重型臥式車床幾何精度檢測與加工精度預估
2020-12-16 來源:天津中德應用技術大學機械工程學(xué)院 作(zuò)者:馬林旭 王麗娜
摘要: 以一(yī)台(tái)重型臥式車床為例,基於剛體(tǐ)運動學原理建立了機床幾何誤差模型,得到了各軸線幾何誤差源與(yǔ)加工誤差之間(jiān)的映射關係,而後采(cǎi)用激光幹涉儀、水平儀等(děng)測量儀器獲取了機床部分幾何誤差源的誤差數據,並進而預(yù)估出機床全工作空間內的加工誤差(chà)變化規律,可用於指導機床的誤差補(bǔ)償(cháng)等工作,以(yǐ)提高(gāo)機床的精度性能。
關鍵(jiàn)詞: 重型臥式車床; 幾何誤差建模; 誤差檢測(cè); 精度預估
重型臥式車床廣泛(fàn)應用於能源、石化、船舶、航天等領域(yù),是車削各類大型回轉類零件的重要(yào)工作母機,對國防軍工、國民經濟發展具有重要戰略(luè)意義[1]。幾何精度是重型臥式車床的重要性能指標之一[2],影(yǐng)響幾何(hé)精度的因素主要包括主軸回轉精度以及直線進給軸運動精度兩類,而直(zhí)線進給軸運動(dòng)精度是影響整機(jī)幾何精度的最重要因素。針對重型臥式車床(chuáng)幾(jǐ)何精(jīng)度檢測,諸多學者開(kāi)展了大量的研究工(gōng)作[3-8],所采用的測量方法主要包括激(jī)光跟蹤儀、激光幹涉儀、自準直儀、水平(píng)儀以及步(bù)距規等,然(rán)而對於如何利用測量數據預估加工精度,並指導誤差(chà)補償以及加工工藝規劃,尚未有係統性研究。本(běn)文以一台重型(xíng)臥式(shì)車床為例,首先建立機床幾何誤差模型,並分析(xī)不同誤差源對加工精度的影響規律,之後采用激光幹涉儀(yí)開展誤差檢測實驗,最後基於檢測數據預估機床全工作空間內的加工誤差。
1、 誤差建模(mó)與(yǔ)分析
本文研究對象為一台 SKODA SR5-420 /16m 型號的重(chóng)型臥式車床,如圖 1 所示。該重型臥式車床主要由主(zhǔ)軸箱、卡盤、刀架、尾座、床(chuáng)身與滑座構成,刀架(jià)進給方向為 x 向,滑座進給方向為 z 向。機床最大加工工(gōng)件(jiàn)直徑為 4 200 mm,最大切削長度為 16 m,最大(dà)加工工件質量為 250 t。為了描述運動部件刀架及滑座的(de)運(yùn)動誤差對刀尖點加工誤差的映射關係(xì),建立如圖 2 所示(shì)坐標係統。當刀架位於坐標零點位置時,在其所在導軌麵中心點 X0處建立與導軌固定連接(jiē)的坐標係 X0-xyz,並同時在(zài)刀架上與(yǔ) X0點重合的 X 點建立與刀架(jià)固定連接的連體坐標係 X-xyz。這樣一來,當刀架運動至坐標 x 處時,坐標係原(yuán)點 X 與 X0之間的 x 方向(xiàng)坐標差即為 x。同理,對於滑座所在的 z 軸建立類似的坐標係 Z0-xyz 與 Z-xyz。

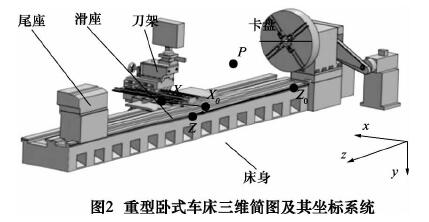
計(jì)刀尖點為點 P,利用(yòng)剛體運動學基本原理,當刀架運動至坐(zuò)標 x 處時,由刀架運(yùn)動誤差引起的刀尖點空間位置誤差 Δr刀架可以表示為:
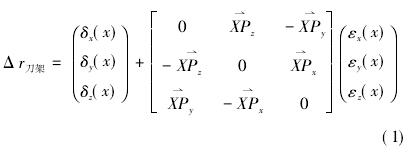
其中: δx( x) 、δy( x) 、δz( x) 與 εx( x) 、εy( x) 、εz( x) 分別表示刀架運動(dòng)過程中沿 3 個坐標方向的位置誤差與繞這 3 個(gè)坐標回轉的轉(zhuǎn)角誤差,XP→表示由(yóu)點 X 指向點 P的位置向量,腳標 x、y、z 表示向量XP→的 3 個分量。同理,當滑座運動至坐標 z 處時,由滑座(zuò)運動誤差引起的刀尖點空間位置誤差 Δ r滑座可以表示為:
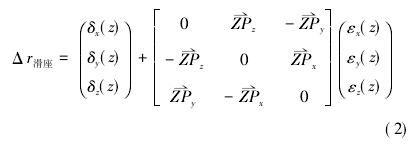
於是,同時考慮刀架與滑座的影響,刀(dāo)尖(jiān)點位置誤差 Δr 可以表示為(wéi):
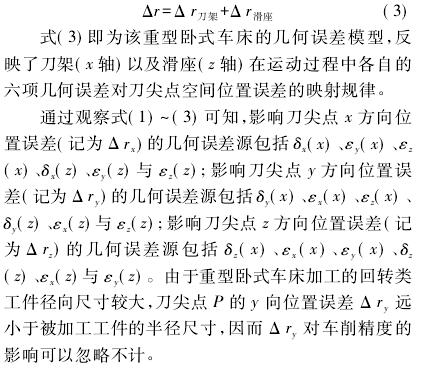
2 、幾何誤差檢測
由上節中的分析可知,Δ ry對加工精度的影響可忽(hū)略,因(yīn)而在誤(wù)差(chà)檢測與加工精度預測的過程中僅需重點關注與 Δ rx、Δ rz相關的幾何(hé)誤差源。由於對 Δ rx與 Δ rz的(de)研究方(fāng)法完全一致,本文僅針對與刀尖(jiān)點 P的 x 向位置誤(wù)差 Δ rx相關的幾何誤差源進行檢測、分析與預測。下麵將采用激光幹涉儀以及電子水平儀等手段檢測與 Δ rx相關的 6 項幾何誤差源。具體檢測方法與檢測結果如(rú)下。
2.1 刀架運動誤差檢測(cè)
三(sān)項相關的幾何誤差源均采用激光幹涉(shè)儀進行誤差(chà)檢測。x 軸測(cè)量行程為 2 000 mm,每間隔(gé) 200 mm 測量(liàng)一次,測量點位數目為 11 個。測量過程中 x 軸進(jìn)給速度為8 m / min,每個測點停留時間(jiān)為 5 s,越(yuè)程量(liàng)為 5 mm,具體測量流程參照 GBT 16462.7-2009 中所述方法。針對每(měi)一項誤差源,一共往(wǎng)返測量 3 次,獲取 6 組誤差(chà)數據。利用激光幹涉(shè)儀轉角誤差檢測鏡組檢測 x 軸運動部件( 刀架) 繞 y 偏(piān)轉轉角誤差 εy( x) 的現場(chǎng)照片如圖3 所示。誤差源 δx( x) 、εy( x) 與 εz( x) 的檢測結果分別如圖(tú) 4 ~ 6 所示。依據 GBXXX 所提供的數據評價方法,定位誤差 δx( x) 偏(piān)轉的定位精度為 0.796 mm,重複定位精度為(wéi) 0.005 mm; 轉角誤差 εy( x) 的精(jīng)度為 0.019mm / m,重複精度為(wéi) 0.012 mm / m; 顛轉轉角誤差 εz( x)的精度為 0.282 mm /m,重(chóng)複精度為 0.013 mm /m。2.2 滑座運動誤差檢測直線度誤差 δx( z) 以及偏轉轉角誤差(chà) εy( z) 采用激光幹涉儀進行檢測,傾轉轉角誤差 εz( z) 由於旋轉(zhuǎn)方向繞其軸線,用(yòng)激光幹涉儀誤差檢測,故采用電子水(shuǐ)平儀進行檢測。z 軸測量行程為 17 000 mm,每間隔 500mm 測量一次,測量點位數(shù)目(mù)為 35 個。測量過程中 z軸進給速度為 8 m/min,每個(gè)測點停留時(shí)間為 5 s,越程(chéng)量為 5 mm。針對(duì)每一項誤差源,一共往(wǎng)返測量 3次,獲取 6 組誤差數據。
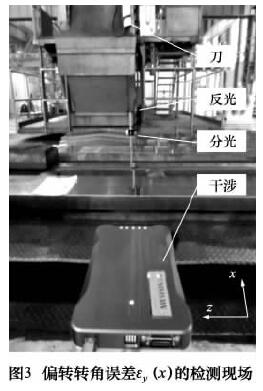
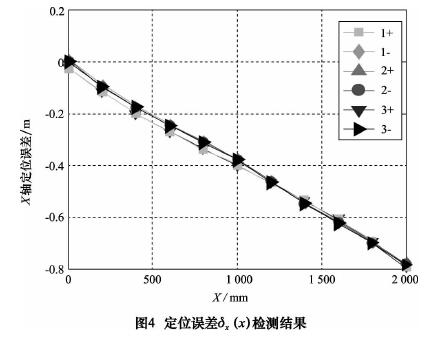
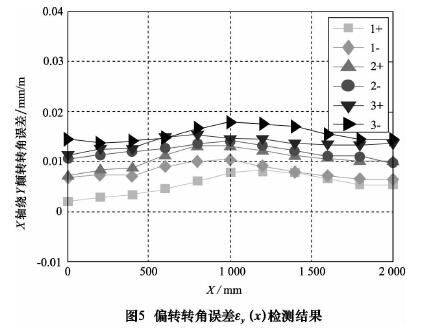
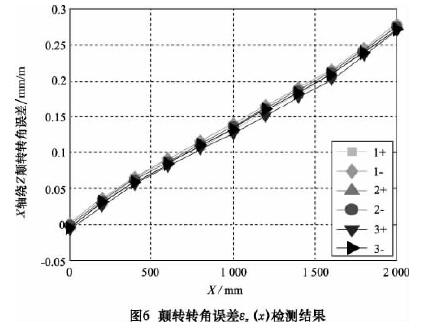
利(lì)用激(jī)光幹涉儀直線度誤差檢(jiǎn)測鏡組檢測 z 軸運動部件( 滑座) 沿 x 方向直線度誤差 δx( z) 的現場照片如圖 7 所示。誤差源 δx( z) 、εy( z) 與 εz( z) 的檢測結果分別如圖 8 ~ 10 所示。直線度誤差 δx( z) 的精度為0.054 mm,重複定位精度為 0.018 mm; 偏轉轉角誤差(chà)εy( z) 的精度為(wéi) 0.067 mm /m,重複精度為(wéi) 0.018 mm /m; 傾轉轉角誤差 εz( z) 的精(jīng)度為 0.042 mm /m,重複精度為 0.007 mm/m。
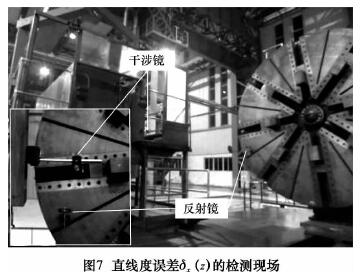
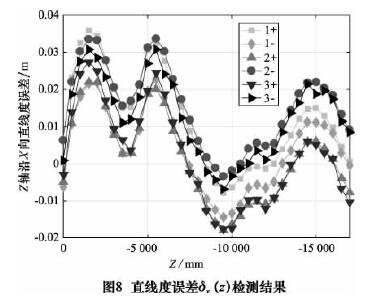
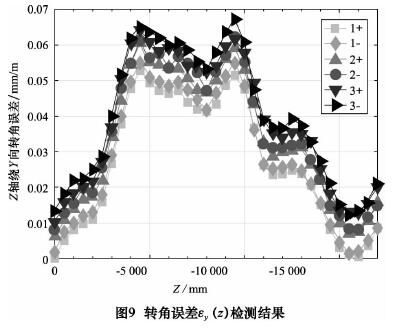
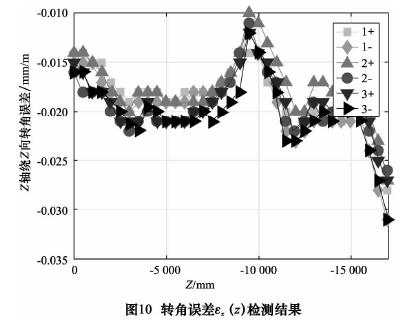

3 、加(jiā)工精度預測
重型臥式車床的工作空間為由 x 軸(zhóu)和 z 軸構成的經過(guò)主軸(zhóu)旋(xuán)轉軸線的矩形平麵區域。依據車床幾何誤差模型式( 3) ,將第 2 節(jiē)中(zhōng)檢測得到的(de) 6 項幾何誤差源數據代(dài)入(rù)到(dào)誤差模型中,即可預估(gū)出刀尖點的 x 向(xiàng)位置誤差在全部(bù)工作空間中的變化情況(kuàng),具體結果如圖 11 所(suǒ)示。可以看出隨著 x 坐標的增大,即刀尖點遠離主軸旋轉軸線,刀尖點(diǎn)誤差 Δ rx呈逐漸增大的趨(qū)勢; 隨著 z 坐標的變化,Δ rx呈波浪形(xíng)變化,無明顯規律。全工作空間中,Δ rx的平均值為(wéi) 0.246 mm,最大(dà)值為 0.479 mm。刀尖(jiān)點 z 向位置誤差Δ rz也可利用相同的方法獲得。基於上述(shù)結果,我們可以獲取車床運動至工作(zuò)空間任意一點處的加工誤差,並基(jī)於此修正加工程序,抵消機床誤差對加工精度的不利影響。
4 、結語
本文以一台重型臥式車床為例,為了提高其加(jiā)工精度,基於剛體運動學原理建立(lì)了機床幾何誤差模型,得(dé)到了各(gè)軸線(xiàn)幾何誤差源與加工(gōng)誤差之間的映(yìng)射關(guān)係,而後采用(yòng)激光(guāng)幹涉儀、水平儀等測量儀(yí)器獲(huò)取了機床(chuáng)部分(fèn)幾何誤差源的誤差數據,並進而預(yù)估(gū)出機(jī)床全工作空間內的加工誤差變化規律,可用於指導機床的誤差補償等(děng)工作,以提高機床的精度性能。
投稿箱:
如(rú)果您有機(jī)床行業、企業相關新(xīn)聞稿件發表,或進行資訊合作,歡(huān)迎聯係(xì)本(běn)網編輯部, 郵箱:skjcsc@vip.sina.com
如(rú)果您有機(jī)床行業、企業相關新(xīn)聞稿件發表,或進行資訊合作,歡(huān)迎聯係(xì)本(běn)網編輯部, 郵箱:skjcsc@vip.sina.com
更多相關信息
業界視點
| 更多
行業數據
| 更多
- 2024年11月 金屬切削機床產量數據
- 2024年11月 分地區金屬切削機床產量(liàng)數據
- 2024年11月 軸承出口情況
- 2024年11月 基本型乘用車(轎車)產量數據
- 2024年11月 新能源汽(qì)車產量數據
- 2024年11月 新能源汽車銷量情(qíng)況
- 2024年10月(yuè) 新(xīn)能源汽車產量數(shù)據
- 2024年10月 軸承出口情況
- 2024年10月 分地區金屬切削機床產量數據
- 2024年10月 金屬切削(xuē)機床產量數據
- 2024年9月(yuè) 新(xīn)能源汽車銷量情況
- 2024年8月 新能源汽車產量數據(jù)
- 2028年8月 基(jī)本型乘用車(轎車)產量數據