0前言(yán)
薄板衝壓(yā)成(chéng)形是汽車和航空(kōng)航天等行業十分重要的製造技術,其中汽車車身中的金屬零件幾乎100%為薄板衝(chōng)壓件,因此(cǐ)汽車車身(shēn)的改型換代一直受到(dào)薄板衝壓成形技術的(de)影響和製約。由於薄板衝壓成形是一個十分複雜的力學過程,衝壓工藝與模具的設計一直(zhí)是很難的工程問題,常常導致模具製造和調(diào)試周期長、花費高,嚴重影響汽車新產品的開發進(jìn)程(chéng)。衝壓成形模具的設計製造一(yī)般流程如圖(tú)1所示。
對一個典型的汽車(chē)覆蓋件的拉延工序來說,在最大並(bìng)行化(huà)流程中,各階段的相對(duì)時間可估算(suàn)如下:工藝(yì)分析與(yǔ)設計2天,模具設計5天,毛坯製造02天,機械加工 01天,組裝與調試10天以上。在上述時間估算中,毛坯製造含製作泡(pào)模時(shí)間約1周,鑄造時間(jiān)約2周,組裝與(yǔ)調(diào)試時間理論上沒有上限,即如果工藝設計失敗,調試就會耗時(shí)很長,甚至無(wú)法(fǎ)成功。由此可知要縮短模具的設計製造總周期,縮短毛坯製造時(shí)間和調試時間是十分重要的。
要縮短調試時間關鍵是把好工(gōng)藝設計關, 工藝設計合理,調試(shì)時間就可以控製, 否則就難以控製。隨著CAE技術的不(bú)斷成(chéng)熟,通過(guò)應用CAE技術優化工藝方案(àn)和工藝參數是縮短調(diào)試時間的有效途徑。要縮短毛坯製造時間,有多種方法可以采用(yòng)。對新產品研製來說(shuō),采用低熔點合金鑄造或快(kuài)速原(yuán)型技術(shù)等方法是行之有效的。對(duì)中(zhōng)小批量生產來說,不少企業采用鋼板組焊模,並取得(dé)了高速(sù)度(dù)和低成本的良好綜合效果。調查研究表明,鋼(gāng)板組焊模不僅已在實踐(jiàn)中表現出高速度和低成本的優點,而(ér)且也具備高品(pǐn)質(zhì)的潛(qián)力,其中關鍵是要提高鋼板組焊模設計製造中的技術含量。在國家科技部"十五"重點科技攻關課題支持下,開展了這方麵技(jì)術的係統研究(jiū), 並提出了一套大型覆蓋件衝壓模(mó)具(jù)毛坯快速製 造的新技術。這裏將重點討(tǎo)論(lùn)模(mó)具毛坯快(kuài)速製造中的關鍵技術, 即(jí)毛坯型麵(miàn)的快速成形技術與裝備。
1基(jī)於離散型麵(miàn)模的毛坯曲麵構件(jiàn)快速成形技(jì)術與(yǔ)裝置
通(tōng)過對大型(xíng)覆蓋件衝壓成(chéng)形模具的係統分析,人們不難發現其毛坯可分成平麵構件和曲麵構件兩大類,如圖2所示。其(qí)中平麵構(gòu)件(jiàn)可(kě)用厚鋼板切割組焊(hàn)而成,而(ér)曲麵構件則需經過較複雜的(de)加工方可製得。現在企業中常使用的方法包括兩類,即壓力機輔助的手工冷彎和手工熱彎。
手工冷彎適合(hé)厚度較小的鋼板,如板厚小十(shí)03Inln,而熱彎適合於厚度大於03mm的鋼板,目前(qián)的問題在(zài)於無論是熱彎(wān)還是冷彎都憑工(gōng)人(rén)的技巧來獲取給定的構件曲麵形狀,誤差很大,有時可大到一(yī)個板厚,使毛坯在加工時被完全銑穿,從而使毛坯報廢。為解決這一問(wèn)題,開發了一套離散型麵模係統,如圖3所示。
該係統包括如圖3所示的上、下模總成,其中上(shàng)、下模又分別由模座(zuò)和(hé)頂杆組成。頂杆一端為平頭與模(mó)座用螺栓連接(jiē),而另一端為球(qiú)頭,且高度通過中間螺(luó)紋聯接可以調整。上、下模頂杆根據欲成形的曲麵構件形狀調節成一定(dìng)的高度分布,其球(qiú)頭包絡麵便形成上下離散型麵模腔。將調節好的模座裝在壓力機上便可方便(biàn)地成形(xíng)任意複雜的曲麵構件。這一過程本質(zhì)上與多點無模成形是一致的,但由於其(qí)特殊用途,因此(cǐ)又有其獨特的性能和設計要(yào)求。首先(xiān)它專為模具毛(máo)坯曲麵構件的(de)製造而設計,具有(yǒu)較(jiào)小型麵離散分(fèn)辨率和特定的頂杆(gǎn)變化高度,且上下(xià)模離散麵的對應關係非常密切,因此稱(chēng)其為離散型麵模成(chéng)形比多(duō)點無模成形更為貼切(qiē)。其次,上(shàng)下模頂(dǐng)杆的相互對應關係對厚板成形的精度和穩定性有重要影響,對不同的曲麵(miàn)構件應有(yǒu)不同的設計。第三,為減(jiǎn)小回彈量,這一成形過程(chéng)婦采用熱成形過程,一次成形多個曲麵構件。同時這種結構簡單可靠,成本遠低於通用的多點無模成形設(shè)備。
下麵對上述設備成形的基本性能作一簡要分析(xī)。
1.1最大理論成形梯度
在下模座(zuò)上定(dìng)義(yì)如(rú)圖4所示的坐標係(xì),這裏成形梯度指成形麵在成形方向即z方向的位移隨x和(hé)y坐標的變化率,即
式中u-成形麵的位移,Tx,Ty-x和y方向的(de)成形梯度
本(běn)裝置的最大成(chéng)形梯(tī)度Txmax和(hé)Tymax與頂杆(gǎn)球頭半徑和最大調節(jiē)高度(dù)有(yǒu)關,即Txmax=Tymax=0.5h/r式中h一-一最大調(diào)節高度 r一一-球頭半徑若型麵的成形梯(tī)度大於上述(shù)值,則不能直接(jiē)成形,而要分塊成形。
1.2理論成形板厚的影響因(yīn)素分析
最(zuì)大理論成形板厚(hòu)一般不受設備幾何尺寸的限製,而是受其力學特(tè)性的限製,並與成形梯度有關。如圖5所示,成形梯度越(yuè)大,對頂杆的彎曲力矩(jǔ)越大,為了不使彎矩(jǔ)過大(dà),應盡量(liàng)使板厚減小。精確的理論(lùn)成形板厚計算一般要用到有限(xiàn)元方法。但實踐表明,對30mrn至50rDIn厚的(de)板加熱到800℃左右後,上述裝置在,30mm的條件下,可完成梯度達2.0的成形。
1. 3 最小成形(xíng)曲率半徑
假設不計成形中板厚的變化,最(zuì)小成形(xíng)曲率半(bàn)徑(jìng)對厚度小於r的板料可取頂杆(gǎn)球頭的半徑,如圖6所示。當板厚(hòu)大於;時,曲率半徑會(huì)變大。由於受很強的局部熱變形影響(xiǎng),變大的具體(tǐ)數值一般要(yào)通過(guò)有限元法方(fāng)能(néng)定量(liàng)計算。
以下分別(bié)討論如何基於這一專用設備對給定(dìng)的複雜(zá)模具(jù)型麵進(jìn)行分塊並(bìng)製造出(chū)相(xiàng)應(yīng)的分塊構件。
2 任意(yì)複雜型麵的毛坯模塊(kuài)化
上節提到離散型麵模所能提供的(de)成形梯(tī)度受到一(yī)定的限製。同時,一次成形的型麵總尺寸和總成形深度也受設備(bèi)幾何尺寸的限製。因此對於大型覆蓋件模具而言,不可能用一塊整板通過成形來(lái)製造其型腔毛坯表層結(jié)構,而(ér)隻能通過合理分塊來實現離散型麵(miàn)模的成形。合理分塊的原則如下:a使總的分塊數量最少,分塊數量(liàng)越少,表麵焊縫越少,便於型麵的數控加工,也便於減少毛坯變形。b使每塊的成形梯度盡可(kě)能小,並小於最大成形梯(tī)度式枷又和界栩(xǔ)囂。»使分塊邊界線遠離型麵重要(yào)工作部分,如局部(bù)凸起部分,並使分塊邊界線盡量呈對稱分布。
基於上述原則(zé),可提出一般情況(kuàng)下拉延模型麵(miàn)的分塊方案。無論汽車覆蓋件具體(tǐ)形(xíng)狀多麽複雜,都可以(yǐ)用圖7來(lái)表示其拉延成形模具的型腔構成。
圖中ABCD表示的是(shì)凹模的型(xíng)麵輪廓,其中B、C、D和E表(biǎo)示可能的分塊邊界線位置。C點和D點都為凹模的凹部,為次要成(chéng)形麵,故(gù)可考慮為焊縫所(suǒ)在處,B點和E點為拉延筋位置,如有必要也可選為焊縫所在處。對壓邊圈而(ér)言,問題比較簡單,因為它(tā)一方麵型麵較(jiào)小,另一方麵也不含有太大的(de)成形梯(tī)度。對凸模來說,其型麵(miàn)輪廓IJKL在J 處和(hé)K處分塊,一般都能滿足成形方麵的綜合要求。
如果焊縫處為次要成(chéng)形麵,且焊縫設計合(hé)理(lǐ)的(de)話,有(yǒu)可能完全避免對焊縫的數控加工和打磨,從而提高加工效率。用於型腔表層結構(gòu)的鋼板一般為25mm。以上的厚板,其焊(hàn)縫坡口可按如圖8所示的形式和尺寸(cùn)設計, 其中a大於(yú)等於10mm, 由於型腔表層結構通常有(yǒu)足夠多的(de)筋板支撐,且在焊縫處可設附加筋(jīn)板,故焊縫不一定要求滿焊。如果焊縫處有明顯的材料(liào)流動,可用高性能膠合劑填平焊縫再經(jīng)打(dǎ)磨後用(yòng)拉延油潤滑。
3 型麵毛坯(pī)模塊的成形過程設計
型麵毛坯分塊後(hòu),就要對其成形過程進行設計,以保證成形後的毛坯模塊符合毛坯組焊的基本要求。這個設計過程要解決如下幾(jǐ)個方麵主要問題。
3.1毛(máo)坯板厚(hòu)的確(què)定
毛坯板厚的確定主要根(gēn)據毛坯模塊的局部凹凸情況確定。所謂局部凹(āo)凸這裏指不能通過調節頂杆高度進(jìn)行成(chéng)形而獲得的凹凸形狀。由前節可知,如果型麵(miàn)形狀的曲率半徑(jìng)小於最小成形曲率半徑,那麽該部分形狀屬於局部(bù)凹凸。如(rú)果不允許毛坯模塊堆焊局部凸塊,那麽毛坯的最(zuì)小板厚應按下式計算
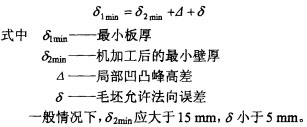
由此可知,對於帶圓弧半徑小(xiǎo)於5mm的拉延筋的壓邊圈部分,用25mm厚(hòu)的鋼板即可滿足型麵(miàn)加(jiā)工(gōng)的基本要求。
3.2上(shàng)下模相對位裏的確定
上、下模的相對位置主要指(zhǐ)在(zài)垂(chuí)直於衝壓(yā)方向的(de)平麵內的相對位置(zhì),如圖9所示。其中圖9a表示上、下模頂杆中心線重合的情形,而圖9b表示上、下模頂杆中心錯(cuò)開(kāi)半個頂杆(gǎn)中心距時(shí)的情形。盡管(guǎn)介於這兩種情形之(zhī)間還可有多種其他相對位置的(de)選擇,但其(qí)意義並不大。
上下模相對位置的(de)確定主要(yào)與毛坯模塊曲麵的最小曲率半徑有關。如果毛坯模(mó)塊最小曲(qǔ)率半徑足夠大,就可直接采用第一種(zhǒng)方案(àn),否(fǒu)則就采用第二種方案。
采用第一種方(fāng)案時裝模和(hé)調試(shì)較方便(biàn),而采用第二種方(fāng)案時(shí)裝模和調試都相對較(jiào)困難一些。斌同一毛坯模塊的成形,既(jì)可采用第一種方案,也可采用(yòng)第二種(zhǒng)方案,但對應的(de)頂杆高度分布是不一樣的。
3.3頂杆(gǎn)高(gāo)度的確定
上下模(mó)頂杆高(gāo)度的確定(dìng)是最終決定毛坯(pī)模塊(kuài)的關鍵因素(sù)。對於第一種上下模相對位置的選擇方案,給定型(xíng)麵(miàn)條件下的頂杆高度可按如下方法確定。
為了使球頭包絡麵能精確地逼近模具型腔曲麵,需要(yào)獲得oxy(離散型麵模底座平麵,後同)平麵上均勻分布頂杆的精(jīng)確高度位置(z向坐標)。如圖10所示,曲(qǔ)麵(miàn)S沿法向偏移一個球頭半徑得到曲麵sl,當球頭球心位於S1上任(rèn)意一點時,球(qiú)體必與S相切 (S的曲(qǔ)率半徑應大於球頭半徑)。因此,利用(yòng)s1可避開球頭與毛(máo)坯鋼板接觸(chù)點的搜索,頂杆高度(dù)計算變成計算曲麵(miàn)sl上在口砂,平麵均布的點的(de)z向坐標(biāo)。對於求取曲麵(miàn)上x,y坐(zuò)標確定的點的z向(xiàng)坐標,有解析法(fǎ)和數值法。解析法對(duì)於一些基本曲線、曲(qǔ)麵,計算速度快,精度很高。在CAD軟件(jiàn)中,曲麵造型采用的是複雜(zá)曲線、曲麵表示(shì)方(fāng)法,且數據結構複雜,雖然解析法可能(有時很難求得解析(xī)解)可以獲得很高的精度,但軟件開發工作量大。與解析法相比,數值解法是將曲麵由大量(liàng)的細小離散平麵構成,然後用插值的方法求出對應x,夕坐標的點的z向坐標。它的計算精度取決於原始(shǐ)離散精度和插值方(fāng)法,離散(sàn)平麵越小,計算誤差越小,但要消耗更多的計算時間。在本項目應用中,精度要求最大弦偏差小於.02rnr。,采用數值方法可以取得很好的效果。
首先在CAD軟件中完(wán)成模具設計,然後將模具型腔(qiāng)曲麵導出轉換成標準圖形交換格式IGES,采用有限元前處(chù)理軟件如Dynaforln、Hypermesh等從曲麵生成(chéng)網格這(zhè)裏並不需(xū)要生成高質 量元(高質量是對有限元計算而言), 故網格生成工作量(liàng)很小(xiǎo)。當頂杆直徑為60mm時, 限定生成網格最小尺(chǐ)寸為8mm,最大尺(chǐ)寸20mm, 最大弦偏差0.13mm.。生(shēng)成網格後(hòu),將網格法向向下偏移一個球頭半徑,即可獲得下模頂杆離散球心曲麵(miàn)。輸出上下模球心離散曲麵節點信息,提供給離散頂杆高(gāo)度計算程序。由(yóu)於獲(huò)得的這些節點並不在頂杆球心處,各(gè)頂杆球(qiú)心的z向高度是通過搜索最近的3個(gè)鄰近節點再插值(zhí)求(qiú)得,算(suàn)法如下。
(l)搜索鄰近節點(diǎn):給球心Ci置(zhì)3個初始鄰近節點(取1,2,3號節(jiē)點),並按與球心的距離(xoy平麵上)排序。然後依次讀入其餘待(dài)選節點,計算與球心的距離,若待選節(jiē)點比(bǐ)最遠的鄰近節(jiē)點更靠近球心,則用它取代該(gāi)鄰近節點,並按距離重新排序,直至搜索完所有的待選節點,完成一個球心的3個鄰(lín)近節點搜(sōu)索。
(2)插值:球心C搜索到3個鄰近節點為ni1,ni2,ni3,鄰近節點z向高度分別為zi1,zi2,zi3,與(yǔ)球心ci在xoy平麵(miàn)上(shàng)的(de)距離分(fèn)別為di1,di2,di3,對插值函數給定如下約束:a當dij=0時, ci的高度zi=zij,1小於等於(yú)j小於等於3。b當dil=di2=di3時,
Zi=
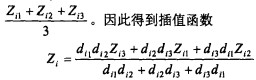
對於第二種上、下模相對位置的選擇方案,頂杆高度的計算步驟與前麵基本(běn)相同。區別在於計算(suàn)上模頂杆高度位置時,將上模頂杆球心在口樸,平麵上沿x、y軸平移半(bàn)個球頭直徑距離,然後再搜索球心鄰近點,插值計算得到上模頂杆球心高度。
4 應(yīng)用實例
這裏討論的快速毛坯(pī)製造技術已應用到多個汽車新產品開發和改型中,圖1為某汽車公司開發的車頂外覆蓋件拉延成形模。應用上述技術可使組焊方法製造(zào)毛(máo)坯的周期比普通(tōng)的鑄造毛(máo)坯製造周期(qī)縮短達50%,並且在采用一定的鑲塊工藝後,其(qí)壽命和品質可以滿足中小批量(5一10萬件)生產的需要。
5 結論
基於組焊技術的(de)模具毛坯快速製造技(jì)術是一種值得進一步研究(jiū)和開發的模具製造技術,它以平麵構件和曲麵構件為基礎通過一定的(de)優化組焊工藝完成(chéng)模具毛坯的快速製造,該快速製造方法可以看作(zuò)一種特殊的快速原型製造技術,但成本遠比傳統的快(kuài)速原型製造技術(shù)低,且可製(zhì)造尺寸很(hěn)大的製件。這一技(jì)術(shù)的核心(xīn)之一是曲麵構件(jiàn)的快速成形,采用討論的基於離散型麵模成形技術後,可(kě)快速獲得精確的曲(qǔ)麵構件。雖以典型拉延模(mó)為例討論了任意複雜型麵的毛坯模塊化和(hé)型麵毛(máo)坯(pī)模塊的成形設(shè)計,但其結論同時(shí)適合於其他類的模具的毛坯設計製造。實踐表明這一(yī)技術可使毛坯製造時間縮短50%以上,有產生重大社會效益和經(jīng)濟效益(yì)的前景。
如果您有機床行業、企業(yè)相關新聞稿(gǎo)件發表,或進行(háng)資訊合(hé)作,歡迎聯係本網編輯部, 郵(yóu)箱:skjcsc@vip.sina.com