基於葉(yè)輪等複(fù)雜部件的智能製造生產線設計
2024-4-7 來源: 滕州華數智能製造研究院研發部 作者:範(fàn)業鵬
【摘要】: 為了解決複(fù)雜部件加工製造工藝的複雜性,以葉輪等複雜部件的智(zhì)能製造生產線設計為(wéi)基礎,通過智能製造生產線的工藝分析和設計方(fāng)案(àn),結合機(jī)器視覺、智能檢測(cè)、智能物流和工業互聯等技(jì)術(shù)進行產線仿真與驗證。 結果表明(míng) : 該智能製造生產線設計不(bú)僅滿(mǎn)足生產要求、工作運行穩定,而且實現生產(chǎn)過程(chéng)的自動化、信息(xī)化和智能化,滿足多品種小批量產(chǎn)品的(de)定製化(huà)混流生(shēng)產,達到為企(qǐ)業降本增效的(de)目的。
【關鍵詞】: 智能(néng)製造生產線 ; 設施布局 ; 設計與仿真 ; 葉輪加(jiā)工
本文作者以葉輪等複雜部件的智能製造生產線設計為基礎(chǔ),以智能產線功能設計需求為導向,分析智能製造生產線的工藝設計及模塊設計,最後對其進行仿真與驗證。
1. 功(gōng)能設計
智能(néng)製造生產線是智(zhì)能工廠建(jiàn)設的重點和離散製造型(xíng)中柔性生產的關鍵部分,以產品的生產流程為基礎,結合智能化(huà)生產係統、網絡化分布設施,采用(yòng)數控裝備、工業機器人、智能傳感器、數字化倉儲設備、物流輸送設(shè)備和(hé)自動化專機作為(wéi)智能化設備,融入自主(zhǔ)數據判斷處理等智能化軟件分(fèn)析,實現(xiàn)產品的智能排產和生產(chǎn)過程。以葉輪等複雜零件為(wéi)研究示例,以實現葉輪的智(zhì)能(néng)化生產過程為基礎進行需求分析和概要設計。
(1)需求分析。 以葉(yè)輪為典型複雜(zá)零件,以智能化產線設計方法為導引,結合葉輪加工生產工藝,完成生產、分析和總(zǒng)結過程。
(2) 總體功能。 以複雜零件葉(yè)輪加工生產為(wéi)核心(xīn),通過智能裝備的並行和串行設計組成生產(chǎn)線,並能結合信息化網(wǎng)絡化實現智(zhì)能生產和分析決策等過程,提高產量和產品質量,達到工藝合理化,智能設備與工業軟件(jiàn)的(de)融合(hé),各個物理鏈路和工業互聯的鏈接。
(3)電氣網需求。380V/220V、50Hz 三相五線製,氣(qì)源壓力(lì) 0.5~0.8MPa,提供 Internet 接入。
(4)設備需(xū)求。 以加工工件工藝路(lù)線為核心,完成複雜零件葉輪軸、軸(zhóu)套的加工檢測及(jí)裝配,涵蓋機械加工(車床、加工中心等)、檢測、裝配、倉儲(chǔ)等(děng)模塊。
表 1 葉(yè)輪軸零件加工工藝分析
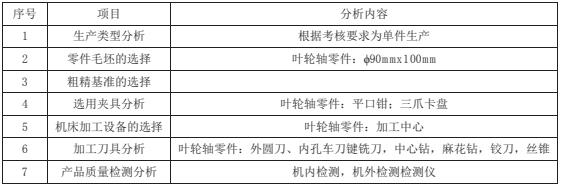
2.智能製造生產線的工藝設(shè)計分析
文中主要以葉輪軸和軸套為(wéi)生產工件進(jìn)行分(fèn)析。葉輪軸結構如圖(tú) 1 所示。 葉輪軸零件加工工藝分析如表 1 所示。
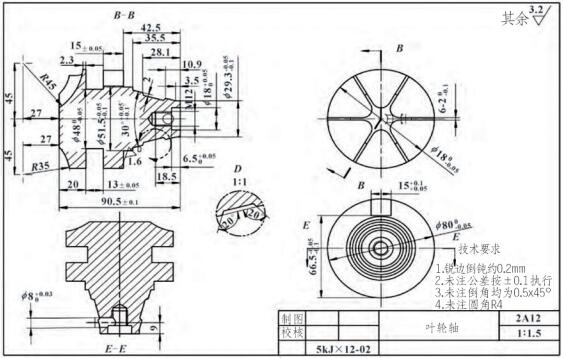
圖 1 葉(yè)輪軸結構
從圖1可以看出: 葉輪軸零件直徑為Φ48、Φ51.5、Φ18、Φ15m m,加工精度要(yào)求(qiú)較高,加工難度也較大,對應(yīng)的軸套(tào)零件Φ80、Φ66、Φ8、Φ4.1、Φ40 mm等尺寸精度要求也較(jiào)高。 為保證上述加工精度,首先對軸套各個軸段進(jìn)行車削(xuē)加工,隨後(hòu)銑削(xuē)平麵和鑽孔。 葉輪(lún)軸、軸套配合後(hòu),要求台階銷(xiāo)能(néng)插入Φ8mm 的孔中,為了達到這個要求,必須將葉輪軸、軸(zhóu)套進行組合加工。
因此,在工藝路線設置中綜合考慮零件結構、加工難度和數控(kòng)設備情(qíng)況(kuàng),選擇數控車床和加工中心完成加工內容,選用專用檢測設備完成(chéng)關鍵尺寸檢(jiǎn)測。
3.智能製造生產線的模(mó)塊設計分析
3.1 智(zhì)能(néng)製產造線生(shēng)整體分析(xī)
此智(zhì)能產(chǎn)線主要由智(zhì)能製造加工單元,智(zhì)能中央控製(zhì)單元模塊、智能裝配模塊(kuài)、智能(néng)倉(cāng)儲物流單元、智能檢測模塊和(hé)機(jī)器(qì)人視覺單元組成。在整體架構上采(cǎi)用智能設備層、智能傳感層、智能執行層和(hé)智能決策(cè)層。 通過智能設備層與傳感層構建(jiàn)智能化生(shēng)產(chǎn)協(xié)同柔性自動(dòng)化生產線,由智能執行層與智(zhì)能決策(cè)層構建生產智能製造的管控平(píng)台,以物聯網技術為基礎,應用大數據處理,可以實現生產過程全覆蓋監控(kòng),係統遇到生產的殘次品會(huì)自動報警,保證出貨(huò)良品率。 智能製造(zào)加工單元機械手裝配(pèi)快換夾具,保證加工效率和實現柔性連接,其裝備流程如圖 2 所示。
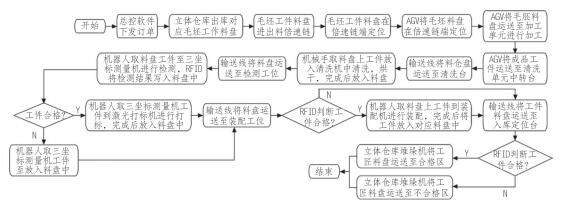
圖 2 裝配流程
3.2 智能製造生產線(xiàn)整體設計
根據工藝分析及功能分析,以工藝流(liú)程為模塊設計的基礎,結合智(zhì)能製造生產線設計規劃(huá),設計架構如圖 3 所示。
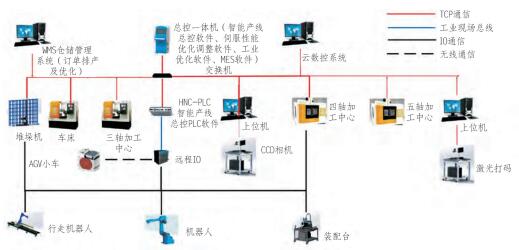
圖 3 網絡拓撲結構
綜合上述分析,此智能(néng)製造生產線布局如圖4所示。 框架分(fèn)析為整體架構的形成奠定基礎,下麵將詳細分析每個模塊設計的原理和定位。
(1) 倉儲物流模塊
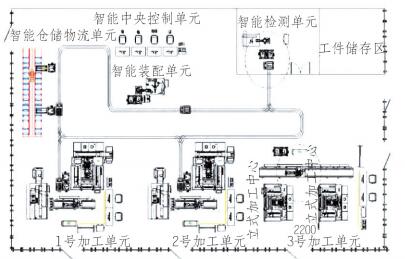
圖(tú) 4 整(zhěng)體(tǐ)布局
倉儲物流模塊根據(jù)功能和總體設(shè)計配置立體料倉、AGV 小車(含調度係統)、輸送設備、物料定位台、RFID 係統、視覺檢測係統等。 能夠實(shí)現物料的自動出入庫、自動運輸、自動檢測智能追蹤等功能(néng),如圖 5 所示(shì)。
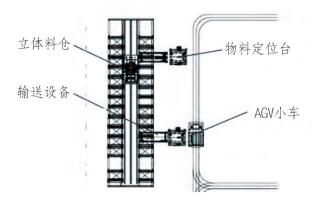
圖 5 智(zhì)能倉儲物流單元
(2)加工模(mó)塊
加(jiā)工單元的配置以工件的(de)工藝設計(jì)為(wéi)基(jī)礎,此生產線加工零件葉輪軸和軸套(tào)類零件(jiàn)均以(yǐ)車床加工中心的組(zǔ)合方式完成加工(gōng),因葉(yè)輪軸(zhóu)在加工中心上(shàng)完成時間較長,設置單獨(dú)的(de)加工單元完成加工中心的工序,同時在加工中心設置機內檢測,便於在加工完成後即檢(jiǎn)測關鍵尺寸,完成第一次合格品篩選,提高生產線加(jiā)工效率。 各單元工序(xù)流程如下 : 1 號加工單(dān)元和 2 號加工單元 : 單(dān)元總控係統根(gēn)據輸送(sòng)物料下(xià)單→工業機器人從物料定(dìng)位台取料→機器人放料到數控車(chē)床→機器人放料到加工中心→ 機內檢測(cè)→放置回物(wù)料定位台→合格進入下一工序(不合格直接返回料倉,入(rù)不合格品庫)。3 號加工單元 : 單元總控係統根據輸送物(wù)料(葉輪軸)下單→工業機器人從物料定位台取料→機器人放料到加(jiā)工中心→機器人從物料定位(wèi)台(tái)取第二件葉輪軸(zhóu)放料(liào)到加工中心→ 加工完成後均進行機內檢測→放置回物料定位台→合格進入下一工序(不合格直接返回料倉,入不合格品庫)。
(3)智能檢測模塊
為了提高加工產品的加工(gōng)精(jīng)度,提高(gāo)後段效率,配置三坐標檢測儀及其輸送設備組成智能檢測單(dān)元。因三坐標檢測環境的特殊性,在此模塊中設置恒溫室(shì)。 工序過程如下 : AGV 小車進入(rù)模塊→物料定位台接(jiē)收物料儀檢測→機器人取料→機器人上料至三坐標檢(jiǎn)測→機器人取檢測完成物料(liào)放入物料定位台→物料輸(shū)送至 AGV 小車→合格進入下(xià)一工序(不合格直接返(fǎn)回料倉,入不合格品庫)。
3.3 智能裝配單(dān)元
葉輪軸和軸套(tào)在此單元完成裝配。根據兩類(lèi)零件的結構特(tè)性選用六關節機器人(rén)完成工件(jiàn)的(de)運轉,設計工作台完成工件的裝配,在工作台上選(xuǎn)用 SCARA 機器人,配置定位機構完成工件的(de)桌麵(miàn)式裝配。
(1) 智能製造生產線中央控製模塊。 此模塊主要依據(jù)中央控製係統實現對智能產線運行的控製、排產、監測(cè)、數據采集分析、定期維護等功能。中央控製係統(tǒng)用於生產製造(zào)產線執行層的生產信息化(huà)管理,包括製造數(shù)據管理(lǐ)、生產調度管理、設備管理、看板管理、生產(chǎn)過程控製、設備數據采集及集(jí)成等管理模塊。整個產線的智能化生產流程控製(zhì)和(hé)管理整體架構如圖 6 所示。
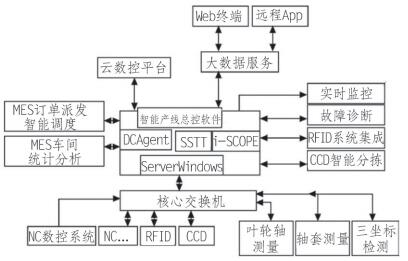
圖 6 智能製造生產線(xiàn)中央控製係統組成模塊
(2) 中央控製係統主要實現立體(tǐ)料倉(cāng)、RFID係統、AGV 小車、上下料機(jī)器人、數控機床、檢測設備、裝配(pèi)設備等的數據采集功能,訂單管理功能,生產排產功能,生產調度功能,生產統計分析功能。 係統打通生(shēng)產、物料(liào)、設備、質量、工藝、資源和人員之間的數據及實體交互,構建完整的工廠運作流程,如圖(tú) 7 所示。
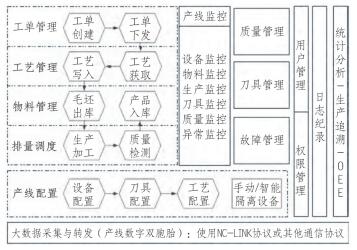
圖 7 中央控製係統框架
4.智(zhì)能製(zhì)造生產(chǎn)線仿真與(yǔ)驗證
4.1 產線仿真
根據產線整體設計規劃圖,通過建模軟件進行三維建模,整體模(mó)型采(cǎi)用輕量化技術,保證大規模場景的流暢顯示,從而建立一個與實際環境1:1 的虛擬環境。 根(gēn)據(jù)設計圖紙進行三維建模能夠顯示整條線體的全貌,主要包含 :(1)設備建模 : 數字化立體倉庫、堆垛機、輸送(sòng)線、AGV、定位台、上(shàng)下料機(jī)器人、加工零件、數(shù)控車床(chuáng)、加工中心、機器人軌道、檢測機(jī)構、裝配機構等設備模型 ; (2) 場(chǎng)景建模 : 虛擬的環境,包含房 屋、加工(gōng)工(gōng)件、其(qí)他輔助設備等。
此虛擬工廠模型采用 3ds Max 建模軟件建模並采用烘焙(bèi)貼出等(děng)進(jìn)行效果處理,通過插件將模型文件導入 PE 引擎中,再通過 PE 引擎對模型整體的效果進(jìn)行調整(zhěng),包含材質、紋理、燈光等(děng)的處理,最終整(zhěng)合得虛擬三維工廠。 葉輪加工單元仿(fǎng)真如圖 8 所示,其加工數據如表 2 所示,其中,葉輪軸允許的讀數(shù)誤差為 ±0.007mm。
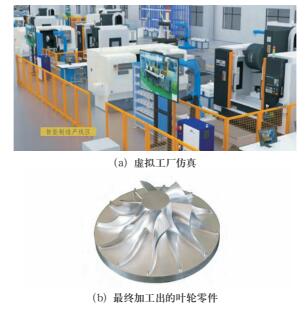
圖 8 葉輪加工單元仿真
由表 2 可知 : 工作流程及加工工藝滿足(zú)要求,產品合格。
表 2 葉輪加工數據(jù)
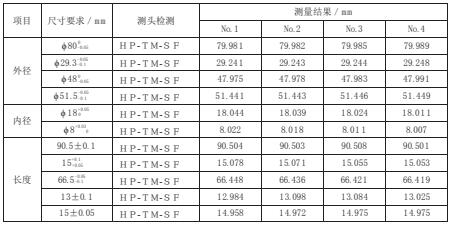
4.2 基於事實數據驅動的虛擬(nǐ)驗證
基於三維虛擬產線,通過與實時數據庫、設備監控係統集成,建立數據驅動的動態仿(fǎng)真機製(zhì)如圖 9 所示,實現生產(chǎn)數據驅動的三維虛擬(nǐ)可視化(huà)監控,並實(shí)現虛擬產線與物理產線的融(róng)合,即通過(guò)在三維虛擬產線漫遊,查看生產(chǎn)計劃執行狀態、設備狀(zhuàng)態、質量狀(zhuàng)態、生(shēng)產曆史、生(shēng)產(chǎn)績效
等實況。
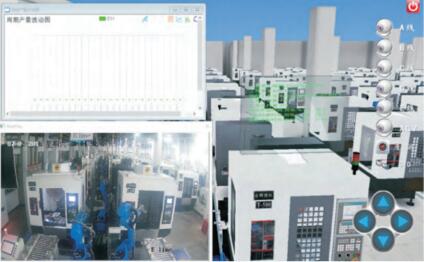
圖 9 智能(néng)製造生產線實地照片
5. 結論(lùn)
文中(zhōng)智能製造生產線的設計以技(jì)術技能為導向,以典型工程問題為基礎,引入設備+軟件的(de)控製應用,結(jié)合當前智能製造技術的發展和應用,將智能製造全產(chǎn)業鏈的關鍵技術要素(sù)包含智能加(jiā)工、智能機器人、智能物流和倉儲、測量、裝配、自(zì)動化工藝、自動搬運和碼垛等進行模塊化組合,融(róng)入工業軟件控製係統,完整體現智能製造(zào)關鍵技術的應用。 同時結合虛實(shí)一體運行結果的對(duì)比實驗,可知此智能製造生產(chǎn)線的設計滿足要求、運行穩定、可達設計目標。
投稿箱:
如果(guǒ)您有機床行業、企業相關新聞稿件發表,或進行資訊合(hé)作,歡(huān)迎聯係本網編輯(jí)部, 郵箱:skjcsc@vip.sina.com
如果(guǒ)您有機床行業、企業相關新聞稿件發表,或進行資訊合(hé)作,歡(huān)迎聯係本網編輯(jí)部, 郵箱:skjcsc@vip.sina.com
更多相關信息
業界視點
| 更多
行業數據
| 更多
- 2024年11月 金屬切削機床產量數(shù)據
- 2024年11月 分地(dì)區(qū)金屬切削機床產量數(shù)據
- 2024年11月 軸承出口情況
- 2024年11月(yuè) 基本型乘(chéng)用車(轎車)產量數據
- 2024年11月 新能源汽車產量數據
- 2024年11月 新能源汽車銷量情況
- 2024年10月 新能源汽車產量數據
- 2024年10月 軸承出(chū)口情況
- 2024年10月 分地區金屬(shǔ)切(qiē)削機床產量數(shù)據
- 2024年10月(yuè) 金屬切(qiē)削機床產(chǎn)量數據
- 2024年9月 新能(néng)源汽車銷量(liàng)情況
- 2024年8月 新能源汽車(chē)產量數據
- 2028年8月(yuè) 基本型乘(chéng)用車(轎車)產量(liàng)數據
博文選萃(cuì)
| 更多