三坐(zuò)標測量機測量同軸(zhóu)度的方(fāng)法討論
2023-7-14 來源(yuán): 上海航天控製技術研究所 作(zuò)者:鄒昊生 馮加(jiā)印
【摘 要】: 三坐標測(cè)量機作為一種先進的檢測設(shè)備 , 具有自動化、高效率、高精度的特點 ,在(zài)科研生產活動中發揮著重要作用。然(rán)而在同軸度(dù)測量中 , 經常出現測(cè)量值與理論值偏差大、測量重複性差的問題。本文分析了同軸度誤差(chà)產生原因 , 介紹了直接測量法、公共軸(zhóu)線法、直(zhí)線度法、投影法等測量方法(fǎ) , 指出了每種測量方法的特點和(hé)使用環境 , 並對同軸度標注、檢測提出了建議。
【關鍵詞】: 同軸度 ; 三(sān)坐標測量 ;
測量誤差同軸度檢測是尺寸測量的重點之一。針對不同類型的零件,GB/T1958—2017給出了不同的解決方案(àn) , 詳細介紹五種(zhǒng)典型同軸度檢驗操作示例。但(dàn) GB/T1958-2017給出的方案均為傳統的形位誤(wù)差(chà)測量方(fāng)法 , 測(cè)量過程中需要借助直板尺、平板、芯軸等輔助工具進行。傳統測量方案不僅需要額外硬件投資 , 還耗時耗力 , 測量誤差(chà)影響因素(sù)較多(duō) , 對於一些大型或不(bú)規則零件 , 采用常規方法測量同軸度更難以實現。
三坐標測量機可以在保證檢測工作效率的前提下 , 檢 測(cè)不(bú)同零件(jiàn)的具體尺寸、精度(dù) , 而被廣泛(fàn)的(de)應用(yòng)在各個行業。 但在實際測量過(guò)程中 , 由於設計意圖傳遞不準(zhǔn)確 , 操(cāo)作人員(yuán)對三坐標測量原(yuán)理不到位 , 難以正確地選擇測量方法 , 容(róng)易(yì)造成測量誤差大、測量重複性差等問題。針對這一現象 , 為保證檢測結果真實、準確、有效 , 本文對三坐標測量方法的原理進行分(fèn)析 ,並對已有檢測方法進行說明、改進 , 力求得到更加(jiā)科學合理的檢測(cè)結果。
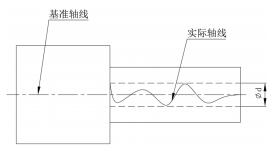
圖 1 同軸度誤差
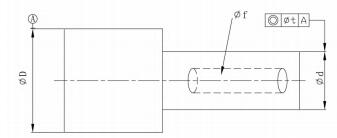
圖(tú) 2 同軸度公差
1. 同(tóng)軸度坐標測量原(yuán)理
1.1 同軸度定義
同軸度誤差(chà) : 要求在同一直線上的兩根軸(zhóu)線 ,實際生產(chǎn)加工(gōng)過程(chéng)中會發生偏離 , 它(tā)們之間偏離量的值 , 如圖 1 所示 ,Φd 為同軸度(dù)誤差。
同軸(zhóu)度公差 : 公差值前(qián)標注(zhù)符(fú)號 Φ, 限製被測軸線在 以(yǐ)基準軸線為軸線、以 Φf 為直徑的區域內 , 如圖 2 所示 , Φf 為同軸度公差。
1.2 同軸度(dù)誤差解析模型
實際測量中 , 首先應確(què)定基準軸線。基準軸線是通過測(cè)量基準(zhǔn)圓柱麵上的(de)輪廓要素(sù) , 擬合出的具有理想形狀的直線。 具體方法如下 :
(1) 在基準圓柱麵上取多個與基準軸垂直的截麵 , 采集截麵(miàn)數(shù) n ≥ 2;
(2) 對各截麵(miàn)進行測量 , 每個截麵上均勻(yún)采集 m 個離散點 , m ≥ 3, 采集點數越(yuè)多(duō) , 截麵越接近於實際輪廓形狀。
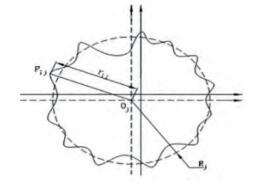
圖 3 第 j 個截麵上的采樣點
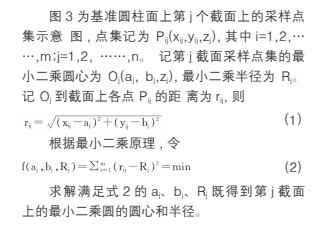
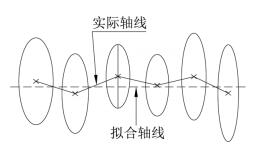
圖 4 各采樣截麵擬合圓心與最小二乘軸線
(3) 連接各截麵上的(de)圓心 Oj 行成一條 3D 折線(xiàn) , 如圖 4 所示(shì) , 選取截麵數越多 , 則該折線越近似基(jī)準圓的實際軸線(xiàn) , 記其最小二乘軸線L的方向向量為(wéi) ,L與XOY的交點為J0(x0,y0,0), 記(jì) Oj 到 L 的距離為 dj, 則
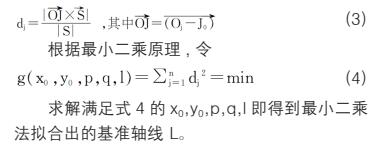
(4) 在被測圓柱麵上取 w 個截(jié)麵 , 記各截麵最小(xiǎo)二乘擬合(hé)圓(yuán)心為 ck,k=1,2,……,w。各圓心 ck 到基準(zhǔn)軸線 L 的(de)距離(lí)為 distk, 則同軸(zhóu)度誤差 ε 為(wéi)

1.3 三坐標測量同軸度誤(wù)差的實現
使用三坐標(biāo)測量機時 , 一般首先測量基準元(yuán)素 , 並以此為基礎 , 建立工件坐標(biāo)係 ; 然後(hòu)測(cè)量其他幾何元素 ; 最後得出測量結果。三坐標測量機進行測量時 , 一般按如下步驟進行 :首(shǒu)先 , 建立零件基準 , 並按此基準建立零件(jiàn)坐標係。同軸度基準的建立 , 應根據零(líng)件的圖紙標注來(lái)確定,可參考 GB/T1958—2017的規定。一(yī)般情況下 , 同軸度(dù)測量時選擇內(nèi)孔(kǒng)或外圓柱麵(miàn)的軸線作為基準軸。建(jiàn)立坐標係時(shí) , 至少需要采集兩個截(jié)麵圓 , 每個截麵圓至少選取 3個 點 , 各點應均(jun1)勻分布 , 三坐(zuò)標測量機(jī)軟件(jiàn)根據內(nèi)部算法 , 自動生成一條(tiáo)軸線 , 然後作為坐標(biāo)係的基準軸。
其次 , 采用同樣的方法測量被測要素 , 被測要素各截麵應均勻分(fèn)布 , 並盡可能覆蓋被測要素。測量完(wán)畢 , 最終生成一條(tiáo)被測軸線。最後 , 得出測量(liàng)結果(guǒ)。測量結果一般由三坐標測量機(jī)軟件自動計(jì)算 ; 還可以(yǐ)按最小條件 ,通過被測要素與基準要(yào)素的關係手動計算。
按上述三坐標測量步驟 , 當被測要(yào)素與基準要素相距較遠、兩者又比較短時(shí) , 理想值與測量值會有很(hěn)大偏差 , 測量重複性也很差。
2. 測量誤差源探(tàn)究
測量(liàng)結果會受到人為因素、設備係統(tǒng)誤差因素、測量(liàng)方法因素等的(de)影響 , 從而導(dǎo)致(zhì)測量結果與真(zhēn)實數據(jù)之間存在差(chà)值(zhí) , 即測量誤差。一般情況下極限測量總誤差允許占給定公差值(zhí)的 10%~33%。測量誤差越小(xiǎo) , 測量結果越接近真值。因此(cǐ) , 在確定測(cè)量方案前 , 首先應評定測量 誤差來源(yuán) , 采取措施消(xiāo)除、減(jiǎn)小測(cè)量誤差至合理範圍。
產生測(cè)量(liàng)誤差(chà)的主要原因包括 : 測量設備本身的係統性誤(wù)差 ( 如設備結構(gòu)誤差、軟件(jiàn)計算誤差等 )、測量條件(jiàn)引起的(de)誤差 ( 如地麵振動、裝夾方式、溫度條件(jiàn)等引起的誤差 )、測量方(fāng)法引(yǐn)起的誤差。由於三坐標測量機各部件有較高的剛度 , 變(biàn)形小 , 測量環境要求較高等原因 , 測量機係統誤差、環境條件引起(qǐ)的誤差可(kě)以忽略不計。本文主要研(yán)究測(cè)量方法引起的誤差。在實際測量過程中 , 直接采用測量軟件進行計算 , 測量結果(guǒ)往往與理論值(zhí)有(yǒu)很大差距(jù)。
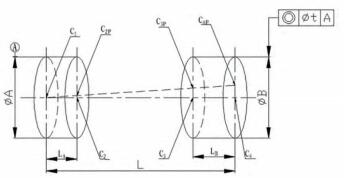
圖(tú) 5 基準軸線延長至被(bèi)測要素時引入測量誤(wù)差示意(yì)圖
如圖 5 所示 , 在基準 A 兩端覆蓋最大(dà)基準範圍的位 C1、C2 兩個截麵圓作為基(jī)準軸線 ; 同理 ,在被(bèi)測圓柱麵上取 C3、C4 兩個截麵圓。理想(xiǎng)狀(zhuàng)態下 , 基準軸線 C1C2 和被測軸(zhóu)線 C3C4 應為同一條(tiáo)直線 , 同軸度理(lǐ)論值為 0。但是 , 由於測量機的係統誤差、人為因素、環境因(yīn)素等的影響 , 基準軸線存在測量偏(piān)差C2C2P, 在計算同軸度時 , 根據同軸度定義 , 基準軸為(wéi) C1C4P, 同軸度為 C3C4 與 C1C4P 之(zhī)間(jiān)的最(zuì)大距離 , 由三角形相(xiàng)似性原理得 :
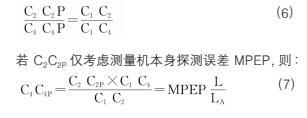
上述分(fèn)析(xī)說明 , 當被測要(yào)素與基準要素(sù)本身較短、距 離較遠時 , 測量誤差會被放大。 因此 ,某些情況下 , 使用三坐標測量軟件直接測量、計算同軸度時(shí) , 應對測量誤差進行評定(dìng) , 確保測(cè)量誤差不會被放大。
采用 GB/T1958-2017 中所述的傳統測量方法 , 可借助芯棒 , 若(ruò)芯棒(bàng)與(yǔ)孔(kǒng) A、孔 B 正確裝配 ,則孔 B 的同軸度合格 , 若不能正確裝配 , 則同軸度超差。但借助芯棒 , 無法確定同軸度具體數值 ,隻(zhī)能給出(chū)合格與否的結論(lùn)。
在實際測量過程中(zhōng),為減(jiǎn)小(xiǎo)三坐(zuò)標測量誤差,一方麵 , 應盡量增加基準(zhǔn)要素、被測要素截麵數、截麵間距、增加各截麵的取點數、各點之間(jiān)盡量均勻分布 , 以減小(xiǎo)基準(zhǔn)軸線、被(bèi)測(cè)軸線偏(piān)離程度(dù) ,逼近實際形狀 ; 另一方麵 , 當圖紙與技術條件中無特殊要求說明時(shí),則(zé)以尺寸較大的方向為基準。
3.合理(lǐ)選擇(zé)測量(liàng)方法
實際測量過程中 , 同軸度公差(chà)各不相同 , 在采用三坐(zuò)標測量時應根(gēn)據基準要素作(zuò)用範圍、零件設(shè)計(jì)意圖、零(líng)件具體形態等具體條件 , 從以下方案(àn)中選擇合適的測量方法。
3.1直接測(cè)量法
當基準(zhǔn)要素作用範圍較長 ( 如圖(tú) 6 所示 ) 或基準作(zuò)用範圍延長引起的誤差較(jiào)小 , 即公式 (7)的(de)值(zhí)較小 , 在可接受範圍內時 , 可由三坐標測量機直接計算同(tóng)軸(zhóu)度誤差。

圖 6 被測要素在基準要(yào)素作用範圍內
3.2公共軸線法
當被測要素法和基準要素相距較(jiào)遠時 , 如圖5 所示 , 可以采用公共軸線法。
具體檢(jiǎn)測方案 : 在(zài)被測要素、基準要素上選取多個截麵圓 ; 然後模擬零件裝配狀態 , 將這些截麵圓心擬合成(chéng)一條 3D 公共軸線 ; 最後以該 3D公共軸線為基準 , 分別計算 基準要素和被測(cè)要素同(tóng)軸度 , 取最大值作為(wéi)該零件的同軸度誤差。當被測要素與(yǔ)基準要素距離較遠時 , 該方案效果非常明顯。
公共軸線法是模擬零件實際裝配狀態。 在公差標注時 , 為準確傳遞設計意圖 , 可以參考GB/T1182-2008 的 標注方式 , 如圖 7 所示。
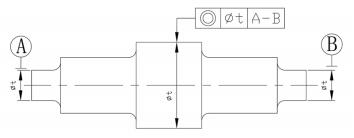
圖 7 基準標注為公共軸線
3.3測直線(xiàn)度法
實際測量工(gōng)作中 , 會遇到由 3 個及(jí)以上截麵(miàn)孔構成的孔(kǒng)係 , 尤(yóu)其當單個孔(kǒng)工作截麵較短時 , 同(tóng)軸(zhóu)度誤差(chà)測量更加困難。此(cǐ)時可以用直線(xiàn)度公差值代替給出的同軸度的公差(chà)值。
具(jù)體檢測方案(àn) : 根據各孔軸線長度 , 確定該孔采集(jí)截麵圓的數量 , 軸線越長 , 截麵圓越多 ;所有孔元素截麵圓采(cǎi)集完(wán)成後 , 把所有截麵圓心擬合成一條(tiáo) 3D 軸線(xiàn) ; 計算該 3D 軸線的直線度 ; 直線度值的 2 倍作為孔係同軸度誤差。圖 8可按照此評價方法進行檢測。
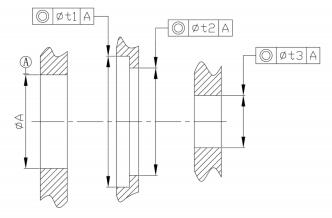
圖 8 孔係同軸度(dù)測量示意圖
從本質上來說 , 直線度法與公共軸線法都是模擬芯軸穿過孔的零件(jiàn)裝(zhuāng)配狀態 , 能較好地反應零件裝配性。軸心連(lián)線的(de)直線度能控製各孔軸心的偏(piān)移量(liàng) , 進(jìn)而影響零件的裝配性能 , 因此 , 孔係各(gè)軸心連接線(xiàn)的直線度能反應零件同軸度。截麵孔軸線越短 , 各孔間距越大 , 該測量方案效果越好。
3.4 投影(yǐng)法(fǎ)
實際生產過程中 , 孔軸裝配也(yě)會用零件端麵進行定位 , 若(ruò)軸間距 ( 隻有(yǒu)一個軸(zhóu)或孔時 , 則(zé)是軸長或孔(kǒng)長(zhǎng) ) 大於端麵尺寸時 ,則以軸線為基準(zhǔn) ;反之 ,則以端(duān)麵(miàn)為基準。如圖 9 所示 , 基準要素與被測要(yào)素軸長均小於端麵尺寸 , 此時可以將(jiāng)端麵作為(wéi)基準平麵 , 將被測要素、基準要素投影到基準平(píng)麵上 , 取其圓(yuán)心(xīn)距離的兩倍作(zuò)為零件的同軸度。
這個基準平麵必須與被測(cè)要素、基準要素垂直誤差不大(dà)於 0.02。可以(yǐ)將(jiāng)基準要素、被測要素上(shàng)任一截麵圓投影到基準平麵上 , 以同心度代替同軸度。
針對這種端麵定位的(de)同軸(zhóu)度公差 , 為(wéi)避免不必要的(de)理(lǐ)解差異、更準確的(de)傳遞設計意(yì)圖 ,在(zài)公差標注時可以參考 GB/T1182-2008按兩基準體(tǐ)係標注 , 如圖 9 所示。
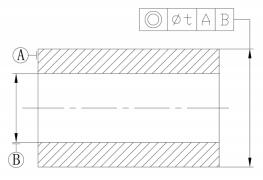
圖 9 兩基準體係標(biāo)注
4. 結語
檢(jiǎn)測方法(fǎ)多種多樣 , 應根據不同零件的結構(gòu)、圖紙設計要求 , 來確定合理的(de)測量方案。確定測量方案時 , 還應充分考慮並減小各種因素造成的測量誤差 , 保證測量的準確性(xìng)。在進行零件設計時 , 應(yīng)遵守相關標準的要求 , 準確表達設計意圖(tú)。隻有這樣 , 才能更準確的把握設計意圖 , 得到精(jīng)確的檢測結果 , 真實反映被測件的狀態(tài)。
投稿箱:
如果您有機床行業、企業相關(guān)新聞(wén)稿件發表,或進行資訊合作,歡迎聯係本網編輯(jí)部(bù), 郵箱:skjcsc@vip.sina.com
如果您有機床行業、企業相關(guān)新聞(wén)稿件發表,或進行資訊合作,歡迎聯係本網編輯(jí)部(bù), 郵箱:skjcsc@vip.sina.com
更多相關(guān)信息
業界視點
| 更多(duō)
行業數據
| 更(gèng)多
- 2024年(nián)11月 金屬切削機床產量數據
- 2024年11月 分地區金屬切削機床產量數據
- 2024年11月 軸承出口情況
- 2024年11月 基本型乘用車(轎車)產量數據
- 2024年11月 新能源汽車產量數據
- 2024年(nián)11月 新能源汽車銷量情況
- 2024年10月 新能源汽車(chē)產量數據
- 2024年10月 軸承出口情況(kuàng)
- 2024年10月 分(fèn)地區金屬切削機床產量數據
- 2024年10月 金屬切削(xuē)機床產量數據
- 2024年9月 新能源汽車銷量情況
- 2024年8月 新能源汽車產量數據
- 2028年8月 基本型乘用車(轎(jiào)車(chē))產量數(shù)據