智能製造(zào)在美國、德國、日本有啥不(bú)同?
2017-8-9 來源(yuán):智能製(zhì)造IM 作者(zhě):--
在西方國家有(yǒu)這樣一句話:To live well, a nation must produce well,說明製造業是一個國(guó)家綜合國力最重要(yào)的體(tǐ)現。
在經(jīng)曆了互聯網泡沫和經濟危(wēi)機後,世界各國,尤其是發達國家開始重新意識(shí)到製造業的重要性,也在(zài)重新審視自己競爭力的優(yōu)劣勢。
第四次工業革命(mìng)的到來為各個國家提供了發展和轉型(xíng)的機遇,也麵臨競爭力格局變化的挑戰,智能製造成為各國競爭(zhēng)的新戰場(chǎng)。各國圍繞製造業,都提出了相應的戰略——美國的“國家製造創新網絡”、德國的“工業(yè)4.0”,日本的“工業價值鏈”,當然還有中國(guó)的“中(zhōng)國製造2025”。那麽,這些戰略之間有何差異呢?而形成這些差異的根本原因又是什麽?
1、對知(zhī)識的(de)理解、積累和傳承方式的差異決定了製(zhì)造哲學和文化
對製造業而言,簡單地來講即是“發現(xiàn)問題(比如質量缺陷、精度(dù)缺失、設備故障、成本較高、效率低下等)、了(le)解問題,在此過程(chéng)中獲取信息,並將(jiāng)其抽象化為知識,再利用(yòng)知識去認識、解決和避免問題的過程。”
了解和(hé)解決問題的手(shǒu)段和方法決定了(le)所獲得知識的形式,而將知識抽象化加以運用的過程和形式(shì)則決定(dìng)了知識傳承的形式。這(zhè)個過程可以通過“人來完成”、“數(shù)據(jù)來完成”或是“係統(tǒng)來完成”,這也是決(jué)定一個國家製造哲學的最根本原因。
日(rì)本
“通過組織文化和人(rén)的訓練不斷改善,在知識承載上非(fēi)常依賴人”
日本獨特的(de)克(kè)忍、服從(cóng)和集體觀念文化(huà)也深(shēn)深地影響了日本的製造文化,其(qí)最主要的(de)特征就是通過組織的不斷優化(huà)、文化建設和人的訓練來解決生產係統中的問題。這一點相信國內許多製造企業都感同身受,因為大家在接受精益(yì)培(péi)訓的時候被反複強調的3個方麵就是“公(gōng)司文化”、“三級組織”和“人(rén)才訓練”。最典型的體現就(jiù)是日本在20世紀70年代(dài)提出的以“全生產係統維護(TPM)”為核心的生產管理體係。其核心思(sī)想可以用“三全”來概(gài)括:全效率、全係統和全員參與。實現方式(shì)主要包括在3個方麵的改善:提高工作技能、改(gǎi)進團隊精神和改善工作環境,以致在20世紀90年代以後日本選擇“精益製造(zào)(Lean Manufacturing)”作(zuò)為其轉型方向,而(ér)非“6-sigma質量管理體係”。
日本企業在人才的培養方麵也(yě)是不(bú)遺餘力的,尤其是“雇員終身(shēn)製”文化,將雇員與企業的命(mìng)運緊密聯係在(zài)一起,使得人的經驗和知識能夠(gòu)在企業內部積累、運用和傳承。
日本企業解決問題的方式通常是:發生問題→人(rén)員迅速到現場、確認現物、探究現實(shí)(三現),並解決問題→分析問題產生的原因(yīn),通過改善來避免問題(tí)。最終(zhōng)的知識落在了人的身上,人的技能提升之後,解決和避免問題的能力也(yě)就上升了。
因(yīn)此對(duì)於日(rì)本企業(yè)而言,員工是最重要的價值,對人的信任遠(yuǎn)勝於對設備、數據和係統的信任,所有的自動化或是信息化建設也都是圍繞著幫助人去工作為目的,所以日(rì)本企業從來不會談機器換人或是無人(rén)工廠。如果中國想(xiǎng)要(yào)學習工匠精神,那麽最應該借鑒的是日(rì)本孕育工匠的組織文(wén)化和製度(dù)。但是這樣的文化在近幾年遇到了一個(gè)十(shí)分巨大的挑戰,就是日(rì)本的老齡化(huà)和製造業年輕一(yī)代大量短缺的問題(tí),使得沒有人能夠去傳承這些(xiē)知識。
日本也意識到了自己(jǐ)在數據和(hé)信息係統方麵的(de)缺失,開始在這些(xiē)方麵發力。這一點在日(rì)本的“工業價值鏈產業聯盟”的構架和目標上能夠清晰地看到。該聯盟提出的19條工作項目中(zhōng)有7條與大數據直接相關。可以說日本的轉型戰略是應(yīng)對其人口結構問題和社會矛盾的無奈之舉,核心是要解決替代人(rén)的知識獲取和傳承方式。
但日本(běn)在(zài)轉型過程中同樣麵臨著(zhe)許多(duō)挑戰:首先是數據積累的缺失,使得知識和經(jīng)驗(yàn)從人轉移到信息化體係和(hé)製造係統的(de)過程中(zhōng)缺少了依據和判斷標準。其次是日本工業企業保守的文化、造成軟件和IT技術人才的(de)缺失(shī),正如日本(běn)經產省公布的《2015年製造白皮書》中所表達的憂慮:“相對於在德國和美國正在加快的製造業變革,現在日本企(qǐ)業(yè)表現(xiàn)出重視軟件的姿態。”
德國
“通過設備和生產係統的不斷升級,將知識固化在設備上”
德國的先進設備(bèi)和自動化(huà)的生產線(xiàn)是舉世聞名的,可以說在(zài)裝備製造業的實力(lì)上有(yǒu)著傲視群雄的資格。同(tóng)時德國人嚴謹的風格(gé),以及其獨特的“學徒(tú)製”高等(děng)教育模式,使得(dé)德國製造(zào)業的風(fēng)格非常務實,理論研究(jiū)與工業應用(yòng)的結合也最緊密(mì)。然而德國也很早(zǎo)就麵臨勞動力短缺的間題,在2015年各國競爭力指數的報告中,勞動力是德國唯一弱於創新(xīn)驅(qū)動型國家平均水平的一項。因此,德國不得(dé)不通過研發更先進的(de)裝備和高度(dù)集成自(zì)動的生產線來彌(mí)補這(zhè)個不(bú)足(zú)。
德國的製造業解決問題的邏輯是:發(fā)生問題→人(rén)(或裝(zhuāng)備)解決問題→將解決(jué)問題(tí)的知識和流程固化到裝備和生(shēng)產(chǎn)線中(zhōng)→對相似問題自動解(jiě)決或避免。
舉個比較直觀的例子(zǐ)來比較日本和德國解決問題方式的不同:如果生產線上經常(cháng)發生物料分揀(jiǎn)出錯的現象,那麽日本(běn)的解決方式很有可能是改善物料辨識度(顏色等)、員工訓練,以及設(shè)置(zhì)複查製度。而德國則很可能會設計一個射頻識別(RFID)掃(sǎo)碼自動分揀(jiǎn)係統,或是利用圖像識別+機械手臂自動進行分揀。
又比如,德國很早就(jiù)將誤差補償(cháng)、刀具壽命預測、多軸同步(bù)性算法、主軸震頻補(bǔ)償等(děng)解(jiě)決方式以功能包的形式固化到了機床中,因(yīn)此即便是對製造工藝和操作並不熟練的工人也能(néng)夠生(shēng)產出可靠的產(chǎn)品。也(yě)正是這個原因成就(jiù)了德國(guó)世界第一的(de)裝備製造業大國地位(wèi)。
除了(le)在生產現場追求問題的自動解決之外,在企業(yè)的管理和經營方麵也能夠看到其盡力減少人為影(yǐng)響因素的努力。比如最好的ERP、MES、APS等軟件供應商都來自德國,大量的信息錄入和計劃的生成及追溯通過軟件自動完成,盡量減少人為因素帶來的不確定性。
然而,德國同樣對數據的(de)采集缺少(shǎo)積累,因為在德國的製造係(xì)統中對故障(zhàng)和(hé)缺陷采用零容忍的態度,出現了問題就通過裝備端的改造一(yī)勞永逸(yì)地(dì)解決。在德國(guó)人的意識(shí)中不允許出現問題(tí),也就自然不會由問題產生數據,最直接的表現就是找遍德國的(de)高校和企業,幾乎沒有人在做設備預診與健康管理(lǐ)(PHM)和虛擬測量等質量預測性分析。另外由於德國生產線的高度自動化和集(jí)成化,使得其整體設備效率(OEE)非常穩定,利(lì)用數據進行優化的空間也較小。
德國依靠裝備和工業產品的出口獲得(dé)了巨大的經濟回報,因為產品優秀的質量和可靠性,使得德(dé)國製造擁有(yǒu)非常好的品牌口碑。然而德國近年來也(yě)發現了一個問題,那就是(shì)大多數工(gōng)業產品本身隻能夠賣一次,所以賣給一個客戶(hù)之後也就少了一個客(kè)戶。同時,隨著一些發(fā)展中國家的裝備(bèi)製造和工業能力的崛起,德國的市場也在不斷被擠壓。因此,在2008—2012年的5年時間裏,德(dé)國工業出口幾乎沒有增長。由此,德國開始意識到賣裝備不如賣整(zhěng)套的解決方案,甚至同時如果還能(néng)夠賣服務就更好了(le)。
於是,德國提出的工業4.0計劃,其背後是德國在製造係統中所(suǒ)積累的知識體(tǐ)係集成後所產(chǎn)生的(de)係統產品,同時將德國製造的知識以軟件或是工(gōng)具包的形式提供給客戶作(zuò)為增值服務,從而實現在客戶身上的可持續的盈(yíng)利能力。這一點從(cóng)德國的工(gōng)業(yè)4.0設計框架中能夠十分明顯地看(kàn)到,整個框架中的核心要素就是“整合”,包括縱向的整合、橫向的整(zhěng)合和端到端(duān)的整合等,這簡直太像(xiàng)德國製造體係的風格了,既是德國所擅長的,也為其提供增值服務提供(gòng)了途徑。所以第四次工業(yè)革命中德國的主(zhǔ)要目的是利用知識進一步提升其(qí)工業產品出口的競爭力,並產生直接的經濟回報。
美國
“從數(shù)據和移民(mín)中獲得新的知識(shí),並擅長顛覆和重新定義問題”
與日本和德國相比,美國在解決問題的方式中(zhōng)最注重數據的作用,無(wú)論是客戶的需求分析、客(kè)戶關係管理(lǐ)、生(shēng)產過程中的質量管理、設備的(de)健康(kāng)管理、供應鏈管理、產品的服役期管理和(hé)服務等方麵(miàn)都大量地(dì)依靠數據進行(háng)。這也造成(chéng)了20世紀90年代後美國(guó)與日本選擇了兩種不同的製造係統(tǒng)改善方式,美國企業普遍選擇了非常依賴數據的(de)6-sigma體係(xì),而日(rì)本選擇了非常依賴人和製度的精益管理體係。
中國的製造企(qǐ)業(yè)在2000年以後的質量(liàng)和管理改革上,大多選擇了精益體(tǐ)係這條道路,一方麵因為中國與日本文化的相(xiàng)似性,更多的還是因為中(zhōng)國企業普遍(biàn)缺乏數據的積累和信息化基礎,這個問題到現在也(yě)依然沒(méi)有解決(jué)。
除了從生產係統中獲取數據以外,美國還在21世紀初提出了“產品全生命周期管理(PLM)”的概(gài)念,核心是對所有與產品(pǐn)相關的數據在整個生命周期內(nèi)進行管理,管理的對象即為產品的數據,目的是全生命周期的增值服務和實現到設計(jì)端的數據閉環。
數據也是美國獲取知識的最重要途徑,不僅(jǐn)僅是(shì)對(duì)數據(jù)積(jī)累的重視,更(gèng)重要的是對數據分析的重視,以及企業(yè)決策從數據所反映出來的事實出發的管理文(wén)化。從數據中挖掘出的不(bú)同因素之間的關聯性、事物之(zhī)間的因果關係,對一個現象定性和定量的描述和某一個問題發生的過程等,都可以通過分析數據後建立的模型來(lái)描述,這也是知識形成和傳承的過程。
除了(le)利用知識去解決問題以外,美國也非常擅長(zhǎng)利用知識進行顛覆(fù)式創新,從而對問題進行重新定義。例如美(měi)國的航空發動機製造業,降低發動機的油(yóu)耗(hào)是需(xū)要解決的重要問題。大多數企業會從設計、材料、工藝(yì)、控製優化(huà)等角度去解(jiě)決這個問題,然而通用電(diàn)氣公司(GE)發現飛機的油耗與飛行(háng)員的駕駛習慣以及發動機(jī)的保養情況非常相關,於是(shì)就(jiù)從製造端跳出來轉向運維端去解決這(zhè)個問題,收到的效果比從製造(zào)端的改善還要(yào)明顯。這也就是GE在推廣工業互(hù)聯網時所提出的“1%的力量(Power of 1%)”的依(yī)據和信心來源,其實與製造並沒有太大的關係。所以美國在智能製造革命中的關鍵詞依然是“顛(diān)覆”,這一點從其新(xīn)的戰略布局中可以清(qīng)楚地看到,利用工業互聯(lián)網顛覆(fù)製造業的價值體係,利用數字化、新材料和新的生產方式(3D打印等)去顛覆製造業的生產方式(shì)。
2、製造(zào)中價值鏈的位量是競爭力的決定性(xìng)因素
我們從日本、德(dé)國和美國三(sān)者之(zhī)間文化差異性方麵分析(xī)了三個國家對智能製造革命的理解(jiě)、側(cè)重點和目的(de)的不同。除此以外(wài),這些國家的競爭力差異也是造成其戰略方向差異的關鍵因素,其中各國(guó)在製造價值(zhí)鏈的分布和未來布局的不同起了決定性的作用。
生產活動中(zhōng)的價值要素分布(bù)從上遊(yóu)到下遊依次是:想法創新與需求創造→原材料(liào)與基礎使能技術(shù)→關鍵裝備與核心零部件(jiàn)→生產過程與生產係統→產品和服務。
在整個價值要素的分布中,中國在生產過程與生產(chǎn)係統這兩(liǎng)個環節具有優勢(主要體現(xiàn)在勞動成(chéng)本和生產(chǎn)能力方麵),但是在其它各個環節中均處於劣勢(shì)。
那麽,如果進行橫向比較,世界各主要國家在生產活(huó)動中價值要素的地位,以及(jí)未(wèi)來(lái)改革的布(bù)局是怎樣的?
美國
“牢牢占據生產要素的上遊,努力向下遊延伸”
美國在生產活動要素的分布中,在想法創新和需求(qiú)創造、原材料(liào)和使能(néng)技術,以及產品增值(zhí)服務(wù)端,具有明顯優勢。美國工業係(xì)統(tǒng)的核心競爭力主要來源於“6s的生(shēng)態體係”:
(1)航天航(háng)空:為美國製造業積累了大量技術紅利,成為美國工業(yè)係統中基礎使能技術(shù)最主要的(de)來源。
(2)半導體:近(jìn)年來在低耗能半導體(tǐ)材(cái)科的研發投入巨大,在未來智能化技術的核(hé)心(xīn),低耗能高性(xìng)能芯片技術上具有明顯優勢。
(3)頁岩氣:布局未來新(xīn)能源和清潔能源(yuán)領域,已成為美國最主要的替代能源。
(4)智能(néng)化服務創造經濟(jì):借助美國在計算機和信息化技術領域(yù)的優勢,在利潤最高的(de)製造業服務端進行布局。
(5)矽穀(gǔ)為代表的創(chuàng)新精神:通過不斷創新挖掘用戶的潛在需求,從而不斷獲得新的市場和商業機會的藍海(hǎi)。
(6)可持續人才資源(yuán)。
在第四次工業革命的戰(zhàn)略布(bù)局方麵,美國白宮(gōng)在2012年3月提出了“國家製造創新網絡計劃”,在製造業的4大領域(yù)建立9個研究創新中(zhōng)樞(如下圖)。
智能製造在美國、德國、日(rì)本有啥不同?
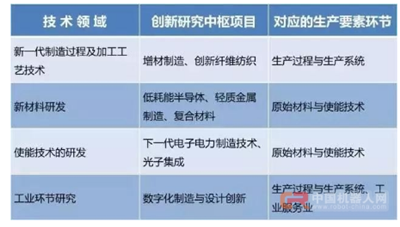
分析美國‘6S’生態係(xì)統和製造(zào)業發展(zhǎn)戰略布局,我們不(bú)難發現,美國力圖在生產係統最基礎的原料端(能源和材料)、工業(yè)產品的使用服務端(互聯網技術和ICT服務(wù)),以及不斷(duàn)由創新驅動的商業模式端,牢牢掌握住(zhù)工業價值鏈當中價值含量最高的幾部分,這樣即便德(dé)國(guó)的製(zhì)造設備再先(xiān)進、中國的製造(zào)係統再高(gāo)效,都可(kě)以從源頭和價值的投放端確保其競爭力的核心(xīn)優(yōu)勢。
德國
“充分發揮在(zài)關鍵裝備與零部件、生(shēng)產過程與生產係統領域的技術優勢,通(tōng)過(guò)服務增強盈利能力與競爭力(lì)”
德國在關鍵裝備與核(hé)心零部件,以及(jí)生產過程與生(shēng)產(chǎn)係統兩個環節上具有十分明顯的技(jì)術優勢,這主要得益於以中小企業為核心(xīn)的隱形冠軍企業,以及德國務實(shí)的學徒製雙元教育,這兩者為德國工業提供了(le)紮實的基礎(chǔ),是德國製造難以被撼動的地基。
德國的隱形冠軍企業幾乎不(bú)被外界所關注,它們規模都不大,但卻在其領域占領(lǐng)著很高的(de)市場份額,在全球位列前(qián)三。這些中小企業占據了德(dé)國出口(kǒu)總量的70%,它(tā)們的銷售回報率均超過德國(guó)普(pǔ)通企業的兩倍,擁有高水平的研發能力與技術創新能力,注重產品價值與客戶的貼合、高質量高效(xiào)率的製造能力和精益化、柔性化的全球化高效運營體係,它們中的很大一部分已經傳承了百年。
高素質的(de)技術工(gōng)人和工程技術專業人才曆來被看作是德國經濟發展的支注,是(shì)“德國(guó)製造”產品的質量保障。旨在培養(yǎng)專業技術(shù)工人的職業教育在德國社會發展中承擔著重(chóng)要的角色,並形成了一套相對完備而(ér)且不斷調整的法規體係,保障了以(yǐ)雙元製為(wéi)主要特(tè)征的職業教育長期穩定的發(fā)展。學徒(tú)不僅(jǐn)要在生產(chǎn)車間裏跟(gēn)隨師傅學習實用技術,還要到學校(xiào)裏學習必要的理論知識。在德國,每年約計60萬(wàn)年輕人開始接受雙元製職業教(jiāo)育,約占同齡人(rén)數的三分之二。
德國是一(yī)個工業產品外向型的國家,由(yóu)於國內市場較小和自身需求的薄弱,其工業產品幾(jǐ)乎全(quán)部用於出口,也因此成就了德國製造業設備出口第一大國的地位。然而,由於以“金磚四國”為(wéi)代表的新興經濟體已基本完成了工業化,東南亞(yà)和非洲國家的新一(yī)輪增長(zhǎng)引擎還沒有完全開啟,導致了德國的工業裝備產品需(xū)求停滯不前(qián)。從(cóng)這幾年德國的工業出口總(zǒng)值上來看,幾乎沒有任何的增長(zhǎng),這(zhè)也從一定程度上影響了德國的經濟發(fā)展。由此(cǐ)可見,德國提出工(gōng)業(yè)4.0的核心目的主(zhǔ)要有兩方麵:
一是(shì),增強德國製造的競爭力,為德國的(de)工業設備出口開拓新的市場;
二是,轉變以(yǐ)往隻賣(mài)設備而服務性收(shōu)入(rù)比重較小的狀態,將重心從產品端向服務端轉移,增強德國工業產品的持續盈利能力。
日本
“雖然在產品這個環節中丟失大量市場,但產業競爭力(lì)在向上轉移”
以往(wǎng)日本製造的核心競爭力主要在(zài)於(yú)生產過程與生(shēng)產係統、產品以及服務端(duān)。近兩(liǎng)年來,日本兩個最強勢的傳統產業,汽車製造和消費(fèi)電子產業中的市場份額(é)不斷被韓國、美(měi)國和中國占據,看似在產品端的優勢已經喪失殆盡。然而在《2015年(nián)全球創新創業百強》榜單(dān)中,日本以(yǐ)40家入圍(wéi)企業成為全球最具創新(xīn)力的國家。同時,在2015年的《全球(qiú)製造力競爭指數》報(bào)告中,日本也由前一年的第10位上升至第4位(wèi)。其實,日本在消費電子領域的衰退(tuì)背後是日本創新方向的轉(zhuǎn)變,日本開始在上遊的原材料及使能技術和關鍵裝(zhuāng)備及(jí)關鍵零部(bù)件領域擁有更多的話語權。
例如鬆下在失去電氣行業的優勢後,在汽車電子、住宅(zhái)能源和商務解決方案等領域找到了新的發展機會,同(tóng)時也成為世界上最先進的電池生(shēng)產商,特斯(sī)拉電動車(chē)使用的就是鬆(sōng)下18650電池。索尼在喪失消費電子領域老大的地位後,在醫療領(lǐng)域(yù)取得突破(pò),已經占據了醫療內窺鏡全球80%以上的份額(é)。夏普(pǔ)也將核心業務轉向智慧醫療、智能住宅、食(shí)品、水、空氣安(ān)全以及教育產業。在日本(běn)發(fā)布的《2015年製造業白皮書》中,將人工(gōng)智能和機器人領域作為重點發展方(fāng)向,同時也將加強在(zài)材料、醫療、能源和關鍵零部件領域的投入。
投稿箱:
如果您有(yǒu)機床行業、企業相關新聞稿件發表,或進行資(zī)訊合作,歡(huān)迎聯係本網編輯部, 郵箱:skjcsc@vip.sina.com
如果您有(yǒu)機床行業、企業相關新聞稿件發表,或進行資(zī)訊合作,歡(huān)迎聯係本網編輯部, 郵箱:skjcsc@vip.sina.com
更多相關(guān)信息
業界視點
| 更多
行業數據
| 更多
- 2024年11月 金屬切削(xuē)機床產(chǎn)量數據
- 2024年11月 分地區金屬切削機(jī)床產量(liàng)數據
- 2024年11月 軸承出口情況
- 2024年11月 基本型(xíng)乘用車(chē)(轎車)產量數據
- 2024年11月 新能源汽車產量數據
- 2024年11月 新能(néng)源(yuán)汽車銷(xiāo)量情況
- 2024年10月 新能源汽車產量數據
- 2024年10月 軸承出口情況
- 2024年10月 分地區金屬切削機床產量數據
- 2024年10月 金屬切削機床產量數據
- 2024年9月 新能源汽車銷量情況
- 2024年8月 新(xīn)能(néng)源汽車(chē)產量數據
- 2028年8月 基本型(xíng)乘用車(轎(jiào)車)產量(liàng)數據