成組技術:在工業 4.0 時代(dài)實現卓越運營
2018-12-17 來(lái)源:山高刀具集團 作(zuò)者:技術經理 Patrick de Vos
上海, 2018 年(nián) 12月 -工業革命發展到現在,製造商們始終擁有一個共同(tóng)的目標,那就是將零(líng)件生產控製在一定時間和成本內(nèi)。製造工藝從手工製造的單件生產模式發展(zhǎn)為大批量生產線,相(xiàng)同零件的產量顯著提高:大批(pī)量/少品(pǐn)種 (HVLM)生產方案。近年來,隨著數字技術開始廣泛應用於編程、機床控(kòng)製和工件處理係統,工業4.0得到了(le)快速發展,推動了多品(pǐn)種/小批量 (HMLV) 生產模式。
在(zài)工業 4.0 時代,企(qǐ)業往往高(gāo)度(dù)重視最新的生產技術和數字化技術。然而,生(shēng)產(chǎn)率和成本效益最大化依舊建立在卓越運營基礎之(zhī)上。在目前的(de)經濟環境下,製(zhì)造商普遍認為速度是(shì)卓越運營的關鍵指標:盡可能縮短從圖紙進入工廠,到(dào)工件成品最(zuì)終離開工廠的時間。製(zhì)造商開展(zhǎn)的提速工作通常集中在例如精益製造或六西格瑪 (SixSigma)等策略上。
然(rán)而,這些策略通常涉及到 HVLM 生產,有時候並不適用於 HMLV 方案(àn)。成組技術方法是簡化 HMLV輸出(chū)的(de)一項重要因素,將零件分類並編(biān)碼到不同的可加工(gōng)係列中,使車間(jiān)能夠實現最高水準的卓越運(yùn)營。
成組技術
成組技術是一種製造組織策略,在該(gāi)策略中,具有某些相似性(例如幾何形狀、材料、製造工藝或質量(liàng)標準)的零件被歸到特(tè)定群組或係(xì)列中,然後采用一種通用的生產方法進行製造。在計劃加工工序時,它針對(duì)的(de)是整(zhěng)個零件係列(liè),而不是單(dān)個工件。
通常,組織生產零件係列被稱為“單元式製造”。單元(yuán)式製造興起於(yú) 20 世紀 80 年代,大約在 HMLV 生(shēng)產時(shí)代開始的時候。製造商(shāng)們認識到,批量生產規模不斷縮小,而工件和新工件材料的種類不(bú)斷增加。車間麵對的是千差萬別且生產批量相對較小的工件(jiàn)。因(yīn)此,生產準備時間大幅增加,製造商們試圖克服這個問題。
成組技術中的零件(jiàn)係列根據零件的編碼(mǎ)和分類(lèi)進行創建。每個零件(jiàn)都會分配一個由字母、數字(zì)或兩者的組合組(zǔ)成(chéng)的代碼,並且每個單獨的字母或數字都代表(biǎo)工件的特定特征或生產工(gōng)件所(suǒ)需的生產技術。如圖 1所示,零件代碼第 6 位表示工件尺寸,第 7 位表示原材料,第 8 位表示工件材(cái)料的原(yuán)始形狀,第 9位表示所需的質量等級(jí)。第 3 位至第 5 位描述了加工零件所需的工序。
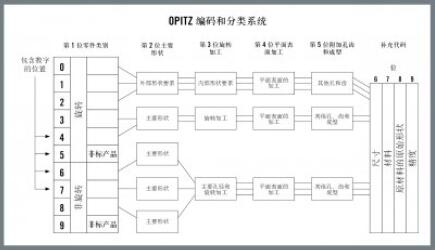
圖 1:優化代碼和分類係統
零件代碼用於計劃生(shēng)產,並通過參考一個稱為“複雜工件”的(de)虛擬或不存在的(de)零件來報價(jià),如圖 2 第二行所示。這裏所謂的(de)“複雜”並不意味著工件難以加工;相反,它描述的是一個通用工件,該工件展示了公司能夠加工的所(suǒ)有特(tè)征,例如高精度和低精度的孔、深腔體和淺腔體、側銑特征等。圖中第一行(háng)的零件代表了可(kě)以選用(yòng)第二行複雜工件所述的工序生產的工(gōng)件。通過將加(jiā)工各個(gè)所需特征的成(chéng)本相加,可以(yǐ)得(dé)出代表性的總(zǒng)成本(běn),並(bìng)且簡化(huà)了定價估算工作。不需要(yào)逐個分析零件成本。
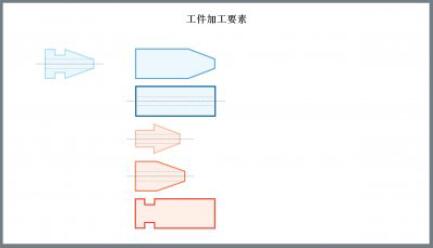
圖(tú) 2:工件加工元素
生產計(jì)劃員和(hé)估價員一起研(yán)究工件圖(tú)紙,通過將工件上的特征與複雜工件上的特征相匹配來進(jìn)行報價,並且還可確(què)定其他生產要素,例如所需的機床、是否需要冷卻液等。此外,借助成熟的(de) CAM 係統執行成組技術還能進一步降低預加工工程時間的要求。另外,由於工廠各部門都基(jī)於相同(tóng)的複雜工件模型工作,這也有效改(gǎi)善了工廠跨部門溝通。
成組技(jì)術方法最初(chū)起源(yuán)於(yú)開發(fā)人員需要與工藝工程師、程序員和計(jì)劃(huá)員接洽,以便收集各種生產工序的成本信息。盡管這種開發(fā)始於 20 世(shì)紀 80年代,但將個(gè)人經驗和數據匯編並組織(zhī)成為一個係統的過程類似於如今盛行的人工智能活動。
在某些(xiē)情(qíng)況下,成(chéng)組技術可以推動車間的重(chóng)組。圖 3 左側顯示了零件在車間中經曆的迂回路徑,該(gāi)車(chē)間采用基於車削、銑削、磨削等機床功能的傳統布局。然而,當工件采用單元布局(圖中右側所示)以係列的形式進行分組和加(jiā)工時,可以布置機床以簡化製造流程,並最大限度地(dì)減少零(líng)件在車間中的移動。每個不同的工件係列均以最高效的方(fāng)式加工,而不需要在(zài)車間內進(jìn)行不必要的運(yùn)輸。因(yīn)此(cǐ)大幅縮短了零件生產時間。
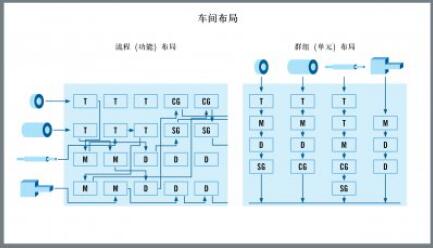
圖 3:車間布局
當(dāng)然,采用新概念既有益處(chù)也(yě)有挑戰。成組(zǔ)技術方法在工(gōng)程設計、工藝規劃和製造(zào)時間節省方麵有不少優點,但也存在一些弊端。首先,在某種程度上,成組(zǔ)技術方法降低了靈活性。如(rú)果某一特定工(gōng)件配置的需求顯著增加,造成生產瓶頸,那麽傳統的車間設置將更加靈活。在傳統布局中,部門中的其他機床可以用來生(shēng)產零件。其次,管理機(jī)床停機時間也會是一項挑戰。如果一(yī)個零件係列出現暫時的(de)需求下降,那麽單元布局中的機床將會閑置。
實施(shī)成組技術概念可能帶來的另一個難題是(shì)往往需要花費過多的時間(jiān)來比較各個編碼(mǎ)係統。然而,比編(biān)碼係(xì)統本身更重要的,是公司應當全麵了(le)解其設備和資(zī)源,以及期望的結果。在這種情況下,內部創建自定義編碼係統將會(huì)是一種簡單而高效的選擇。重新安排車間以更有效地加工零件係(xì)列是另一(yī)項工廠特定的決(jué)策。大型企業(yè)更容易(yì)重新調整他們的機床,而小(xiǎo)型企(qǐ)業可能麵臨經濟方麵的限製和(hé)其他因素。
更快、更準確的(de)報價
創建零件報價的成組技術方法可以提高收入和盈利能力。例如,一家航空航天分包商采用 HMLV生產環境,其批量大小為 1 到 5 個工件(jiàn),每年收到大約 4000份報價(jià)請求。由於沒有足夠的時間對每個零件進行單獨的分析和報價(jià),延緩了定價過程,導致車間隻能對4000 份可能(néng)任務(wù)中的 1500 份進行細致的報價。這(zhè)家分包商(shāng)收到了大約 2600 份訂單。後來,利用成組(zǔ)技術舉措支(zhī)持的(de)分析並利用複雜工件信息進行零件報價後,這家分(fèn)包(bāo)商發現自己每(měi)年可以進行 3000份細致的報價。更多細致的報價吸引(yǐn)到了更多的訂單,達到每年 3200 份訂單的水平。最重要的是,在根據成本和(hé)利潤進行投標時,投標的成本比先前未采用成組技術概念(niàn)的投標平均降低了 30% 以(yǐ)上。
更快、更準確的報價流程具有兩個優(yōu)點。一是錯誤的(de)、對利潤率產生負麵影響的投標價過低情況減少,二是不準確的、令客戶難以接受的虛高報價(jià)情況減少。成組技術概念的實施讓(ràng)製(zhì)造商能夠更好地控製所做的工作及其成本,並降低了不準確報價的發生率。
成組技術規定,不考(kǎo)慮每個單獨的工件及(jí)其生產參數,而是將具有相似特征的零件分組在一(yī)起進行加工。以一家生產皮帶式傳(chuán)動裝置的皮帶輪的車間為例。為了適用於不同尺寸的皮帶,各個皮帶輪的帶槽的直徑(jìng)、寬度(dù)和輪廓有所不同。采用不同配(pèi)置加工時(shí),其間的轉換時(shí)間約為一(yī)個半小時。
工藝流程分析表明,每(měi)次進行皮帶(dài)輪加工轉換時,都(dōu)要完(wán)全拆卸機床,而且需要取出、清洗和放好所有(yǒu)刀(dāo)具。為(wéi)了加工下一個皮帶(dài)輪,需要將大多數相同的刀具放回機床中。在成組技術方法中,相似但不完全相同的皮帶輪被劃分為一個係列。轉換工作包括更改(gǎi) NC 程序、修改一些加(jiā)工參數,有時需要更改用於加工槽形的刀具。根據特定工件,轉換時間從一個半小時(shí)縮短為十分鍾。采用這個方法的主要(yào)難題在於讓車間人員相信,他(tā)們生產的零件屬於同一個係列,可以通過調整工藝流程實現更快地加工。
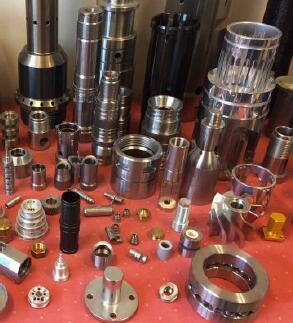
不同工件
結(jié)論
成組(zǔ)技術製造組織策略可幫助(zhù)製造商高效應對 HMLV 生產的挑戰,山高澳大利亞分公司的 Dave Morr 已對此進行了廣泛的開發工作。傳統的生產率提高策略(例如精益製造(zào)和(hé)六(liù)西格瑪)確實能夠(gòu)帶來一定(dìng)改善,特別是在可對大量相同零件的加工工序進行微調的(de) HVLM 生產中。然而,隨著加工技術以及數字產品設計和管理的進步(bù),高(gāo)度多樣化、小批量的製造日益增多。通過將零件歸(guī)類為(wéi)係列並(bìng)整合定價活動(dòng)和(hé)加工工(gōng)序,成(chéng)組技術方法為(wéi)製造商提供(gòng)了一種高效(xiào)應對工(gōng)業 4.0 時代諸多(duō)挑戰的方法。
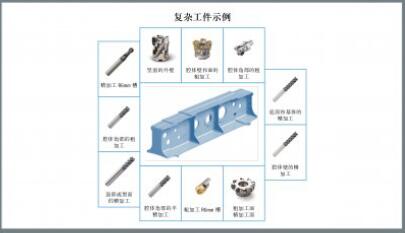
圖 4:複雜工件示例
說明
成組技(jì)術和山高谘詢服務 (SCS)成組(zǔ)技術製造組(zǔ)織策略是實(shí)現卓越(yuè)運營的重要要素,並且(qiě)可以(yǐ)有力地推動製造商各方麵的工作。然而,競爭的壓力迫使許多製造商幾乎隻專注於以特定的成本按時生產特(tè)定數量的零件,而沒有時間或專業知識來仔細分析和優(yōu)化其業務和加工工序。
山高成立(lì)了一個新的業務部門,旨在幫助那些有資源可用於生產改進(jìn),但沒有足夠的資金支付雇用工藝改進工程師的高費用或與大型(xíng)業務谘詢公司進行合作的中型公司。山高谘詢服務 (SCS)可幫助製造(zào)商(shāng)平衡(héng)整體製(zhì)造和業務問題與加工效率和經濟性。SCS對品(pǐn)牌保持中立(lì),支持用戶當前使用的任(rèn)何品牌刀具。
利(lì)用 SCS 的(de)第一步是製造(zào)效率評估 (MEE) 工作,包括對加工、生產係統和運營管理績效的分析。SCS 將(jiāng)分析公司的產能,並檢查準備、加工和(hé)設備處理方麵(miàn)的問(wèn)題。從中能夠揭示(shì)產能(néng)/資產問題的根源,以及(jí)員工的知識短板(bǎn)。準備分析包括編程支持以及方法和零件的標準化。通過方法(fǎ)優化和故障(zhàng)排除來識別並解決加工問題。庫存和消耗可視化以及刀具管(guǎn)理計(jì)劃可解決設備處理問題。
在整個 SCS 計劃中,山高技術教育(yù)服務(STEP 研討(tǎo)會和課程)幫助培訓製造公司的員工。服務的一個(gè)主要方麵包括說服車間人員采(cǎi)用新的策略。僅僅(jǐn)將宣傳海報貼在車(chē)間牆壁(bì)上不能起到多大的效果。事(shì)實上,問題往(wǎng)往不在於缺乏新的(de)知識或理念,而(ér)是因為車間人員傾向於采納(nà)傳統解決方案。成功的關鍵是說服員工認識到新策略的好處,並製(zhì)定實施新(xīn)策略的準(zhǔn)則。
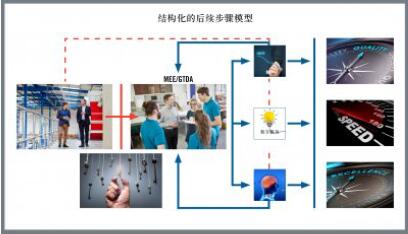
圖 5:NEXT STEP 模型
投稿箱:
如果您有機(jī)床(chuáng)行業、企(qǐ)業相關新聞稿件發表,或進行資訊合作,歡迎聯係本網編輯部, 郵箱:skjcsc@vip.sina.com
如果您有機(jī)床(chuáng)行業、企(qǐ)業相關新聞稿件發表,或進行資訊合作,歡迎聯係本網編輯部, 郵箱:skjcsc@vip.sina.com
更多相關信息
業界視點
| 更多
行業數(shù)據
| 更多(duō)
- 2024年11月 金屬切削機床產量數(shù)據
- 2024年11月(yuè) 分地區(qū)金屬切(qiē)削機床產量數據
- 2024年11月 軸(zhóu)承出口情況
- 2024年11月 基本(běn)型乘用車(轎車)產量數據
- 2024年11月 新能源汽車產(chǎn)量(liàng)數(shù)據
- 2024年(nián)11月 新能源汽車銷量情況
- 2024年10月 新能(néng)源汽車產量數據
- 2024年10月 軸承出(chū)口情況
- 2024年10月 分地區金屬切削機床產量數據
- 2024年10月 金屬切削機床產量(liàng)數據
- 2024年9月 新能源(yuán)汽車銷量(liàng)情況
- 2024年8月 新能源汽車產(chǎn)量數據
- 2028年8月 基本型乘用車(轎車)產量數據
博文選(xuǎn)萃
| 更多