減去理論齒厚取絕對值,得到絕(jué)對齒(chǐ)厚誤差,再除以理論齒厚得到(dào)相對誤(wù)差。用 Matlab 軟件計算(suàn)各齒輪(lún)齒厚誤差的平(píng)均值和均方差,並計算絕對誤差的均值和均方差(chà),所得結果如表 2 所示。
為驗證齒厚誤差與齒坯自重變形的相關性,用Matlab 求出 7 個齒輪齒厚誤差(chà)與(yǔ)齒坯外圈最大變形量之(zhī)間的相關係數,如表 3 所示。
由表 3 中數據可以(yǐ)看出,絕對齒厚誤差的各項(xiàng)統計參數與(yǔ)齒(chǐ)坯外圈最(zuì)大變形量之間有一定的相關性,均方差相關(guān)係數(shù)最大,為 0. 347 6。相對誤差均值(zhí)與外(wài)圈最大變形量之間沒有明顯的相關性(xìng),但均方差有一定的相關性(xìng)。由前麵分析可知,齒坯自重變形會使部分輪齒齒厚增大,部分減小,綜合起來對齒厚平均誤差影響較小,但會影響齒厚誤差的均方差,實驗結果驗證了這一理論分析。
表 2 各齒輪外(wài)圈最大變(biàn)形量及加工誤差
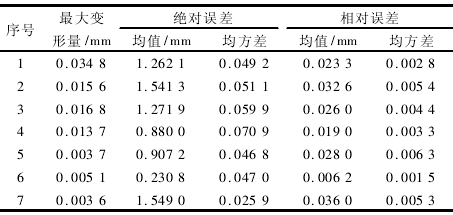
表 3 齒(chǐ)厚誤差與外圈最大變形量之(zhī)間的相(xiàng)關係數

3. 2 齒輪各處(chù)齒厚誤差(chà)與外圈變形量之間的關(guān)係
大齒輪在滾齒加工時,為了減小變形量,各瓣結(jié)合(hé)處放於兩個支撐中間,齒坯放置位置及齒(chǐ)厚測量位置如圖 14 所示。

圖 14 齒坯放置位置及齒厚測量位置
因此,對於有 20 個支撐的 2 號、3 號、4 號四瓣(bàn)齒輪,每個齒輪所測的 8 組數(shù)據各有
4 組( AB、BC、CD、DA) 位於無支撐的齒(chǐ)瓣結合處和 4 組( A、B、C、D) 位(wèi)於有支撐的(de)齒瓣中間處。
無(wú)支撐(chēng)處的(de)齒坯外圈最大(dà)變形量(liàng)相對(duì)較大,對齒厚誤差的影響可能也更大。用ANSYS 對 2
號(hào)、3 號、4 號三個齒坯分(fèn)別進行(háng)建模仿真,得到齒坯外圈支撐處和無支撐處的最大(dà)變形量。將各個齒輪所測數據(jù)分為(wéi)有支撐和沒有支撐的兩組,用 Matlab 分(fèn)別求取均值和(hé)均(jun1)方差進行比較分析( 由於3 個齒輪直徑、齒厚相近,所以(yǐ)隻考慮(lǜ)絕對誤差) 。3個齒輪有支撐和無支(zhī)撐處的外圈最大變形量以及齒厚(hòu)誤差均值與(yǔ)均方差(chà)如表 4 所示。
表 4 外圈(quān)最大變(biàn)形量與齒厚誤差(chà)
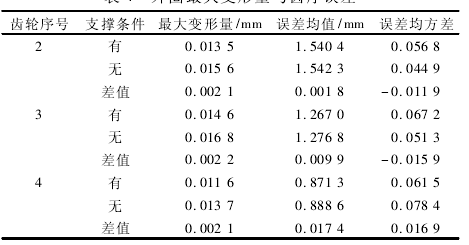
從 3 個大(dà)齒輪(lún)各處誤差數據看,齒坯無支撐處均比有(yǒu)支撐處變形量大(dà),同時變形量大的地方齒厚誤差均值整體偏(piān)大(dà)。而(ér)且對不同的大齒輪,變形量差值越大(dà),齒厚誤(wù)差均值的差值也越大。但均方差值與齒坯外圈最大變形量(liàng)之(zhī)間沒有明(míng)顯關係,可能(néng)因為齒(chǐ)坯外圈變(biàn)形量最大值一般不超過(guò) 0. 04mm,相對於齒輪直徑和齒厚都非常小,在加工(gōng)過程中機床振動、刀(dāo)具磨損、工作台誤差及溫差等因素都會影響齒(chǐ)輪的加工精度,實驗數(shù)據中齒厚誤差均(jun1)方差與齒坯變形量之(zhī)間的關係不是特別(bié)明顯。
4 、結語
加工大齒輪時,齒坯自重變形會導致錐齒和斜齒以及振動現(xiàn)象,使大齒輪輪齒沿齒長方向齒厚不(bú)均,影響(xiǎng)齒側間隙、齒距累(lèi)積誤差、齒形誤差進而影響大齒輪的傳動精度和傳動平穩(wěn)性和載荷(hé)分布的均勻性,影響大齒輪的使用(yòng)壽命。在加工過程中尤其(qí)是滾齒(chǐ)階段(duàn)應采用較多的(de)支撐減小齒(chǐ)坯自重(chóng)變形(xíng),以提高齒輪加工精度。
投(tóu)稿箱:
如果您有機床行業、企業相關新聞稿件發表,或進(jìn)行資訊(xùn)合作,歡迎聯係本網編輯(jí)部(bù), 郵箱:skjcsc@vip.sina.com
如果您有機床行業、企業相關新聞稿件發表,或進(jìn)行資訊(xùn)合作,歡迎聯係本網編輯(jí)部(bù), 郵箱:skjcsc@vip.sina.com
更多相(xiàng)關信息
業界視點
| 更多
行業數據
| 更多
- 2024年11月 金屬切削機床產量數(shù)據
- 2024年11月 分地區金屬切削機床產(chǎn)量數據
- 2024年11月 軸承出口(kǒu)情況
- 2024年11月 基本型乘用車(轎車)產量數據
- 2024年11月(yuè) 新(xīn)能源(yuán)汽車產量數據
- 2024年11月 新能源汽車銷量情(qíng)況
- 2024年10月 新能源汽車產量數據
- 2024年10月(yuè) 軸承出口情況
- 2024年10月(yuè) 分地區金屬切削機床產(chǎn)量數(shù)據
- 2024年10月 金屬切削機床產量數據
- 2024年9月 新能源汽車銷量情況
- 2024年8月 新能源汽車產量數據
- 2028年8月(yuè) 基本型乘用車(轎車)產量數據
博(bó)文選(xuǎn)萃
| 更多
- 機械加(jiā)工過程圖示
- 判斷一台加工中心(xīn)精度的幾種(zhǒng)辦法
- 中走絲線(xiàn)切割機床的發展趨勢(shì)
- 國產數控係統和數控機床何去何從(cóng)?
- 中國的技術工(gōng)人都(dōu)去哪裏了?
- 機械老板做了十多年,為何還(hái)是(shì)小作坊?
- 機械行業最新自殺性(xìng)營銷,害人害己!不倒閉(bì)才
- 製造業大逃亡
- 智能時代,少談點智造,多(duō)談點製造
- 現實(shí)麵前,國人沉默。製造業的騰飛,要從機床
- 一文搞懂數控車床加工刀具補償功能
- 車床鑽孔(kǒng)攻螺紋加工(gōng)方法及工(gōng)裝設計
- 傳統鑽削與螺旋銑孔加工工藝的區別