航空(kōng)整體葉輪(lún)五軸數控加工仿真及參數優化研究 (下)
2016-11-21 來源:天(tiān)津職業技術師範大學 作者(zhě): 盧(lú)輝
第 5 章 基於動力學仿真的切削參數優化
5.1 概述
航空整體式葉輪(lún)約70%的餘料需要切除,因此如何合(hé)理(lǐ)選擇切削參數高效地去除餘料是整體葉輪數控加工中提高生產效率的一個瓶頸問題。切削參數直接(jiē)關係到零件的加工質量,刀具的壽命,生產成本。而在實際生產加工中,切削參數往往是數控工藝人員根據(jù)刀具廠商推薦或憑經驗來選取的。由此產生的直接後果(guǒ)是:一(yī)方麵,由(yóu)於(yú)缺乏理論依(yī)據,所(suǒ)選擇的切削參數過於保守,導致切削效率低下難以充分發揮數控機床,特(tè)別是高速數控機床的效能,造成浪費;另一方(fāng)麵,即使以較(jiào)低的材料去除率進行切削,如果選擇的(de)切削參數不合理,也會因顫振(zhèn)的(de)發生而導致零件尺寸(cùn)超差甚至對機床和刀具本身造成損害。因此,合理地選擇切削(xuē)參數是實際加工生產的迫切需(xū)求。本文將在上一章得到的顫振(zhèn)穩定域的基礎上,進(jìn)行切削參數(shù)的優化。首先基於最短切削時(shí)間(jiān)對切削參數進行正交試驗設計,分析正交(jiāo)試驗結果,得(dé)出最短切削時間的切(qiē)削參數。然後基於動力學仿真進行切(qiē)削(xuē)參數的優化,最終(zhōng)得到最佳切削參數。
5.2 基於顫(chàn)振穩定域的切削(xuē)參數優化
5.2.1 正交試驗方法
正交試(shì)驗是日本田口(kǒu)玄一在(zài)上個世紀40年代設(shè)計出(chū)來的[60]。正(zhèng)交試驗是(shì)在全麵實驗中挑選有代表性的樣點進行來做實驗,這大大減少了實驗次數,因而(ér)在世界範圍內得到廣(guǎng)泛應用[61]。正交試驗設計是運用數理統計(jì)的知識,選取典型的有代表性的樣點進行實驗,對實驗結果進行極差分析和方差分析,找出最佳實驗方案。這(zhè)種方法主要用於優化(huà)多因(yīn)素多水平的科學(xué)實驗,能夠減少實(shí)驗次數(shù),縮短實驗周期,降低實驗成本。
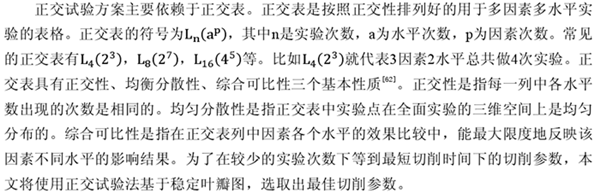
5.2.2 正交試驗設計
切(qiē)削(xuē)加工過程中,在保證加(jiā)工質量的前提下,提高加工效率,即在穩定的切削的(de)前提下,保證(zhèng)材料的最大去(qù)除率[63]。對銑(xǐ)削而言,材料去除率 MRR可表示為軸向切(qiē)削深度 ap徑向切削寬度ae、主軸轉速n、每齒進(jìn)給量f N及(jí)銑刀齒數N的(de)函數。

為了在較(jiào)少的實驗次數下充分考慮切削寬度、切削深度、主軸轉速、每次進給量對切削時間的影響,本實(shí)驗將采用正交試驗法。在本實驗中,切削時間為實驗的(de)指標,切削寬度、切削深度、主軸轉速、每次進給量為影響(xiǎng)因(yīn)素。根據上一章得出的穩定葉瓣圖,每個因素選取4個水平(píng)。根據加工經驗,將切削寬度選取為(wéi)3mm,4mm,5mm。由切(qiē)削寬(kuān)度為3mm,切削寬度(dù)為4mm,切削寬度為5mm仿真得出顫振穩定域分析解如(rú)圖5-1所示。
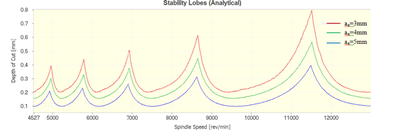
圖 5-1 顫(chàn)振穩定域
從圖中可以看出,隨著切削寬度的增加,顫振穩定域的切削深度降低。這就會影響正交實驗的設計(jì),如果把正交實驗設計為四因素四水平的話,有很(hěn)多組實驗因為(wéi)超出顫振穩定域的切削深度而沒有(yǒu)辦進行。所(suǒ)以為了更好地選取出最佳(jiā)的切削參數,把切削寬度不同的(de)情況,單(dān)獨做正交實驗。就是將(jiāng)正交(jiāo)實驗設(shè)計成切削(xuē)寬度為3mm,切削寬度為4mm,切削寬度為5mm三組三因素四水平的正交試驗。首先,先設計切削寬度為3mm的正(zhèng)交試驗,正交試(shì)驗(yàn)的因(yīn)素水(shuǐ)平表如下表5-1所(suǒ)示。
表5-1 因素(sù)與水平表

5.2.3 參數優化結果及分析
根據因素水平表中的因素和水平(píng),選用正交表L 4 ,如表5-2所示。通過VERICUT軟件幾何仿真,可以得到每組參數的切削(xuē)時間。
表5-2 用正交(jiāo)表安排實驗
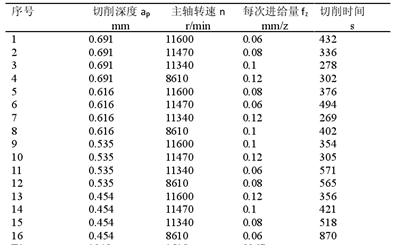
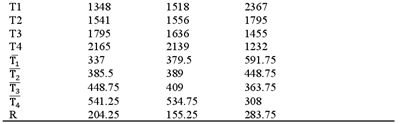
從表5-2中的16次(cì)試驗結果(guǒ)看出,第7號試驗(yàn)ap=0.616, n=11340, fz=0.12的切削(xuē)時(shí)間最短,為269s。從正交試驗結果來看,第7號試驗是最佳切削參(cān)數方案,當由於正交試驗(yàn)隻是(shì)在全麵實驗中做了16組試驗,最佳切削參數不一定在這16組試(shì)驗中,因此為了找出最佳方案,還需要對正交試驗結果進一步分析。表5-2中T1、T2、T3、T4這四行分別是各因素同一水平(píng)結果之和。例如(rú),ap因素T1行列的數據1348是ap因素4個1水平(píng)實驗值的和,而ap因素4個1水平分別(bié)在(zài)第1,2,3,4號試驗,所以ap的T1=432+336+278+302=1348。ap因素的T2、T3、T4如下:
T2=376+494+269+402=1541
T3=354+305+571+565=1795
T4=356+421+518+870=2165
同理(lǐ)n因素的T1、T2、T3、T4為
T1=432+376+354+356=1518
T2=336+494+305+421=1556
T3=278+269+571+518=1636
T4=302+402+565+870=2139
同理(lǐ)fz因素的T1、T2、T3、T4為
T1=432+494+571+870=2367
T2=336+376+565+518=1795
T3=278+402+354+421=1455
T4=302+269+305+356=1232

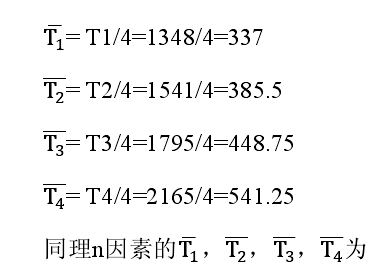
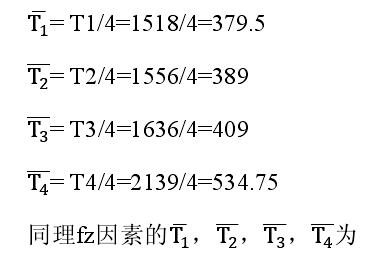
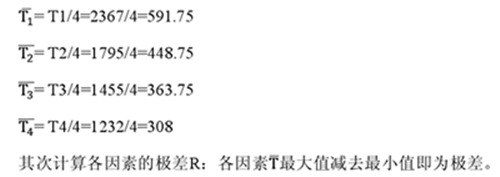
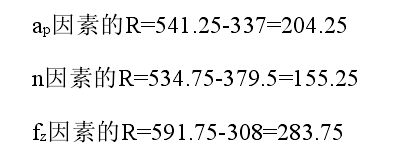
最後分析結果,分析表明極(jí)差越大的因(yīn)素重(chóng)要程度越高。因此,因素主次順序應為:n→ap→fz。為了直觀起見,用因素的水(shuǐ)平變化為橫坐標,切削時間的平均值為縱坐標,畫出水平與切削時間關係圖,如圖5-2所示
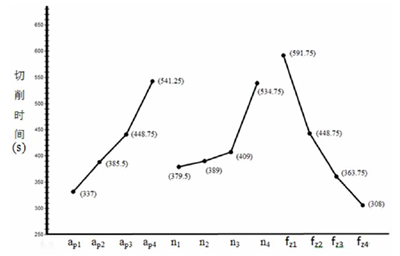
圖 5-2 水平與切削時間關係圖(tú)
從上圖(tú)可以明顯看出,最佳方案是ap1,n1,fz4而正交實驗選出的最佳方(fāng)案(àn)是ap2,n3,fz4。顯然(rán),正交實驗中(zhōng)的16組試驗沒(méi)有ap1,n1,fz4這一方(fāng)案。其是否是最佳實驗還需要(yào)驗證。通過對顫振穩定域圖(tú)分析發現,當ap=0.691, n=11600, fz=0.12時,已經(jīng)超出顫振(zhèn)穩定域的(de)範圍,如圖所(suǒ)示,說明使用這組參(cān)數進行加工時刀具會發(fā)生顫振,不是最佳方(fāng)案。故當ae=3mm時,最佳的切削參數為ap=0.616, n=11340, fz=0.12。
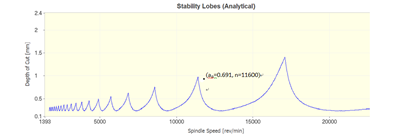
圖 5-3 水平與切削時間關係圖
在前麵進行的極(jí)差分(fèn)析(xī)可以得到(dào)各因素對切削(xuē)時間影響的程度,根據各因素(sù)影響切削(xuē)時間最大的水平數得到最(zuì)佳切削參數。極差分析計算方便,簡單易懂,因此得到廣泛應用。但(dàn)是極差分析不考慮實驗(yàn)誤差,任何實驗中都不可避免出現誤差,無法判斷有誤差引起的數據波(bō)動(dòng)。為了(le)解決這個問題,在正交試驗中引入方差分析。 方差(chà)分析是通(tōng)過離方差平方和分解,構造F統計量,生成方差分析表,對因素效應和(hé)交互效應的顯著性(xìng)作檢查[65]。方差分析可以估計試驗誤差並對其(qí)分析,給出所得結(jié)論的置信度區間,對各因素進行顯著性分析。進行方差分析的基本步驟:1)試驗(yàn)數據總的偏差平方(fāng)和SST;2)因素的(de)偏差平方和;3)誤差平均方和SSE;4)自由度DF;5)均方(fāng)MS;6)F值(zhí);7)顯著性概率P值;
(1)試驗數據總的偏差平方和SST

其中(zhōng)n是正交試驗的總實驗次數,正交(jiāo)表的(de)每(měi)一行代表每(měi)一次試驗得到的實驗數據,共有n個實驗(yàn)數據,記為y ,y ,……,y ,本例n=16。y是n個實驗數據的平均(jun1)值。
(2)因素的偏差平方和。設切削深度、主軸轉速、每齒進給量的偏差(chà)平方和分別為SS1、SS2、SS3。各因素的偏差平方和為:
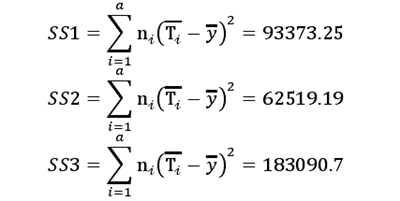
(3)誤差平均方和SSE。計算誤差平方和,不考慮交互作用的一般公式:

(4)自由度DF。在正交設(shè)計中,各列的自由度是水平數減(jiǎn)1,總自由度(dù)是實驗次數減1,即
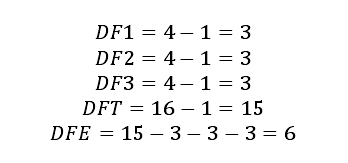
(5)均方MS。均方就是偏差平方和除以自由(yóu)度,即(jí)
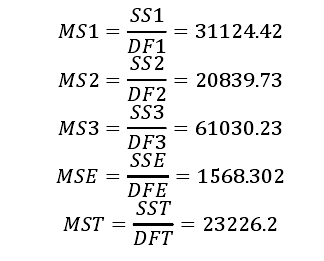
(6)F值。因素的均方和誤差均方差的比(bǐ)值F是(shì)一個統計量,即(jí)
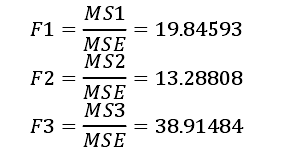
(7)顯著性概率P值。P值可以確定(dìng)兩個(gè)數據集是否存在變化(huà)程度上的不同。借助Excel表軟件來計算(suàn)p值。即


從P值的結果來分析(xī),可以看出每齒進給量(liàng)的顯著(zhe)性最高,其次是切(qiē)削(xuē)深度,最(zuì)後是主軸轉速,說明每齒進給量(liàng)對(duì)切削(xuē)時間影響最大,其次是(shì)切削深度,最後(hòu)是主軸轉速。這與前麵用極差分析是一致的。 前麵討論(lùn)的是(shì)當ae=3mm時候的情況,下(xià)麵來討論ae=4mm,ae=5mm的最優(yōu)切(qiē)削參數,根據穩定葉瓣圖選取表5-3、表5-4的切削(xuē)參數。
表(biǎo)5-3 ae=4mm的因素與(yǔ)水平表

表 5-4 ae=5mm 的因素與水平表(biǎo)

同(tóng)理對表5-3、表5-4做正交試驗得出,當ae=4mm時,最佳的切削參數為ap=0.475, n=11340, fz=0.12,切削(xuē)時間為326s;當ae=5mm時,最(zuì)佳的(de)切削參數為ap=0.375, n=11340, fz=0.12,切削時間為450s。而當ae=3mm,ap=0.616, n=11340, fz=0.12時,切削時間(jiān)為269s。從正交試驗得出的最少切削時間的加工參數是(shì)ae=3mm,ap=0.616, n=11340, fz=0.12,但實際加(jiā)工中還需考(kǎo)慮機床的主軸功率、切(qiē)削力、主軸扭矩等情(qíng)況。因此,使(shǐ)用(yòng)Cutpro9.0軟(ruǎn)件對這三組參數進行切削過程的仿真,預測切削時的主(zhǔ)軸功率、切(qiē)削力(lì)、主(zhǔ)軸扭矩、表麵粗糙度等。
5.3 基(jī)於動力學仿真(zhēn)的切削參數(shù)優化(huà)
5.3.1 Cutpro9.0的動力學仿真功能
在切削過程仿真模塊中(zhōng),通過設定(dìng)刀具幾何(hé)形(xíng)狀、加工參數、工件和刀具的(de)動態模態參數可(kě)以模擬出X、Y、Z方向的切削(xuē)力和切向切削力、在(zài)XY平麵上的切削(xuē)合力、切削厚度變(biàn)化情況、刀具(jù)振動、工件振動、由於(yú)強迫振動和顫振引起的表麵光潔度、主軸的功率(lǜ)和扭矩、作用(yòng)於刀具上的彎矩、切削(xuē)動(dòng)畫等。 切削過程仿真對非線性效應比如刀具走空刀、刀具跳動、複雜的刀具幾何形狀等進行詳細檢查非常有(yǒu)用。切削過程仿真可以預測在考慮刀具和工件(jiàn)結構動態下的切削(xuē)力,看看切削力是否超(chāo)過機床所能承受(shòu)的範圍;可以檢查顫振的情況,如果顫振(zhèn)非(fēi)常激烈的,很容易導致(zhì)刀具的折斷(duàn);可以預測切削過程(chéng)中的主軸功率和扭矩,看是否超出機床最大主軸功(gōng)率和扭矩的範圍;通過近似的切屑模型或形(xíng)成切屑的精確運動(dòng),可以預測切(qiē)削厚度變化情況;可(kě)以顯示刀具(jù)和工件在X、Y方向振動情況;通過觀察(chá)表麵光潔度圖,可以預測表麵(miàn)光潔度的粗糙度值,看看它是否在可接受的公差內。 5.3.2 動力學仿真(zhēn)結果及分析(xī) 在進(jìn)行切削過程仿真之前,使(shǐ)用(yòng)Modal(模態分析模塊)通過(guò)對錘擊實驗獲得的頻響(xiǎng)函數(FRF)進行辨識處理,得到包括固有頻率、阻尼比(bǐ)和剛度在內的模(mó)態參數曲線。首先點擊(jī)“NEW Analysis”,在彈出的對話框中選擇錘擊實驗獲得的頻響函數(shù)文件,選擇想要的模態參數,點擊刷新按鈕,選中的模態參數將擬合成模態參數曲線,點擊保存為.cmp格式文件。如圖5-4、圖5-5分別是D6平底銑(xǐ)刀(dāo)X方向、Y方向的模態參數曲線。
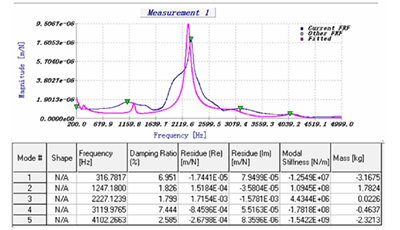
圖 5-4 X 方向的模(mó)態參數曲線
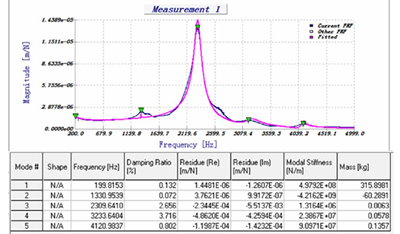
圖 5-5 Y 方向的(de)模態參數曲(qǔ)線
圖5-4和圖5-5中,藍色的曲線是(shì)錘擊試驗獲得的頻響函數,粉色的曲線是模態參數曲線(xiàn),五個綠色的三角符號是選中的模(mó)態(tài)參數,從左到右分(fèn)別對應表格中的一階模態參數,二(èr)階模態參數,三階模態參數,四階模態參數,五階模態參數(shù)。這些參數包(bāo)括了固(gù)有頻率、阻尼比和模態剛(gāng)度(dù)在內等參數(shù)。得到模(mó)態參數曲線(xiàn)後,下麵進行切削過程的仿真。為了敘述方便,本文將ae=3,ap=0.616, n=11340, fz=0.12設為A參數,ae=4,ap=0.475, n=11340, fz=0.12設為B參數,ae=5,ap=0.375, n=11340, fz=0.12設為B參數。仿真(zhēn)具體操作步驟就不再這敘述了,通過切削仿真(zhēn)後得到切(qiē)削參數的主軸功率、切削(xuē)力、主軸扭矩、刀具振動。為了(le)減少篇幅,本(běn)文列出A組仿真結果圖進行分析。圖5-6至5-10為A組切削參數仿真結果(guǒ)。
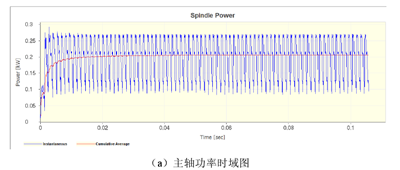
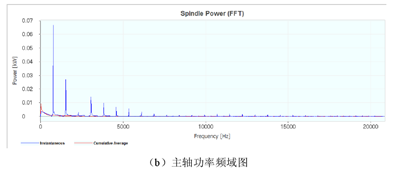
圖5-6 主軸功率仿真結果
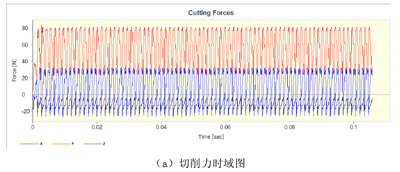
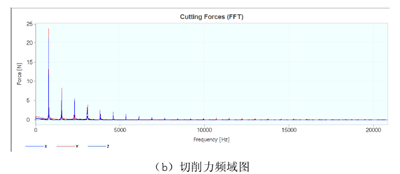
圖(tú)5-7 切削力
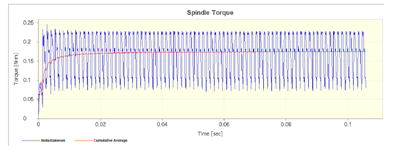
圖5-8 主軸彎矩時域圖
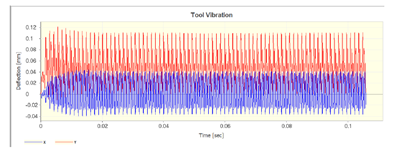
圖5-9 刀具振動時域圖
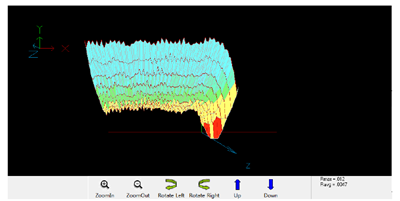
圖5-10 表麵粗(cū)糙度
將立銑(xǐ)的(de)進給方向和進給方向(xiàng)的法向分別定為笛卡爾坐標係的X和Y軸,Y軸方向的任(rèn)何偏差(chà)將產生靜態形狀誤差。螺(luó)旋立銑刀產生的形狀誤差相當複雜[66]。如圖5-7(a)切削力時域圖所示,切削力並(bìng)非常(cháng)數,因為立銑刀是螺旋刃的,切削(xuē)力是隨立銑刀的(de)旋轉(zhuǎn)變化的,另外(wài),由於螺旋槽的螺旋角的存在,也將產生沿著刀具Z軸(zhóu)變化的切(qiē)削力[67]。因為切削力不(bú)是常數,所以主軸功率和主軸彎矩也是瞬時變化的,如圖5-6和5-8所示。順銑加工中,切削厚度是由大變(biàn)小的,切削力在剛切入工件時達(dá)到(dào)最大,隨著切削刃切出離開工件,切削力(lì)逐漸減小(xiǎo)。從(cóng)圖5-7(b)切削力頻域圖可以看出切削力是符合順銑加工周期性變化規律的,這也說明(míng)切削是穩定的沒有發生顫振。如圖(tú)5-9所示,刀具振動(dòng)呈現出(chū)周期(qī)性(xìng)變化,並沒有發現異常,說明切削過程沒有發生顫振。圖5-10是加工表麵(miàn)的光潔度(dù),看到最大值為0.012,平均值(zhí)為0.0047,滿足工件加工要(yào)求。其他兩組的仿真結果如表5-4所(suǒ)示。
表5-4 仿真(zhēn)結果(guǒ)

從表中的仿真結果(guǒ)可以看(kàn)出,三組切削參數的主(zhǔ)軸功率、切削(xuē)力、主軸彎矩、刀具振動差別不(bú)大,A組的表麵(miàn)粗糙度值與B組和C組的表(biǎo)麵粗糙度值相差很大。由前麵(miàn)的正交試驗可知,A組的切削參數是切削時間(jiān)最短的。所以綜合考慮本文選取A組參數進行加工。
5.4 本章小結
為了在較少的實驗次(cì)數下充分考慮切削寬度、切削深度、主軸轉速、每次進給量對切削時間的影響,本節將采用正交試驗法。首先在工藝係統顫振穩定域仿真的基礎(chǔ)上,以切削時間為優化目標,切(qiē)削深度、主軸轉速、每齒進(jìn)給量為實驗因素,設計三(sān)因素四水平的正交試驗,通過幾何仿真獲(huò)得切削時間。然後對實驗結果進行直觀分析和方差分析,得出各組的最佳切削參數。為了更好地選擇切削參(cān)數,實際加工中還需(xū)考慮機床的主軸功率、切削力、主軸扭矩等情況(kuàng)。因此,使用Cutpro9.0軟件對這三(sān)組參數進行(háng)切(qiē)削(xuē)過程的仿真,預測切削時的主軸功率、切(qiē)削力、主軸(zhóu)扭矩(jǔ)、表麵粗糙度,最終得出ae=3mm,ap=0.616, n=11340, fz=0.12為最佳切削(xuē)參數。
第 6 章 葉輪五軸數控加工(gōng)實驗驗證
本(běn)章將進行葉輪的實際加工驗證前麵優(yōu)化的粗加工參數,為了充(chōng)分地驗證優化結果將選取兩組前麵(miàn)優化後的切削參數進行葉輪試切加工。第一(yī)組粗(cū)加工參(cān)數為ae=3,ap=0.691, n=11600, fz=0.12。第二組粗加(jiā)工參(cān)數ae=3,ap=0.616, n=11340, fz=0.12。為了敘述方便,本文將第一組參數加工的葉片稱為第一(yī)組葉片,將第二組參數加工的葉片為第二組葉片(piàn)。
6.1 實驗準備
6.1.1 葉輪毛坯的準備
本文研(yán)究的航空(kōng)整體(tǐ)葉輪總高度為57.1mm,直徑為Φ123.2mm,如圖6-1所示。結合實(shí)驗室的實際情況,將采用三(sān)爪卡盤進行裝夾。為(wéi)了避免加工中主軸(zhóu)與工作台的碰撞,將葉輪的毛坯定為(wéi)直徑為Φ130mm,高度為160mm的棒料。首先使用數控車進行加工棒(bàng)料得到葉輪的毛坯,使(shǐ)用三爪卡盤(pán)裝夾在機(jī)床上如圖6-2所示。
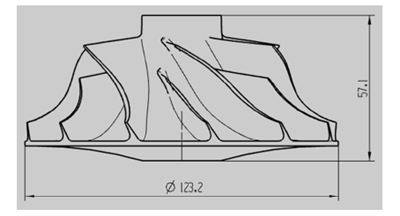
圖6-1 葉(yè)輪的整體尺寸
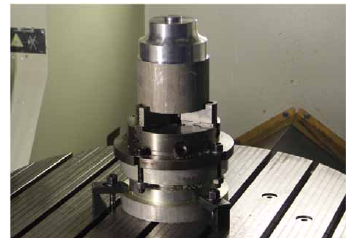
圖6-2 葉輪的(de)裝夾方案
6.1.2 葉(yè)輪數控程序的編製
為了提高葉輪的(de)加工效率,本文選擇3+2定軸加工方法進行葉輪的粗加工。創建葉輪粗(cū)加工的操作過程:首(shǒu)先定義加工坐標係、加工毛(máo)坯,創建加工刀具,打開型腔銑加工策略,按照前(qián)麵優化出來的加工(gōng)參數進行設(shè)置,切削寬度為3mm,切削深度為(wéi)0.616mm,主軸(zhóu)轉速為11340r/min,每齒進給量為0.12 mm/z,生成如圖6-3的葉輪粗加工刀具軌跡。同理設置另一組參數的粗加工和精加工刀具軌(guǐ)跡。
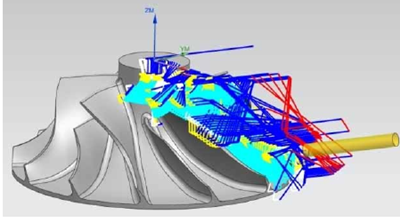
圖6-3 葉輪加工刀具軌跡(jì)
6.2 實驗結果分析
將編製好的(de)數控程序傳輸到五軸機床,裝夾刀具,設置工件坐標係,開始加工葉輪。加工過程中主要觀察刀具是否與夾具等發生幹(gàn)涉。加工(gōng)過程如圖,通過觀察加工過(guò)程,發現刀具與夾具,主軸與工作台等(děng)並沒有發生幹涉,與上一章VERICUT仿真(zhēn)結果一樣。這說明本文構建的VERICUT能夠準確檢查機床幹涉問題。如圖6-4所示第一組切削參(cān)數(shù)得到的粗加工(gōng)結果,和使用第(dì)二組切(qiē)削參數粗加工後的零件。
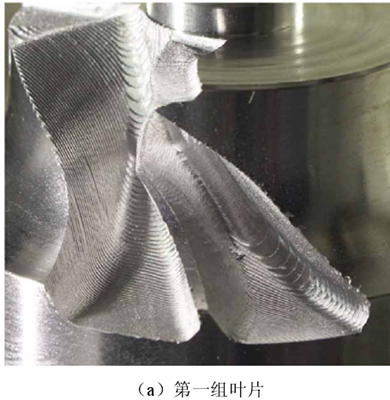
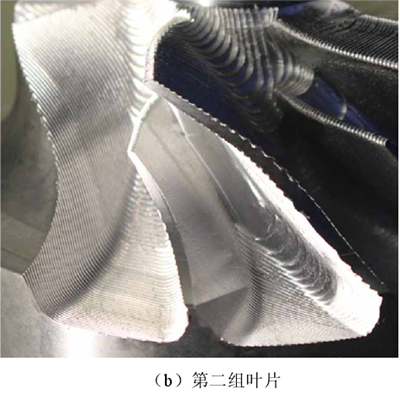
圖6-4 葉輪粗加工
第一組參數的切削(xuē)時(shí)間為10min,第二參數(shù)的切削(xuē)時間為15min。實際的切削時間和前麵預測的切削結(jié)果(guǒ)一樣。下麵進行葉輪(lún)精(jīng)加工。為了敘述方便,本文將第一組精加工得(dé)到的圖6-5是兩組精(jīng)加工後得到的葉
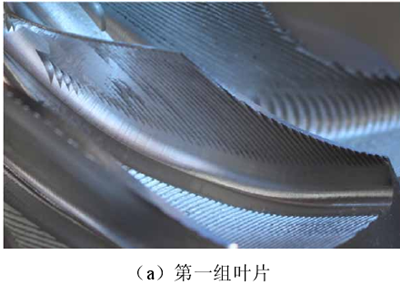
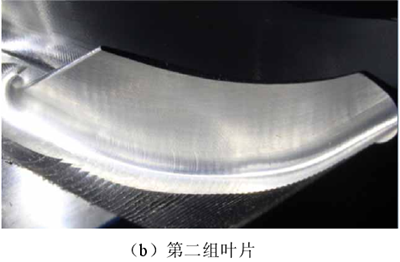
圖6-5 精加工後(hòu)的葉片
從圖6-5中發現,第一組葉片的背麵在精加(jiā)工完之後(hòu)還殘留粗加(jiā)工的刀痕,說明第一組葉片粗加工階段發生過切現(xiàn)象,第二組葉片的背麵是精加工完成後得到光(guāng)潔(jié)的表麵,說明(míng)第二組(zǔ)葉片粗加工時沒有發生(shēng)過切情況。這是因為第一組切削參數的進給速度(dù)太快,而葉片與葉片間的流(liú)道狹窄,機床運動(dòng)軸速度過快而導致(zhì)過切。兩組的葉片正(zhèng)麵都沒有發(fā)生粗加工過切現象。
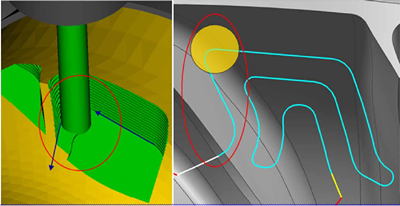
圖6-6 葉片過切(qiē)處刀路軌跡
通過VERICUT仿真查看過葉片過切處的情況,如圖6-6所示,在紅(hóng)色圈內是葉片發生過切處的刀路軌(guǐ)跡,藍色箭頭是刀具的走刀方向。從圖中可以看到刀(dāo)具(jù)是從右向左切削,經過一個角度為銳角的拐角。而第一組的進給速度為5443mm/min,快速通(tōng)過拐角位置時,由於速度越(yuè)快刀具受到的離心力越大,同時拐角的角度為銳(ruì)角,導致刀具變向急(jí)劇,從(cóng)而(ér)導致過(guò)切(qiē)現象。而第(dì)二組的進給速度為2000 mm/min,切削經過拐(guǎi)角處的速度比較慢,受到的離心力小,因而葉片沒有發生過(guò)切現象。
6.3 本章小結
本節使用兩(liǎng)組前麵優化的切削參數,進行葉輪的切削加工。通過觀(guān)察切削過程,並沒有發現(xiàn)機床(chuáng)主軸與夾(jiá)具(jù)、工作台等(děng)發生幹涉,從而驗證了本(běn)文(wén)建立的VERICUT數(shù)控仿真環(huán)境是可行的。葉輪加工完成後,得到第一(yī)組粗加工的(de)切削時間比第二組粗加工切削時間短,但是第一組的粗加工發生(shēng)了過切現象(xiàng),第二組粗加工沒有(yǒu)發生過切情況。這與前麵切削參數(shù)優化分(fèn)析結果一致。
第 7 章 結論與展(zhǎn)望
7.1 結論
本文以航(háng)空整體葉輪為(wéi)研究對象,首先獲取葉輪加工的顫振穩定域,然後基於動力學仿(fǎng)真進行切削參數優化。最後在VERICUT軟件中建立葉輪加工仿真環(huán)境,並(bìng)進行實驗驗證優化後的切削參數和建立(lì)的葉輪(lún)仿真環境。得出以下結論:
1.在 VERICUT環境下建立虛擬的數控機床實體、控製係統、刀庫、坐標係(xì)統等,創建數控仿真環境(jìng),實現針對具體工藝係統(tǒng)的幾何仿真,同時,總結出幾點利用VERICUT軟件進行虛擬數控機床建模的關鍵技術。通過實驗驗證VERICUT數控(kòng)仿真環境有效檢查機床主軸、刀具與工作台、夾具之間碰撞。
2.針對海德漢i TNC530數控係統(tǒng)的傾斜加工麵功能,通過對CLSF刀位軌跡進行齊次變換運算,提(tí)出了機床運動坐標的數控程序後處(chù)理算法(fǎ)。使用UG NX8.5/Post Builder編寫後(hòu)處理文件。通過實例驗證表明該後處理算法能夠實現在傾斜(xié)麵加工上輸出圓弧插補,大大提高(gāo)葉輪加工效率。
3.采用力傳感器和加速度傳感器,通過錘擊實驗(yàn)來獲取機(jī)床-刀具和機(jī)床-工件的頻響函數。然後采用(yòng)Cutpro9.0的動力學仿真功能,在給(gěi)定的徑向切削深度(切寬)條(tiáo)件下,進行顫(chàn)振穩定域仿真,獲得表征主軸轉速和軸向切深關係穩定域葉瓣圖,為後續幾何仿真和動力學仿真的切削參數優化奠定基礎。
4.在工藝係統顫振穩定域的基礎上,以切削時間為優化目標(biāo),切削深(shēn)度、主軸轉速、每齒進給量為實驗因素,設計三(sān)因素四水平的正交試驗,通過幾何仿真獲得切削時間。根據極差(chà)分析和(hé)方差分析,得出三組較(jiào)短切削時間的加工(gōng)參數。對初步優化得到的三組切削參數進一步進行動力學仿真,根據仿真結果確定最優工藝參數。通過葉輪實際切削加工發現,優化後的加工參數(shù)能(néng)夠縮短加工時間,且不發生顫振。
7.2 展望
本文對航(háng)空整體葉輪進行五軸數控加工仿真(zhēn)及參數優化研究(jiū)。由於葉(yè)輪(lún)加(jiā)工仿真及參數優化涉及學科廣泛,本文隻是做(zuò)了一些初步研究,仍有很多不足。有待(dài)進一步研究的幾個方(fāng)麵(miàn):
1.本文研究的葉輪流道比較狹窄,刀具軌跡的直線段距離比(bǐ)較短,實際加工中機床運(yùn)動軸頻頻減速加(jiā)速(sù)或突然變向,未能考慮運動軸在加速減速或突然變向給機(jī)床帶(dài)來額外的振動。
2.本文主要研究了立銑刀定軸(zhóu)加工葉(yè)輪的(de)情況,沒(méi)有對球頭(tóu)銑(xǐ)刀五軸聯動加工葉輪這(zhè)種情況做研究,而且本文主要考慮了機床-刀具的動態特性,沒有考慮到機床-工件的動態特(tè)性。
3.今後的研究,應該在優化五軸(zhóu)機床的刀具軌跡和刀軸幹涉的基礎上,以最小表麵粗糙度為目的優化切削參數。
投稿箱:
如果您有機床(chuáng)行業、企業相關新聞(wén)稿件發表,或進行資訊合作,歡迎聯係本網編輯部, 郵箱:skjcsc@vip.sina.com
如果您有機床(chuáng)行業、企業相關新聞(wén)稿件發表,或進行資訊合作,歡迎聯係本網編輯部, 郵箱:skjcsc@vip.sina.com
更多本專題新聞
專題點(diǎn)擊前十
| 更多